RF (Radio Frequency) sputtering is a specialized form of sputtering that offers several advantages over other thin film deposition techniques. It is particularly useful for depositing thin films of insulating materials, such as oxides and nitrides, which are challenging to deposit using DC sputtering. RF sputtering operates at high frequencies, typically 13.56 MHz, which allows for the efficient deposition of dielectric materials and reduces issues like arcing and charging. Below is a detailed explanation of the benefits of RF sputtering, structured for clarity and depth.
Key Points Explained:
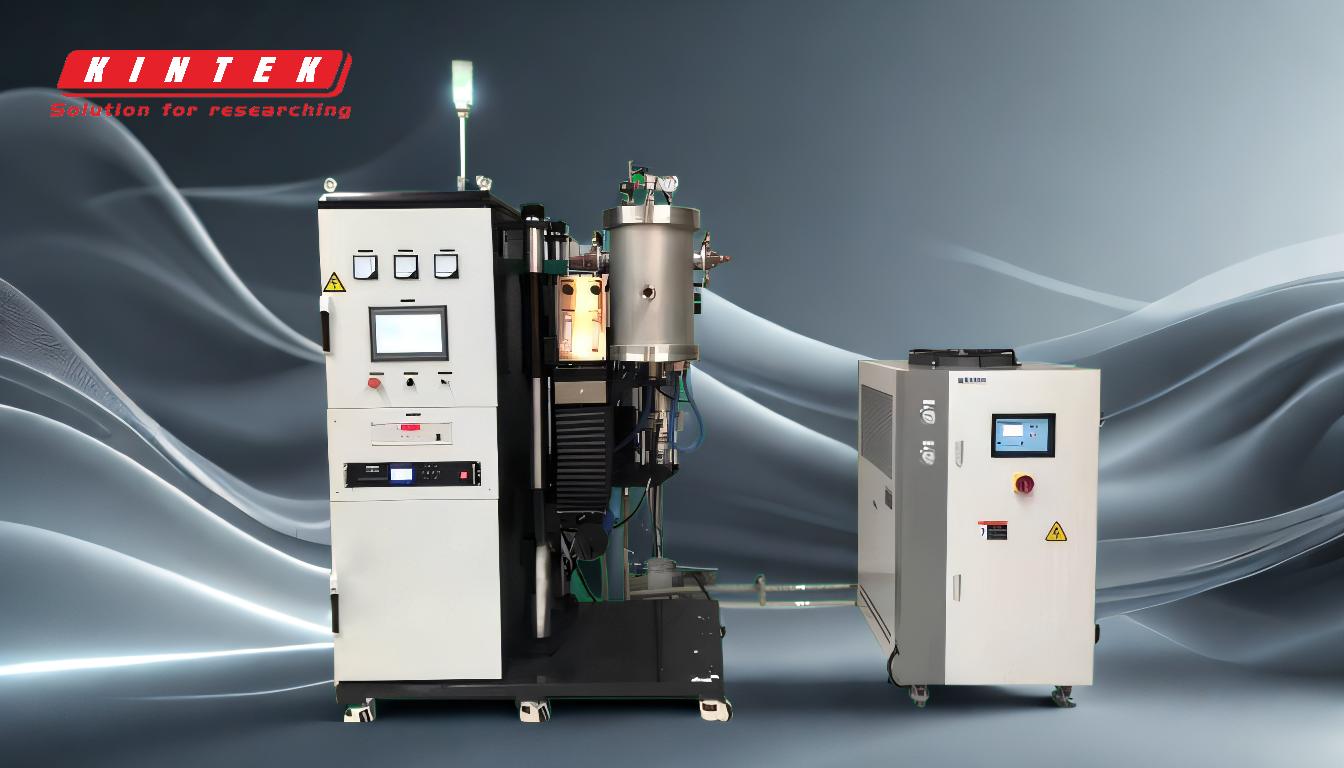
-
Ability to Deposit Insulating Materials
- RF sputtering is uniquely suited for depositing thin films of insulating or dielectric materials, such as silicon dioxide (SiO₂), aluminum oxide (Al₂O₃), and titanium nitride (TiN).
- Unlike DC sputtering, which struggles with insulating targets due to charge buildup, RF sputtering alternates the polarity of the electric field at high frequencies. This prevents charge accumulation on the target surface, enabling consistent and uniform deposition.
-
Reduced Arcing and Charging Issues
- In DC sputtering, insulating targets can develop a charge buildup, leading to arcing and uneven deposition.
- RF sputtering mitigates this problem by rapidly reversing the electric field, neutralizing charge buildup and ensuring a stable deposition process.
-
Improved Film Uniformity and Quality
- RF sputtering provides better control over the deposition process, resulting in highly uniform and high-quality thin films.
- The alternating electric field allows for precise control of ion bombardment, leading to fewer defects and impurities in the deposited film.
-
Versatility in Material Deposition
- RF sputtering can deposit a wide range of materials, including metals, semiconductors, and insulators.
- This versatility makes it a preferred choice for applications in microelectronics, optics, and solar panels, where diverse material properties are required.
-
Compatibility with Reactive Sputtering
- RF sputtering is well-suited for reactive sputtering processes, where a reactive gas (e.g., oxygen or nitrogen) is introduced into the chamber to form compound films like oxides or nitrides.
- The high-frequency operation ensures efficient ionization of the reactive gas, leading to better control over film composition and properties.
-
Lower Substrate Heating
- Compared to other deposition techniques like electron beam evaporation, RF sputtering generates less heat at the substrate.
- This is particularly beneficial for temperature-sensitive substrates, such as polymers or certain semiconductors, where excessive heat can cause damage or degradation.
-
Scalability for Industrial Applications
- RF sputtering is scalable and can be adapted for large-area deposition, making it suitable for industrial applications like solar panels, flat-panel displays, and architectural glass coatings.
- The process can be integrated into production lines with minimal modifications, ensuring cost-effectiveness and high throughput.
-
Advancements in Magnetron RF Sputtering
- Combining RF sputtering with magnetron technology enhances deposition rates and further improves film quality.
- Magnetron RF sputtering is particularly effective for depositing high-performance dielectric and nitride films in microelectronics and semiconductor applications.
In summary, RF sputtering offers significant advantages for depositing thin films, especially for insulating materials and applications requiring high precision and uniformity. Its ability to reduce arcing, improve film quality, and work with a wide range of materials makes it a versatile and reliable technique in industries such as microelectronics, optics, and renewable energy. Ongoing advancements in RF sputtering technology continue to expand its capabilities, ensuring its relevance in modern manufacturing and research.
Summary Table:
Benefit | Description |
---|---|
Deposit Insulating Materials | Ideal for oxides and nitrides; prevents charge buildup with high-frequency operation. |
Reduced Arcing and Charging | Neutralizes charge buildup, ensuring stable and uniform deposition. |
Improved Film Uniformity | High-quality thin films with fewer defects and impurities. |
Versatility in Materials | Deposits metals, semiconductors, and insulators for diverse applications. |
Compatible with Reactive Gases | Efficiently forms oxides and nitrides with precise control over film properties. |
Lower Substrate Heating | Minimizes heat damage to temperature-sensitive substrates. |
Scalable for Industry | Adaptable for large-area deposition in solar panels, displays, and coatings. |
Magnetron RF Sputtering | Enhances deposition rates and film quality for microelectronics and semiconductors. |
Ready to enhance your thin film deposition process? Contact us today to learn more about RF sputtering solutions!