Stirred tank reactors, particularly Continuous Stirred-Tank Reactors (CSTRs), are widely used in industrial and laboratory settings due to their numerous advantages. These reactors are designed with an impeller or agitator that ensures thorough mixing of reactants, leading to uniform and high-quality outcomes. CSTRs are known for their excellent temperature control, economical operation, and large thermal capacity, making them ideal for homogeneous liquid phase flow reactions. They are versatile and can be used alone, in series, or in a battery configuration, and are particularly beneficial in the pharmaceutical industry. Additionally, lab glass reactors, a type of stirred tank reactor, offer enhanced productivity, accuracy, and reproducibility, and are compatible with various auxiliary equipment for optimal process performance.
Key Points Explained:
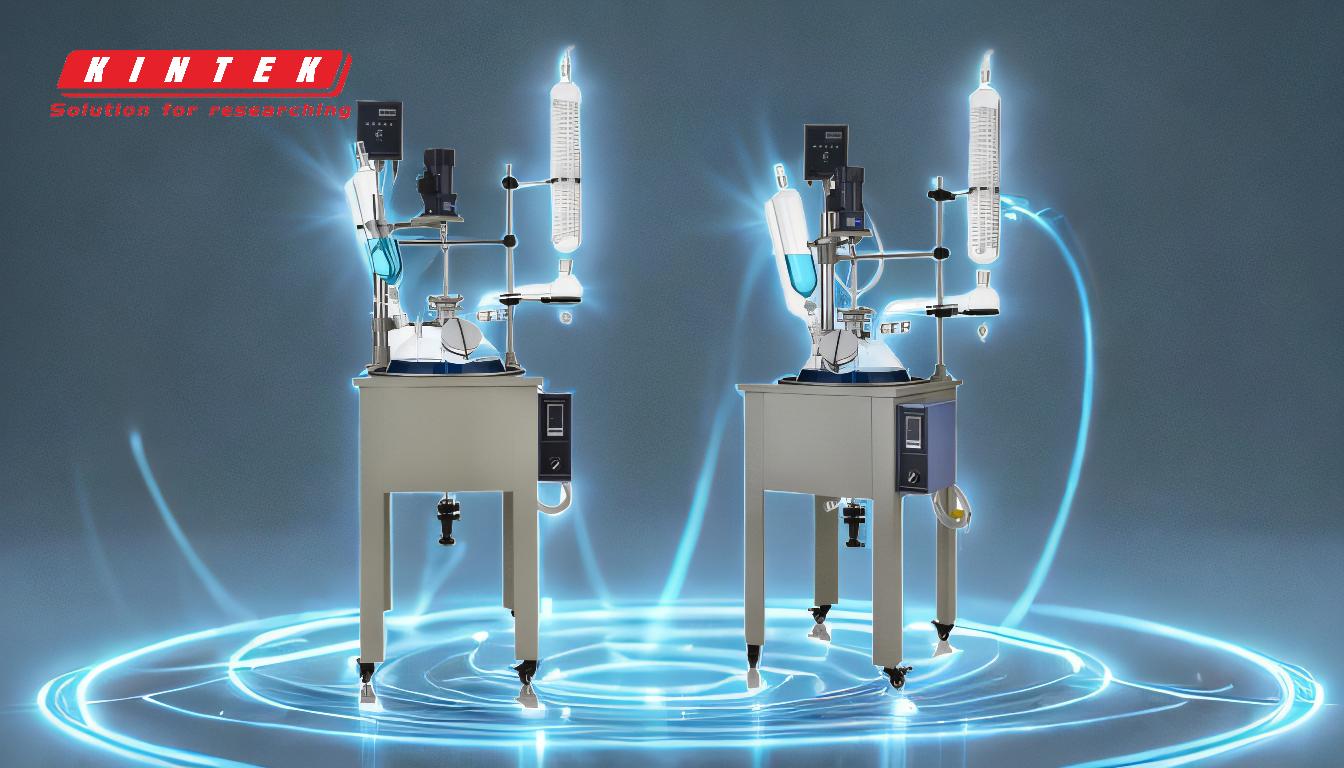
-
Uniform Mixing and High-Quality Outcomes:
- Explanation: The impeller or agitator in a CSTR ensures that all reactants are thoroughly mixed, leading to a uniform reaction environment. This uniformity is crucial for achieving consistent and high-quality outcomes, as it minimizes the risk of localized concentrations that could lead to incomplete reactions or by-products.
