Yes, aluminum can be sputtered. Sputtering is a widely used thin-film deposition technique that involves bombarding a target material with high-energy ions, causing atoms to be ejected from the target's surface. These ejected atoms then deposit onto a substrate, forming a thin film. Aluminum, being a common and versatile material, is frequently used as a target in sputtering processes to create thin films for various applications, such as in electronics, optics, and coatings.
Key Points Explained:
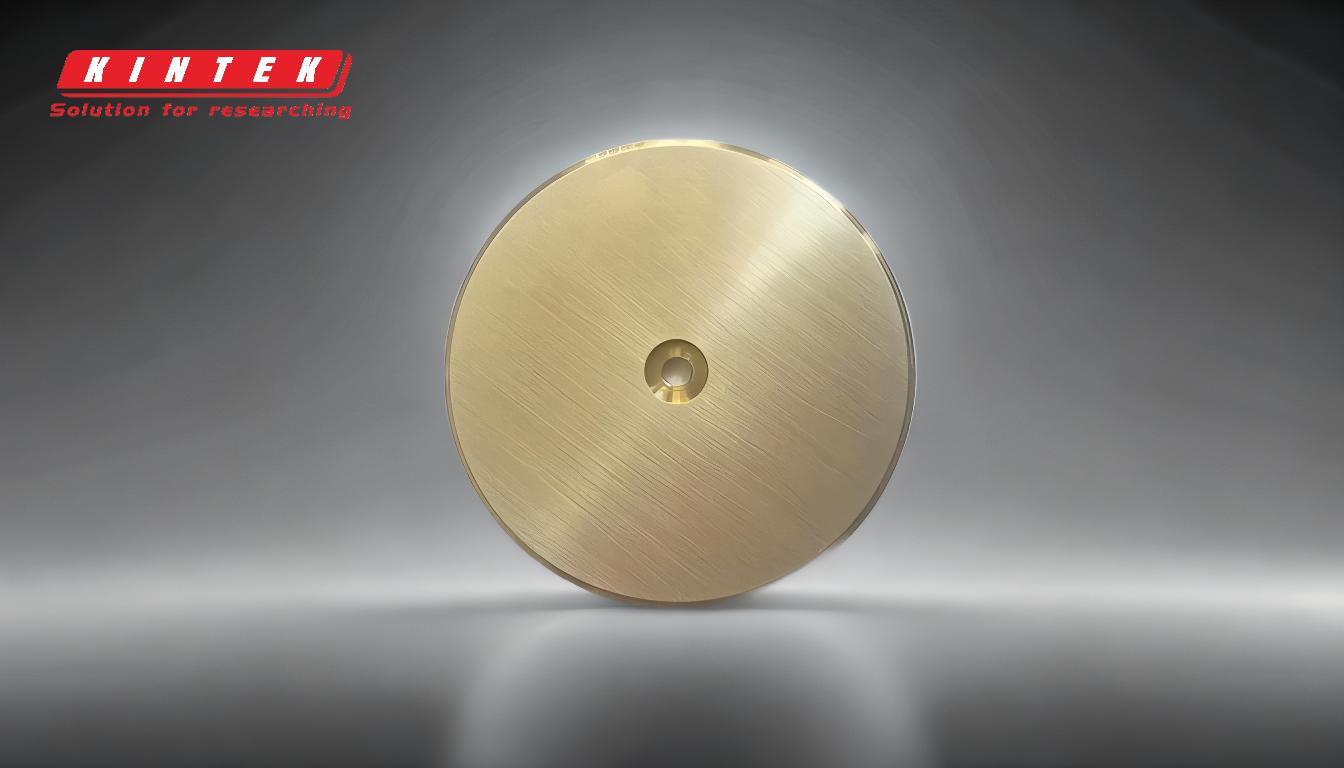
-
Sputtering Process Overview:
- Sputtering is a physical vapor deposition (PVD) technique used to deposit thin films of materials onto substrates.
- The process involves bombarding a target material (in this case, aluminum) with high-energy ions, typically from an inert gas like argon.
- The ions transfer energy to the target material, causing atoms to be ejected from its surface.
- These ejected atoms travel through a vacuum and deposit onto a substrate, forming a thin film.
-
Why Aluminum is Suitable for Sputtering:
- Aluminum is a widely used material in sputtering due to its excellent electrical conductivity, thermal conductivity, and corrosion resistance.
- It is often used to create thin films for applications such as semiconductor devices, reflective coatings, and protective layers.
- Aluminum is relatively easy to sputter because it has a low melting point and good adhesion properties when deposited as a thin film.
-
Steps in Sputtering Aluminum:
- Target Preparation: Aluminum is shaped into a target, which is placed in the sputtering chamber.
- Vacuum Creation: The chamber is evacuated to remove air and other contaminants, ensuring a clean environment for the sputtering process.
- Introduction of Sputtering Gas: An inert gas, typically argon, is introduced into the chamber at a controlled pressure.
- Ion Generation: A high voltage is applied to the target, creating a plasma of ionized gas atoms.
- Bombardment and Ejection: The ionized gas atoms collide with the aluminum target, ejecting aluminum atoms from its surface.
- Deposition: The ejected aluminum atoms travel through the vacuum and deposit onto the substrate, forming a thin film.
-
Applications of Sputtered Aluminum Films:
- Electronics: Aluminum is commonly used in the fabrication of integrated circuits, where it serves as a conductive layer for interconnects.
- Optics: Sputtered aluminum films are used to create reflective coatings for mirrors and other optical components.
- Protective Coatings: Aluminum films can be used to protect surfaces from corrosion and wear.
- Decorative Coatings: Sputtered aluminum is also used in decorative applications, such as coatings on consumer electronics and automotive parts.
-
Advantages of Sputtering Aluminum:
- Uniformity: Sputtering allows for the deposition of highly uniform and precise thin films, which is critical for many applications.
- Adhesion: Sputtered aluminum films typically have excellent adhesion to a variety of substrates, including glass, silicon, and plastics.
- Versatility: The process can be used to deposit aluminum on complex geometries and large areas, making it suitable for a wide range of applications.
- Purity: Sputtering can produce high-purity aluminum films, which is important for applications in electronics and optics.
-
Challenges and Considerations:
- Oxidation: Aluminum is prone to oxidation, so care must be taken to minimize exposure to oxygen during the sputtering process.
- Target Purity: The quality of the sputtered film depends on the purity of the aluminum target. High-purity targets are often required for critical applications.
- Process Control: Parameters such as gas pressure, voltage, and substrate temperature must be carefully controlled to achieve the desired film properties.
In conclusion, aluminum is a highly suitable material for sputtering, and the process is widely used in various industries to deposit thin films with excellent properties. The ability to control the sputtering process allows for the creation of high-quality aluminum films that meet the specific requirements of different applications.
Summary Table:
Key Aspect | Details |
---|---|
Sputtering Process | Physical vapor deposition (PVD) technique using high-energy ions. |
Why Aluminum? | Excellent conductivity, corrosion resistance, and low melting point. |
Steps in Sputtering | Target preparation, vacuum creation, gas introduction, ion generation. |
Applications | Electronics, optics, protective coatings, decorative coatings. |
Advantages | Uniformity, adhesion, versatility, and high purity. |
Challenges | Oxidation, target purity, and precise process control. |
Interested in sputtering aluminum for your project? Contact our experts today to learn more!