Internal mixers are essential equipment in industries like rubber and plastics processing, where they are used to blend raw materials uniformly. The two primary types of internal mixers are the tangential type (MX series) and the intermeshing type (IMX series). Each type has distinct design features and operational advantages, making them suitable for specific applications. The tangential type allows for higher shear rates and faster mixing, while the intermeshing type provides better dispersion and is more efficient for certain materials. Understanding these differences helps in selecting the right mixer for specific industrial needs.
Key Points Explained:
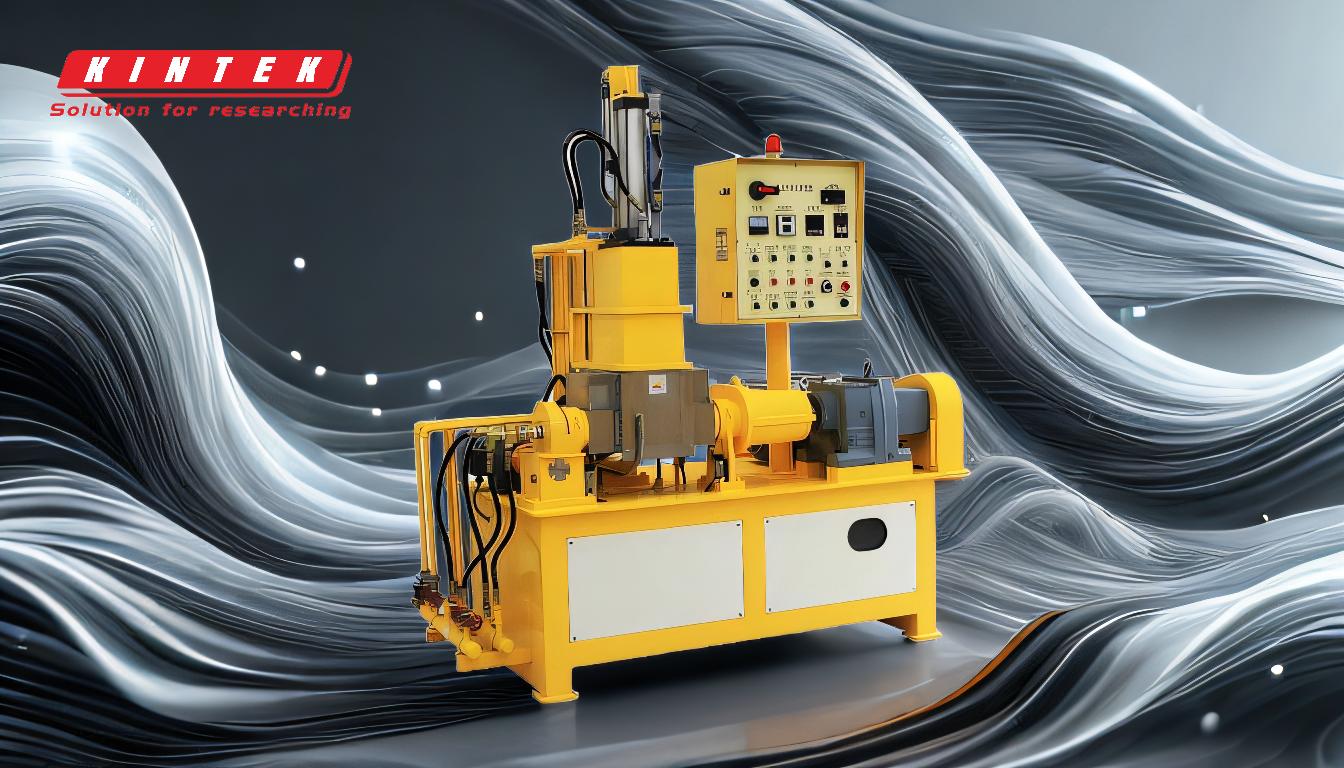
-
Tangential Type (MX Series) Internal Mixers:
- Design: In tangential mixers, the rotors are designed so that their blades move tangentially to each other without overlapping. This creates a high shear force between the rotors and the chamber walls.
-
Advantages:
- High Shear Rates: The design allows for rapid mixing and high shear, which is ideal for materials requiring intense mechanical action.
- Flexibility: Suitable for a wide range of materials, including rubber and plastics.
- Efficiency: Faster mixing times due to the high rotational speeds and shear forces.
- Applications: Commonly used in rubber compounding, where high shear is necessary to break down agglomerates and disperse fillers evenly.
-
Intermeshing Type (IMX Series) Internal Mixers:
- Design: In intermeshing mixers, the rotors are designed to interlock or mesh with each other. This creates a more controlled and uniform mixing action.
-
Advantages:
- Better Dispersion: The intermeshing action ensures a more uniform distribution of materials, making it ideal for applications requiring precise mixing.
- Lower Shear Rates: The design is gentler on materials, which is beneficial for heat-sensitive compounds.
- Energy Efficiency: The intermeshing action reduces the energy required for mixing, as the rotors work together rather than against each other.
- Applications: Often used in the production of high-performance rubber compounds and specialty plastics where uniform dispersion and controlled mixing are critical.
-
Comparison and Selection Criteria:
- Material Properties: The choice between tangential and intermeshing mixers depends on the material being processed. For example, materials requiring high shear and rapid mixing are better suited for tangential mixers, while those needing gentle, uniform mixing benefit from intermeshing mixers.
- Production Requirements: Consider the desired output quality, mixing time, and energy consumption. Tangential mixers are faster but may consume more energy, whereas intermeshing mixers are more energy-efficient but may take longer to achieve the desired mix.
- Operational Environment: The operating temperature and the sensitivity of the materials to heat should also be considered. Intermeshing mixers are generally better for heat-sensitive materials due to their lower shear rates.
-
Maintenance and Durability:
- Tangential Mixers: These mixers may require more frequent maintenance due to the high shear forces and wear on the rotors and chamber walls.
- Intermeshing Mixers: These mixers tend to have a longer lifespan and require less maintenance because the intermeshing action reduces wear and tear on the components.
-
Cost Considerations:
- Initial Investment: Tangential mixers may have a lower initial cost but could incur higher maintenance costs over time. Intermeshing mixers, while potentially more expensive upfront, may offer lower long-term costs due to their durability and energy efficiency.
- Operational Costs: Energy consumption and maintenance costs should be factored into the total cost of ownership when selecting between the two types.
By understanding the differences between tangential and intermeshing internal mixers, purchasers can make informed decisions based on their specific production needs, material properties, and budget constraints.
Summary Table:
Feature | Tangential Mixers (MX Series) | Intermeshing Mixers (IMX Series) |
---|---|---|
Design | Blades move tangentially | Rotors interlock for uniform mixing |
Shear Rates | High shear, faster mixing | Lower shear, gentler on materials |
Dispersion | Suitable for high-shear materials | Better dispersion, uniform mixing |
Energy Efficiency | Higher energy consumption | More energy-efficient |
Applications | Rubber compounding, high shear | High-performance rubber, plastics |
Maintenance | More frequent due to high shear | Less frequent, longer lifespan |
Cost | Lower initial, higher maintenance | Higher initial, lower long-term |
Need help selecting the right internal mixer for your production? Contact our experts today for personalized advice!