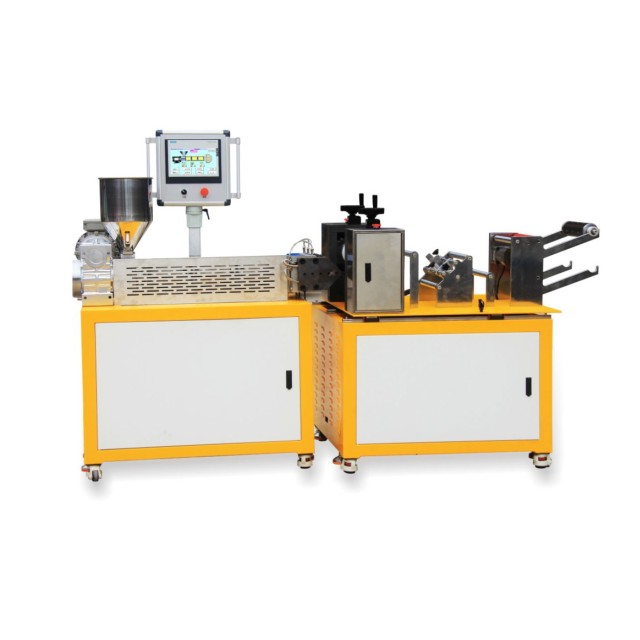
Rubber processing machine
Lab Plastic PVC Calender Stretch Film Casting Machine for Film Testing
Item Number : RPM-02
Price varies based on specs and customizations
- Screw diameter
- 25mm(or customized)
- L:D(Ratio of length to diameter)
- 33:1(or customized)
- Screw speed
- 0-95rpm(Frequency conversion speed regulation)
- Motor power
- 4KW(or customized)
- Die lip width
- 300mm(or customized)
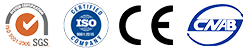
Shipping:
Contact us to get shipping details Enjoy On-time Dispatch Guarantee.
Why Choose Us
Reliable PartnerEasy ordering process, quality products, and dedicated support for your business success.
Introduction
The cast film machine is designed for the molding of cast film products of polymer materials. It has multiple processing functions such as casting, extrusion, stretching, and compounding, and realizes program-controlled integrated linkage through the PLC system to ensure precise process. Product features include cast film molding of various polymer materials, high-precision guide rails of hidden calender units, and