Rotary vacuum pumps, particularly rotary vane vacuum pumps, are essential tools in various industries due to their ability to create strong and consistent vacuum pressures. These pumps are oil-sealed and are commonly used in applications requiring vacuum pressures below 10⁻³ mbar, such as in hydraulic braking systems, freeze dryers, and mass spectrometry. They operate by using a rotating mechanism with vanes that move radially to create a vacuum. Despite their effectiveness, they have some drawbacks, such as the need to handle toxic oil waste and challenges in finding replacement parts. Rotary vacuum pumps are versatile and find applications in fields like laboratories, medical and pharmaceutical industries, and filtration, where specific vacuum levels are required for different processes.
Key Points Explained:
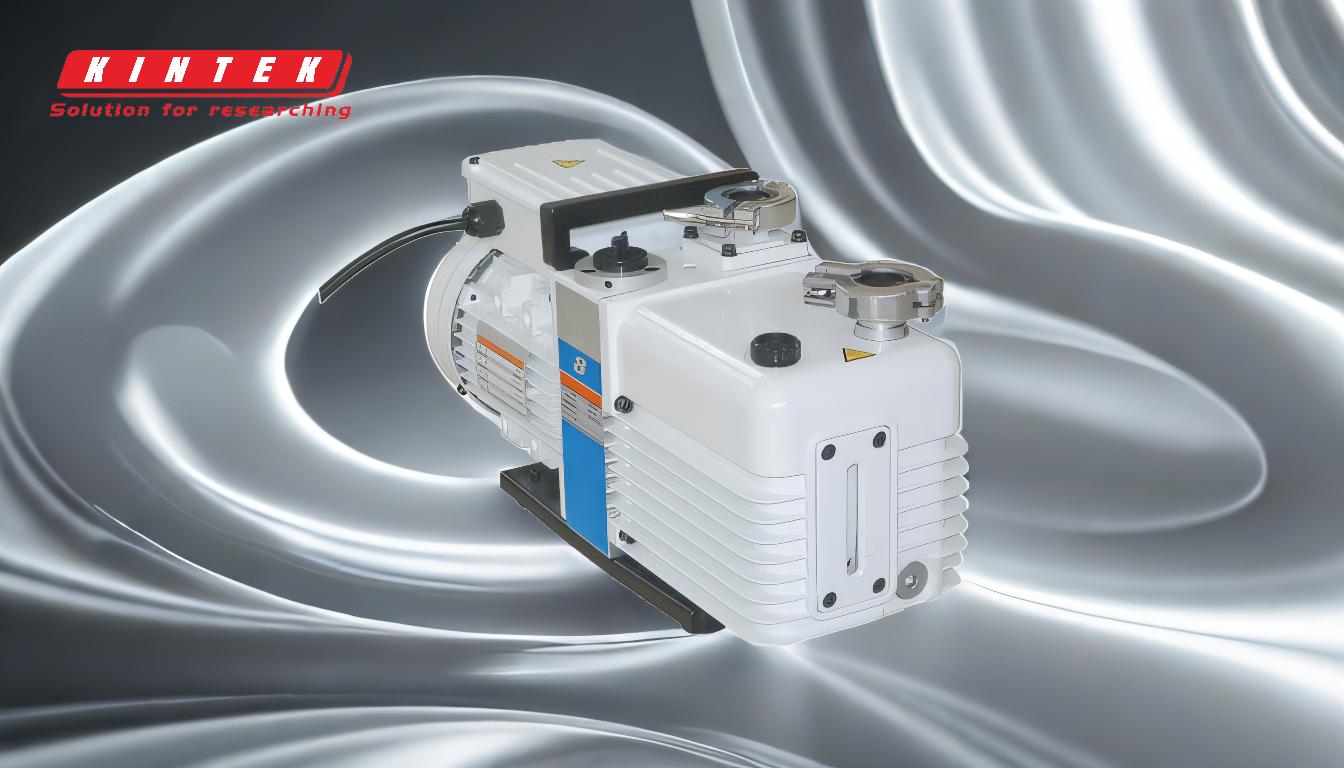
-
Functionality of Rotary Vacuum Pumps:
- Rotary vane vacuum pumps are oil-sealed and operate by using a rotating mechanism with vanes that move radially to create a vacuum.
