Rotary vane vacuum pumps, while cost-effective and widely used, come with several disadvantages that can impact their performance, maintenance requirements, and environmental footprint. These include the need for regular oil top-ups, high operational costs, frequent maintenance, and the release of oil mist into the environment. Additionally, they produce toxic oil waste, have difficulty in sourcing replacement parts, and may not be suitable for applications requiring ultra-high vacuum levels. Understanding these drawbacks is crucial for making informed decisions when selecting vacuum pumps for specific applications.
Key Points Explained:
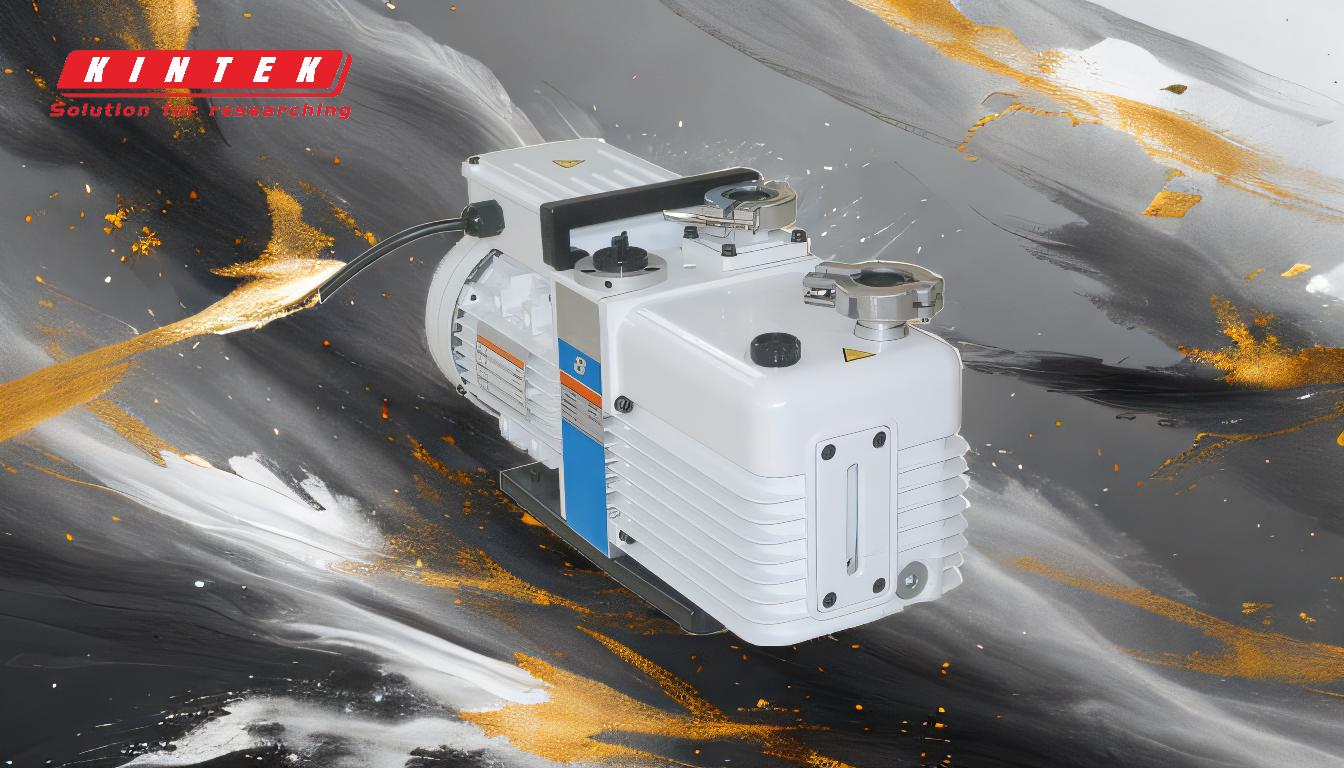
-
Regular Oil Top-Ups:
- Explanation: Oil-sealed rotary vane vacuum pumps require regular oil top-ups to maintain their efficiency. The oil acts as a sealant and lubricant, but it degrades over time and needs to be replenished.
