Compression molds are essential tools in the manufacturing industry, particularly for shaping materials like plastics, rubber, and composites. They come in three primary types: flash molds, positive molds, and semi-positive molds. Each type has distinct characteristics, advantages, and applications. Flash molds are simple and cost-effective, allowing excess material to escape during the pressing process. Positive molds provide precise control over material flow and thickness, making them ideal for high-precision applications. Semi-positive molds strike a balance between the two, offering moderate control over material flow and thickness while being easier to manufacture than positive molds. Understanding these types helps in selecting the right mold for specific manufacturing needs.
Key Points Explained:
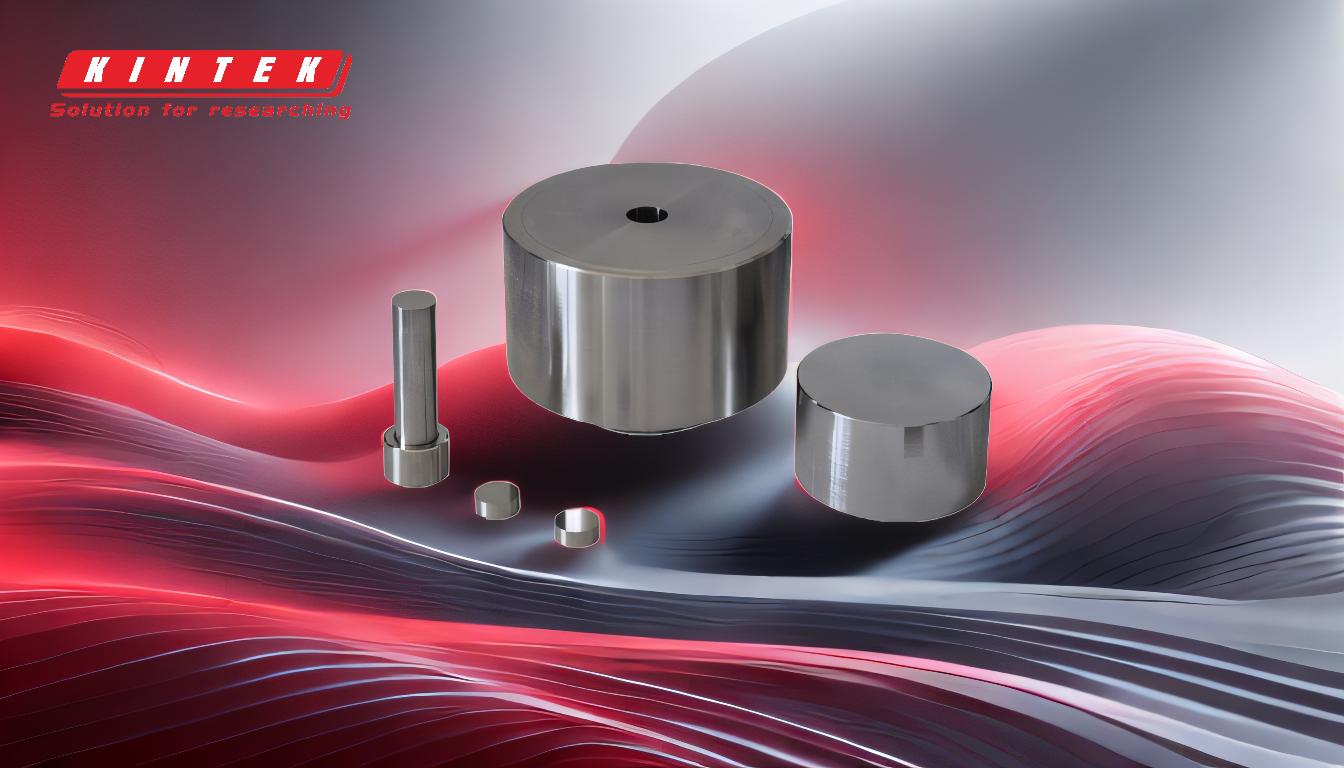
-
Flash Molds
- Structure and Cost: Flash molds have a simple structure, making them easy and inexpensive to manufacture.
- Material Flow: During the pressing process, excess material can escape or "flash" out of the mold cavity. This feature requires careful control of the closing speed to ensure proper material distribution and avoid defects.
- Applications: Ideal for less complex parts where precision is not the primary concern. Commonly used in industries where cost-effectiveness is a priority.
-
Positive Molds
- Precision and Control: Positive molds offer high precision and control over the material flow and thickness of the final product. The mold design ensures that all cavities are filled uniformly without excess material escaping.
- Complexity and Cost: These molds are more complex and expensive to manufacture compared to flash molds. They require precise engineering to achieve the desired results.
- Applications: Suitable for high-precision applications where consistency and exact dimensions are critical. Often used in industries like aerospace, automotive, and medical devices.
-
Semi-Positive Molds
- Balanced Design: Semi-positive molds combine features of both flash and positive molds. They allow some control over material flow and thickness while being easier to manufacture than fully positive molds.
- Material Management: These molds permit a small amount of excess material to escape, but not as freely as in flash molds. This balance helps in achieving better precision than flash molds without the high cost and complexity of positive molds.
- Applications: Ideal for applications that require moderate precision and cost-effectiveness. Commonly used in consumer goods and general manufacturing where a balance between quality and cost is essential.
Understanding the different types of compression molds and their specific characteristics helps manufacturers choose the right mold for their needs, ensuring optimal performance, cost-efficiency, and product quality.
Summary Table:
Type | Characteristics | Advantages | Applications |
---|---|---|---|
Flash Molds | Simple structure, allows excess material to escape | Cost-effective, easy to manufacture | Less complex parts, cost-sensitive industries |
Positive Molds | High precision, controls material flow and thickness | Uniform filling, exact dimensions | Aerospace, automotive, medical devices |
Semi-Positive Molds | Balances material flow control and ease of manufacturing | Moderate precision, cost-effective | Consumer goods, general manufacturing |
Need help selecting the right compression mold for your project? Contact our experts today!