Compression molds are essential tools in manufacturing processes, particularly for shaping materials like plastics, rubber, and composites. The four primary types of compression molds are flash, positive, landed positive, and semi-positive molds, with flash molds being the most commonly used. These molds differ in their design, functionality, and application suitability. Additionally, compression molding techniques are categorized into bulk and sheet molding, with bulk molding involving a mixture of fillers, catalysts, stabilizers, pigments, and fiber reinforcers. Understanding these types and their applications is crucial for selecting the right mold for specific manufacturing needs.
Key Points Explained:
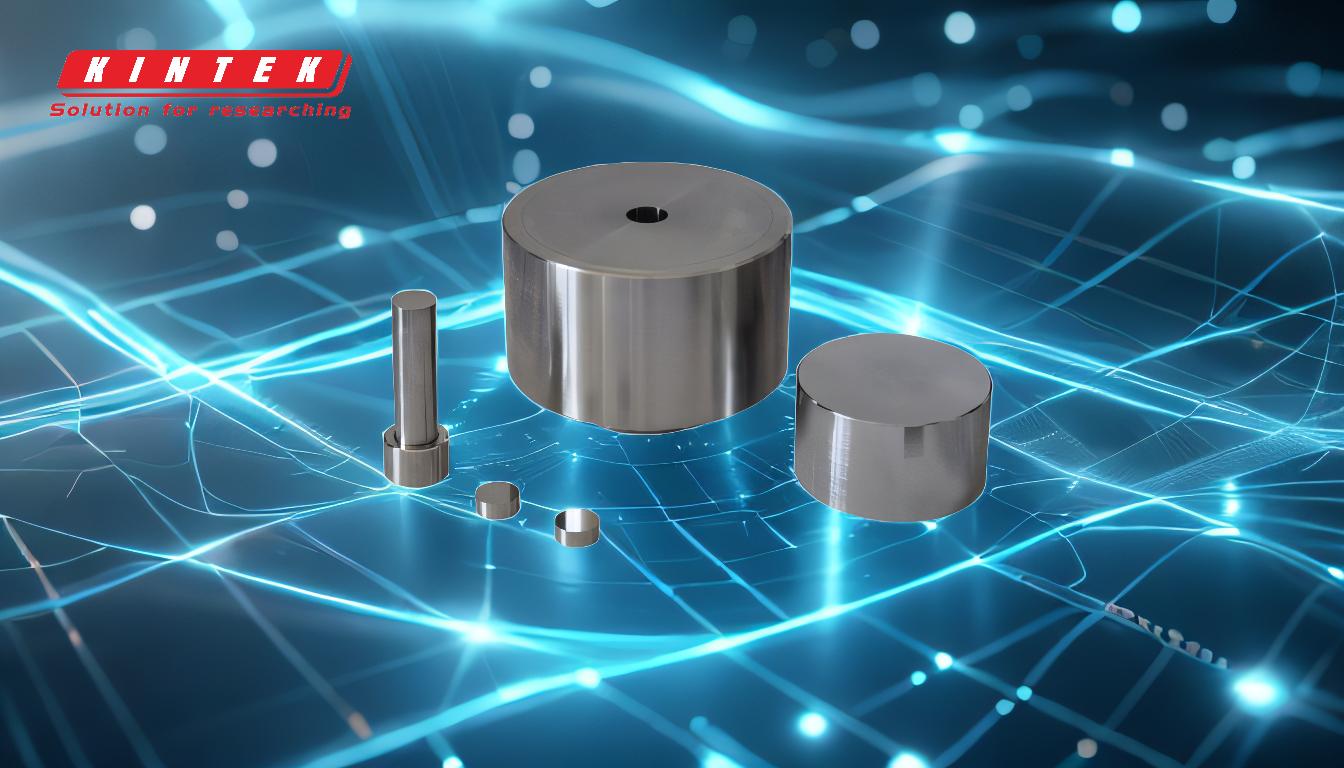
-
Flash Molds:
- Design: Flash molds are designed with excess material flowing out of the mold cavity during compression.