- Impact: This requirement increases the operational burden, as users must monitor and maintain oil levels consistently. Failure to do so can lead to reduced performance or even pump failure.
-
High Operational Costs:
- Explanation: These pumps are relatively expensive to run due to the ongoing costs associated with oil changes, maintenance, and energy consumption.
- Impact: The cumulative cost over time can be significant, making them less economical compared to other types of vacuum pumps that may have lower ongoing expenses.
-
Frequent Maintenance:
- Explanation: Rotary vane vacuum pumps need regular maintenance to ensure they operate efficiently. This includes not only oil changes but also the inspection and replacement of worn parts.
- Impact: The need for frequent maintenance can lead to downtime and increased labor costs, which may be a disadvantage in environments where continuous operation is critical.
-
Release of Oil Mist:
- Explanation: Despite the use of oil filter hardware, these pumps can still release some oil mist into the immediate atmosphere.
- Impact: This can be problematic in laboratory or cleanroom environments where contamination must be minimized. The oil mist can also pose health risks to operators and damage sensitive equipment.
-
Toxic Oil Waste:
- Explanation: The used oil from these pumps is considered toxic waste and must be disposed of properly.
- Impact: Handling and disposing of toxic waste adds to the operational complexity and cost, requiring compliance with environmental regulations and proper waste management practices.
-
Difficulty in Sourcing Replacement Parts:
- Explanation: Finding replacement spare parts for rotary vane vacuum pumps can be challenging, especially for older or less common models.
- Impact: This can lead to extended downtime if parts are not readily available, affecting productivity and increasing repair costs.
-
Limited Suitability for Ultra-High Vacuum Applications:
- Explanation: While rotary vane vacuum pumps provide strong and consistent vacuum pressures, they may not be suitable for applications requiring ultra-high vacuum levels.
- Impact: For applications needing extremely low pressures, alternative pump types such as turbomolecular or cryogenic pumps may be more appropriate, limiting the versatility of rotary vane pumps in certain high-tech or research environments.
-
Environmental and Health Concerns:
- Explanation: The release of oil mist and the handling of toxic oil waste raise environmental and health concerns.
- Impact: These factors can lead to stricter regulatory compliance requirements and potential health risks for operators, making it necessary to implement additional safety measures and protocols.
In summary, while rotary vane vacuum pumps are cost-effective and widely used, their disadvantages—such as high maintenance, operational costs, environmental concerns, and limited suitability for certain applications—should be carefully considered when selecting a vacuum pump for specific needs.
Summary Table:
Disadvantage | Explanation | Impact |
---|---|---|
Regular Oil Top-Ups | Requires frequent oil replenishment for efficiency. | Increases operational burden; risk of reduced performance or pump failure. |
High Operational Costs | Ongoing costs for oil changes, maintenance, and energy consumption. | Cumulative costs make them less economical over time. |
Frequent Maintenance | Regular inspections and part replacements are necessary. | Leads to downtime and increased labor costs. |
Release of Oil Mist | Oil mist can escape into the environment despite filters. | Contaminates cleanroom environments; poses health risks. |
Toxic Oil Waste | Used oil is toxic and requires proper disposal. | Adds complexity and cost to waste management. |
Difficulty in Sourcing Parts | Replacement parts for older or less common models are hard to find. | Causes extended downtime and higher repair costs. |
Limited Suitability for Ultra-High Vacuum | Not ideal for applications requiring extremely low pressures. | Alternative pumps may be needed for high-tech applications. |
Environmental and Health Concerns | Oil mist and toxic waste raise compliance and safety issues. | Requires additional safety measures and regulatory compliance. |
Need help choosing the right vacuum pump for your application? Contact our experts today for personalized advice!