Aluminium sputtering is a specialized form of sputter deposition, a physical vapor deposition (PVD) technique used to create thin films of aluminium on a substrate. This process involves bombarding a solid aluminium target with high-energy ions in a vacuum chamber, causing aluminium atoms to be ejected from the target and deposited onto a nearby substrate. The resulting thin film can range from a few nanometers to several micrometers in thickness. Aluminium sputtering is widely used in industries such as semiconductors, optics, and solar panels due to its ability to produce high-purity, uniform, and durable coatings. The process is particularly valued for its precision and versatility in creating advanced materials and coatings.
Key Points Explained:
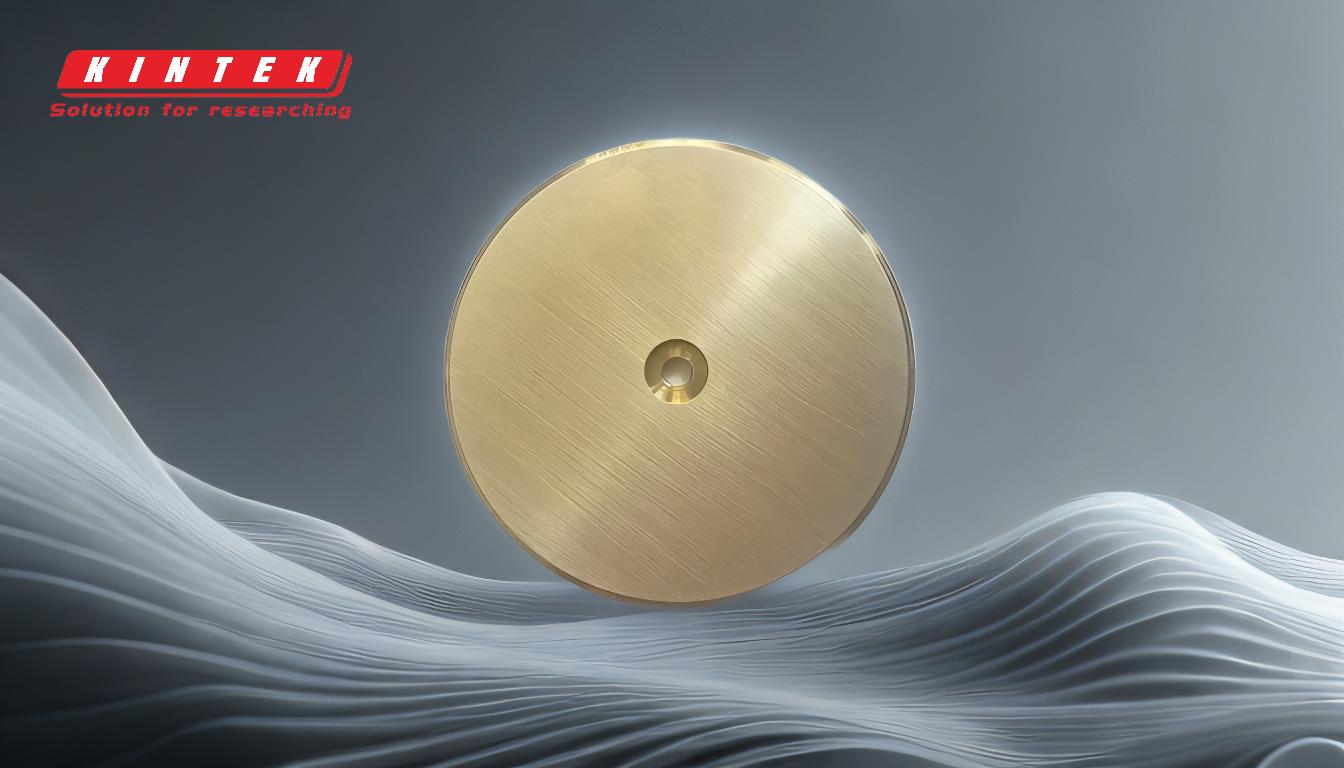
-
Definition and Process of Sputtering:
- Sputtering is a physical process where atoms from a solid target material (in this case, aluminium) are ejected into the gas phase due to bombardment by energetic ions.