-
Rapid Reaction Rates:
- Explanation: The continuous stirring action in CSTRs facilitates faster reaction rates compared to other types of reactors. The constant mixing ensures that reactants are always in contact with each other, which accelerates the reaction process and reduces the time required to reach the desired product.
-
Excellent Temperature Control:
- Explanation: CSTRs are designed with features that allow for precise temperature control. This is particularly important for reactions that are sensitive to temperature changes, as maintaining a consistent temperature ensures the stability and efficiency of the reaction process.
-
Economical Operation:
- Explanation: The design and operation of CSTRs are cost-effective. They require less energy for mixing compared to other reactor types, and their ability to handle continuous flow processes reduces downtime and increases overall productivity, making them an economical choice for industrial applications.
-
Large Thermal Capacity:
- Explanation: CSTRs have a large thermal capacity, which means they can handle reactions that generate or require significant amounts of heat. This makes them suitable for a wide range of chemical processes, including those that are exothermic or endothermic.
-
Versatility in Configuration:
- Explanation: CSTRs can be used alone, in series, or in a battery configuration. This flexibility allows for customization based on the specific requirements of the reaction process, making them adaptable to various industrial applications.
-
Use in the Pharmaceutical Industry:
- Explanation: CSTRs are particularly beneficial in the pharmaceutical industry, where they are used as closed-circuit reactors. This setup ensures that the reaction environment is controlled and free from contaminants, which is critical for producing high-purity pharmaceutical products.
-
Enhanced Productivity, Accuracy, and Reproducibility in Lab Glass Reactors:
- Explanation: Lab glass reactors, a type of stirred tank reactor, offer higher levels of productivity, accuracy, and reproducibility. Their compatibility with auxiliary equipment like thermostats, nutsche filters, and gas scrubbers ensures optimal process performance, making them ideal for laboratory-scale reactions.
-
Safety Features:
- Explanation: Lab glass reactors are designed with safety in mind. Their fireproof design and sealed reaction vessels allow for the safe processing of solvents and acids, reducing the risk of accidents and ensuring a safe working environment.
In summary, stirred tank reactors, particularly CSTRs, offer a range of advantages including uniform mixing, rapid reaction rates, excellent temperature control, economical operation, large thermal capacity, and versatility in configuration. These features make them highly suitable for various industrial and laboratory applications, especially in the pharmaceutical industry. Lab glass reactors further enhance these benefits with their focus on productivity, accuracy, reproducibility, and safety.
Summary Table:
Advantage | Key Benefit |
---|---|
Uniform Mixing | Ensures consistent, high-quality outcomes with minimized by-products. |
Rapid Reaction Rates | Accelerates reactions through constant mixing, reducing processing time. |
Excellent Temperature Control | Maintains stable reaction conditions for sensitive processes. |
Economical Operation | Reduces energy use and downtime, enhancing productivity. |
Large Thermal Capacity | Handles exothermic or endothermic reactions efficiently. |
Versatility in Configuration | Adaptable for use alone, in series, or in battery setups. |
Pharmaceutical Industry Applications | Ensures high-purity, contaminant-free production environments. |
Lab Glass Reactors | Offers enhanced productivity, accuracy, and safety for lab-scale processes. |
Ready to optimize your chemical processes with CSTRs? Contact us today to learn more!