imported melt metering pumps and pressure sensors. Its application range covers cast product research and development, formula optimization, quality control, process parameter optimization, and teaching and scientific research.
Detail & Parts
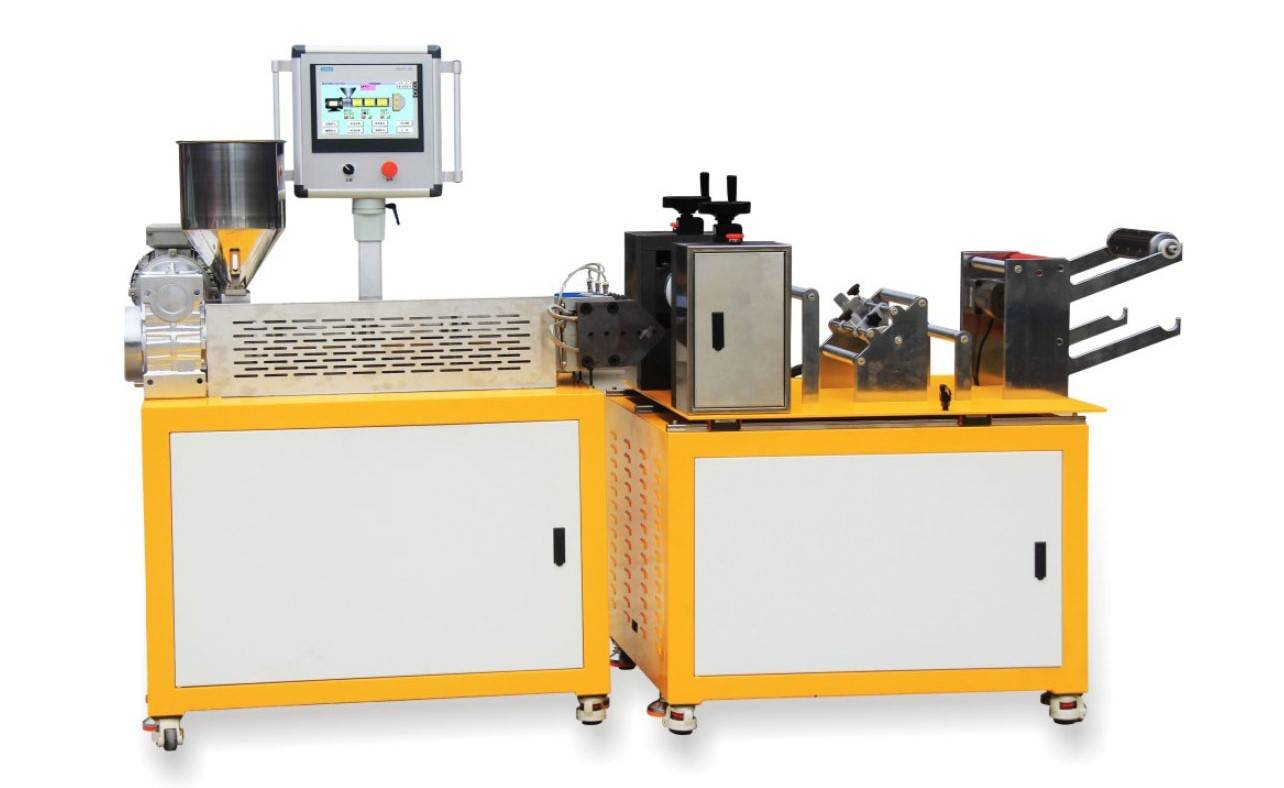
The Single layer cast film machine :Focusing on the industry research of polymer material cast film product molding, sheet extrusion molding, material performance testing, process optimization, product quality testing, etc. It can complete molding and processing tests such as extrusion, casting, stretching, and compounding;
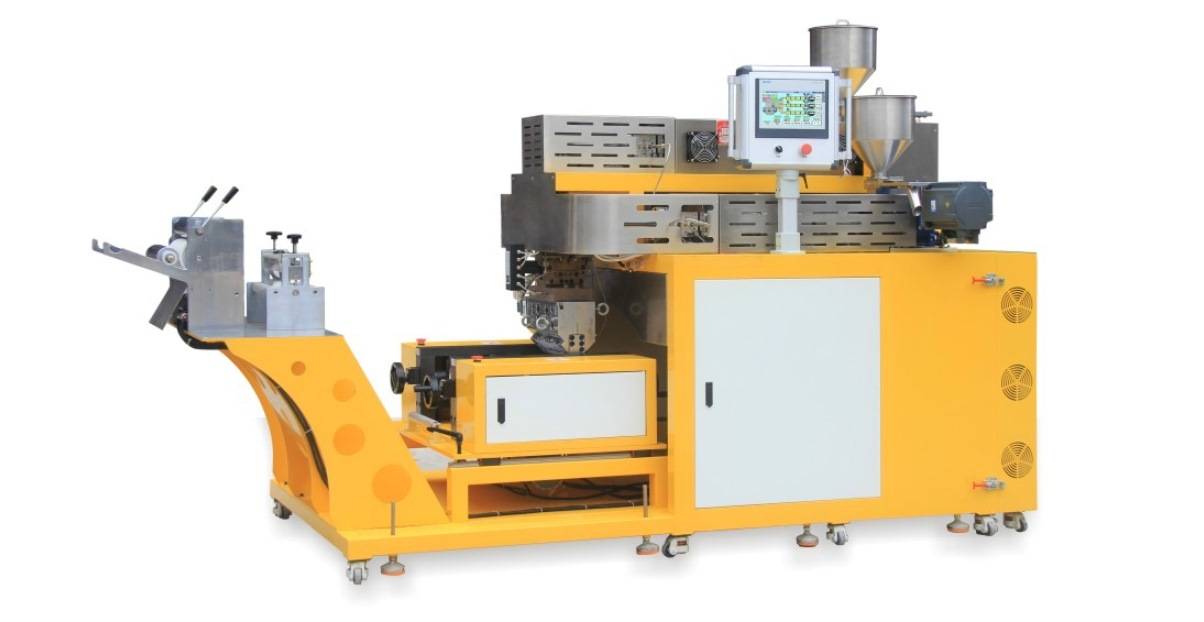
- Multi-layer co extrusion casting film machine
- After multiple polymer melts are collected through the co-extrusion die, they become a film melt flow composed of multiple layers of different polymer melts, and after cooling, a multi-layer co-extruded film or sheet is obtained;
- The integrated linkage of PLC system program control to complete extrusion, melt metering, melt pressure monitoring, casting, calendering, winding or cutting and other processes.
