The sintering temperature of ceramic membranes varies depending on the type of ceramic material and the desired properties. For most ceramic membranes, sintering occurs at high temperatures, typically ranging from 900°C to 2100°C. Oxide-based membranes are sintered at lower temperatures, around 1200-1600°C, while zirconia-based membranes require temperatures closer to 1500°C for optimal densification. The sintering process is critical for achieving durable physical and chemical properties, reducing porosity, and consolidating the powdery structure. Factors such as ramp rate, hold time, and cooling rate are also crucial for achieving the best results.
Key Points Explained:
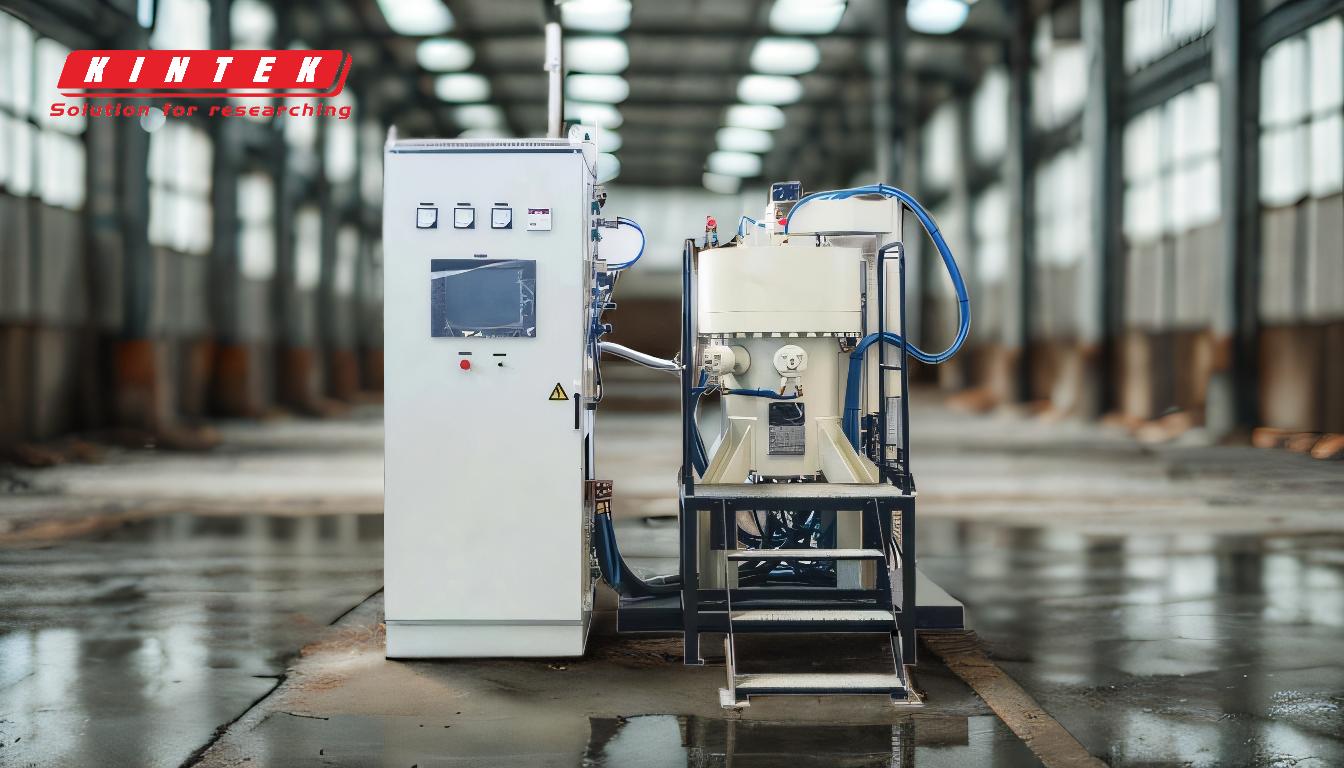
-
Temperature Range for Ceramic Membrane Sintering:
- Ceramic membranes are sintered at high temperatures, typically between 900°C and 2100°C.
- The exact temperature depends on the material type and desired properties. For example:
- Oxide-based membranes: 1200-1600°C.
- Zirconia-based membranes: ~1500°C (with densification occurring at higher temperatures).
-
Material-Specific Sintering Temperatures:
- Zirconia: Sintering typically occurs at ~1500°C, although the structural transformation from monoclinic to polytetragonal happens at 1100-1200°C. Higher temperatures (closer to 1500°C) result in denser zirconia, achieving up to 99% of theoretical maximum density.
- Oxide-based Ceramics: These are sintered at lower temperatures, generally between 1200°C and 1600°C.
-
Importance of Sintering Temperature:
- Sintering at high temperatures reduces porosity and consolidates the powdery structure, leading to durable physical and chemical properties.
- Higher temperatures result in denser materials, which are critical for applications requiring high strength and durability.
-
Process Parameters Beyond Temperature:
- Ramp Rate: The rate at which the temperature increases from 900°C to the top temperature is critical. A controlled ramp rate ensures uniform heating and prevents defects.
- Hold Time: Maintaining a consistent temperature during the hold phase is essential for achieving uniform densification.
- Cooling Rate: The rate of cooling back to ~900°C must be controlled to avoid thermal stresses and cracking.
-
Applications of Ceramic Sintering:
- Ceramic sintering is used in manufacturing ceramic objects like pottery, membranes, and restorations.
- The process is also applied in advanced materials, such as ceramic composites, which are sintered at temperatures between 900°C and 1250°C.
-
Inert Atmosphere:
- For some high-temperature sintering processes (e.g., up to 2100°C), an inert atmosphere is used to prevent oxidation and ensure the stability of the ceramic material.
By understanding these key points, a purchaser can make informed decisions about the appropriate sintering conditions for specific ceramic membrane applications, ensuring optimal performance and durability.
Summary Table:
Material Type | Sintering Temperature Range | Key Characteristics |
---|---|---|
Oxide-based Membranes | 1200°C - 1600°C | Lower sintering temperatures, ideal for applications requiring moderate durability. |
Zirconia Membranes | ~1500°C | Higher densification, achieving up to 99% of theoretical maximum density. |
Ceramic Composites | 900°C - 1250°C | Used in advanced materials, balancing strength and thermal stability. |
General Ceramics | 900°C - 2100°C | High-temperature sintering reduces porosity and enhances durability. |
Need help determining the right sintering temperature for your ceramic membranes? Contact our experts today for tailored solutions!