Injection molding is a manufacturing process used to produce parts by injecting molten material into a mold. The process involves several critical steps that ensure the final product meets the desired specifications. Below is a detailed explanation of the five key steps in the injection molding process, which include clamping, injection, dwelling, cooling, and ejection. Each step plays a vital role in shaping the final product, ensuring precision, durability, and quality.
Key Points Explained:
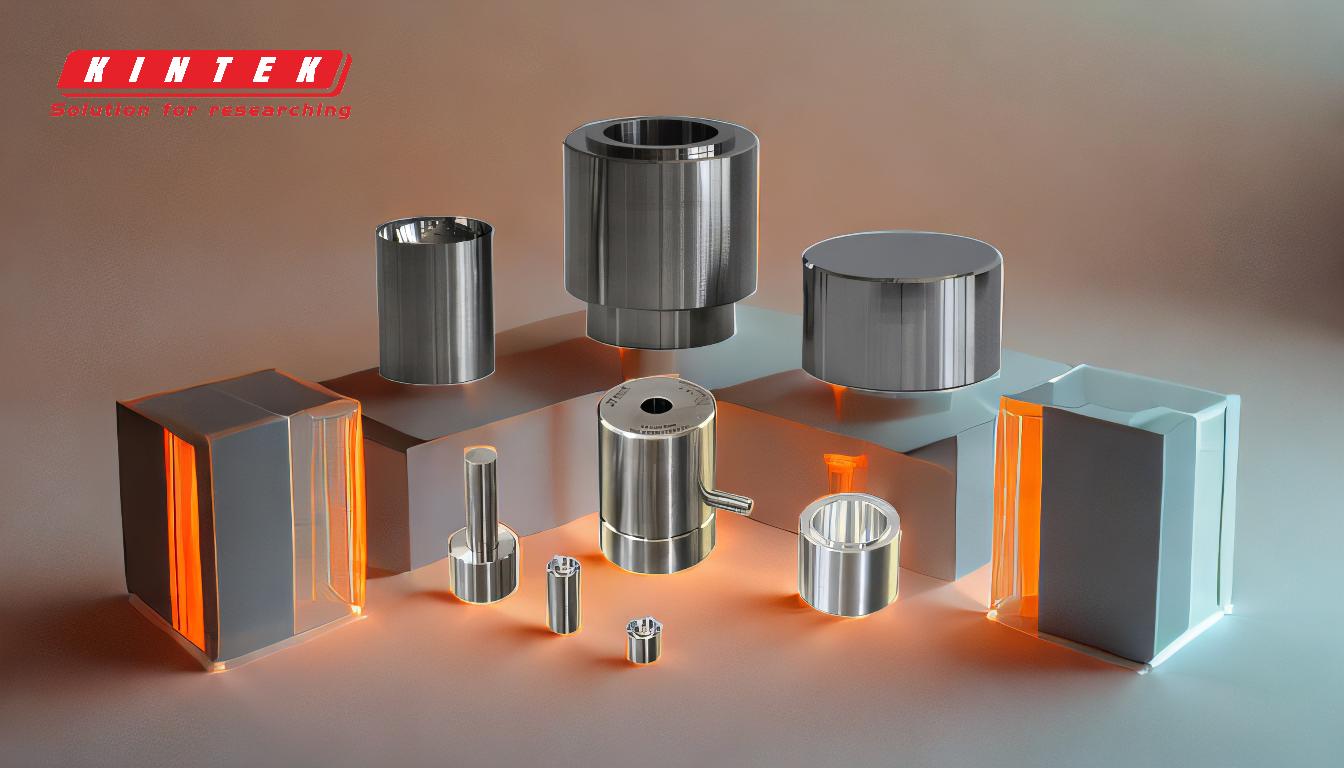
-
Clamping
- Purpose: The clamping step ensures that the mold is securely closed before the injection process begins.
- Process: The two halves of the mold (the stationary side and the moving side) are brought together and held tightly by a clamping unit. This prevents any molten material from leaking out during injection.
- Importance: Proper clamping is essential to maintain the shape and integrity of the final product. Insufficient clamping force can lead to defects such as flash (excess material) or incomplete parts.
-
Injection
- Purpose: In this step, the molten material is injected into the mold cavity.
- Process: The material (typically plastic pellets) is heated until it reaches a molten state and then forced into the mold under high pressure. The injection unit consists of a screw or plunger that pushes the material into the mold.
- Importance: The injection phase determines how well the material fills the mold. Factors such as injection speed, pressure, and temperature must be carefully controlled to ensure the material flows evenly and fills all parts of the mold.
-
Dwelling
- Purpose: The dwelling phase ensures that the molten material completely fills the mold and compensates for any shrinkage as the material cools.
- Process: After the initial injection, additional pressure is applied to pack the material tightly into the mold. This step ensures that the material reaches all corners and details of the mold.
- Importance: Proper dwelling prevents defects like sink marks (depressions on the surface) or voids (empty spaces within the part). It also ensures dimensional accuracy and consistency.
-
Cooling
- Purpose: Cooling solidifies the molten material into the desired shape.
- Process: The mold is cooled using channels that circulate water or another cooling medium. The cooling time depends on the material used, the thickness of the part, and the mold design.
- Importance: Cooling is critical for achieving the final shape and structural integrity of the part. Insufficient cooling can lead to warping or deformation, while excessive cooling can increase cycle times and reduce efficiency.
-
Ejection
- Purpose: The ejection step removes the solidified part from the mold.
- Process: Once the part has cooled and solidified, the mold opens, and ejector pins push the part out of the mold cavity. The mold then closes again, ready for the next cycle.
- Importance: Proper ejection ensures that the part is removed without damage. The design of the ejector system must account for the shape and size of the part to avoid issues like sticking or breakage.
By following these five steps—clamping, injection, dwelling, cooling, and ejection—manufacturers can produce high-quality, consistent parts efficiently. Each step requires precise control of parameters such as temperature, pressure, and timing to achieve the desired results. Understanding these steps is crucial for anyone involved in the design, production, or procurement of injection-molded parts.
Summary Table:
Step | Purpose | Process | Importance |
---|---|---|---|
Clamping | Securely close the mold before injection. | Mold halves are held tightly by a clamping unit. | Prevents defects like flash or incomplete parts. |
Injection | Inject molten material into the mold cavity. | Molten material is forced into the mold under high pressure. | Ensures even material flow and complete mold filling. |
Dwelling | Ensure complete mold filling and compensate for shrinkage. | Additional pressure is applied to pack the material tightly. | Prevents sink marks, voids, and ensures dimensional accuracy. |
Cooling | Solidify the molten material into the desired shape. | Mold is cooled using water or another medium. | Critical for part shape and structural integrity; avoids warping or deformation. |
Ejection | Remove the solidified part from the mold. | Ejector pins push the part out of the mold cavity. | Ensures part removal without damage; avoids sticking or breakage. |
Ready to optimize your injection molding process? Contact our experts today for tailored solutions!