Sputtering of inorganic materials is a physical vapor deposition (PVD) technique used to deposit thin films of inorganic materials onto substrates. This process involves bombarding a target material with high-energy ions, typically from an inert gas like argon, in a vacuum chamber. The ions dislodge atoms from the target, which then travel through the vacuum and deposit onto a substrate, forming a thin film. Sputtering is widely used in industries such as semiconductors, optics, and aerospace for applications like integrated circuit fabrication, anti-reflective coatings, and corrosion-resistant films. It is a versatile and precise method for creating high-quality, uniform thin films of inorganic materials.
Key Points Explained:
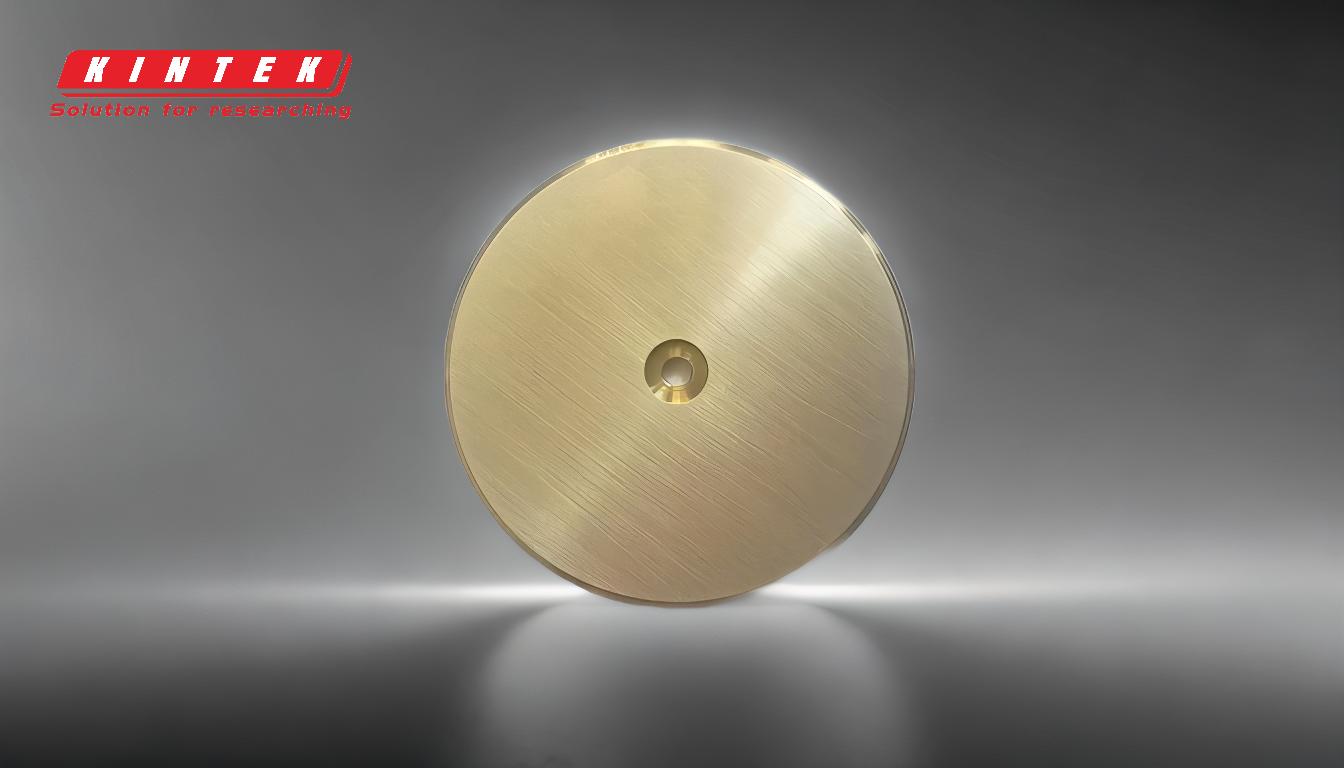
-
Definition of Sputtering:
- Sputtering is a physical vapor deposition (PVD) process where high-energy ions bombard a target material, causing atoms to be ejected from the target surface.
