Sputter coating is a widely used technique in various industries, including semiconductor manufacturing, microscopy, and decorative applications. It involves depositing a thin layer of metal onto a substrate to enhance properties such as conductivity, reflectivity, or corrosion resistance. The choice of metal for sputter coating depends on the specific application, desired properties, and compatibility with the substrate. Commonly used metals include gold, silver, platinum, chromium, carbon, tungsten, iridium, and palladium. Each metal has unique characteristics that make it suitable for particular applications, such as gold's high conductivity for SEM imaging or carbon's compatibility with EDX analysis.
Key Points Explained:
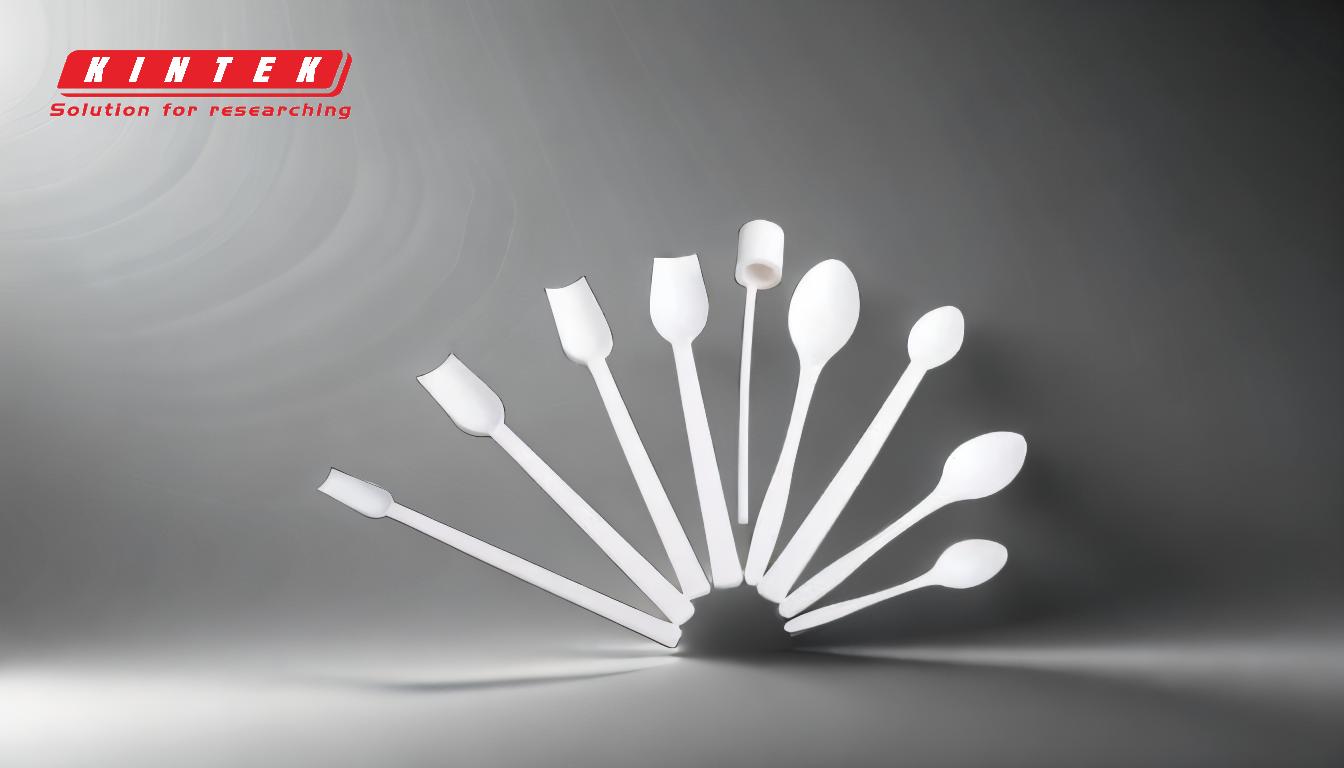
-
Common Metals Used in Sputter Coating:
- Gold (Au): Gold is frequently used in sputter coating due to its high electrical conductivity and small grain size, which makes it ideal for applications requiring high-resolution imaging, such as scanning electron microscopy (SEM). However, gold is not suitable for high-magnification imaging due to its tendency to form large islands or grains, which can interfere with image clarity.
- Silver (Ag): Silver is another conductive metal used in sputter coating. It offers excellent reflectivity and is often used in decorative applications or where high conductivity is required. However, silver is prone to tarnishing, which can limit its use in certain environments.