- The imported melt metering pump is equipped with a pressure sensor to monitor the melt pressure, ensuring that the melt flow rate is always consistent.

Application
- Film forming simulation: Through calendering or stretching process, the film forming process in actual production is simulated to ensure that the film prepared in the laboratory has similar structure and performance to the film in industrial production.
- Performance testing: The prepared film can be used for various performance tests, such as tensile strength, elongation at break, heat shrinkage, light transmittance, haze, etc., to evaluate the quality and applicability of the film.
- Formulation optimization: By adjusting the raw material formula and process parameters, the laboratory calender/stretch cast film machine can help researchers optimize the film formula to achieve specific performance requirements.
- New material development: For the development of new materials, this equipment can be used to quickly evaluate the forming performance and potential applications of new materials, and accelerate the transformation process of new materials from laboratory to industrial production.
- Quality control: During the production process, laboratory equipment can be used for sampling and testing to ensure that the quality of each batch of film meets the standards and reduce the defective rate.
Features
- Versatility: supports cast film forming and laminating processes of various polymer materials to meet the processing requirements of different materials.
- PLC system program control linkage: through the advanced PLC system, the integrated control of extrusion, casting, calendering and winding processes is realized to improve production efficiency and operation convenience.
- Hidden calendering unit: adopts high-precision guide rails to ensure smooth operation, and at the same time facilitates the disassembly and cleaning of the mold to reduce maintenance time.
- Multi-layer co-extrusion technology: multiple polymer melts are collected through the co-extrusion die to form a film melt flow composed of multiple layers of different polymer melts, and after cooling, a multi-layer co-extruded film or sheet is obtained.
- Precision control: equipped with imported melt metering pumps and pressure sensors, real-time monitoring of melt pressure, ensuring the consistency of melt flow, thereby ensuring product quality.
Technical specifications
Model No. | RPM-02A | RPM-02B |
---|---|---|
Name | Single layer | Three layers |
Screw diameter | 25mm(or customized) | |
L:D(Ratio of length to diameter) | 33:1(or customized) | |
Screw speed | 0-95rpm(Frequency conversion speed regulation) | |
Motor power | 4KW(or customized) | |
Die lip width | 300mm(or customized) | |
Optional configuration | 3CC melt pump or customized、Manual or hydraulic screen changer、Pressure sensor、Pressure sensor、Unwinding device | |
calendering part | 160x350mmx2or customized | |
Installation method of calender roller | Vertical or parallel | |
Winding device | Friction winding | |
(W*D*H) Volume | 2800*800*1650mm | 3500*1600*2200mm |
Weight(kg) | ≈750kg | ≈1.2T |
Power Supply | 3∮,AC380V |
FAQ
What Is A Casting Film Machine, And How Does It Work?
What Are The Primary Applications Of Casting Film Machines?
What Are The Advantages Of Using A Casting Film Machine Over Other Film Production Methods?
What Are The Key Parameters To Consider When Operating A Casting Film Machine?
How Does A Casting Film Machine Ensure Uniform Film Thickness And Quality?
4.7
out of
5
Incredible speed and precision, a game-changer for our lab!
4.8
out of
5
Top-notch quality and durability, worth every penny.
4.9
out of
5
Technologically advanced, simplifies our casting process beautifully.
4.7
out of
5
Efficient and reliable, a must-have for any dental lab.
4.8
out of
5
Outstanding value for money, highly recommend!
4.9
out of
5
Revolutionary technology, enhances our lab's capabilities.
4.7
out of
5
Fast delivery and excellent customer service.