- Functionality: The excess material, or flash, is trimmed off after the molding process.
- Applications: Commonly used for high-volume production due to their simplicity and cost-effectiveness.
- Advantages: Easy to manufacture and maintain, suitable for parts with simple geometries.
- Disadvantages: Material wastage due to flash, may require additional post-processing.
-
Positive Molds:
- Design: Positive molds have a cavity that is completely closed off during the molding process.
- Functionality: No excess material escapes, ensuring precise control over the final product dimensions.
- Applications: Ideal for producing parts with tight tolerances and complex shapes.
- Advantages: High precision, minimal material wastage.
- Disadvantages: More complex and expensive to manufacture, requires precise alignment.
-
Landed Positive Molds:
- Design: A variation of positive molds with a landing area that stops the mold at a specific point.
- Functionality: Ensures consistent part thickness and prevents over-compression.
- Applications: Suitable for parts requiring uniform thickness and high dimensional accuracy.
- Advantages: Improved control over part dimensions, reduced risk of over-compression.
- Disadvantages: Higher cost and complexity compared to flash molds.
-
Semi-Positive Molds:
- Design: Combines features of both flash and positive molds, with a controlled amount of material escaping.
- Functionality: Allows for some material flow while maintaining precise control over part dimensions.
- Applications: Used for parts requiring both precision and some flexibility in material flow.
- Advantages: Balances precision and material efficiency, suitable for a wide range of applications.
- Disadvantages: More complex than flash molds, may require fine-tuning for optimal performance.
-
Bulk Molding:
- Process: Involves using a mixture of fillers, catalysts, stabilizers, pigments, and fiber reinforcers.
- Applications: Commonly used for producing large, complex parts with high strength and durability.
- Advantages: Versatile, can produce parts with enhanced mechanical properties.
- Disadvantages: Requires precise control over material composition and molding conditions.
-
Sheet Molding:
- Process: Involves pre-formed sheets of material that are compressed into the desired shape.
- Applications: Suitable for producing flat or slightly curved parts with consistent thickness.
- Advantages: Efficient for high-volume production, consistent material distribution.
- Disadvantages: Limited to simpler geometries, may require additional processing for complex shapes.
Understanding the different types of compression molds and their respective molding techniques is crucial for selecting the appropriate method for specific manufacturing needs. Each type offers unique advantages and challenges, making it essential to consider factors such as part complexity, material properties, and production volume when choosing the right mold.
Summary Table:
Type | Design | Applications | Advantages | Disadvantages |
---|---|---|---|---|
Flash Molds | Excess material flows out of the mold cavity during compression. | High-volume production, simple geometries. | Easy to manufacture, cost-effective. | Material wastage, additional post-processing. |
Positive Molds | Completely closed cavity, no excess material escapes. | Parts with tight tolerances and complex shapes. | High precision, minimal material wastage. | Complex and expensive to manufacture, requires precise alignment. |
Landed Positive | Variation of positive molds with a landing area for consistent thickness. | Parts requiring uniform thickness and high dimensional accuracy. | Improved control over dimensions, reduced over-compression risk. | Higher cost and complexity compared to flash molds. |
Semi-Positive | Combines features of flash and positive molds, controlled material flow. | Parts requiring precision and flexibility in material flow. | Balances precision and material efficiency. | More complex than flash molds, may require fine-tuning. |
Bulk Molding | Uses a mixture of fillers, catalysts, stabilizers, pigments, and fibers. | Large, complex parts with high strength and durability. | Versatile, enhanced mechanical properties. | Requires precise control over material composition and molding conditions. |
Sheet Molding | Pre-formed sheets compressed into desired shapes. | Flat or slightly curved parts with consistent thickness. | Efficient for high-volume production, consistent material distribution. | Limited to simpler geometries, may require additional processing for complex shapes. |
Need help selecting the right compression mold for your project? Contact our experts today for personalized guidance!