Argon is the preferred gas for sputtering processes due to its unique combination of properties that make it highly effective and efficient for this application. It is an inert gas, meaning it does not react with the target material or other elements, ensuring a clean and uncontaminated deposition process. Additionally, argon has a high sputtering rate due to its relatively high atomic mass, which enhances the efficiency of the sputtering process. Its availability in pure form and relatively low cost further contribute to its widespread use. While other noble gases like krypton and xenon can also be used, argon remains the most practical and economical choice for most sputtering applications.
Key Points Explained:
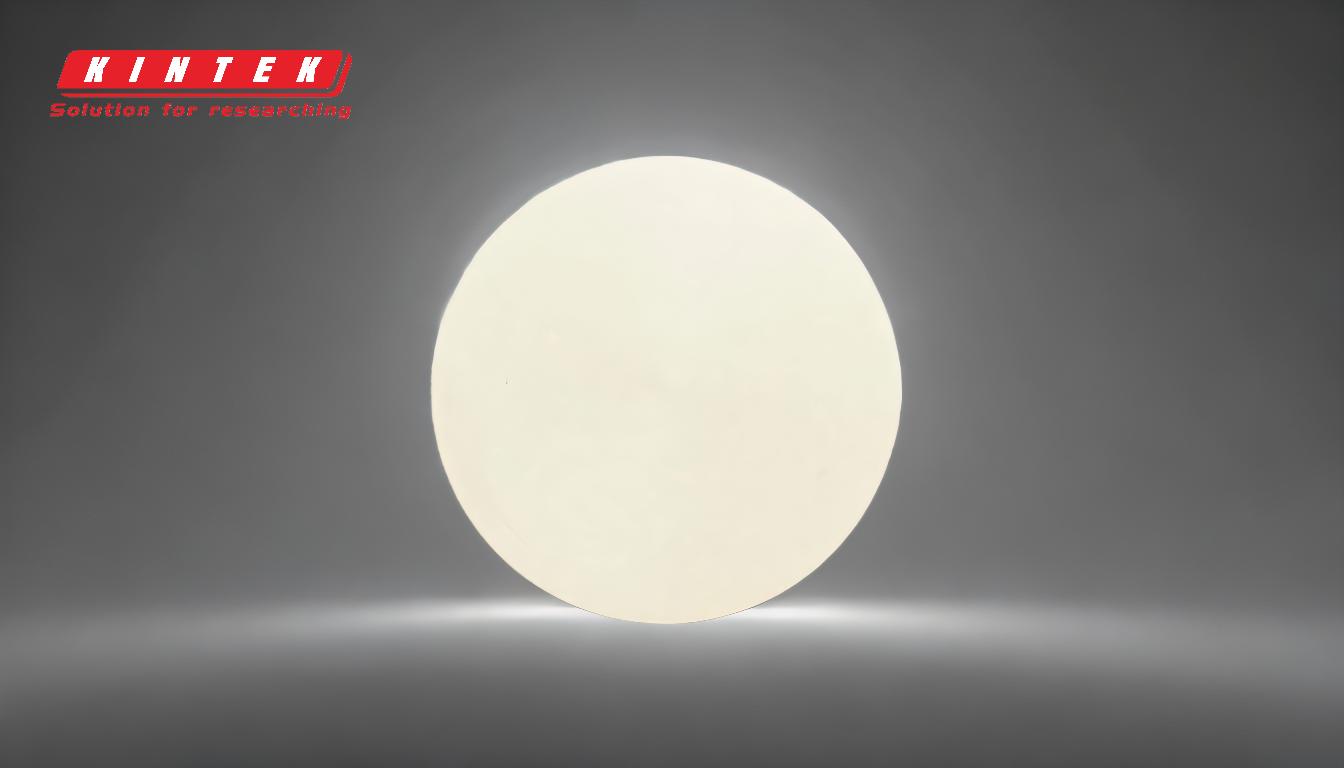
-
Inert Nature of Argon:
- Argon is a noble gas, meaning it is chemically inert and does not react with the target material or other elements in the sputtering process. This ensures that the deposited film remains pure and uncontaminated by unwanted chemical reactions.
- In contrast, reactive gases like oxygen could cause chemical reactions with the target material, altering the composition and properties of the deposited film. This makes argon ideal for applications where material purity is critical, such as in semiconductor manufacturing or aerospace coatings.
-
High Sputtering Rate:
- Argon has a relatively high atomic mass (40 atomic mass units), which makes its ions more effective at dislodging atoms from the target material during the sputtering process. This results in a higher sputtering rate compared to lighter gases like helium or neon.
- The high sputtering rate improves the efficiency of the process, allowing for faster deposition of thin films, which is particularly beneficial in industrial applications where throughput is a key consideration.
-
Availability and Purity:
- Argon is abundantly available in the Earth's atmosphere, making it easy to extract and purify. This ensures a consistent supply of high-purity argon gas, which is essential for achieving reliable and repeatable results in sputtering processes.
- The availability of argon in pure form also reduces the risk of contamination, which is critical for high-precision applications such as microelectronics and optical coatings.
-
Cost-Effectiveness:
- Compared to other noble gases like krypton and xenon, argon is significantly less expensive. This makes it a more economical choice for large-scale industrial applications where cost is a major factor.
- While krypton and xenon may offer certain advantages in specific applications (e.g., higher sputtering rates for heavier target materials), their higher cost often outweighs these benefits, making argon the preferred choice for most sputtering processes.
-
Compatibility with Magnetron Sputtering:
- Argon is particularly well-suited for magnetron sputtering, a widely used technique in thin-film deposition. In this process, argon ions are accelerated toward the target material by a magnetic field, enhancing the sputtering efficiency.
- The inert nature of argon ensures that the target material is not chemically altered during the process, resulting in high-quality, uniform films. This is especially important for applications requiring precise control over film properties, such as in the production of solar cells or display panels.
-
Comparison with Other Noble Gases:
- While argon is the most commonly used gas for sputtering, other noble gases like krypton and xenon can be used in specific situations. For example, krypton and xenon have higher atomic masses than argon, which can be advantageous when sputtering heavier target materials.
- However, these gases are significantly more expensive and less readily available than argon, limiting their use to specialized applications where their unique properties are essential.
In summary, argon's combination of inertness, high sputtering rate, availability, and cost-effectiveness makes it the ideal choice for most sputtering processes. Its widespread use in industries ranging from microelectronics to aerospace underscores its importance as a key component in modern thin-film deposition technologies.
Summary Table:
Property | Advantage |
---|---|
Inert Nature | Ensures pure, uncontaminated deposition; ideal for critical applications. |
High Sputtering Rate | High atomic mass enhances efficiency, enabling faster thin-film deposition. |
Availability & Purity | Abundant and easy to purify, ensuring consistent, high-quality results. |
Cost-Effectiveness | More economical than krypton or xenon, making it ideal for large-scale use. |
Magnetron Compatibility | Enhances sputtering efficiency, producing high-quality, uniform films. |
Optimize your sputtering process with argon—contact our experts today to learn more!