The lifetime of a sputtering target is influenced by a variety of factors, including material properties, manufacturing processes, and operational conditions. Key determinants include the target's purity, grain size, surface condition, and manufacturing technology, which affect its performance and longevity. Operational factors such as sputtering rate, ion current density, and usage optimization techniques also play a significant role. By understanding and controlling these factors, the lifespan of a sputtering target can be maximized, ensuring efficient and cost-effective thin film deposition processes.
Key Points Explained:
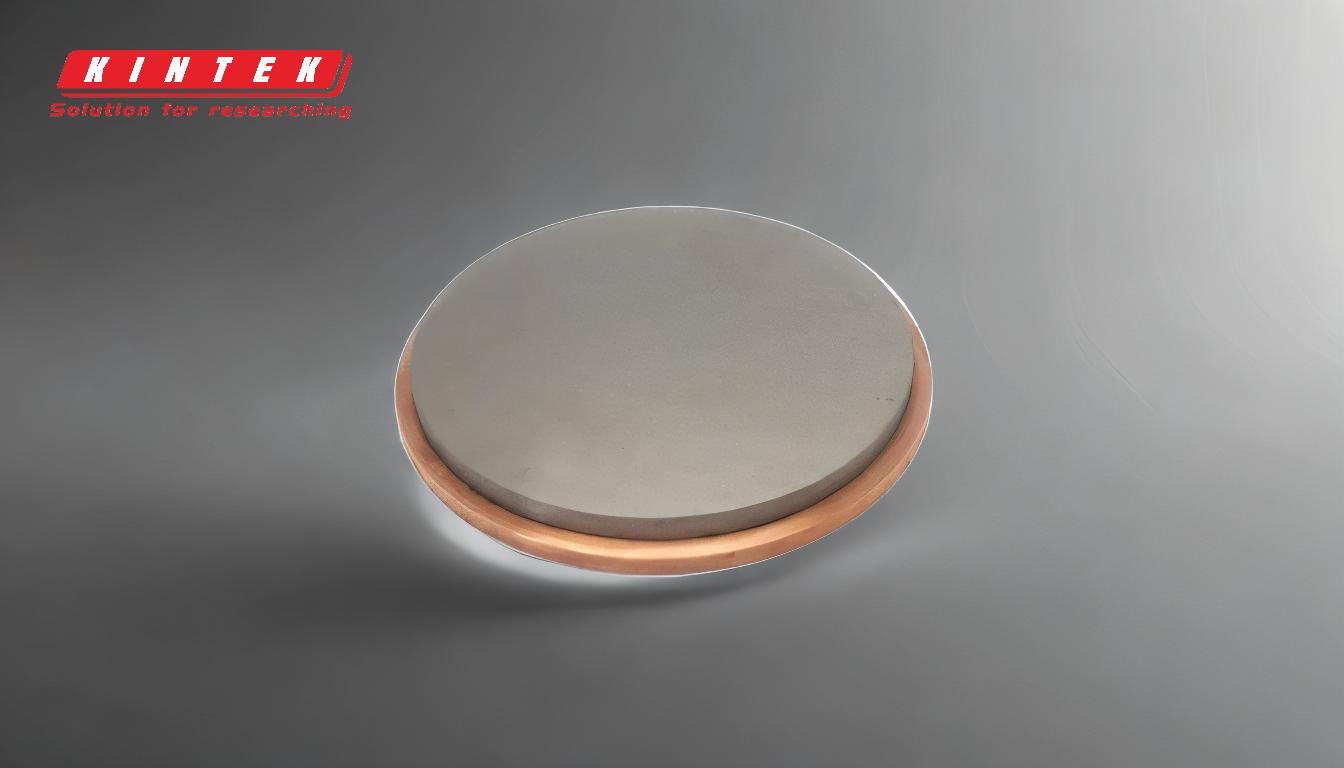
-
Material Properties:
- Purity: High-purity targets are essential for producing defect-free thin films. Impurities can lead to defects in the deposited film, reducing the target's effective lifespan.
- Grain Size: Smaller grain sizes generally result in better film properties and can enhance the target's durability and performance.
- Surface Condition: A smooth surface minimizes defects in the thin film and can extend the target's usable life.
-
Manufacturing Technology:
- VIM Casting, Hot Pressing, Powder Processing: The choice of manufacturing method affects the target's grain structure, oxygen content, and overall stability. These factors influence the target's suitability for specific applications and its longevity.
- Material Stability: Targets produced with stable materials and controlled processes are less prone to degradation over time.
-
Operational Factors:
- Sputtering Rate: Defined by the equation ( \text{Sputtering rate} = \frac{MSj}{pNAe} ), where ( M ) is the molar weight, ( S ) is the sputter yield, ( j ) is the ion current density, ( p ) is the material density, ( NA ) is the Avogadro number, and ( e ) is the electron charge. Higher sputtering rates can lead to faster target depletion.
- Ion Current Density: Higher ion current densities increase the sputtering rate, potentially reducing the target's lifespan.
-
Usage Optimization:
- Distance and Coating Thickness: Reducing the distance from the target to the sample and optimizing coating thickness can enhance target usage efficiency.
- Thickness Monitoring: Using a thickness monitor helps in achieving the optimum coating thickness, reducing unnecessary target wear.
- Multiple Samples: Coating multiple samples in a single cycle maximizes target utilization.
- Argon Pressure: Lowering the pressure of Argon in the sample chamber can improve sputtering efficiency and extend target life.
- Material Choice: Using cost-effective materials like Silver and Argon as the sputter gas can also contribute to longer target life.
- Target Maintenance: Cleaning the target surface outside the racetrack area and using thicker targets can further increase cost efficiency and lifespan.
-
Composition and Ion Type:
- Material Composition: The effectiveness and longevity of a sputtering target are influenced by its composition. Different materials have varying sputtering yields and durability.
- Ion Type: The type of ions used in the sputtering process can affect the target's wear rate. Choosing appropriate ions for the target material can help in maintaining its integrity over time.
By carefully considering these factors and implementing best practices in both the selection and use of sputtering targets, their lifetime can be significantly extended, leading to more efficient and economical thin film deposition processes.
Summary Table:
Factor | Impact on Target Lifespan |
---|---|
Material Properties | High purity, small grain size, and smooth surfaces enhance durability and performance. |
Manufacturing Process | VIM casting, hot pressing, and powder processing affect grain structure and material stability. |
Operational Factors | Sputtering rate and ion current density directly influence target depletion. |
Usage Optimization | Optimizing distance, coating thickness, and argon pressure extends target life. |
Composition & Ion Type | Material composition and ion type affect wear rate and target integrity. |
Optimize your sputtering process and extend target lifespan—contact our experts today for tailored solutions!