A sputtering target is a critical component in the sputtering process, which is widely used in thin film deposition for various industries, including semiconductors, solar cells, and optical devices. The target is a solid piece of material that, when bombarded by high-energy ions, ejects atoms or molecules that form a thin film on a substrate. This process occurs in a vacuum chamber where argon gas is ionized to create a plasma, and the ions are accelerated toward the target, causing material to be sputtered. The target's shape, size, and material composition play a significant role in determining the efficiency and quality of the thin film deposition. Sputtering targets are designed to ensure precise and uniform coatings, making them essential in advanced manufacturing and technology applications.
Key Points Explained:
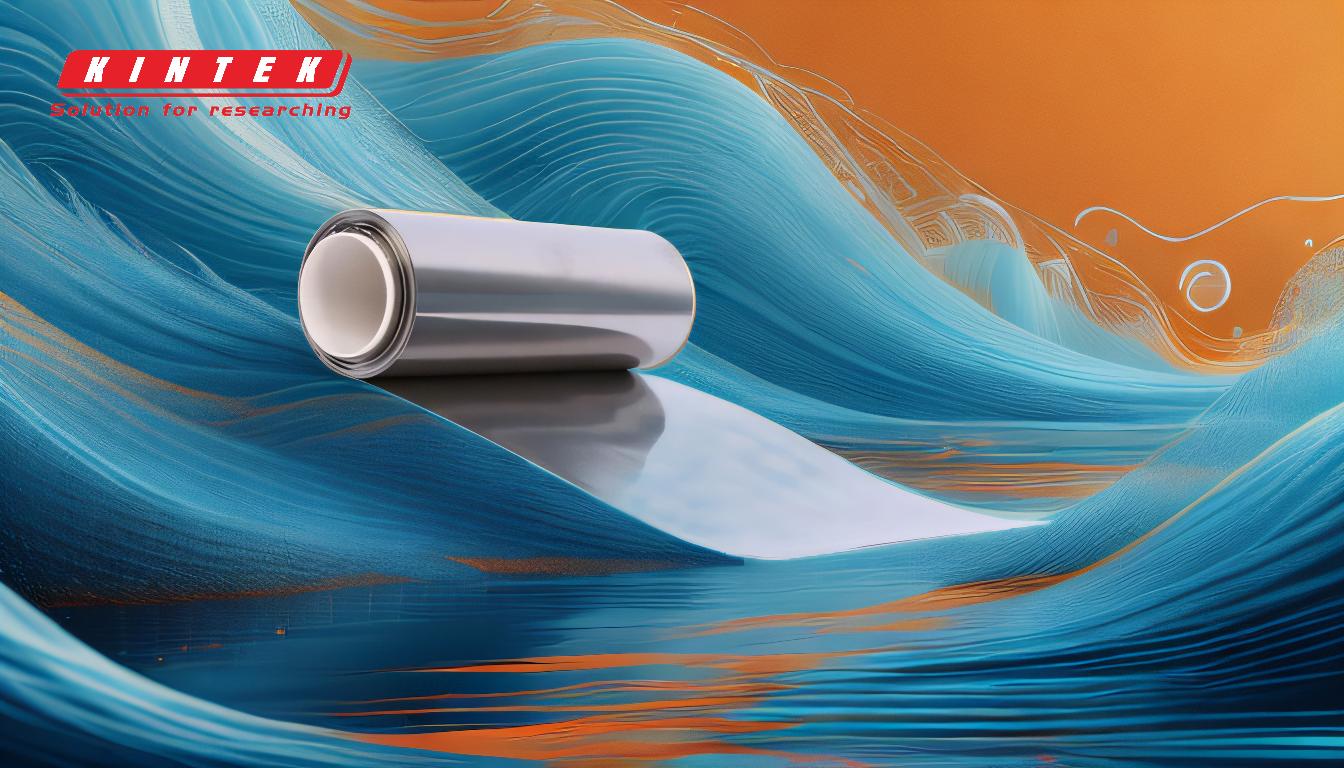
-
Definition and Role of a Sputtering Target:
- A sputtering target is a solid piece of material used in the sputtering process to create thin film coatings.
- It serves as the source of atoms or molecules that are ejected and deposited onto a substrate, forming a thin film.
- The target is typically flat or cylindrical and must be large enough to avoid unintended sputtering of other components.
-
How Sputtering Works:
- Sputtering occurs in a vacuum chamber where argon gas is introduced and ionized to create a plasma.
- A cathode is electrically energized to generate the plasma, and positively charged argon ions are accelerated toward the negatively charged target.
- The high-energy ions collide with the target, dislodging atoms or molecules that form a vapor stream.
- This vapor stream deposits onto the substrate, creating a thin film or coating.
-
Types of Sputtering Techniques:
- RF Magnetron Sputtering: This technique does not require the target to be conductive, making it suitable for a wider range of materials, including insulators.
- Rotational Sputtering: Targets shaped like long cylinders offer greater surface area and faster deposition rates compared to flat targets, improving precision and efficiency.
-
Applications of Sputtering Targets:
- Semiconductors: Sputtering targets are used to deposit thin films of conductive and insulating materials onto silicon wafers.
- Solar Cells: Targets made of materials like cadmium telluride, copper indium gallium selenide, and amorphous silicon are used to create high-efficiency thin film solar cells.
- Optical Devices: Sputtering is used to deposit thin films for applications such as CDs, disk drives, and other optical components.
-
Advantages of Sputtering Targets:
- Versatility: Sputtering targets can be made from a wide range of materials, including metals, alloys, ceramics, and compounds.
- Precision: The process allows for precise control over film thickness and composition, ensuring uniform coatings.
- Efficiency: Techniques like rotational sputtering increase deposition rates and reduce material waste.
-
Challenges and Considerations:
- Target Erosion: Over time, the target surface develops grooves or "race tracks" due to repeated ion bombardment, necessitating periodic replacement.
- Material Selection: The choice of target material depends on the desired properties of the thin film, such as conductivity, transparency, or durability.
- Process Optimization: Factors like gas pressure, voltage, and target-substrate distance must be carefully controlled to achieve optimal results.
In summary, sputtering targets are essential components in the thin film deposition process, enabling the creation of high-quality coatings for a wide range of applications. Their design, material composition, and the sputtering technique used all contribute to the efficiency and precision of the deposition process.
Summary Table:
Aspect | Details |
---|---|
Definition | Solid material used to eject atoms/molecules for thin film deposition. |
Process | High-energy ions bombard the target in a vacuum chamber, creating a plasma. |
Techniques | RF Magnetron Sputtering, Rotational Sputtering. |
Applications | Semiconductors, solar cells, optical devices. |
Advantages | Versatile, precise, efficient. |
Challenges | Target erosion, material selection, process optimization. |
Discover how sputtering targets can enhance your manufacturing process—contact our experts today!