4.8
out of
5
Impressive build quality, very durable.
4.9
out of
5
State-of-the-art features, boosts our productivity.
4.7
out of
5
Exceptional performance, exceeded our expectations.
4.8
out of
5
User-friendly and efficient, a great addition to our lab.
4.9
out of
5
Highly advanced, perfect for precision casting needs.
4.7
out of
5
Reliable and sturdy, handles high workloads with ease.
4.8
out of
5
Innovative design, enhances our casting accuracy.
4.9
out of
5
Excellent value and support, couldn't be happier.
Products
Lab Plastic PVC Calender Stretch Film Casting Machine for Film Testing
REQUEST A QUOTE
Our professional team will reply to you within one business day. Please feel free to contact us!
Related Products
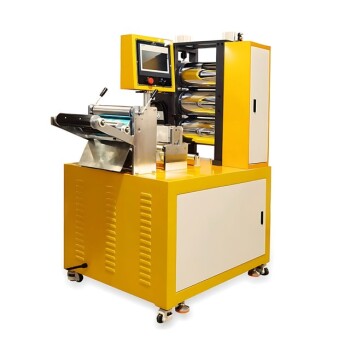
Small Lab Rubber Calendering Machine
Small lab rubber calendering machine is used for producing thin, continuous sheets of plastic or rubber materials. It is commonly employed in laboratories, small-scale production facilities, and prototyping environments to create films, coatings, and laminates with precise thickness and surface finish.
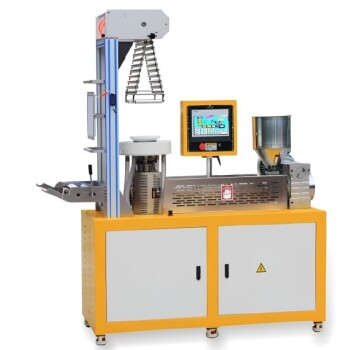
Lab Blown Film Extrusion Three Layer Co-Extrusion Film Blowing Machine
Lab blown film extrusion is mainly used to detect the feasibility of film blowing of polymer materials and the colloid condition in the materials, as well as the dispersion of colored dispersions, controlled mixtures, and extrudates;
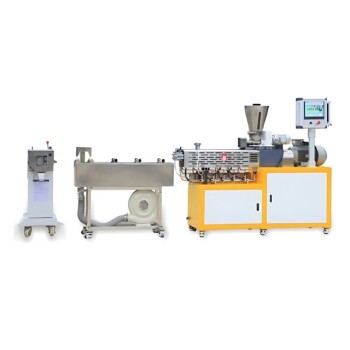
Twin Screw Extruder Plastic Granulation Machine
Twin screw extruder plastic granulation machine is designed for the mixing and processing experiments of engineering plastics, modified plastics, waste plastics and masterbatches.
Related Articles
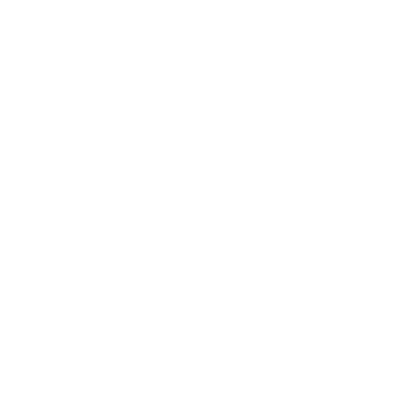
Electron Beam Evaporation Coating: Advantages, Disadvantages, and Applications
An in-depth look at the pros and cons of electron beam evaporation coating and its various applications in industries.
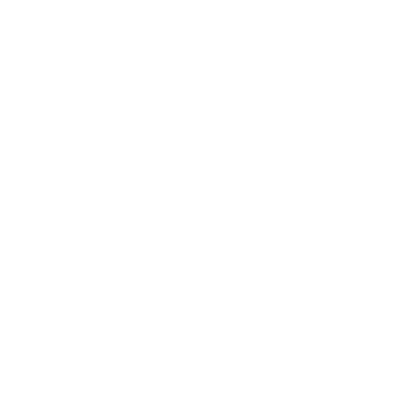
Thin Film System Design: Principles, Considerations, and Practical Applications
An in-depth exploration of thin film system design principles, technological considerations, and practical applications in various fields.
