Bioreactors are essential tools in biotechnology, used for cultivating cells, microorganisms, or tissues under controlled conditions. Designing a bioreactor involves careful consideration of various factors to ensure optimal performance, scalability, and reproducibility. Key design considerations include the type of biological process, environmental control (temperature, pH, oxygen levels), mixing and agitation, sterilization, scalability, and material compatibility. These factors are critical to achieving the desired biological output, whether for research, industrial production, or therapeutic applications.
Key Points Explained:
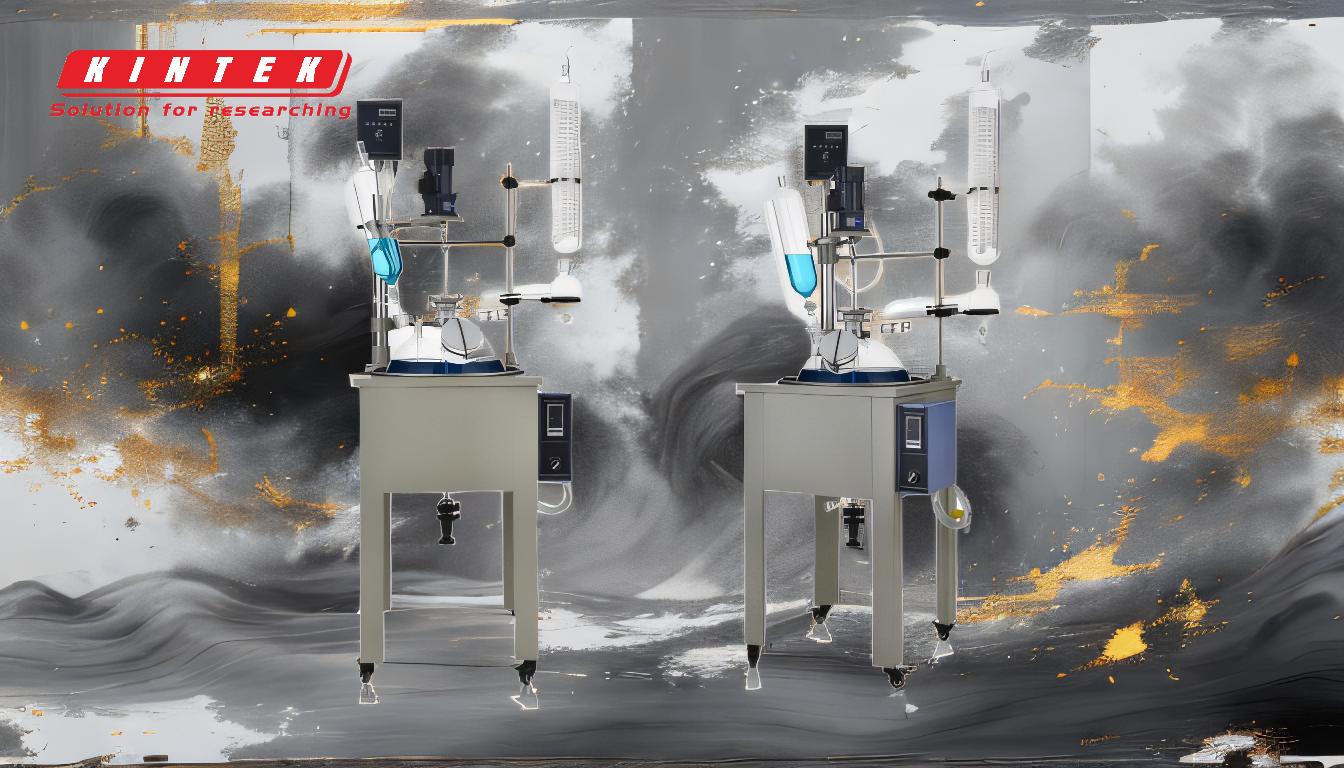
-
Type of Biological Process:
- The biological process being carried out (e.g., fermentation, cell culture, tissue engineering) dictates the design of the bioreactor. For example:
- Fermentation: Requires robust mixing and aeration for microbial growth.
- Cell Culture: Needs gentle agitation to avoid shear stress on delicate cells.
- Tissue Engineering: Demands specialized scaffolds and perfusion systems to support tissue growth.
- The choice of bioreactor type (e.g., stirred-tank, airlift, or packed-bed) depends on the specific requirements of the process.