- This process occurs in a vacuum chamber to ensure a controlled environment and prevent contamination.
- The ejected aluminium atoms then form a thin film on a substrate placed nearby.
-
Applications of Aluminium Sputtering:
- Semiconductor Industry: Aluminium sputtering is extensively used in the semiconductor industry to deposit thin films of aluminium in integrated circuit processing. These films are crucial for creating conductive pathways and interconnects in microelectronic devices.
- Optical Applications: Aluminium sputtering is used to deposit thin antireflection coatings on glass, enhancing the optical properties of lenses and mirrors. It is also used in the production of reflective coatings for mirrors and packaging materials.
- Solar Panels: The technique is employed in the manufacturing of photovoltaic solar cells, where aluminium films are used as back contacts to improve the efficiency of solar energy conversion.
- Data Storage: Aluminium sputtering is used in the production of CDs, DVDs, and hard disks, where thin aluminium layers are deposited to create reflective and conductive surfaces.
- Tool Coating: The process is also used to coat tool bits with aluminium-based materials, enhancing their durability and performance.
-
Advantages of Aluminium Sputtering:
- High Purity: The vacuum environment and controlled ion bombardment ensure that the deposited aluminium films are of ultra-high purity, which is essential for applications in the semiconductor and optical industries.
- Uniformity: Sputtering allows for the deposition of highly uniform thin films, which is critical for applications requiring precise thickness control, such as in semiconductor fabrication.
- Versatility: Aluminium sputtering can be used to deposit thin films on a wide range of substrates, including silicon wafers, glass, and plastics, making it a versatile technique for various industries.
- Durability: The thin films produced by sputtering are highly durable and resistant to wear, making them suitable for applications in harsh environments.
-
Technical Considerations:
- Vacuum Chamber: The process requires a high-vacuum environment to minimize contamination and ensure the quality of the deposited films.
- Ion Source: The ion source used for bombardment must be carefully controlled to achieve the desired sputtering rate and film properties.
- Substrate Preparation: The substrate must be thoroughly cleaned and prepared before deposition to ensure good adhesion and film quality.
- Process Parameters: Parameters such as ion energy, target material, and substrate temperature must be optimized to achieve the desired film properties.
-
Historical Context and Evolution:
- Sputtering as a technique has been known since the early 1800s, but its widespread industrial application began in the mid-20th century with the advent of advanced vacuum technology and ion sources.
- Over the years, the technique has evolved to become a key method for depositing thin films in various high-tech industries, including semiconductors, optics, and solar energy.
-
Future Trends:
- Advanced Materials: As the demand for advanced materials with specific properties grows, aluminium sputtering is likely to play a crucial role in the development of new alloys and composite materials.
- Miniaturization: The trend towards miniaturization in electronics and other industries will drive the need for even thinner and more precise aluminium films, further advancing sputtering technology.
- Sustainability: There is a growing focus on making sputtering processes more energy-efficient and environmentally friendly, which will likely lead to innovations in sputtering equipment and techniques.
In summary, aluminium sputtering is a highly precise and versatile technique used to deposit thin films of aluminium on various substrates. Its applications span multiple industries, including semiconductors, optics, and solar panels, and it offers numerous advantages such as high purity, uniformity, and durability. As technology continues to advance, aluminium sputtering is expected to play an increasingly important role in the development of new materials and devices.
Summary Table:
Aspect | Details |
---|---|
Definition | Physical process ejecting aluminium atoms from a target to form thin films. |
Applications | Semiconductors, optics, solar panels, data storage, tool coating. |
Advantages | High purity, uniformity, versatility, durability. |
Technical Considerations | Vacuum chamber, ion source, substrate prep, process optimization. |
Future Trends | Advanced materials, miniaturization, sustainability. |
Discover how aluminium sputtering can enhance your projects—contact our experts today!