A continuous batch reactor, often referred to as a semi-batch reactor, combines elements of both batch and continuous flow reactors. In this setup, one or more reactants are added continuously to the reactor while the reaction progresses, but the product is removed only after the reaction is complete. This hybrid approach allows for better control over reaction conditions, such as temperature and concentration, and can improve yield and efficiency compared to traditional batch reactors. Continuous batch reactors are particularly useful in processes where precise control over reactant addition is crucial, such as in polymerization or exothermic reactions. They offer a balance between the flexibility of batch reactors and the efficiency of continuous flow reactors.
Key Points Explained:
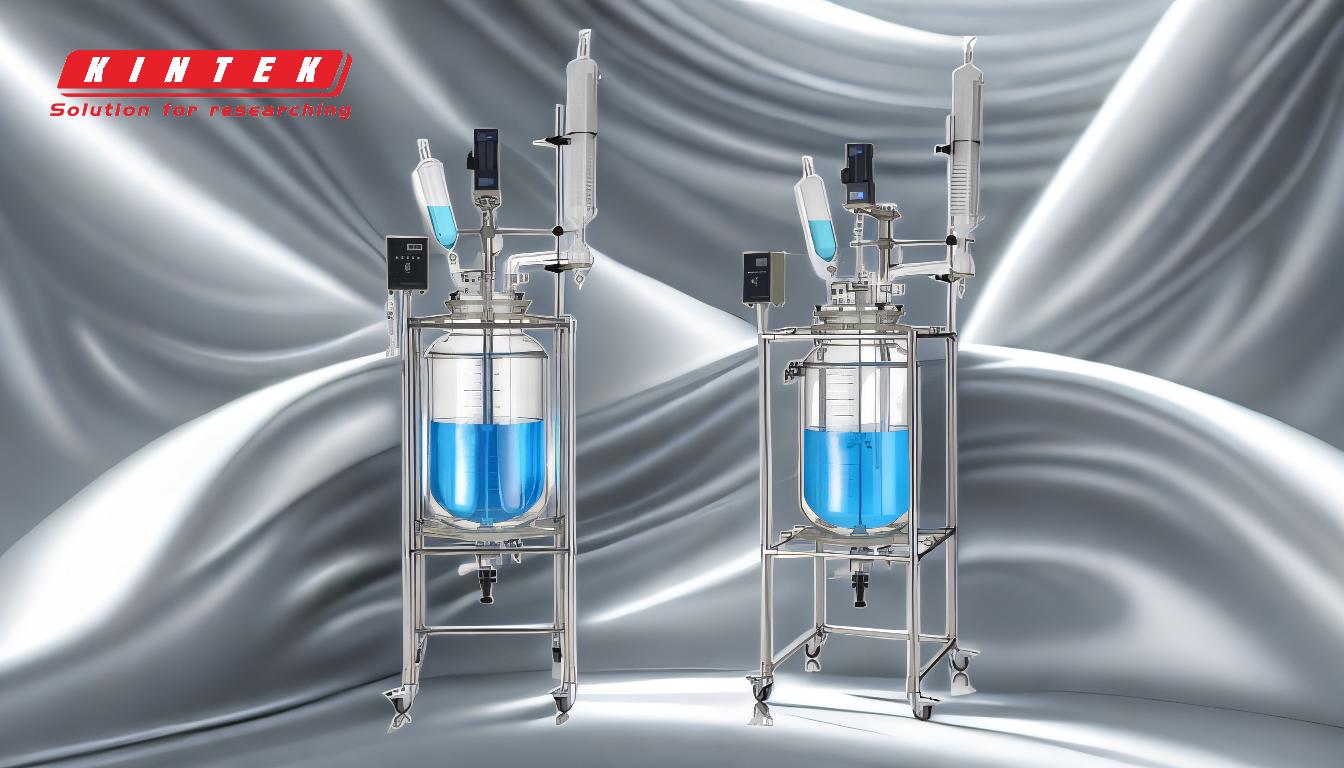
-
Definition and Operation:
- A continuous batch reactor is a hybrid system where reactants are added continuously during the reaction, but the product is removed only after the reaction is complete.
- This setup allows for better control over reaction conditions, such as temperature and concentration, which can lead to improved yields and efficiency.
-
Advantages Over Traditional Batch Reactors:
- Enhanced Control: Continuous addition of reactants allows for precise control over reaction conditions, which is particularly beneficial in exothermic reactions or processes requiring specific reactant concentrations.
- Improved Yield: By maintaining optimal reaction conditions throughout the process, continuous batch reactors can achieve higher yields compared to traditional batch reactors.
- Flexibility: Like traditional batch reactors, continuous batch reactors can handle a variety of processes without the need for redesigning the reactor.
-
Comparison with Continuous Flow Reactors:
- Efficiency: Continuous flow reactors are generally more efficient than batch reactors, but continuous batch reactors offer a middle ground by combining some of the efficiencies of continuous flow with the flexibility of batch processing.
- Material Usage: Continuous batch reactors can reduce material usage compared to traditional batch reactors, similar to continuous flow reactors, but they do not require the same level of advanced technology or infrastructure.
-
Applications:
- Polymerization: Continuous batch reactors are often used in polymerization processes where precise control over reactant addition is crucial.
- Exothermic Reactions: These reactors are ideal for exothermic reactions where controlling the reaction temperature is critical to prevent runaway reactions.
- Pharmaceutical and Food Industries: Continuous batch reactors are used in industries where flexibility and control over the reaction process are essential, such as in the production of pharmaceuticals or food products.
-
Challenges and Considerations:
- Complexity: Continuous batch reactors are more complex to design and operate compared to traditional batch reactors, requiring careful control over reactant addition and reaction conditions.
- Cost: While they can be more efficient, the initial setup and operational costs of continuous batch reactors may be higher than those of traditional batch reactors.
- Scalability: Scaling up continuous batch reactors can be challenging, as maintaining precise control over reaction conditions becomes more difficult with larger volumes.
In summary, a continuous batch reactor offers a versatile and efficient solution for processes that require precise control over reaction conditions. By combining the flexibility of batch reactors with some of the efficiencies of continuous flow reactors, they provide a balanced approach suitable for a variety of industrial applications. However, the complexity and cost associated with their design and operation should be carefully considered when choosing this type of reactor for a specific process.
Summary Table:
Aspect | Details |
---|---|
Definition | Hybrid system with continuous reactant addition and batch product removal. |
Advantages | Enhanced control, improved yield, and flexibility. |
Applications | Polymerization, exothermic reactions, pharmaceuticals, and food industries. |
Challenges | Higher complexity, cost, and scalability issues. |
Want to optimize your process with a continuous batch reactor? Contact our experts today!