- These ejected atoms travel through a vacuum and deposit onto a substrate, forming a thin film.
-
Mechanism of Sputtering:
- Ion Bombardment: Inert gas ions (usually argon) are accelerated towards the target material.
- Energy Transfer: The ions transfer their kinetic energy to the target atoms, causing them to be ejected.
- Deposition: The ejected atoms travel through the vacuum and deposit onto the substrate, forming a thin film.
-
Applications of Sputtering:
- Semiconductor Industry: Sputtering is used to deposit thin films of various materials in integrated circuit processing.
- Optical Industry: It is used for depositing anti-reflective coatings on glass and producing polarization filters.
- Architectural Glass: Sputtering is used to coat large area surfaces, such as low-emissivity coatings on double-pane windows.
- Data Storage: It is used in the fabrication of CDs, DVDs, and hard disks.
- Aerospace and Defense: Sputtering is used to apply gadolinium films for neutron radiography.
- Medical Devices: It is used to produce dielectric stacks to electrically isolate surgical tools.
-
Advantages of Sputtering:
- Precision: Sputtering allows for the deposition of very thin and uniform films, ranging from a few nanometers to micrometers in thickness.
- Versatility: It can be used to deposit a wide range of materials, including metals, alloys, and ceramics.
- Quality: Sputtering produces high-quality films with excellent adhesion and uniformity.
- Complex Geometries: It can coat complex shapes and large areas uniformly.
-
Types of Sputtering:
- DC Sputtering: Uses a direct current (DC) power supply to generate the plasma.
- RF Sputtering: Uses radio frequency (RF) power to generate the plasma, suitable for insulating materials.
- Magnetron Sputtering: Uses magnetic fields to enhance the sputtering process, increasing deposition rates and improving film quality.
-
Materials Used in Sputtering:
- Target Materials: Typically inorganic materials such as metals (e.g., aluminum, gold), alloys, and ceramics (e.g., oxides, nitrides).
- Substrates: Can be various materials including silicon wafers, glass, plastics, and metals.
-
Process Parameters:
- Vacuum Level: High vacuum is required to ensure the purity of the deposited film.
- Gas Pressure: The pressure of the inert gas (usually argon) affects the sputtering rate and film quality.
- Power Supply: The type and power of the electrical supply (DC, RF) influence the sputtering process.
- Temperature: Substrate temperature can affect film properties such as adhesion and stress.
-
Historical Context:
- Sputtering has been used since the early 1800s and has evolved into a mature and widely adopted technique for thin film deposition.
- It has played a crucial role in the development of modern technologies, including semiconductors, optical coatings, and data storage devices.
-
Future Trends:
- Advanced Materials: Development of new target materials for specialized applications.
- Process Optimization: Continuous improvement in sputtering techniques to enhance film quality and deposition rates.
- Sustainability: Focus on reducing energy consumption and environmental impact of sputtering processes.
Sputtering of inorganic materials is a critical technology in modern manufacturing, enabling the production of high-performance thin films for a wide range of applications. Its precision, versatility, and ability to produce high-quality films make it indispensable in industries such as semiconductors, optics, and aerospace.
Summary Table:
Aspect | Details |
---|---|
Definition | Physical vapor deposition (PVD) process using high-energy ions to eject atoms from a target. |
Mechanism | Ion bombardment → Energy transfer → Deposition onto substrate. |
Applications | Semiconductors, optics, architectural glass, data storage, aerospace, medical devices. |
Advantages | Precision, versatility, high-quality films, uniform coating on complex shapes. |
Types | DC Sputtering, RF Sputtering, Magnetron Sputtering. |
Materials | Metals (e.g., aluminum, gold), alloys, ceramics (e.g., oxides, nitrides). |
Process Parameters | Vacuum level, gas pressure, power supply, substrate temperature. |
Discover how sputtering can enhance your manufacturing process—contact our experts today!