Aluminum sputtering is a physical vapor deposition (PVD) technique used to deposit thin films of aluminum onto substrates. The process involves bombarding a solid aluminum target with high-energy ions, typically from an inert gas like argon, in a vacuum chamber. These ions dislodge aluminum atoms from the target, which then travel through the vacuum and deposit onto the substrate, forming a thin, uniform film. The process is highly precise and is widely used in industries such as semiconductors, optics, and coatings. Key steps include creating a vacuum, ionizing the sputtering gas, bombarding the target, and depositing the aluminum onto the substrate.
Key Points Explained:
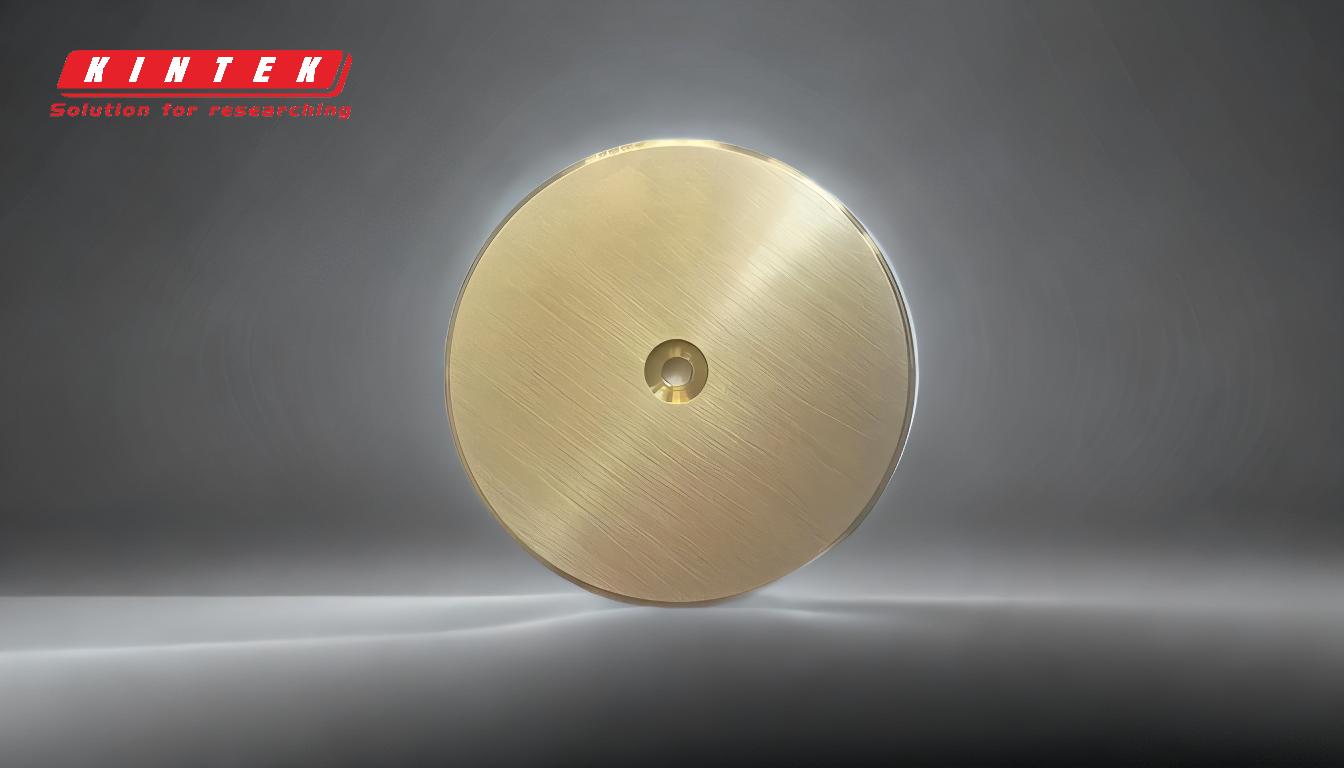
-
Overview of Sputtering:
- Sputtering is a PVD process where a target material (in this case, aluminum) is bombarded with high-energy ions, causing atoms to be ejected and deposited onto a substrate.
- It is a versatile and precise method for creating thin films with excellent uniformity and adhesion.
-
Setup and Components:
- Vacuum Chamber: The process takes place in a vacuum chamber to minimize contamination and ensure a controlled environment.
- Target Material: The aluminum target is placed in the chamber, acting as the cathode.
- Substrate: The material to be coated is placed opposite the target, acting as the anode.
- Sputtering Gas: Inert gases like argon are introduced into the chamber and ionized to create plasma.
-
Key Steps in Aluminum Sputtering:
- Creating a Vacuum: The chamber is evacuated to remove air and other contaminants, ensuring a clean environment for the process.
- Ionizing the Gas: A voltage is applied between the target and substrate, ionizing the sputtering gas (e.g., argon) to create a plasma.
- Bombarding the Target: The ionized gas atoms are accelerated toward the aluminum target, dislodging aluminum atoms through momentum transfer.
- Transport and Deposition: The ejected aluminum atoms travel through the vacuum and deposit onto the substrate, forming a thin film.
-
Types of Sputtering Techniques:
- Magnetron Sputtering: Uses magnetic fields to enhance ionization efficiency and deposition rates.
- Reactive Sputtering: Introduces reactive gases (e.g., oxygen or nitrogen) to form compound films (e.g., aluminum oxide or nitride).
- Ion Beam Sputtering: Employs a focused ion beam for precise control over film properties.
- Gas Flow Sputtering: Uses a directed flow of gas to improve film uniformity.
-
Advantages of Aluminum Sputtering:
- Precision: Produces highly uniform and controlled thin films.
- Versatility: Suitable for a wide range of substrates and applications.
- Adhesion: Provides excellent adhesion between the film and substrate.
- Purity: Minimizes contamination due to the vacuum environment.
-
Applications:
- Semiconductors: Used for creating conductive layers and interconnects.
- Optics: Deposits reflective and anti-reflective coatings.
- Coatings: Provides protective and decorative coatings for various materials.
- Energy: Used in solar cells and battery technologies.
-
Challenges and Considerations:
- Cost: Requires specialized equipment and controlled environments, making it relatively expensive.
- Complexity: Involves precise control of parameters like pressure, voltage, and gas flow.
- Target Erosion: The target material erodes over time and must be replaced periodically.
By understanding these key points, a purchaser can evaluate the suitability of aluminum sputtering for their specific needs and ensure the process is optimized for their application.
Summary Table:
Aspect | Details |
---|---|
Process | Physical vapor deposition (PVD) using high-energy ions to deposit aluminum. |
Key Components | Vacuum chamber, aluminum target, substrate, sputtering gas (e.g., argon). |
Steps | 1. Create a vacuum. 2. Ionize gas. 3. Bombard target. 4. Deposit aluminum. |
Techniques | Magnetron, reactive, ion beam, gas flow sputtering. |
Advantages | Precision, versatility, excellent adhesion, high purity. |
Applications | Semiconductors, optics, coatings, energy (solar cells, batteries). |
Challenges | Cost, complexity, target erosion. |
Discover how aluminum sputtering can enhance your projects—contact our experts today!