A batch reactor is typically considered to operate under constant volume conditions, especially in ideal scenarios. This assumption simplifies calculations and modeling of the reactor, as it allows for easier analysis of reaction kinetics and thermodynamics. However, in practice, the volume may not always remain strictly constant due to factors such as temperature changes, pressure variations, or the addition/removal of materials during the reaction. Despite these practical considerations, the constant volume assumption is a foundational concept in understanding and designing batch reactors.
Key Points Explained:
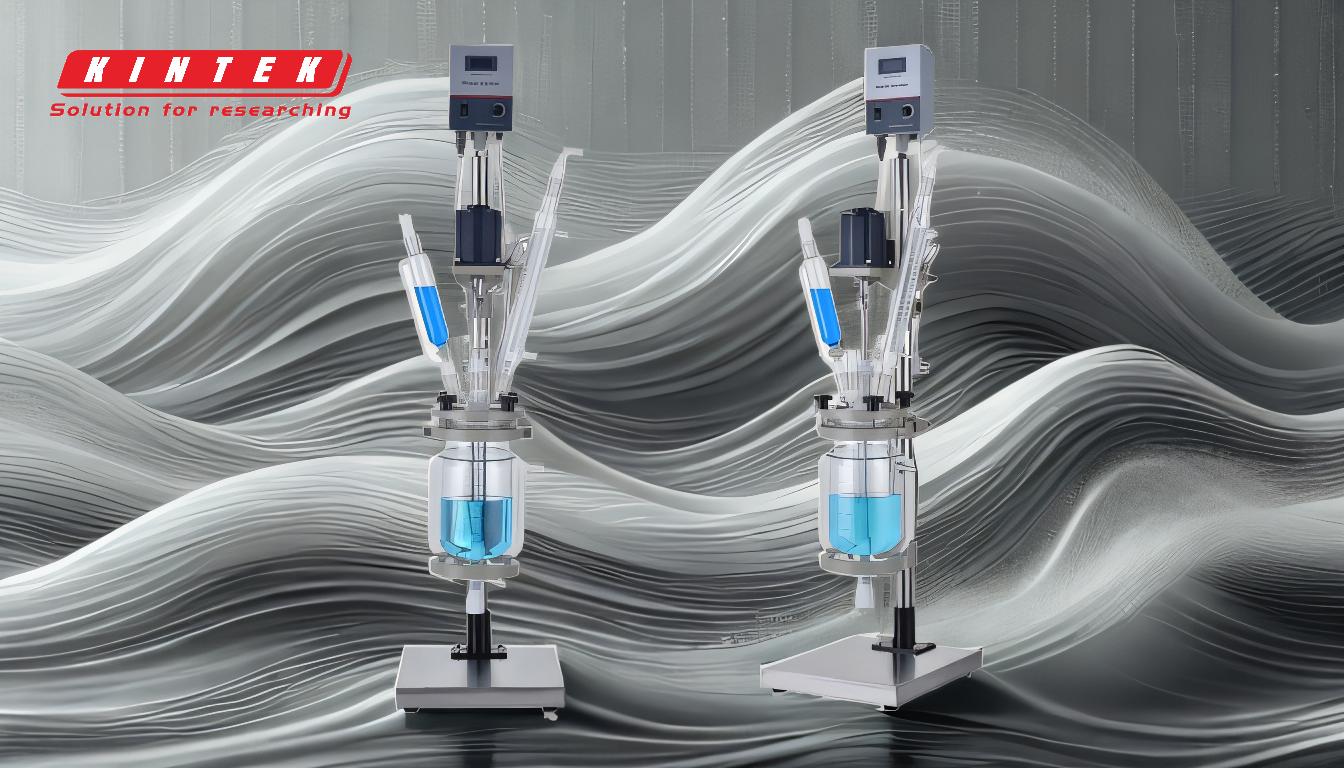
-
Ideal Assumption of Constant Volume:
- In theoretical and educational contexts, batch reactors are often assumed to operate at constant volume. This simplification is useful for modeling reaction kinetics and understanding basic reactor behavior.
- The constant volume assumption allows for straightforward calculations of reaction rates, concentrations, and other parameters.
-
Practical Considerations:
- Temperature and Pressure Effects: In real-world applications, temperature changes during the reaction can cause thermal expansion or contraction of the reactor contents, leading to volume changes. Similarly, pressure variations can affect the volume.
- Material Addition/Removal: Although batch reactors are typically closed systems, there might be instances where small amounts of reactants or products are added or removed, which can alter the volume.
- Phase Changes: Reactions involving phase changes (e.g., gas to liquid) can also result in volume changes within the reactor.
-
Design and Operation:
- Batch reactors are designed to minimize volume changes by ensuring a sealed environment. This is crucial for maintaining control over the reaction conditions.
- The use of sensors and control systems helps monitor and regulate parameters like temperature and pressure, which can indirectly help maintain a constant volume.
-
Applications and Implications:
- Laboratory Settings: In lab-scale batch reactors, the constant volume assumption is more likely to hold true due to smaller scales and better control over conditions.
- Industrial Settings: In larger-scale industrial applications, maintaining a strictly constant volume can be more challenging, but the assumption is still useful for initial design and analysis.
-
Advantages of Constant Volume Assumption:
- Simplifies mathematical modeling and simulation of the reactor.
- Facilitates easier understanding and teaching of reactor dynamics and kinetics.
- Provides a baseline for comparing more complex reactor designs and behaviors.
-
Challenges and Limitations:
- The constant volume assumption may not always be accurate, especially in reactions with significant heat release or absorption, or where phase changes occur.
- Engineers and scientists must account for potential volume changes when scaling up from laboratory to industrial scales.
In summary, while batch reactors are often assumed to operate at constant volume for simplicity, practical factors can lead to deviations from this ideal. Understanding these nuances is crucial for effective reactor design and operation.
Summary Table:
Aspect | Details |
---|---|
Ideal Assumption | Simplifies modeling and analysis of reaction kinetics and thermodynamics. |
Practical Challenges | Volume changes due to temperature, pressure, material addition/removal, or phase changes. |
Design Considerations | Sealed environments and control systems help minimize volume fluctuations. |
Applications | More accurate in lab settings; useful for initial design in industrial setups. |
Advantages | Simplifies calculations, teaching, and comparison of reactor designs. |
Limitations | Less accurate in reactions with heat release, absorption, or phase changes. |
Need help designing or optimizing your batch reactor? Contact our experts today for tailored solutions!