The rate of chemical reactions can indeed be controlled through various methods, which are fundamental to optimizing processes in industries like pharmaceuticals, manufacturing, and research. By manipulating factors such as temperature, concentration, surface area, catalysts, and pressure, the reaction rate can be increased or decreased as needed. Understanding these factors allows scientists and engineers to design efficient and safe chemical processes. This answer explores the key methods for controlling reaction rates, their underlying principles, and practical applications.
Key Points Explained:
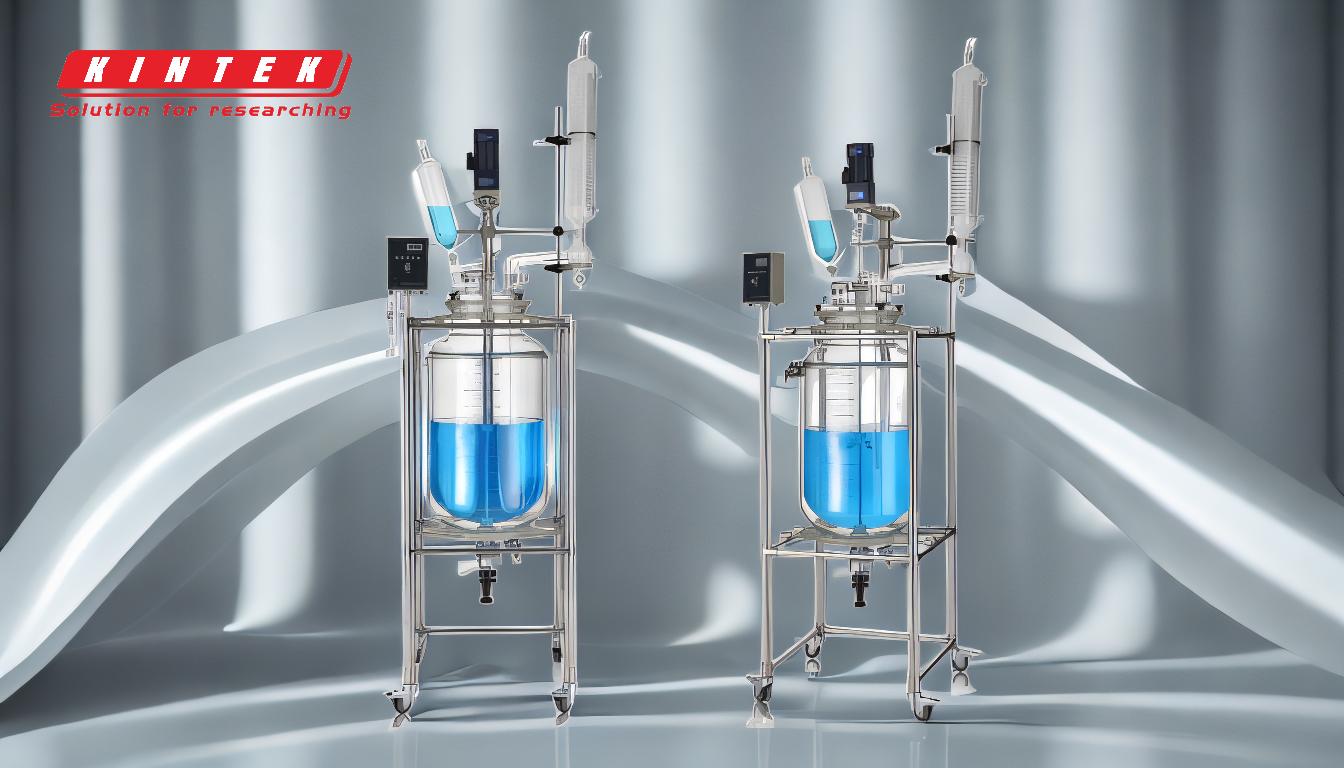
-
Temperature Control:
- Explanation: Increasing temperature generally increases the reaction rate because it provides more energy to reactant molecules, enabling them to overcome the activation energy barrier more easily. Conversely, lowering the temperature slows down the reaction.
- Application: In industrial processes, temperature is carefully regulated to ensure optimal reaction rates. For example, in polymerization reactions, maintaining a specific temperature range is critical to achieving the desired product properties.
