The primary difference between Banbury mixers and internal mixers lies in their design and operational mechanisms. Banbury mixers feature a single-axis rotor with multiple mixing blades, making them highly efficient for high-volume mixing tasks. In contrast, internal mixers, such as Rubber Intermix Internal Mixers, utilize two counter-rotating rotors with specialized blade configurations, offering better control over mixing parameters and uniformity. These differences impact their applications, efficiency, and suitability for specific mixing tasks in industries like rubber and polymer processing.
Key Points Explained:
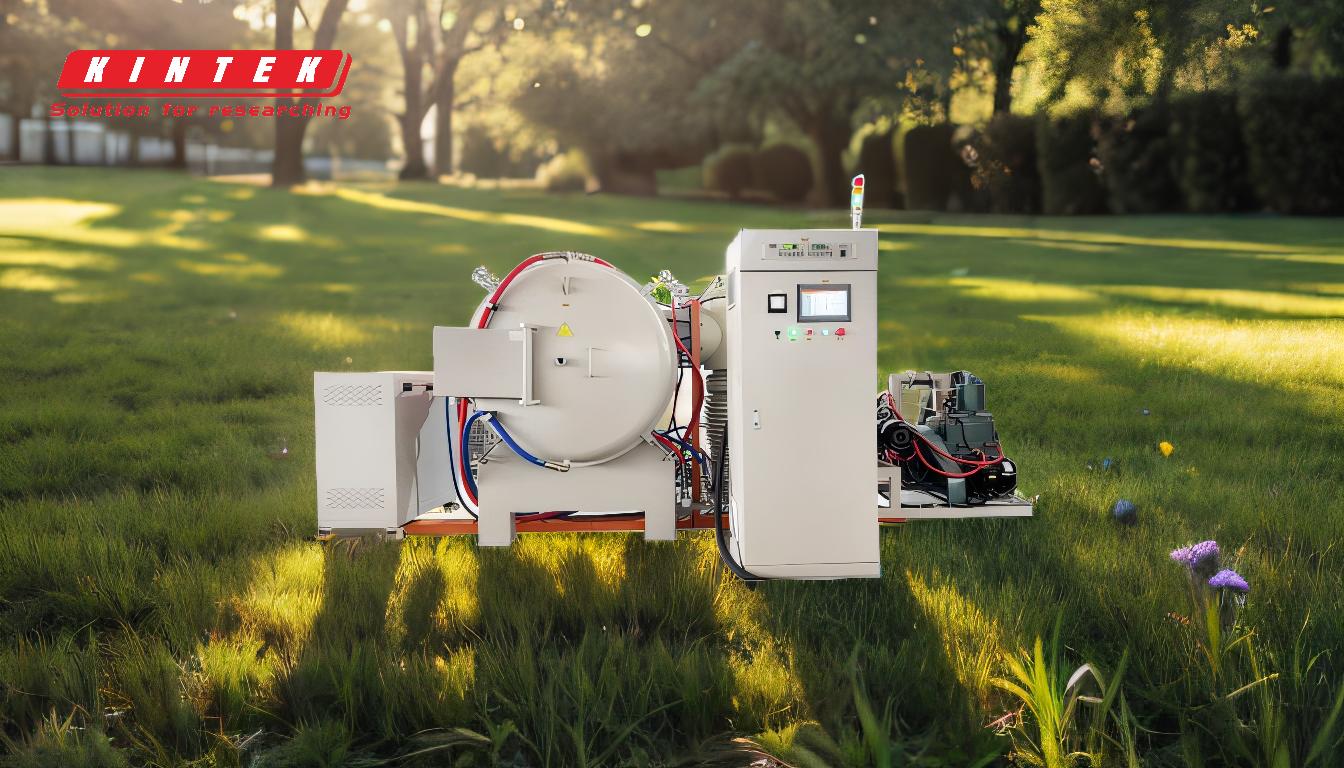
-
Design and Rotor Configuration:
- Banbury Mixers: Equipped with a single-axis rotor with multiple mixing blades, Banbury mixers are designed for high-volume mixing. The single-axis design allows for efficient energy transfer and consistent mixing.
- Internal Mixers: These mixers, like the Rubber Intermix Internal Mixers, feature two counter-rotating rotors with specialized blade configurations. The dual-rotor design enhances mixing uniformity and allows for better control over the mixing process.
-
Operational Mechanism:
- Banbury Mixers: The single-axis rotor design facilitates a straightforward and robust mixing process, ideal for large-scale production where consistency and speed are critical.
- Internal Mixers: The counter-rotating rotors create a more dynamic mixing environment, which can be adjusted to achieve specific mixing characteristics, making them suitable for more complex mixing tasks.
-
Application Suitability:
- Banbury Mixers: Best suited for industries requiring high-volume production with consistent quality, such as in the rubber and polymer industries.
- Internal Mixers: More versatile, these mixers are ideal for applications requiring precise control over mixing parameters, such as in the production of specialized rubber compounds or polymers.
-
Efficiency and Control:
- Banbury Mixers: Known for their efficiency in large-scale operations, they provide consistent results with relatively simple controls.
- Internal Mixers: Offer greater control over the mixing process, allowing for adjustments in rotor speed, temperature, and other parameters to achieve desired outcomes.
-
Maintenance and Durability:
- Banbury Mixers: Generally require less maintenance due to their simpler design and are known for their durability in high-volume applications.
- Internal Mixers: While they may require more frequent maintenance due to their complex design, they offer greater flexibility and precision in mixing tasks.
Understanding these key differences helps in selecting the appropriate mixer based on specific production needs, ensuring optimal performance and quality in the final product.
Summary Table:
Feature | Banbury Mixers | Internal Mixers |
---|---|---|
Rotor Configuration | Single-axis rotor with multiple blades | Two counter-rotating rotors with specialized blades |
Operational Mechanism | Straightforward, high-volume mixing | Dynamic, adjustable mixing environment |
Application Suitability | High-volume production (rubber, polymers) | Precise control for specialized compounds |
Efficiency and Control | Consistent results, simple controls | Greater control over mixing parameters |
Maintenance and Durability | Less maintenance, durable for high-volume | More frequent maintenance, greater flexibility |
Need help choosing the right mixer for your production? Contact our experts today for personalized advice!