Sputtering targets are essential components in the sputtering process, a technique used to deposit thin films onto substrates. The process involves creating a vacuum environment, igniting argon plasma, and accelerating argon ions toward a negatively charged cathode (the sputtering target). The high-energy argon ions collide with the target, dislodging atoms from its surface. These ejected atoms travel through the vacuum chamber and deposit as a thin film on a substrate, such as a silicon wafer. This method is widely used in industries like semiconductors, optics, and coatings due to its precision and ability to work with heat-sensitive materials.
Key Points Explained:
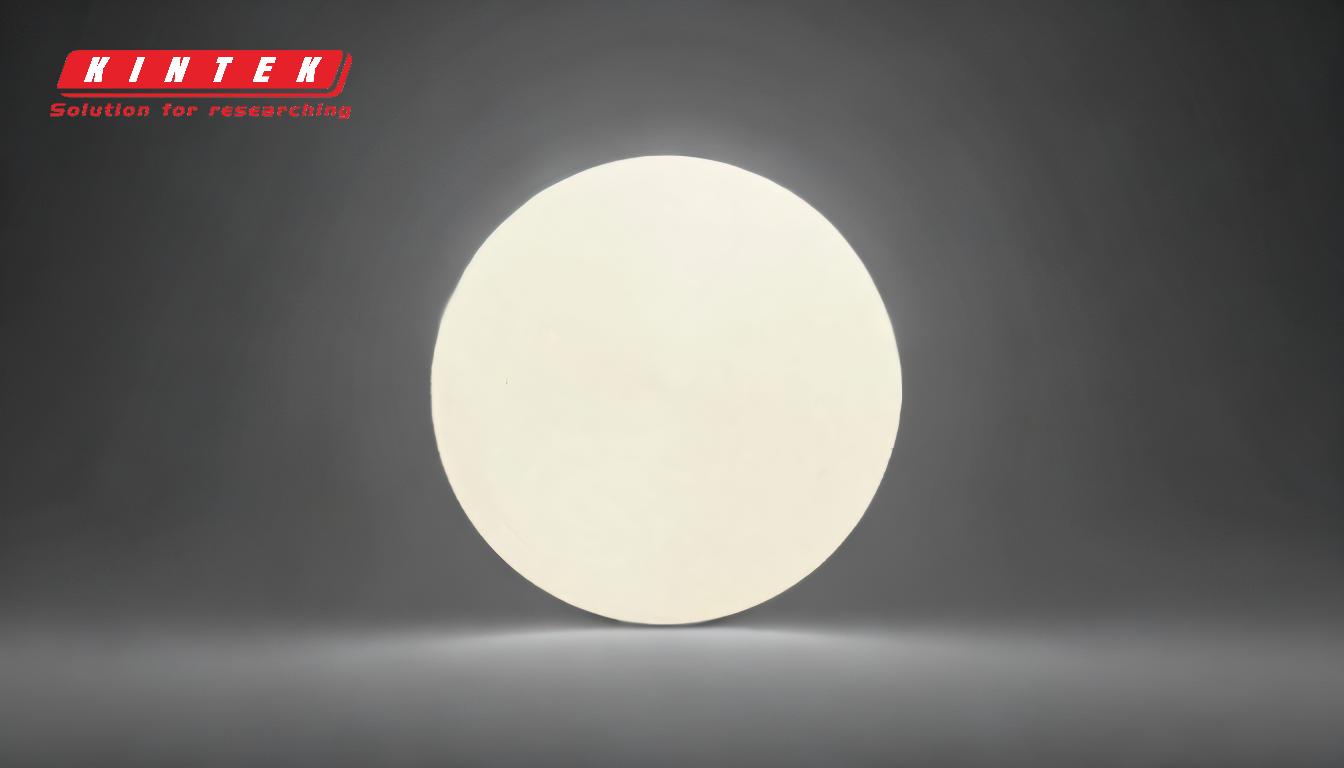
-
What is a Sputtering Target?
- Sputtering targets are typically thin discs or sheets made of materials like metals, alloys, or ceramics.
- They serve as the source material for thin film deposition in the sputtering process.
- The target material is chosen based on the desired properties of the thin film, such as conductivity, reflectivity, or durability.
-
The Sputtering Process Overview
- The process occurs in a vacuum chamber to prevent contamination from air or other gases.
- Argon gas is introduced into the chamber and ionized to create a plasma.
- A high-voltage electrical field accelerates argon ions toward the negatively charged sputtering target.
-
Role of Argon Plasma
- Argon plasma is created by ionizing argon gas, which produces positively charged argon ions.
- These ions are accelerated toward the sputtering target due to the electrical field.
- The high kinetic energy of the argon ions is critical for dislodging atoms from the target material.
-
Ejection of Target Atoms
- When the argon ions collide with the sputtering target, they transfer energy to the target atoms.
- This energy transfer physically ejects (or "sputters") atoms from the target's surface.
- The ejected atoms form a spray of particles that travel through the vacuum chamber.
-
Deposition on the Substrate
- The ejected target atoms diffuse through the vacuum chamber and condense on a substrate.
- The substrate is typically placed opposite the sputtering target to ensure uniform deposition.
- The deposited atoms form a thin film with properties determined by the target material.
-
Advantages of Sputtering
- Precision: Sputtering allows for highly controlled and uniform thin film deposition.
- Versatility: It can deposit a wide range of materials, including metals, alloys, and ceramics.
- Low Temperature: The process is suitable for heat-sensitive substrates, such as plastics, because the sputtered particles have low thermal energy.
-
Applications of Sputtering Targets
- Semiconductors: Used to deposit conductive and insulating layers on silicon wafers.
- Optics: Applied in the production of reflective and anti-reflective coatings for lenses and mirrors.
- Coatings: Used to create durable and corrosion-resistant coatings on various materials.
-
Key Considerations for Equipment and Consumables Purchasers
- Material Purity: Ensure the sputtering target material meets the required purity standards for the application.
- Target Geometry: Choose the appropriate shape and size of the target for your sputtering system.
- Compatibility: Verify that the target material is compatible with the sputtering process and substrate.
- System Maintenance: Consider the durability and longevity of the target material to minimize replacement frequency.
By understanding how sputtering targets work and their role in the sputtering process, purchasers can make informed decisions about selecting the right materials and equipment for their specific applications.
Summary Table:
Key Aspect | Details |
---|---|
What is a Sputtering Target? | Thin discs/sheets of metals, alloys, or ceramics used for thin film deposition. |
Sputtering Process | Vacuum environment, argon plasma, and high-energy ion collisions eject target atoms. |
Role of Argon Plasma | Ionized argon gas accelerates ions to dislodge target atoms. |
Advantages | Precision, versatility, and low-temperature processing. |
Applications | Semiconductors, optics, and durable coatings. |
Key Considerations | Material purity, target geometry, compatibility, and system maintenance. |
Need the right sputtering target for your application? Contact our experts today to get started!