Sputtering targets are critical components in thin-film deposition processes, used in industries such as semiconductors, optics, and solar panels. Their manufacturing involves specialized techniques tailored to the material properties and intended applications. Common methods include classical and vacuum hot-pressing, cold-pressing and sintering, and vacuum melting and casting. Advanced techniques like electroplating, sputtering, and vapor deposition are also employed to achieve fine grain structures and precise shapes. The choice of method depends on factors such as material type, desired grain structure, and end-use requirements.
Key Points Explained:
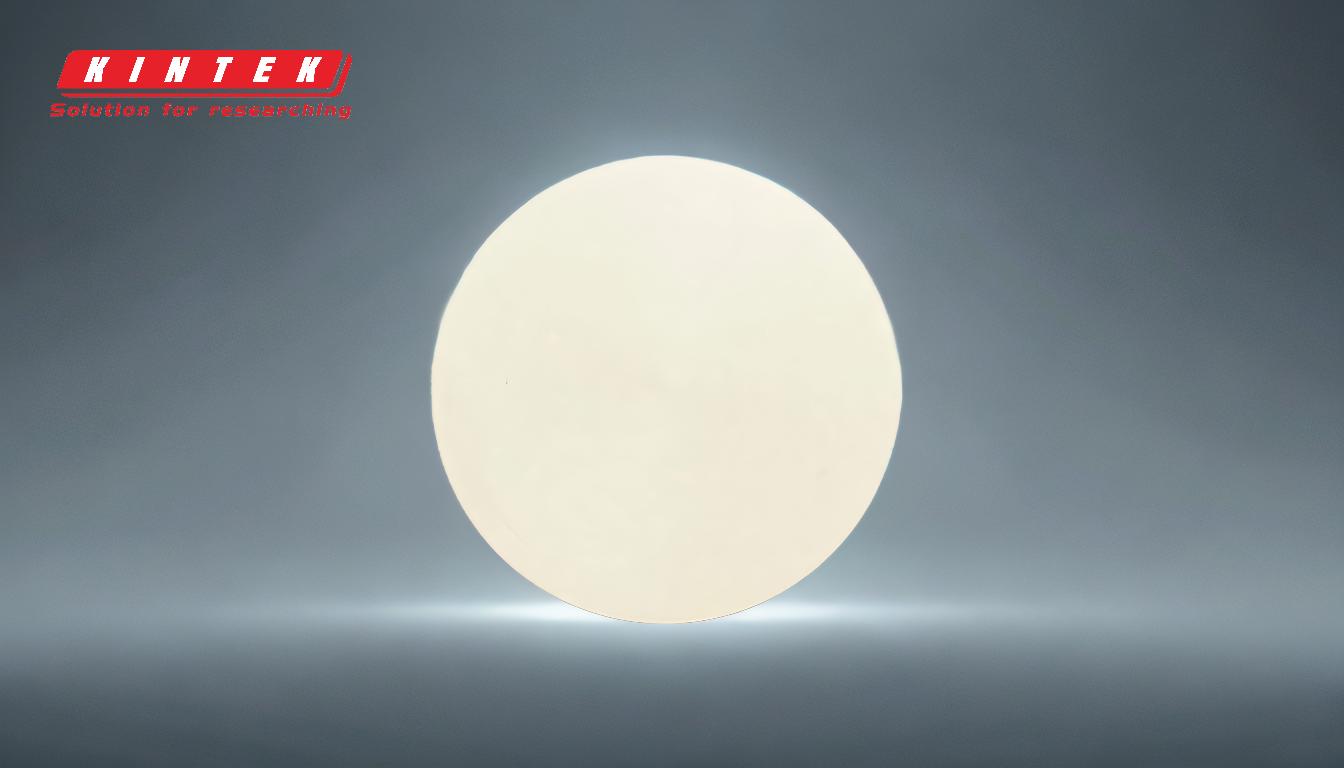
-
Overview of Sputtering Target Manufacturing:
- Sputtering targets are manufactured using processes that ensure high purity, uniformity, and structural integrity.
- The manufacturing method is selected based on the material properties (e.g., metals, ceramics, or alloys) and the intended application (e.g., semiconductors, optics).
-
Classical and Vacuum Hot-Pressing:
- This method involves applying heat and pressure to compact powdered materials into dense, uniform targets.
- Vacuum hot-pressing is used for materials that require high purity and minimal oxidation, such as refractory metals or ceramics.
- The process enhances grain structure and reduces porosity, making it suitable for high-performance applications.
-
Cold-Pressing and Sintering:
- Cold-pressing compacts powdered materials at room temperature, followed by sintering (heating below the melting point) to bond particles.
- This method is cost-effective and suitable for materials that do not require extremely fine grain structures.
- It is commonly used for manufacturing ceramic or composite sputtering targets.
-
Vacuum Melting and Casting:
- This process involves melting the material in a vacuum to prevent contamination and casting it into the desired shape.
- It is ideal for metals and alloys that require high purity and homogeneity.
- The resulting targets have excellent mechanical and thermal properties, making them suitable for demanding applications.
-
Advanced Manufacturing Methods:
- Techniques like electroplating, sputtering, and vapor deposition are used to create targets with ultra-fine grain structures.
- These methods allow for precise control over material composition and microstructure, enabling the production of targets in nearly any shape or size.
- Advanced methods are often used for specialized applications, such as high-performance semiconductors or optical coatings.
-
Material-Specific Considerations:
- The choice of manufacturing method depends on the material's properties, such as melting point, reactivity, and grain structure requirements.
- For example, silicon sputtering targets may use vapor deposition to achieve high purity and uniformity, while refractory metals may require vacuum hot-pressing.
-
Quality Control and Testing:
- Sputtering targets undergo rigorous quality control to ensure they meet industry standards for purity, density, and grain size.
- Testing methods include microscopy, spectroscopy, and mechanical testing to verify material properties and performance.
-
Applications and End-Use Requirements:
- The manufacturing process is tailored to the target's intended application, such as semiconductor fabrication, solar panels, or decorative coatings.
- For instance, semiconductor targets require extremely high purity and fine grain structures, while decorative coatings may prioritize cost-effectiveness and scalability.
By understanding these key points, equipment and consumable purchasers can make informed decisions when selecting sputtering targets, ensuring they meet the specific requirements of their applications.
Summary Table:
Manufacturing Method | Key Features | Common Applications |
---|---|---|
Classical & Vacuum Hot-Pressing | High purity, minimal oxidation, enhanced grain structure | Refractory metals, ceramics |
Cold-Pressing & Sintering | Cost-effective, suitable for less fine grain structures | Ceramics, composites |
Vacuum Melting & Casting | High purity, homogeneity, excellent mechanical properties | Metals, alloys |
Advanced Methods (Electroplating, Sputtering, Vapor Deposition) | Ultra-fine grain structures, precise control over composition | High-performance semiconductors, optics |
Need sputtering targets tailored to your application? Contact our experts today for personalized solutions!