XRF (X-ray Fluorescence) films or coatings are typically measured in terms of thickness, and the range of measurable thicknesses depends on the specific application and the elements involved. Handheld XRF devices can measure thicknesses ranging from 0.001 mm (1 µm) to 0.01 mm (10 µm), which is suitable for common surface engineering techniques like plating, vapor deposition, and resin bonding. However, XRF technology as a whole can detect thicknesses from as low as 1 nm up to 50 µm. Below 1 nm, the signal is too weak to distinguish from noise, and above 50 µm, the X-rays cannot penetrate the coating effectively to provide accurate measurements.
Key Points Explained:
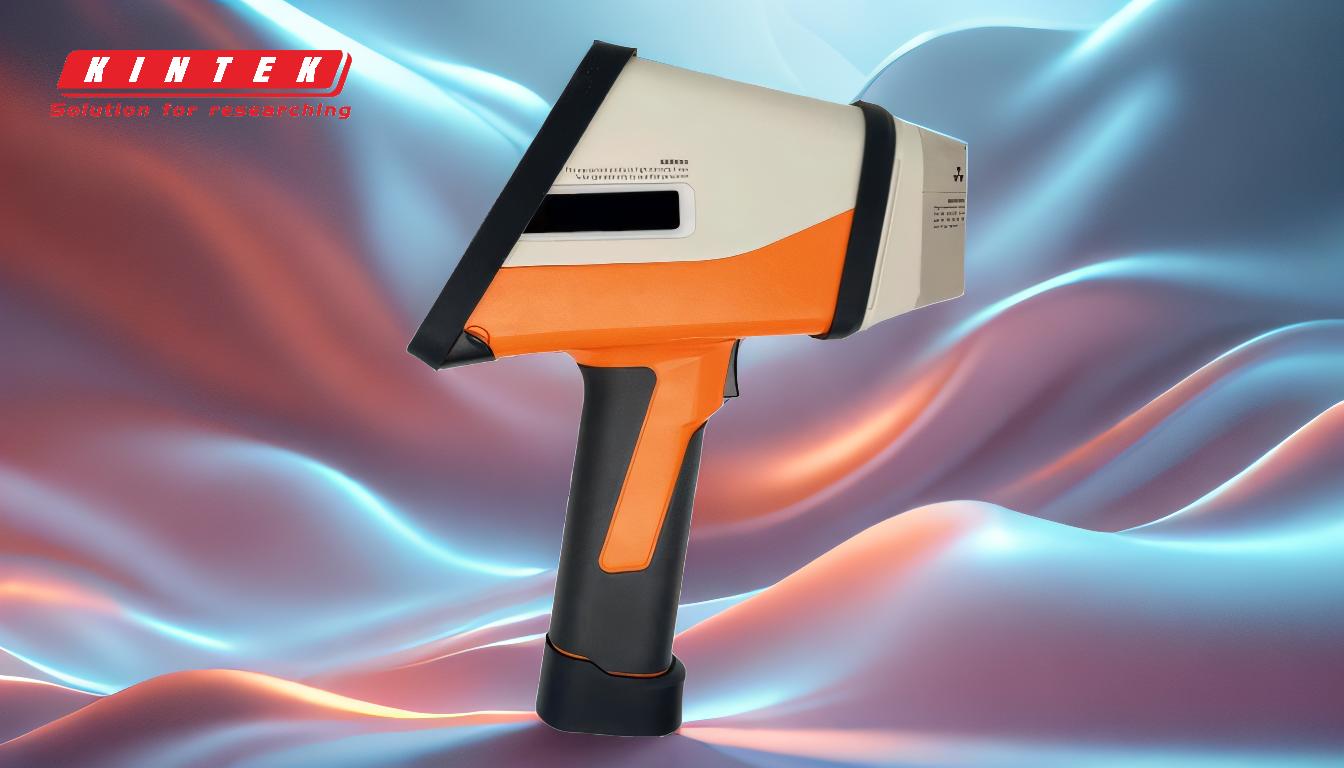
-
Thickness Range of XRF Films:
- XRF films or coatings can be measured in a wide range of thicknesses, depending on the technology and application.
- Handheld XRF devices typically measure thicknesses between 0.001 mm (1 µm) and 0.01 mm (10 µm).
- General XRF technology can detect thicknesses from 1 nm to 50 µm.
-
Lower Limit of Detection:
- The lower limit for XRF measurement is approximately 1 nm.
- Below this thickness, the characteristic X-rays emitted by the coating material are too weak to be distinguished from background noise, making accurate measurement impossible.
-
Upper Limit of Detection:
- The upper limit for XRF measurement is around 50 µm.
- Beyond this thickness, the X-rays cannot penetrate the coating effectively to reach the inner layers, preventing accurate measurement of thicker coatings.
-
Applications and Techniques:
- XRF is commonly used for measuring coatings applied through techniques such as plating, vapor deposition, and resin or lacquer bonding.
- These techniques often result in coatings within the measurable range of XRF devices, making it a versatile tool for quality control and process monitoring.
-
Factors Affecting Measurement:
- The measurable thickness range depends on the element being measured and the specific XRF device used.
- Different elements have varying X-ray emission characteristics, which can influence the detectable thickness range.
By understanding these key points, purchasers of XRF equipment or consumables can make informed decisions about the suitability of XRF technology for their specific coating thickness measurement needs.
Summary Table:
Aspect | Details |
---|---|
Thickness Range (Handheld XRF) | 0.001 mm (1 µm) to 0.01 mm (10 µm) |
Thickness Range (General XRF) | 1 nm to 50 µm |
Lower Limit of Detection | 1 nm (below this, signals are too weak) |
Upper Limit of Detection | 50 µm (beyond this, X-rays cannot penetrate effectively) |
Common Applications | Plating, vapor deposition, resin/lacquer bonding |
Key Factors | Element being measured, specific XRF device used |
Ensure precise coating measurements with XRF technology—contact our experts today for tailored solutions!