Low-temperature evaporation technology is a method used to gently remove solvents or water from substances by applying controlled heat and vacuum conditions. This technique is particularly advantageous in applications like rotary evaporator cooking, where it helps preserve the taste, aroma, and nutritional value of food. By operating at lower temperatures, it ensures safer and more efficient processing, making it suitable for delicate materials and human consumption. Below, we break down the key aspects of this technology, its benefits, and its applications.
Key Points Explained:
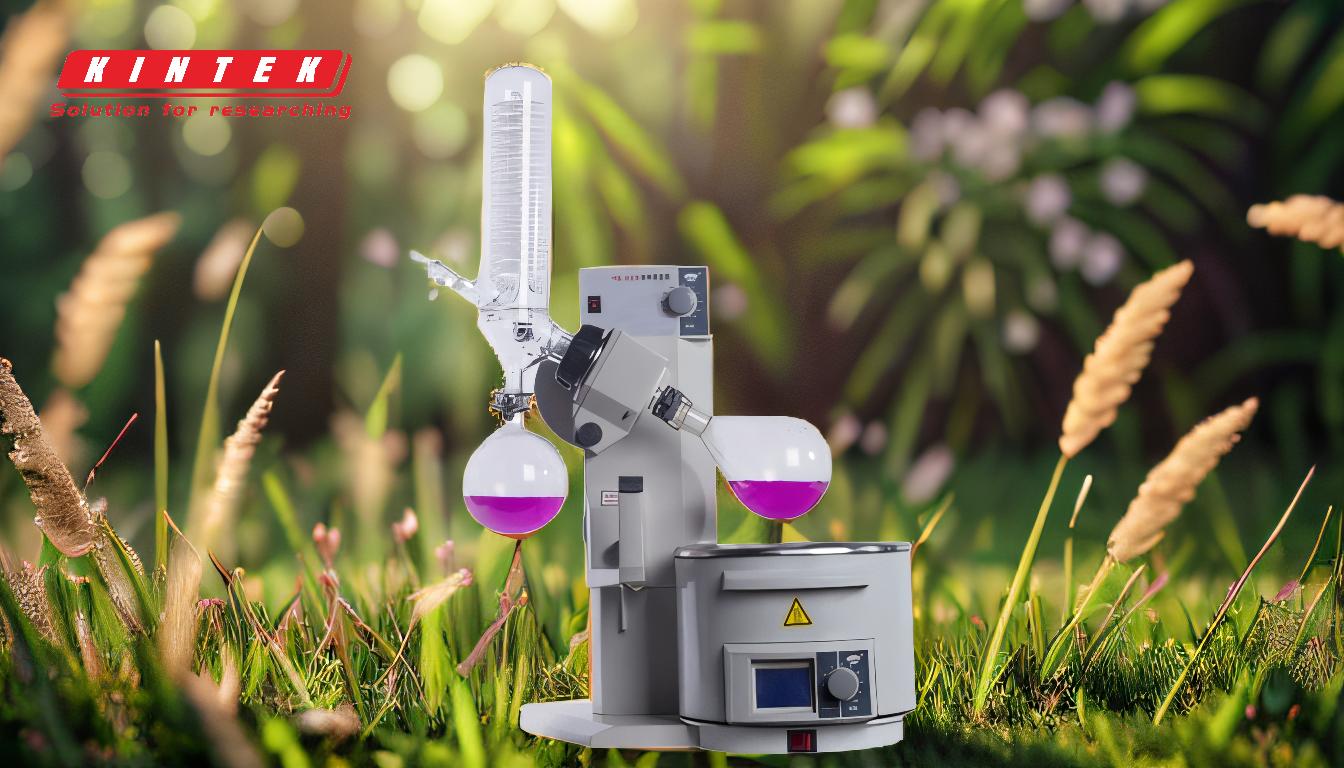
-
Definition and Principle of Low-Temperature Evaporation
- Low-temperature evaporation involves reducing the boiling point of a liquid (usually water or solvents) by lowering the pressure in the system using a vacuum. This allows evaporation to occur at temperatures far below the normal boiling point, minimizing thermal damage to the substance being processed.
- For example, water typically boils at 100°C at atmospheric pressure, but under vacuum, it can evaporate at temperatures as low as 30–40°C.
-
Applications in Rotary Evaporator Cooking
- Rotary evaporators are commonly used in culinary applications to concentrate flavors, extract essences, or create infusions. Low-temperature evaporation is ideal for this purpose because it preserves the delicate compounds responsible for taste, aroma, and nutritional value.
- This technology is particularly useful for processing heat-sensitive ingredients like herbs, spices, and fruits, which can lose their beneficial properties at high temperatures.
-
Benefits of Low-Temperature Evaporation
- Preservation of Quality: By avoiding high temperatures, the technology prevents the degradation of volatile compounds, ensuring that the final product retains its natural flavor, aroma, and nutrients.
- Energy Efficiency: Lower operating temperatures reduce energy consumption compared to traditional evaporation methods.
- Safety: The process is safer for operators and reduces the risk of overheating or burning the material being processed.
- Versatility: It can be used for a wide range of applications, from food processing to chemical and pharmaceutical industries.
-
How It Works in Practice
- The substance to be evaporated is placed in a rotating flask within the rotary evaporator.
- A vacuum pump reduces the pressure inside the system, lowering the boiling point of the liquid.
- Gentle heat is applied to the flask, causing the liquid to evaporate at a controlled, low temperature.
- The vapor is then condensed and collected in a separate flask, leaving behind a concentrated product.
-
Comparison to Traditional Evaporation Methods
- Traditional evaporation methods often require high temperatures, which can degrade sensitive compounds and alter the chemical composition of the material.
- Low-temperature evaporation, on the other hand, minimizes thermal stress, making it suitable for high-quality, heat-sensitive products.
-
Considerations for Equipment Purchasers
- When selecting equipment for low-temperature evaporation, consider factors such as:
- Vacuum Strength: A strong vacuum pump is essential for achieving the desired low boiling points.
- Temperature Control: Precise temperature regulation ensures consistent results and prevents overheating.
- Material Compatibility: Ensure the equipment is made from materials that are resistant to corrosion and chemical damage, especially if used for food or pharmaceutical applications.
- Scalability: Choose equipment that can handle the required volume and scale of your operations.
- When selecting equipment for low-temperature evaporation, consider factors such as:
-
Future Trends and Innovations
- Advances in vacuum technology and energy-efficient heating systems are making low-temperature evaporation more accessible and cost-effective.
- Integration with automation and digital controls is improving precision and reproducibility in processes.
- Growing demand for sustainable and high-quality products is driving the adoption of this technology across various industries.
In summary, low-temperature evaporation technology is a gentle and efficient method for processing heat-sensitive materials, offering significant advantages in preserving quality, ensuring safety, and reducing energy consumption. Its applications span from culinary arts to industrial processes, making it a valuable tool for professionals seeking to achieve superior results with minimal thermal impact.
Summary Table:
Aspect | Details |
---|---|
Definition | Reduces boiling point using vacuum, enabling evaporation at low temperatures. |
Applications | Rotary evaporator cooking, food processing, pharmaceuticals, and chemicals. |
Benefits | Preserves quality, energy-efficient, safe, and versatile. |
Key Considerations | Vacuum strength, temperature control, material compatibility, scalability. |
Future Trends | Advances in vacuum tech, automation, and sustainable product demand. |
Ready to explore low-temperature evaporation for your applications? Contact us today to learn more!