Vacuum is used in evaporators primarily to lower the boiling point of solvents or samples, enabling evaporation at reduced temperatures. This preserves the integrity of sensitive materials, prevents degradation, and ensures a controlled and efficient distillation process. Additionally, vacuum systems remove unwanted vapors, minimize contamination, and allow for precise control over evaporation rates and substrate thickness. By reducing pressure, vacuum systems also enhance safety by preventing volatile vapors from escaping into the environment.
Key Points Explained:
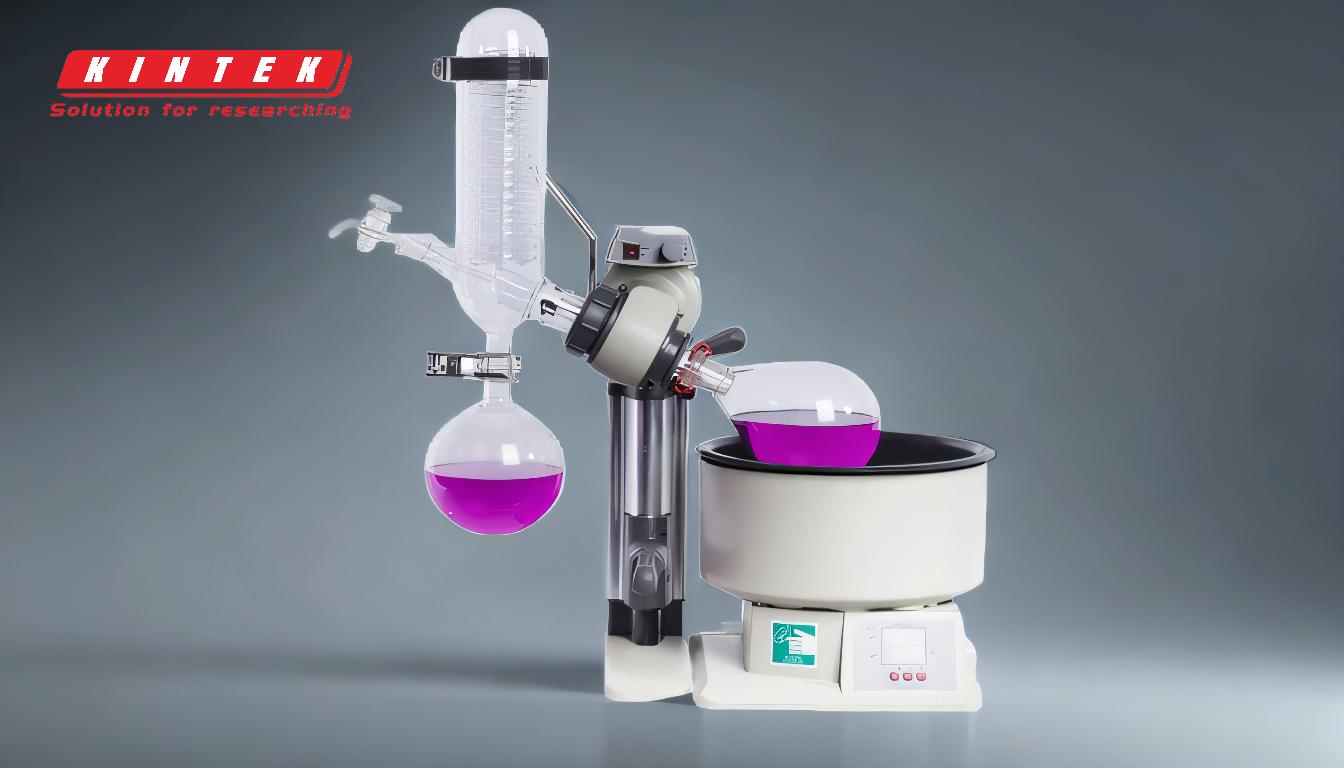
-
Lowering the Boiling Point of Solvents:
- A vacuum reduces the pressure within the evaporator, which directly lowers the boiling point of the solvent or sample. This allows evaporation to occur at much lower temperatures than would be possible under normal atmospheric pressure.