- The biological process being carried out (e.g., fermentation, cell culture, tissue engineering) dictates the design of the bioreactor. For example:
-
Environmental Control:
- Maintaining optimal environmental conditions is crucial for biological activity. Key parameters include:
- Temperature: Must be tightly controlled, as biological processes are highly temperature-sensitive.
- pH: Requires monitoring and adjustment to maintain the ideal range for the organism or cells.
- Oxygen Levels: Adequate oxygen supply is essential for aerobic processes, often achieved through sparging or agitation.
- Nutrient Supply: Continuous or periodic feeding is necessary to sustain growth and productivity.
- Maintaining optimal environmental conditions is crucial for biological activity. Key parameters include:
-
Mixing and Agitation:
- Proper mixing ensures uniform distribution of nutrients, gases, and cells, preventing gradients and dead zones. Considerations include:
- Agitation Speed: Must balance mixing efficiency with shear stress, especially for sensitive cells.
- Impeller Design: Affects flow patterns and mixing efficiency (e.g., Rushton turbines for high shear, marine propellers for low shear).
- Baffles: Improve mixing by disrupting circular flow patterns.
- Proper mixing ensures uniform distribution of nutrients, gases, and cells, preventing gradients and dead zones. Considerations include:
-
Sterilization:
- Bioreactors must be sterilizable to prevent contamination. Common methods include:
- Autoclaving: For small-scale bioreactors.
- In-Place Sterilization (SIP): For large-scale systems, using steam or chemical sterilants.
- Material Compatibility: Materials must withstand sterilization conditions (e.g., stainless steel for high temperatures, autoclavable plastics for smaller units).
- Bioreactors must be sterilizable to prevent contamination. Common methods include:
-
Scalability:
- Bioreactor design must consider scalability from laboratory to industrial scale. Key factors include:
- Geometric Similarity: Maintaining similar aspect ratios and mixing patterns across scales.
- Mass Transfer: Ensuring oxygen and nutrient transfer rates remain effective at larger volumes.
- Process Control: Implementing automated control systems for consistent operation at all scales.
- Bioreactor design must consider scalability from laboratory to industrial scale. Key factors include:
-
Material Compatibility:
- The materials used in bioreactor construction must be compatible with the biological process and sterilization methods. Considerations include:
- Stainless Steel: Durable and resistant to corrosion, suitable for large-scale industrial bioreactors.
- Glass or Transparent Plastics: Ideal for small-scale bioreactors, allowing visual monitoring.
- Coatings: Non-toxic coatings may be required to prevent cell adhesion or contamination.
- The materials used in bioreactor construction must be compatible with the biological process and sterilization methods. Considerations include:
-
Process Monitoring and Control:
- Advanced monitoring systems are essential for real-time control of bioreactor parameters. Key features include:
- Sensors: For measuring temperature, pH, dissolved oxygen, and biomass concentration.
- Automation: Enables precise control and reduces human error.
- Data Logging: Facilitates process optimization and troubleshooting.
- Advanced monitoring systems are essential for real-time control of bioreactor parameters. Key features include:
-
Economic and Operational Considerations:
- The design must balance performance with cost and operational efficiency. Factors include:
- Energy Consumption: Minimizing energy use for mixing, aeration, and temperature control.
- Maintenance: Designing for easy cleaning, repair, and replacement of components.
- Regulatory Compliance: Ensuring the bioreactor meets industry standards and regulatory requirements.
- The design must balance performance with cost and operational efficiency. Factors include:
By addressing these design considerations, bioreactors can be optimized for specific applications, ensuring efficient and reproducible biological processes. Whether for research, industrial production, or therapeutic development, a well-designed bioreactor is critical to achieving success.
Summary Table:
Design Consideration | Key Factors |
---|---|
Type of Biological Process | Fermentation, cell culture, tissue engineering |
Environmental Control | Temperature, pH, oxygen levels, nutrient supply |
Mixing and Agitation | Agitation speed, impeller design, baffles |
Sterilization | Autoclaving, in-place sterilization, material compatibility |
Scalability | Geometric similarity, mass transfer, process control |
Material Compatibility | Stainless steel, glass, transparent plastics, coatings |
Process Monitoring and Control | Sensors, automation, data logging |
Economic and Operational | Energy consumption, maintenance, regulatory compliance |
Ready to design a bioreactor tailored to your needs? Contact our experts today for personalized guidance!