-
Concentration of Reactants:
- Explanation: Higher concentrations of reactants lead to more frequent collisions between molecules, increasing the reaction rate. This is described by the collision theory.
- Application: In chemical manufacturing, reactant concentrations are often adjusted to control the speed of production. For instance, in the Haber process for ammonia synthesis, nitrogen and hydrogen concentrations are optimized to maximize yield.
-
Surface Area:
- Explanation: Increasing the surface area of solid reactants (e.g., by grinding into powder) exposes more particles to the reaction environment, enhancing the reaction rate.
- Application: This principle is used in catalytic converters, where a large surface area of the catalyst ensures efficient conversion of exhaust gases into less harmful substances.
-
Catalysts:
- Explanation: Catalysts speed up reactions by providing an alternative pathway with a lower activation energy. They are not consumed in the reaction and can be reused.
- Application: Enzymes in biological systems and industrial catalysts like platinum in hydrogenation reactions are examples of catalysts controlling reaction rates.
-
Pressure (for Gaseous Reactions):
- Explanation: Increasing pressure in gaseous reactions forces molecules closer together, increasing the frequency of collisions and thus the reaction rate.
- Application: In the production of ammonia via the Haber process, high pressure is applied to accelerate the reaction between nitrogen and hydrogen gases.
-
Nature of Reactants:
- Explanation: The chemical nature of reactants (e.g., bond strength, molecular structure) influences the reaction rate. Reactions involving simpler molecules or weaker bonds tend to proceed faster.
- Application: This principle is considered when designing chemical processes to ensure compatibility between reactants and desired reaction rates.
-
Inhibitors:
- Explanation: Inhibitors are substances that decrease the reaction rate by interfering with the reaction mechanism, often by binding to catalysts or reactants.
- Application: Inhibitors are used in food preservation to slow down spoilage reactions and in medicine to control enzymatic activity.
-
Light and Radiation:
- Explanation: Certain reactions, such as photosynthesis or photochemical reactions, are influenced by light or radiation, which provides energy to initiate or accelerate the reaction.
- Application: Photolithography in semiconductor manufacturing relies on light-induced reactions to create intricate patterns on silicon wafers.
-
Stirring and Mixing:
- Explanation: Agitation ensures uniform distribution of reactants, increasing the likelihood of collisions and thus the reaction rate.
- Application: Stirring is essential in batch reactors to maintain consistent reaction conditions and prevent localized concentration gradients.
-
Reaction Medium:
- Explanation: The solvent or medium in which a reaction occurs can affect the reaction rate. Polar solvents, for example, can stabilize charged intermediates, accelerating certain reactions.
- Application: In organic synthesis, the choice of solvent is critical to achieving the desired reaction rate and selectivity.
By understanding and manipulating these factors, scientists and engineers can precisely control reaction rates to achieve desired outcomes in both laboratory and industrial settings. This control is essential for optimizing efficiency, safety, and product quality in chemical processes.
Summary Table:
Factor | Explanation | Application |
---|---|---|
Temperature Control | Increases reaction rate by providing energy to overcome activation energy. | Used in polymerization to achieve desired product properties. |
Concentration | Higher concentrations increase collision frequency, speeding up reactions. | Optimized in the Haber process for ammonia synthesis. |
Surface Area | Larger surface area exposes more particles, enhancing reaction rate. | Applied in catalytic converters for efficient gas conversion. |
Catalysts | Provide an alternative pathway with lower activation energy, speeding up reactions. | Used in hydrogenation reactions and biological systems. |
Pressure | Increases collision frequency in gaseous reactions. | Applied in the Haber process to accelerate ammonia production. |
Nature of Reactants | Simpler molecules or weaker bonds react faster. | Considered in chemical process design for compatibility. |
Inhibitors | Decrease reaction rates by interfering with the reaction mechanism. | Used in food preservation and medicine. |
Light and Radiation | Provides energy to initiate or accelerate reactions. | Used in photolithography for semiconductor manufacturing. |
Stirring and Mixing | Ensures uniform reactant distribution, increasing collision likelihood. | Essential in batch reactors to maintain consistent conditions. |
Reaction Medium | Solvent choice affects reaction rate and selectivity. | Critical in organic synthesis for achieving desired outcomes. |
Want to optimize your chemical processes? Contact our experts today for tailored solutions!