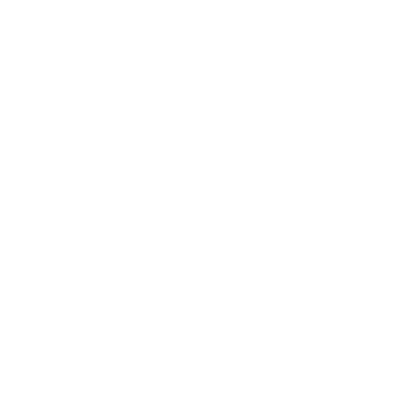
Controlling Film Thickness Tolerance in Magnetron Sputtering Coating
Discusses methods to ensure film thickness tolerance in magnetron sputtering coating for optimal material performance.
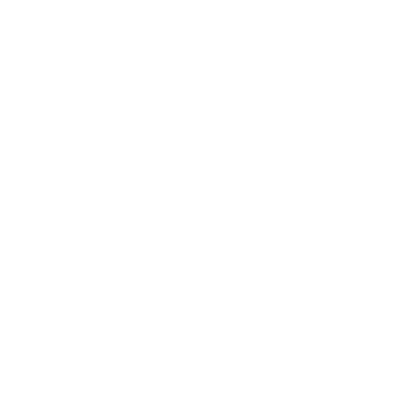
Electron Beam Evaporation: Advanced Thin Film Creation
Explores the technology and applications of electron beam evaporation in thin film production.
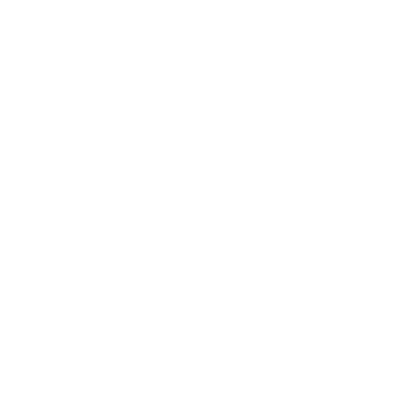
What is Isostatic Pressing Machine
Isostatic molding is a molding method that uses the incompressibility of a liquid medium and the uniform transfer of pressure. It is suitable for powder dense parts with equal pressure in all directions. The principle is to fill the mold with a liquid medium, such as water, and then subject the mold to uniform pressure. The pressure is applied by a piston or a flexible membrane.
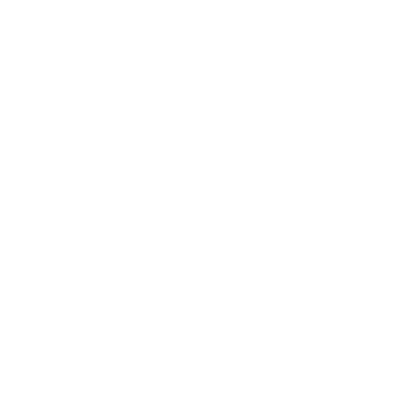
Isostatic Pressing Technology: Principles, Classification, and Applications
An in-depth look at isostatic pressing technology, its types, and diverse applications across various industries.
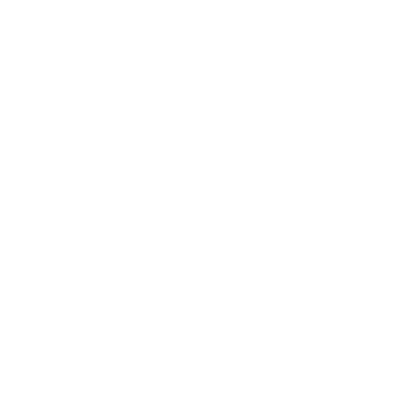
Comprehensive Guide to Isostatic Pressing:Processes, and Features
Isostatic pressing is a versatile manufacturing process that is widely used in various industries. It involves subjecting a material to equal pressure from all directions to achieve uniform density and shape. Isostatic pressing offers numerous advantages, such as the ability to produce complex shapes, uniformity in material properties, and high precision. This comprehensive guide will delve into the different types of isostatic pressing, including cold, warm, and hot pressing. We will explore the processes, features, and applications of each type, providing you with a thorough understanding of this essential manufacturing technique. So let's dive in!
