In sputtering, inert gases like argon and xenon are primarily used because they do not react chemically with the target material or process gases, ensuring a purely physical deposition process. Argon is the most commonly used inert gas due to its high molecular weight, which enhances sputtering and deposition rates. The process involves creating a vacuum in the chamber and introducing the inert gas to form plasma, which facilitates the sputtering of target material onto a substrate. This method is widely used in thin-film deposition for applications in electronics, optics, and coatings.
Key Points Explained:
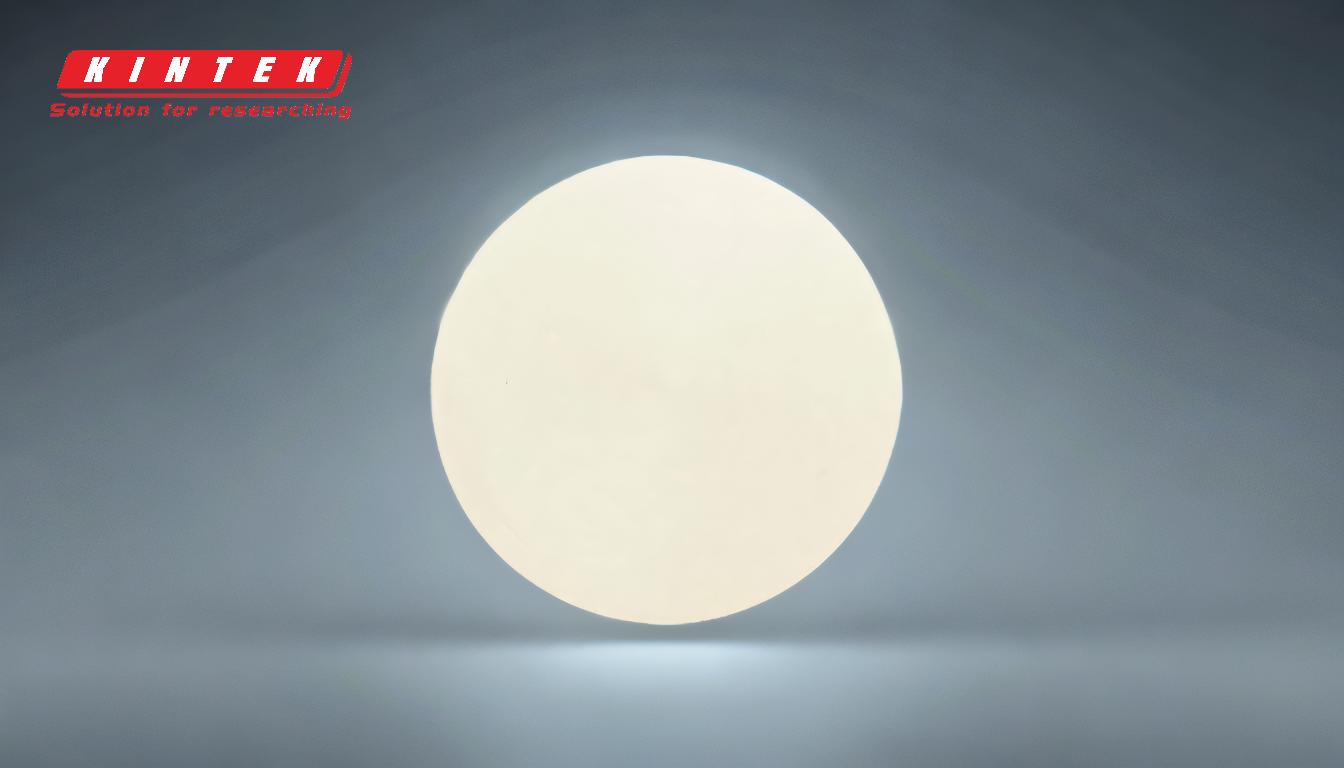
-
Definition of Sputtering:
- Sputtering is a physical vapor deposition (PVD) technique used to deposit thin films of material onto a substrate. It involves bombarding a target material with high-energy ions, causing atoms to be ejected from the target and deposited onto the substrate.
-
Role of Inert Gases in Sputtering:
- Inert gases are used in sputtering because they do not react chemically with the target material or other process gases. This ensures that the deposition process is purely physical, avoiding unwanted chemical reactions that could alter the properties of the deposited film.
-
Commonly Used Inert Gases:
- Argon (Ar): The most commonly used inert gas in sputtering due to its high molecular weight, which results in higher sputtering and deposition rates. Argon is also relatively inexpensive and readily available.
- Xenon (Xe): Occasionally used in specialized applications where higher sputtering rates are required. Xenon has an even higher molecular weight than argon, which can lead to more efficient sputtering, but it is more expensive.
-
Process of Using Inert Gases in Sputtering:
- Vacuum Creation: The sputtering chamber is first evacuated to create a low-pressure environment.
- Introduction of Inert Gas: An inert gas, typically argon, is introduced into the chamber at a controlled pressure.
- Plasma Formation: A high-voltage electric field is applied to ionize the inert gas, creating a plasma. The ions in the plasma are then accelerated towards the target material.
- Sputtering: The high-energy ions collide with the target material, causing atoms to be ejected and deposited onto the substrate.
-
Advantages of Using Inert Gases:
- Chemical Inertness: Inert gases do not react with the target material or other process gases, ensuring a clean deposition process.
- High Sputtering Rates: The high molecular weight of inert gases like argon and xenon results in more efficient sputtering and higher deposition rates.
- Controlled Deposition: The use of inert gases allows for precise control over the deposition process, leading to high-quality thin films with desired properties.
-
Applications of Sputtering with Inert Gases:
- Electronics: Used in the fabrication of semiconductor devices, thin-film transistors, and magnetic storage media.
- Optics: Applied in the production of anti-reflective coatings, optical filters, and mirrors.
- Coatings: Used for decorative coatings, wear-resistant coatings, and barrier layers in packaging materials.
-
Considerations for Equipment and Consumable Purchasers:
- Gas Purity: Ensure that the inert gas used is of high purity to avoid contamination of the deposited film.
- Gas Supply: Consider the availability and cost of the inert gas, especially for large-scale or continuous operations.
- Chamber Design: The sputtering chamber should be designed to maintain a stable vacuum and allow for precise control of gas pressure and flow.
- Target Material Compatibility: Ensure that the target material is compatible with the chosen inert gas to achieve the desired deposition properties.
In summary, inert gases like argon and xenon are essential in the sputtering process due to their chemical inertness and high molecular weight, which facilitate efficient and controlled thin-film deposition. Argon is the most commonly used gas due to its cost-effectiveness and availability, while xenon is used in specialized applications requiring higher sputtering rates. Understanding the role and selection of inert gases is crucial for optimizing the sputtering process and achieving high-quality thin films for various applications.
Summary Table:
Aspect | Details |
---|---|
Inert Gases Used | Argon (most common), Xenon (specialized) |
Key Role | Prevent chemical reactions, enable physical deposition |
Process Steps | Vacuum creation, inert gas introduction, plasma formation, sputtering |
Advantages | Chemical inertness, high sputtering rates, controlled deposition |
Applications | Electronics, optics, coatings |
Considerations | Gas purity, supply, chamber design, target material compatibility |
Optimize your sputtering process with the right inert gases—contact our experts today for tailored solutions!