- Platinum (Pt): Platinum is known for its durability and resistance to corrosion, making it suitable for applications requiring long-term stability. It is often used in high-temperature environments or where chemical resistance is critical.
- Chromium (Cr): Chromium is commonly used as an adhesion layer in sputter coating due to its strong bonding properties. It is also used in applications requiring hardness and wear resistance.
- Carbon (C): Carbon is preferred for energy-dispersive X-ray (EDX) analysis because its X-ray peak does not interfere with other elements. It is also used in applications requiring a non-conductive coating or where minimal interference with the substrate's properties is desired.
- Tungsten (W): Tungsten is used in applications requiring high melting points and thermal stability. It is often used in semiconductor manufacturing and other high-temperature applications.
- Iridium (Ir): Iridium is valued for its high density and resistance to corrosion, making it suitable for specialized applications in harsh environments.
- Palladium (Pd): Palladium is used in applications requiring a balance of conductivity and corrosion resistance. It is often used in electronics and catalytic applications.
-
Factors Influencing Metal Selection:
- Conductivity: Metals like gold and silver are chosen for their high electrical conductivity, which is essential for applications such as SEM imaging or electronic components.
- Grain Size: The grain size of the sputtered metal affects the resolution of imaging techniques. Gold, with its small grain size, is ideal for high-resolution SEM imaging, while larger grain sizes can interfere with image quality.
- Chemical Stability: Metals like platinum and iridium are selected for their resistance to corrosion and chemical stability, making them suitable for harsh environments or long-term applications.
- Adhesion Properties: Chromium is often used as an adhesion layer due to its strong bonding properties, ensuring that the sputtered layer adheres well to the substrate.
- X-ray Compatibility: Carbon is preferred for EDX analysis because its X-ray peak does not conflict with other elements, allowing for accurate elemental analysis.
-
Applications of Sputter Coating:
- SEM Imaging: Sputter coating is commonly used in SEM to enhance the conductivity of non-conductive samples, improving image quality and resolution.
- EDX Analysis: Carbon coatings are used in EDX analysis to avoid interference with the X-ray peaks of other elements, ensuring accurate elemental analysis.
- Decorative Coatings: Metals like gold and silver are used in decorative applications to provide a reflective or aesthetically pleasing finish.
- Semiconductor Manufacturing: Sputter coating is used in semiconductor manufacturing to deposit thin films of conductive or insulating materials onto silicon wafers.
- Corrosion Resistance: Metals like platinum and iridium are used in applications requiring corrosion resistance, such as in harsh chemical environments or high-temperature conditions.
-
Sputtering Techniques:
- Magnetron Sputtering: This technique uses a magnetic field to confine electrons near the target material, increasing the efficiency of the sputtering process. It is widely used for depositing thin films in semiconductor manufacturing and other applications.
- Three-Pole Sputtering: This technique involves using three electrodes to generate plasma, allowing for precise control over the sputtering process. It is often used in research and development applications.
- RF Sputtering: RF (radio frequency) sputtering uses radio frequency energy to generate plasma, making it suitable for sputtering insulating materials. It is commonly used in applications requiring high-quality thin films.
-
Importance of High-Purity Argon Gas:
- High-purity argon gas, known as 'White spot' grade, is essential for achieving fast sputter rates and good pump-down times. Impurities in the gas can affect the quality of the sputtered film, leading to defects or reduced performance.
In conclusion, the choice of metal for sputter coating depends on the specific application, desired properties, and compatibility with the substrate. Common metals include gold, silver, platinum, chromium, carbon, tungsten, iridium, and palladium, each offering unique advantages for different applications. Understanding the properties and applications of these metals is crucial for selecting the appropriate material for sputter coating.
Summary Table:
Metal | Key Properties | Common Applications |
---|---|---|
Gold (Au) | High conductivity, small grain size | SEM imaging, electronics |
Silver (Ag) | Excellent reflectivity, prone to tarnishing | Decorative coatings, high-conductivity applications |
Platinum (Pt) | Durable, corrosion-resistant | High-temperature environments, chemical resistance |
Chromium (Cr) | Strong adhesion, hardness | Adhesion layers, wear-resistant coatings |
Carbon (C) | Non-conductive, X-ray compatible | EDX analysis, non-conductive coatings |
Tungsten (W) | High melting point, thermal stability | Semiconductor manufacturing, high-temperature applications |
Iridium (Ir) | High density, corrosion-resistant | Harsh environments, specialized applications |
Palladium (Pd) | Balanced conductivity and corrosion resistance | Electronics, catalytic applications |
Need help selecting the right metal for sputter coating? Contact our experts today for tailored advice!