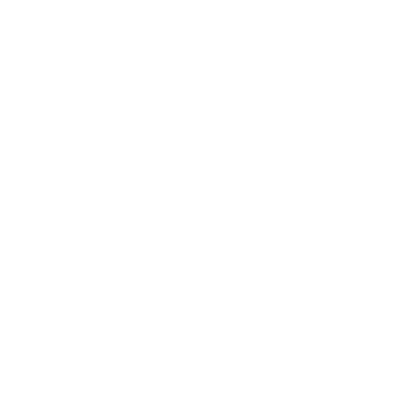
Zirconia Ceramic Rod Production Processes: Isostatic Pressing vs. Dry Pressing
A comparison of isostatic pressing and dry pressing in zirconia ceramic rod production, highlighting differences and advantages.
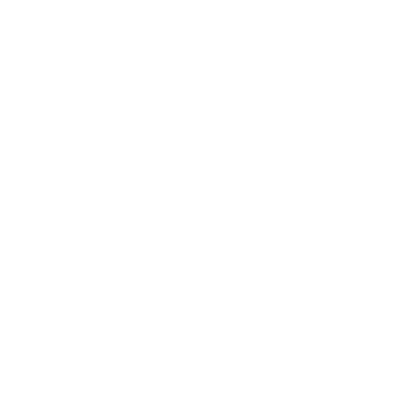
Selecting Isostatic Pressing Equipment for High-Density Molding
An in-depth look at isostatic pressing techniques and equipment selection for achieving high-density molding.
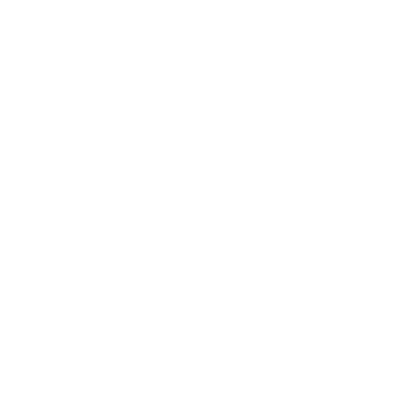
Comprehensive Guide to Isostatic Pressing: Types, Processes, and Features(3)
Isostatic pressing is a versatile manufacturing process that is widely used in various industries. It involves subjecting a material to equal pressure from all directions to achieve uniform density and shape. Isostatic pressing offers numerous advantages, such as the ability to produce complex shapes, uniformity in material properties, and high precision.
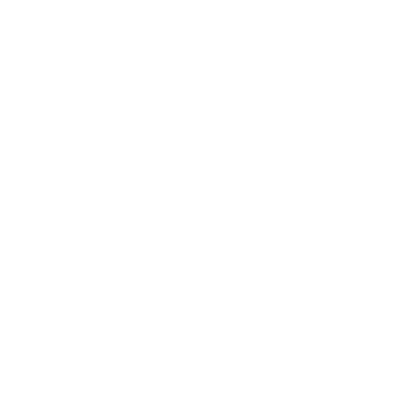
Isostatic Pressing Technology: Revolutionizing Ceramic Material Densification
Explore how isostatic pressing techniques enhance ceramic properties, achieving 100% theoretical density and eliminating porosity.
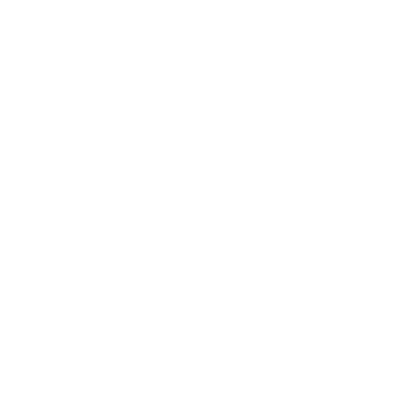
Understanding Isostatic Pressing: Process, Benefits, Limitations, and Applications
Isostatic pressing is a manufacturing process that offers numerous benefits and applications in various industries. It involves subjecting a material to equal pressure from all directions to achieve uniform density and shape. This method is particularly advantageous compared to other production techniques.