The sputtering target process is a highly precise and controlled method used to deposit thin films of material onto a substrate. It involves placing a target material and a substrate in a vacuum chamber, creating a plasma of inert gas (typically argon), and accelerating ions from the plasma toward the target. These ions bombard the target, causing atoms to be ejected and deposited onto the substrate as a thin film. The process is widely used in industries such as semiconductors, optics, and coatings due to its accuracy and ability to produce uniform layers.
Key Points Explained:
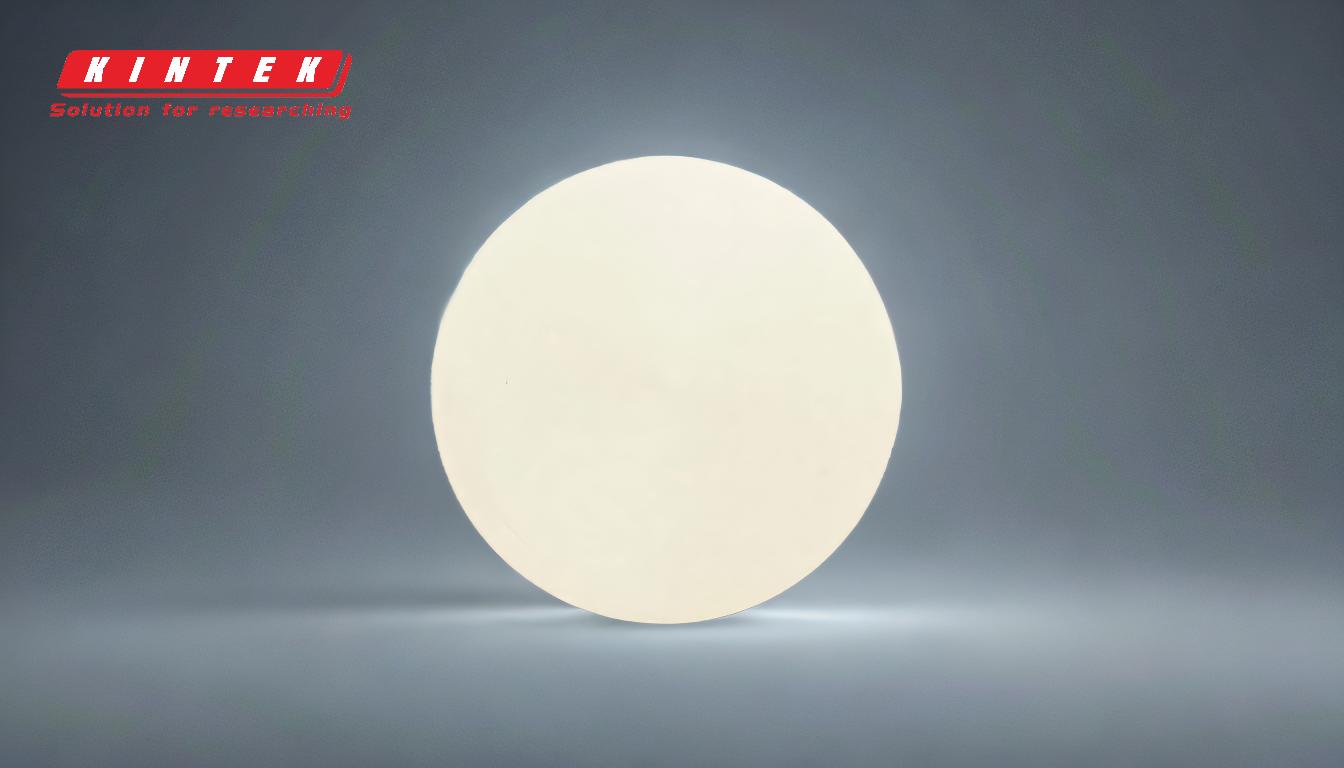
-
Setup of the Vacuum Chamber:
- The sputtering process begins with placing the target material (source) and the substrate (destination) inside a vacuum chamber.
- The chamber is evacuated to remove almost all air molecules, creating a low-pressure environment.
- This vacuum is essential to minimize contamination and ensure the purity of the deposited film.
-
Introduction of Inert Gas:
- After creating the vacuum, the chamber is backfilled with an inert gas, typically argon, though other gases like xenon, oxygen, or nitrogen may also be used depending on the application.
- The choice of gas depends on the desired properties of the thin film and the target material.
-
Creation of Plasma:
- A voltage is applied between the target (cathode) and the substrate (anode), ionizing the inert gas and creating a plasma.
- The plasma consists of positively charged ions and free electrons, which are essential for the sputtering process.
-
Ion Bombardment of the Target:
- The positively charged ions from the plasma are accelerated toward the negatively charged target due to the electrical field.
- When these ions collide with the target, they transfer their kinetic energy, causing atoms or molecules of the target material to be ejected (sputtered).
-
Ejection and Deposition of Target Material:
- The ejected target atoms travel through the vacuum chamber in the form of neutral particles.
- These particles condense onto the substrate, forming a thin, uniform film.
- The process is highly controlled, allowing for precise thickness and composition of the deposited layer.
-
Control and Precision:
- The sputtering process is adjustable by controlling parameters such as voltage, gas pressure, and target-substrate distance.
- This control ensures the production of high-quality films with specific properties, such as conductivity, reflectivity, or durability.
-
Applications of Sputtering:
- Sputtering is widely used in industries such as semiconductors (for creating integrated circuits), optics (for anti-reflective coatings), and decorative coatings (for mirrors or architectural glass).
- It is also used in the production of precision components, where uniform and defect-free coatings are critical.
-
Advantages of Sputtering:
- The process allows for the deposition of a wide range of materials, including metals, alloys, ceramics, and compounds.
- It produces films with excellent adhesion, uniformity, and density.
- Sputtering is compatible with complex geometries, making it versatile for various applications.
By following these steps, the sputtering target process achieves the deposition of high-quality thin films, making it a cornerstone of modern manufacturing and technology.
Summary Table:
Step | Description |
---|---|
Vacuum Chamber Setup | Target and substrate placed in a vacuum to minimize contamination. |
Inert Gas Introduction | Argon or other gases are introduced to create a plasma environment. |
Plasma Creation | Voltage ionizes the gas, forming a plasma of ions and electrons. |
Ion Bombardment | Ions accelerate toward the target, ejecting atoms for deposition. |
Deposition of Thin Film | Ejected atoms condense onto the substrate, forming a uniform film. |
Control & Precision | Adjustable parameters ensure high-quality films with specific properties. |
Applications | Used in semiconductors, optics, and coatings for precise, uniform layers. |
Advantages | Versatile, compatible with complex geometries, and produces dense, uniform films. |
Discover how the sputtering target process can enhance your manufacturing—contact us today!