DC sputtering is widely used for metal deposition due to its cost-effectiveness, ease of control, and efficiency in producing high-quality thin films. This method leverages a DC power supply, which is less expensive and simpler to operate compared to other power sources like RF. The process involves bombarding a metal target with ions in a low-pressure environment, causing atoms to be ejected and deposited onto a substrate. The addition of magnets in DC magnetron sputtering further enhances the process by trapping electrons near the target surface, increasing ionization efficiency and deposition rates. This makes DC sputtering ideal for applications requiring precise, uniform, and durable metal coatings in industries such as microelectronics, solar energy, and optoelectronics.
Key Points Explained:
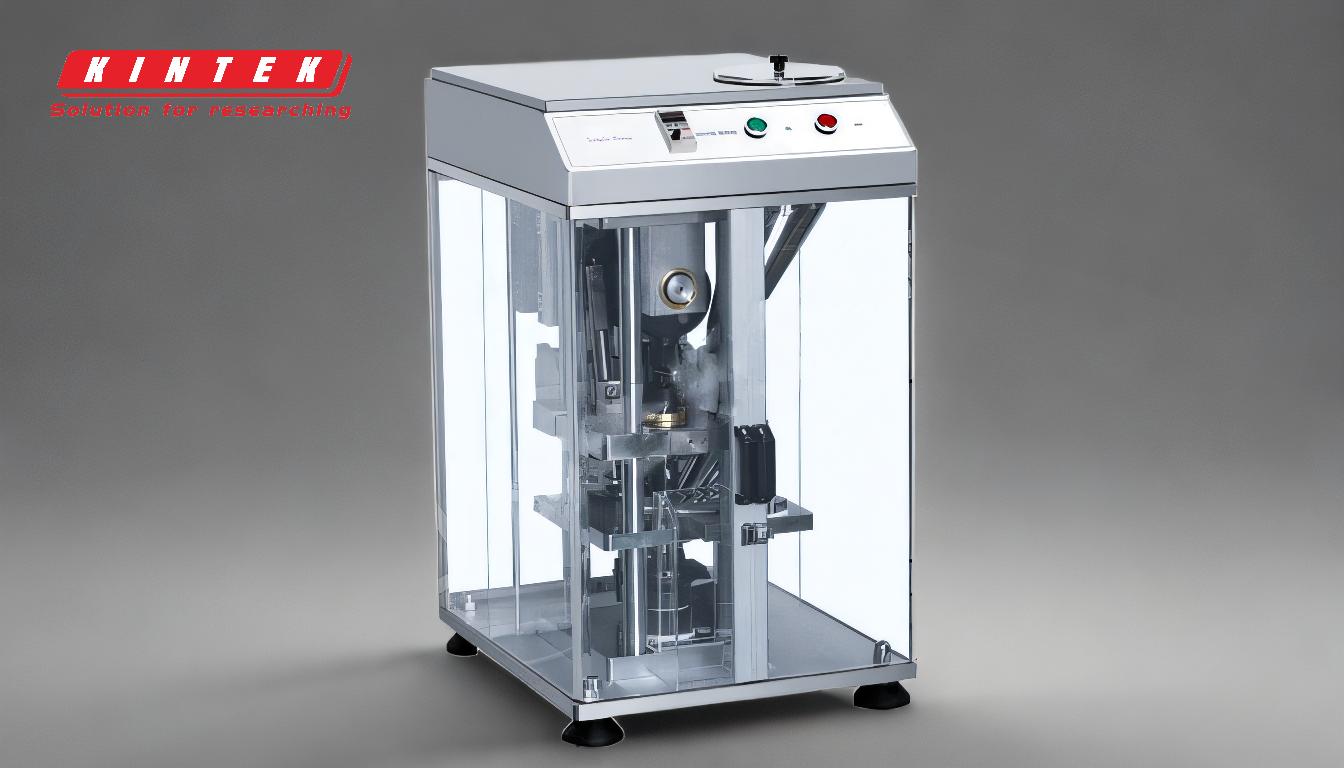
-
Cost-Effectiveness:
- DC power supplies are significantly cheaper than alternative power sources like RF, making DC sputtering a low-cost option for metal deposition.
- The affordability of DC power supplies makes this method economically viable for large-scale industrial applications.
-
Ease of Control:
- DC sputtering systems are straightforward to operate, allowing for precise control over the deposition process.
- This ease of control ensures consistent and high-quality thin film production, which is critical for applications requiring uniformity and precision.
-
High Deposition Rates:
- In DC magnetron sputtering, magnets are used to trap electrons near the target surface, creating a magnetic field that enhances ionization efficiency.
- This results in faster deposition rates, enabling quicker production of thin films without compromising quality.
-
Versatility and Precision:
- DC sputtering is highly versatile, capable of depositing a wide range of conductive materials onto various substrates.
- The process produces thin films with excellent adhesion, uniformity, and precision, making it suitable for applications in microelectronics, solar panels, and decorative coatings.
-
Energy Efficiency:
- DC sputtering operates in low-pressure environments, which reduces power consumption and enhances energy efficiency.
- The lower power requirements contribute to the overall cost-effectiveness of the process.
-
Industrial Scalability:
- The combination of low cost, ease of control, and high deposition rates makes DC sputtering scalable for mass production.
- Industries such as semiconductor manufacturing and solar energy benefit from the ability to produce large quantities of high-quality thin films efficiently.
-
Material Limitations:
- While DC sputtering is highly effective for conductive materials, it is not suitable for non-conductive targets.
- This limitation is offset by the method's advantages when working with metals and other conductive materials.
In summary, DC sputtering is a preferred method for metal deposition due to its cost-effectiveness, ease of operation, and ability to produce high-quality, uniform thin films at high deposition rates. Its scalability and energy efficiency further enhance its suitability for industrial applications across various sectors.
Summary Table:
Advantage | Description |
---|---|
Cost-Effectiveness | DC power supplies are cheaper than RF, making it affordable for large-scale use. |
Ease of Control | Simple operation ensures precise and consistent thin film production. |
High Deposition Rates | Magnets enhance ionization, speeding up film production without quality loss. |
Versatility | Deposits a wide range of conductive materials with excellent adhesion. |
Energy Efficiency | Low-pressure operation reduces power consumption, enhancing cost-effectiveness. |
Industrial Scalability | Ideal for mass production in industries like microelectronics and solar energy. |
Material Limitations | Limited to conductive materials but excels with metals. |
Ready to optimize your metal deposition process? Contact us today to learn more about DC sputtering solutions!