- They provide strong, consistent vacuum pressures below 10⁻³ mbar, making them suitable for applications requiring high vacuum levels.
-
Common Applications:
- Hydraulic Braking Systems: These pumps are used to maintain the necessary vacuum pressure in hydraulic braking systems, ensuring efficient operation.
- Freeze Dryers: In freeze-drying processes, rotary vacuum pumps help in removing moisture by creating a vacuum, which is essential for preserving the quality of the dried products.
- Mass Spectrometry: These pumps are crucial in mass spectrometry, where they help maintain the required vacuum levels for accurate analysis.
-
Laboratory and Industrial Uses:
- Vacuum Packaging Machines: Rotary vacuum pumps are used in vacuum packaging to remove air from packages, extending the shelf life of products.
- Pick and Place Machines: These pumps assist in the precise handling and placement of components in manufacturing processes.
- Drying of Components: They are used in drying processes where a vacuum is needed to remove moisture or solvents from components.
- Bottle Filling: In industries like pharmaceuticals, rotary vacuum pumps are used in bottle filling machines to ensure accurate and contamination-free filling.
- Holding and Lifting: These pumps are used in applications where vacuum pressure is needed to hold or lift objects securely.
-
Advantages:
- Consistent Vacuum Pressure: Rotary vane vacuum pumps provide a strong and consistent vacuum, which is essential for many industrial and laboratory applications.
- Versatility: They can be used in a wide range of applications, from laboratory research to industrial manufacturing.
-
Disadvantages:
- Toxic Oil Waste: The oil used in these pumps can become contaminated and must be disposed of properly, which can be challenging and environmentally hazardous.
- Replacement Parts: Finding replacement parts for rotary vane vacuum pumps can be difficult, especially for older models.
-
Technical Specifications:
- Rotating Speed: These pumps typically operate at a rotating speed of approximately 1500 revolutions per minute.
- Vacuum Levels: Depending on the application, rotary vacuum pumps can achieve different vacuum levels, from rough vacuums to high and ultrahigh vacuums.
-
Importance in Specific Processes:
- Rotary Evaporators: In rotary evaporator applications, vacuum pumps reduce the pressure within the system, lowering the boiling temperature of the solvent. This results in faster evaporation and safer operation.
- Mass Spectrometry: The pumps maintain the necessary vacuum levels, which are critical for the accurate functioning of mass spectrometers.
-
Industry-Specific Requirements:
- Agri-Food and Drying: Rough vacuums are sufficient for these applications.
- Vacuum Metallurgy and Distillation: Higher vacuum levels are required for these processes.
- Surface State Physics and Particle Acceleration: Ultrahigh vacuums are essential for these advanced scientific applications.
In summary, rotary vacuum pumps are indispensable in various industries due to their ability to create and maintain specific vacuum levels. They are particularly valued for their consistency and versatility, though they do come with some challenges, such as handling toxic oil waste and finding replacement parts. Understanding the specific requirements of different applications is crucial for selecting the right type of vacuum pump.
Summary Table:
Aspect | Details |
---|---|
Functionality | Oil-sealed, rotating vanes create consistent vacuum below 10⁻³ mbar. |
Common Applications | Hydraulic braking, freeze dryers, mass spectrometry, vacuum packaging. |
Advantages | Consistent vacuum pressure, versatile for labs and industries. |
Disadvantages | Toxic oil waste disposal, difficulty in finding replacement parts. |
Technical Specifications | Rotating speed: ~1500 RPM; vacuum levels: rough to ultrahigh. |
Industry Uses | Agri-food, vacuum metallurgy, surface state physics, particle acceleration. |
Need a reliable rotary vacuum pump for your application? Contact us today to find the perfect solution!