- This is particularly important for heat-sensitive materials, as excessive heat can degrade or alter their chemical composition. For example, in the food and pharmaceutical industries, preserving the flavor, aroma, or active ingredients of a sample is critical.
-
Preserving Sample Integrity:
- By evaporating solvents at lower temperatures, a vacuum protects sensitive samples from thermal degradation. This is especially valuable in applications involving delicate compounds, such as essential oils, pharmaceuticals, or biological samples.
- The gentle evaporation process ensures that the sample retains its desired properties, such as flavor, potency, or structural integrity.
-
Controlled and Efficient Distillation:
- A vacuum allows for precise control over the evaporation process. By adjusting the pressure, operators can fine-tune the evaporation rate to match the requirements of the specific application.
- This control ensures even evaporation and improves the separation of solvents from the desired product, leading to higher purity and yield.
-
Removing Unwanted Vapors:
- A vacuum system removes vapors that are not from the desired source material, ensuring the purity of the process. This is crucial in applications like thin-film deposition, where contamination from background gases can compromise the quality of the final product.
- By creating a clean environment, vacuum systems prevent unwanted interactions between evaporated particles and background gases, which could otherwise lead to contamination or reduced deposition efficiency.
-
Enhancing Safety:
- Vacuum systems prevent volatile vapors from escaping into the surrounding environment, reducing the risk of fire, explosion, or exposure to hazardous substances.
- This is particularly important in industrial settings where large volumes of solvents or hazardous materials are processed.
-
Improving Evaporation Rates:
- A vacuum can significantly increase the evaporation rate without raising the temperature of the heating bath. This is achieved by lowering the pressure, which accelerates the transition of the solvent from liquid to vapor.
- This feature is especially useful in high-throughput applications, where faster evaporation rates can improve productivity and reduce processing time.
-
Ensuring Consistent Substrate Thickness:
- In processes like thin-film deposition, a vacuum ensures that evaporated particles travel directly to the deposition target without interference from background gases. This results in a more uniform and controlled thickness of the substrate.
- Consistency in substrate thickness is critical for applications in electronics, optics, and coatings, where even minor variations can affect performance.
-
Energy Efficiency:
- By reducing the need for excessive heat, vacuum systems are more energy-efficient compared to traditional evaporation methods. This not only lowers operational costs but also reduces the environmental impact of the process.
In summary, the use of a vacuum in evaporators is essential for achieving precise, efficient, and safe evaporation processes. It enables lower-temperature evaporation, protects sensitive materials, ensures process purity, and enhances control over the entire operation. These benefits make vacuum systems indispensable in industries ranging from pharmaceuticals and food processing to electronics and materials science.
Summary Table:
Key Benefit | Explanation |
---|---|
Lower Boiling Point of Solvents | Reduces pressure to enable evaporation at lower temperatures, ideal for heat-sensitive materials. |
Preserve Sample Integrity | Protects sensitive samples from thermal degradation, maintaining flavor, potency, or structure. |
Controlled and Efficient Distillation | Precise pressure control ensures even evaporation, higher purity, and better yield. |
Remove Unwanted Vapors | Eliminates background gases, ensuring process purity and preventing contamination. |
Enhance Safety | Prevents volatile vapors from escaping, reducing fire, explosion, or exposure risks. |
Improve Evaporation Rates | Accelerates solvent transition to vapor without raising temperature, boosting productivity. |
Ensure Consistent Substrate Thickness | Enables uniform deposition in thin-film processes, critical for electronics and coatings. |
Energy Efficiency | Reduces heat requirements, lowering operational costs and environmental impact. |
Optimize your evaporation process with advanced vacuum systems—contact us today to learn more!