Rotary vane pumps, while widely used and cost-effective, come with several limitations that can impact their performance, maintenance, and suitability for certain applications. These limitations include the need for regular oil top-ups and maintenance, the release of oil mist into the environment, challenges with toxic oil waste disposal, difficulty in sourcing replacement parts, and sensitivity to chemical vapors. Additionally, they may not be ideal for applications requiring very high vacuum levels or those involving corrosive or reactive gases. Understanding these limitations is crucial for selecting the right pump for specific needs and ensuring efficient operation.
Key Points Explained:
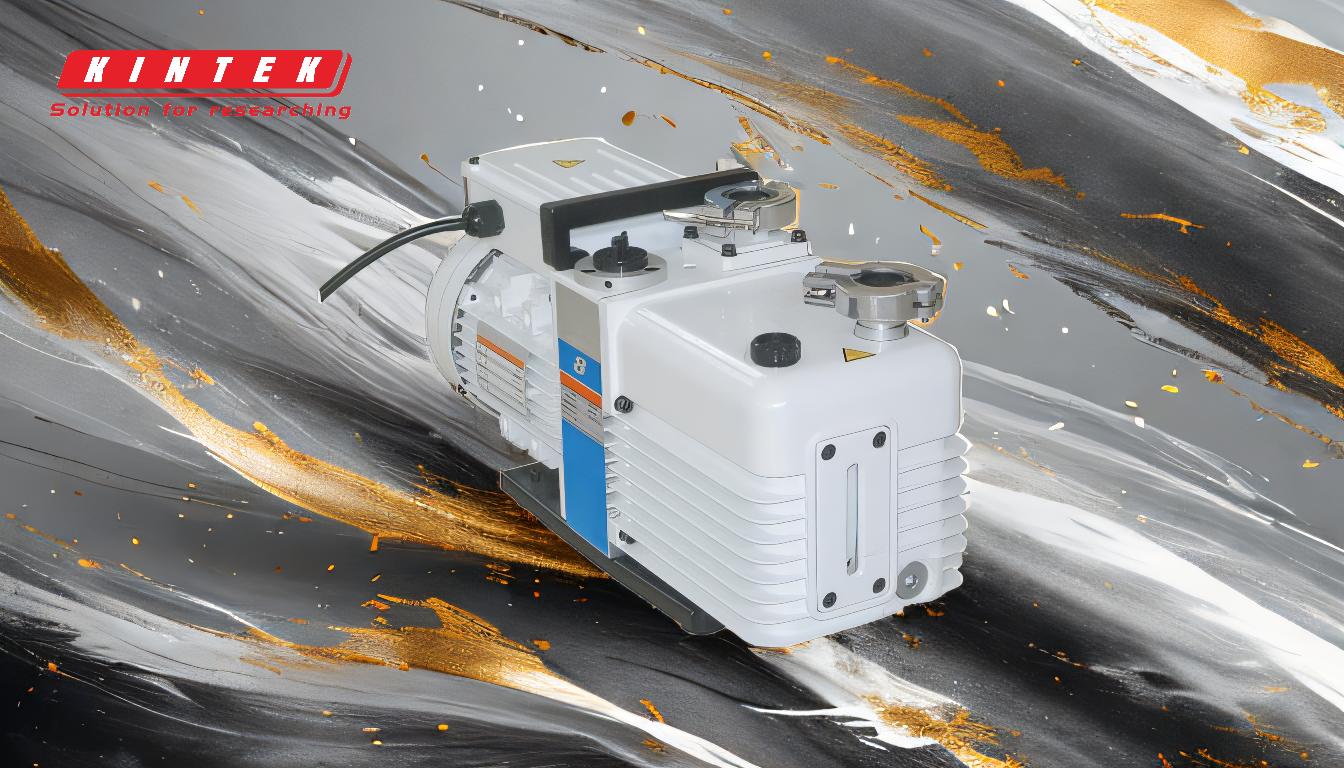
-
Oil Dependence and Maintenance Requirements:
- Rotary vane pumps are oil-sealed, meaning they rely on oil for lubrication and sealing. This necessitates regular oil top-ups and frequent maintenance to ensure proper functioning.
- The need for continuous oil replenishment increases operational costs and requires diligent monitoring to avoid pump failure.
-
Oil Mist Emission:
- Despite the use of oil filters, these pumps can release oil mist into the surrounding environment. This can be problematic in laboratory or cleanroom settings where contamination must be minimized.
- The release of oil mist also poses potential health and safety risks, especially in enclosed spaces.
-
Toxic Oil Waste Disposal:
- The used oil from rotary vane pumps can be toxic and requires proper disposal. This adds to the operational complexity and cost, as specialized waste management procedures must be followed.
- Improper disposal of oil waste can lead to environmental contamination and regulatory compliance issues.
-
Difficulty in Sourcing Replacement Parts:
- Rotary vane pumps may have limited availability of replacement parts, making repairs challenging and potentially leading to extended downtime.
- The difficulty in finding spare parts can also increase the long-term cost of ownership, as specialized components may be required.
-
Sensitivity to Chemical Vapors:
- These pumps are often exposed to chemical vapors, which can degrade the oil and other components, leading to increased maintenance requirements.
- The presence of corrosive or reactive gases can further exacerbate wear and tear, reducing the pump's lifespan and efficiency.
-
Limited Vacuum Pressure Capability:
- While rotary vane pumps are effective for many applications, they may not be suitable for processes requiring very high vacuum levels (below 10^-3 mbar).
- For applications needing higher vacuum levels, alternative pump types, such as diaphragm pumps, might be more appropriate.
-
Operational Costs:
- The combination of oil consumption, maintenance needs, and potential downtime due to part replacements makes rotary vane pumps relatively expensive to run over time.
- Users must weigh these costs against the initial purchase price when considering the total cost of ownership.
-
Environmental and Safety Concerns:
- The release of oil mist and the handling of toxic oil waste raise environmental and safety concerns, particularly in sensitive environments like laboratories or food processing facilities.
- Proper ventilation and waste management protocols are essential to mitigate these risks.
In summary, while rotary vane pumps are a popular and cost-effective choice for many vacuum applications, their limitations—such as oil dependence, maintenance requirements, environmental concerns, and sensitivity to chemical vapors—must be carefully considered. These factors can influence the suitability of rotary vane pumps for specific applications and highlight the importance of thorough evaluation before making a purchase decision.
Summary Table:
Limitation | Impact |
---|---|
Oil Dependence & Maintenance | Requires regular oil top-ups and frequent maintenance, increasing costs. |
Oil Mist Emission | Releases oil mist, posing contamination and health risks. |
Toxic Oil Waste Disposal | Complex and costly disposal process for toxic oil waste. |
Replacement Parts Availability | Limited availability, leading to potential downtime and higher costs. |
Sensitivity to Chemical Vapors | Degrades oil and components, increasing maintenance needs. |
Limited Vacuum Pressure Capability | Not suitable for very high vacuum levels (below 10^-3 mbar). |
Operational Costs | High long-term costs due to oil, maintenance, and part replacements. |
Environmental & Safety Concerns | Oil mist and toxic waste raise environmental and safety risks. |
Need help choosing the right pump for your application? Contact our experts today for personalized guidance!