A regenerator is a type of compact heat exchanger that operates by alternately storing and releasing heat using a heat storage matrix. During the heating phase, hot gas flows through the regenerator, transferring heat to the matrix. In the cooling phase, the cooler gas passes through the same matrix, absorbing the stored heat. This cyclical process allows for efficient heat exchange, making regenerators particularly useful in applications like gas turbines, Stirling engines, and cryogenic systems. The key to their efficiency lies in the ability of the matrix to store and release heat rapidly, minimizing energy loss and maximizing thermal performance.
Key Points Explained:
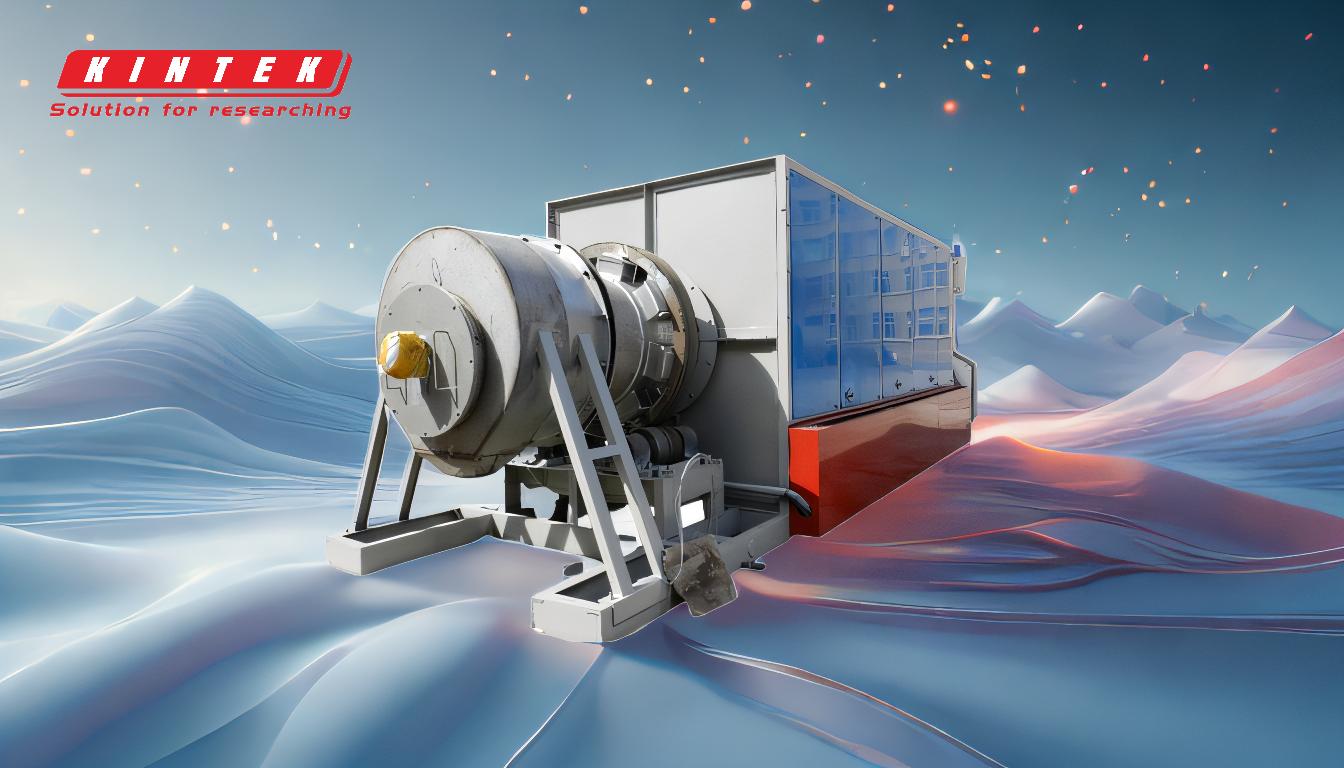
-
Definition and Function of a Regenerator
- A regenerator is a compact heat exchanger designed to store and release heat alternately using a heat storage matrix.
- Its primary function is to improve thermal efficiency by recovering and reusing heat that would otherwise be lost.
-
How the Regenerator Works
- Heating Phase: Hot gas flows through the regenerator, transferring its heat to the heat storage matrix. The matrix, often made of materials with high thermal capacity (e.g., ceramic or metal), absorbs and stores this heat.
- Cooling Phase: Cooler gas passes through the same matrix, absorbing the stored heat. This process ensures that the heat is reused, reducing energy waste.
- The alternation between heating and cooling phases is continuous, making the regenerator a dynamic and efficient system.
-
Heat Storage Matrix
- The matrix is the core component of the regenerator, responsible for temporarily storing heat.
- Materials used for the matrix must have high thermal conductivity, high heat capacity, and durability to withstand repeated thermal cycling.
- Common materials include ceramics, metals, and specialized alloys.
-
Applications of Regenerators
- Gas Turbines: Regenerators recover heat from exhaust gases, improving overall efficiency.
- Stirling Engines: They play a critical role in the engine's thermodynamic cycle by storing and releasing heat.
- Cryogenic Systems: Regenerators are used to achieve extremely low temperatures by efficiently managing heat exchange.
-
Advantages of Regenerators
- Energy Efficiency: By reusing heat, regenerators significantly reduce energy consumption.
- Compact Design: Their compactness makes them suitable for applications with space constraints.
- Cost-Effectiveness: Over time, the energy savings provided by regenerators can offset their initial cost.
-
Challenges and Limitations
- Material Degradation: Repeated thermal cycling can lead to wear and tear of the matrix material.
- Pressure Drop: The flow of gases through the matrix can cause a pressure drop, which may affect system performance.
- Complexity in Design: Optimizing the regenerator for specific applications requires careful engineering and material selection.
-
Future Developments
- Research is ongoing to develop advanced materials with better thermal properties and longer lifespans.
- Innovations in design aim to minimize pressure drops and improve overall efficiency.
- Integration with renewable energy systems is an emerging area of interest, where regenerators can play a role in energy storage and recovery.
By understanding these key points, equipment and consumable purchasers can make informed decisions about the suitability of regenerators for their specific applications. The ability to recover and reuse heat makes regenerators a valuable component in systems where energy efficiency is a priority.
Summary Table:
Key Aspect | Details |
---|---|
Definition | Compact heat exchanger using a heat storage matrix. |
How It Works | Alternates between heating (stores heat) and cooling (releases heat) phases. |
Heat Storage Matrix | Made of ceramics, metals, or alloys with high thermal capacity. |
Applications | Gas turbines, Stirling engines, cryogenic systems. |
Advantages | Energy efficiency, compact design, cost-effectiveness. |
Challenges | Material degradation, pressure drop, design complexity. |
Future Developments | Advanced materials, minimized pressure drops, renewable energy integration. |
Ready to enhance your system's efficiency with regenerators? Contact our experts today for tailored solutions!