Yes, SiO2 (silicon dioxide) can be sputtered. Sputtering is a physical vapor deposition (PVD) technique used to deposit thin films of materials onto substrates. SiO2 is a common material used in various applications, such as insulating layers in microelectronics, optical coatings, and protective layers. Sputtering SiO2 involves bombarding a SiO2 target with high-energy ions, typically argon, in a vacuum chamber. This process ejects SiO2 atoms or molecules from the target, which then deposit onto the substrate. The sputtering of SiO2 can be performed using various methods, including RF (radio frequency) sputtering, which is particularly effective for insulating materials like SiO2 due to its ability to prevent charge buildup on the target surface.
Key Points Explained:
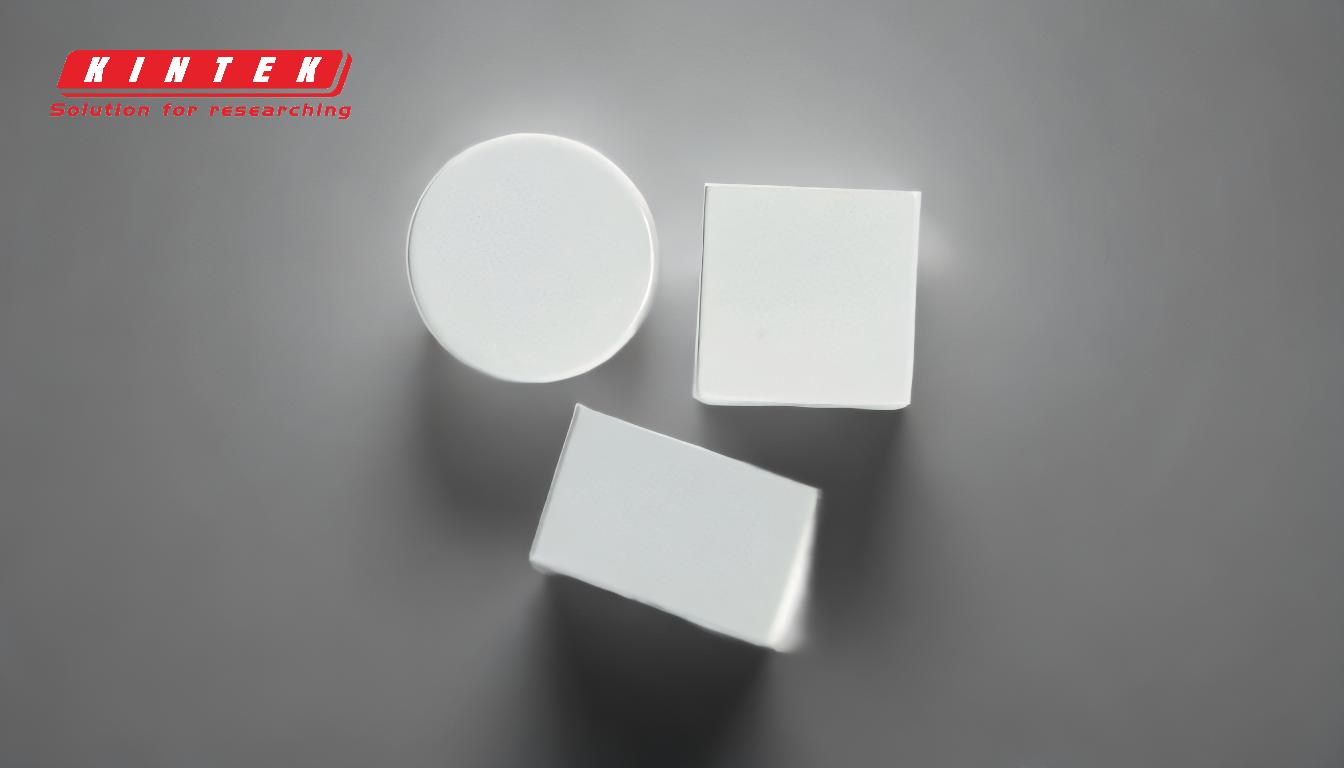
-
What is Sputtering?
- Sputtering is a physical vapor deposition (PVD) process where atoms are ejected from a solid target material due to bombardment by high-energy ions, typically argon. These ejected atoms then deposit onto a substrate, forming a thin film.
-
Why SiO2 is Suitable for Sputtering?
- SiO2 is a widely used material in the semiconductor industry, optics, and protective coatings due to its excellent insulating properties, high thermal stability, and transparency in the visible and near-infrared regions. Its ability to form uniform and dense thin films makes it ideal for sputtering.
-
Challenges in Sputtering SiO2
- SiO2 is an insulating material, which can lead to charge buildup on the target surface during sputtering. This can cause arcing and uneven deposition. To mitigate this, RF sputtering is often used. RF sputtering alternates the polarity of the electric field, preventing charge accumulation and enabling the sputtering of insulating materials like SiO2.
-
RF Sputtering of SiO2
- RF sputtering is the most common method for depositing SiO2 thin films. In this process, an RF power source is used to generate a plasma in the sputtering chamber. The alternating electric field allows for the efficient sputtering of insulating materials by neutralizing the charge buildup on the target surface.
-
Applications of Sputtered SiO2
- Sputtered SiO2 films are used in a variety of applications, including:
- Microelectronics: As insulating layers in integrated circuits.
- Optics: As anti-reflective coatings and protective layers on lenses.
- Protective Coatings: To provide corrosion resistance and mechanical protection.
- Sputtered SiO2 films are used in a variety of applications, including:
-
Comparison with Other Deposition Methods
- While sputtering is a common method for depositing SiO2, other techniques like chemical vapor deposition (CVD) and thermal oxidation are also used. However, sputtering offers advantages such as better control over film thickness, uniformity, and the ability to deposit at lower temperatures.
-
Role of Al2O3 Ceramic in Sputtering
- Al2O3 ceramic is often used in sputtering systems as a component of the target or as a substrate material due to its high thermal and electrical insulation properties. It can also be used as a backing plate for the SiO2 target to improve thermal conductivity and prevent overheating during the sputtering process.
-
Optimizing SiO2 Sputtering Parameters
- To achieve high-quality SiO2 films, it is important to optimize sputtering parameters such as:
- Power: RF power should be adjusted to ensure efficient sputtering without causing damage to the target.
- Pressure: The chamber pressure should be maintained at an optimal level to ensure a stable plasma and uniform deposition.
- Substrate Temperature: Controlling the substrate temperature can influence the film's microstructure and properties.
- To achieve high-quality SiO2 films, it is important to optimize sputtering parameters such as:
In conclusion, SiO2 can indeed be sputtered, and RF sputtering is the preferred method due to its effectiveness in handling insulating materials. The process is widely used in various industries, and optimizing the sputtering parameters is crucial for achieving high-quality SiO2 films. The use of Al2O3 ceramic in sputtering systems further enhances the process by providing thermal and electrical insulation, making it a valuable component in the deposition of SiO2 and other materials.
Summary Table:
Aspect | Details |
---|---|
What is Sputtering? | A PVD process where atoms are ejected from a target and deposited on a substrate. |
Why Use SiO2? | Excellent insulation, thermal stability, and transparency for thin films. |
Challenges | Charge buildup on insulating targets; mitigated by RF sputtering. |
Applications | Microelectronics, optics (anti-reflective coatings), and protective layers. |
Optimization Tips | Adjust RF power, chamber pressure, and substrate temperature for best results. |
Ready to enhance your processes with sputtered SiO2? Contact our experts today for tailored solutions!