In video compression, frames are categorized into three main types: I-frames, P-frames, and B-frames. These frames serve different purposes in the compression process, optimizing storage and transmission efficiency. I-frames are complete images that serve as reference points, P-frames use data from previous frames to predict content, and B-frames use data from both past and future frames for even greater compression. Understanding these frame types is crucial for anyone involved in video encoding, decoding, or purchasing equipment for video processing.
Key Points Explained:
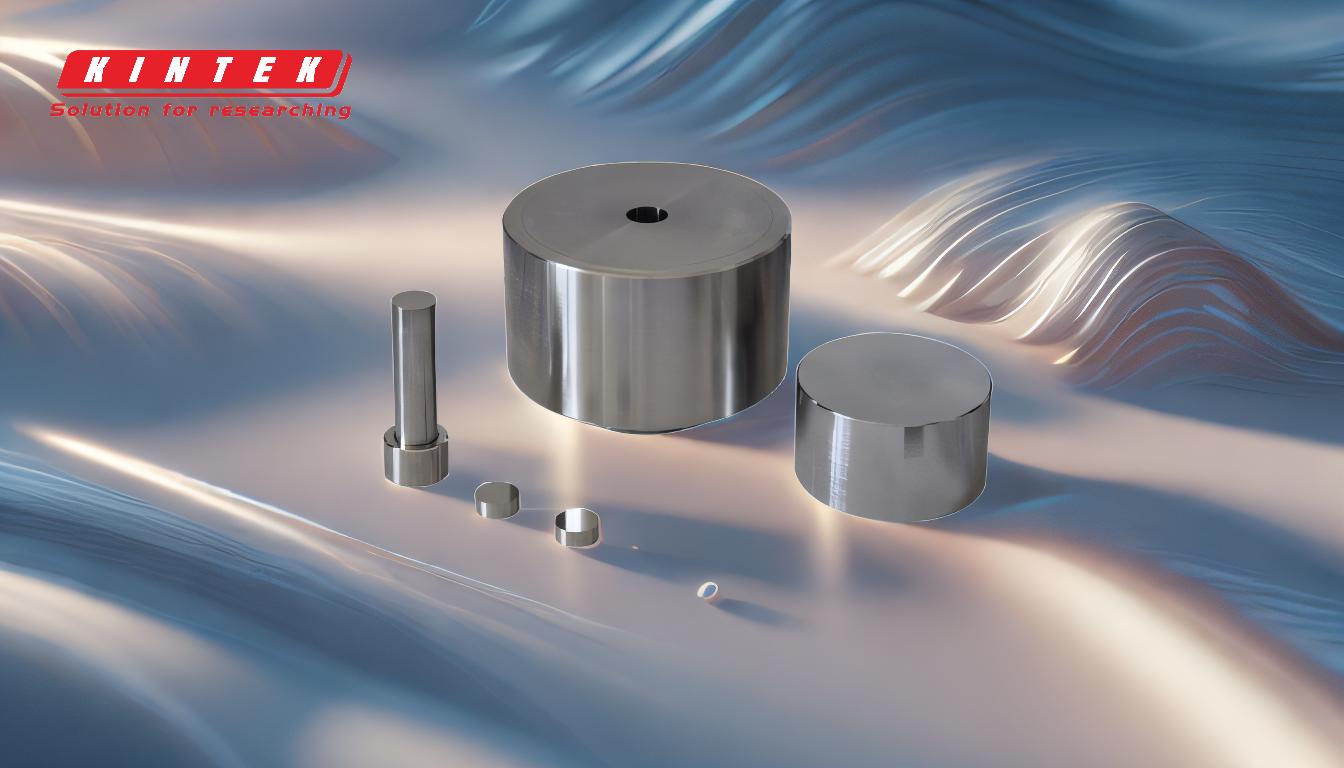
-
I-frames (Intra-coded frames)
- Definition: I-frames are complete, standalone images that do not rely on other frames for information. They are similar to a JPEG or BMP image file.
- Purpose: Serve as reference points for other frames (P-frames and B-frames) in the video sequence.
- Compression: Since they contain all the data needed to display the image, they are less compressed compared to P-frames and B-frames.
- Usage: Typically used at the beginning of a video sequence or at regular intervals to ensure quality and provide anchor points for decoding.
-
P-frames (Predicted frames)
- Definition: P-frames are predicted frames that rely on data from previous frames (either I-frames or other P-frames) to reconstruct the image.
- Purpose: Reduce file size by storing only the changes (or differences) from the previous frame.
- Compression: More compressed than I-frames, as they only encode the differences rather than the entire image.
- Usage: Commonly used in sequences where there is minimal motion, as they are efficient in reducing data without significant loss of quality.
-
B-frames (Bi-directional predicted frames)
- Definition: B-frames are bi-directional frames that use data from both past and future frames (I-frames or P-frames) to predict the current frame.
- Purpose: Achieve the highest level of compression by utilizing information from multiple frames.
- Compression: Highly compressed, as they store only the differences from both past and future frames.
- Usage: Ideal for scenes with complex motion, as they provide a balance between compression efficiency and visual quality.
-
Sequence of Frames in Compression
- A typical video sequence might consist of an I-frame followed by a series of P-frames and B-frames. For example: I, B, P, B, P, B, I.
- This sequence ensures efficient compression while maintaining video quality by periodically resetting with I-frames.
-
Implications for Equipment and Consumables Purchasers
- Storage and Bandwidth: Understanding frame types helps in selecting storage solutions and network equipment that can handle the varying data rates of compressed video streams.
- Encoding/Decoding Hardware: Equipment capable of efficiently processing I, P, and B frames is essential for high-quality video playback and editing.
- Software Compatibility: Ensure that video editing and playback software supports the frame types used in your video files.
By understanding these frame types, purchasers can make informed decisions about the equipment and software needed for video processing, ensuring optimal performance and cost-efficiency.
Summary Table:
Frame Type | Definition | Purpose | Compression | Usage |
---|---|---|---|---|
I-frames | Complete, standalone images | Serve as reference points | Less compressed | Used at the start or intervals of a video |
P-frames | Predicted frames using previous frames | Reduce file size by storing changes | More compressed | Ideal for minimal motion sequences |
B-frames | Bi-directional frames using past and future frames | Achieve highest compression | Highly compressed | Best for complex motion scenes |
Need help selecting the right video processing equipment? Contact our experts today for tailored solutions!