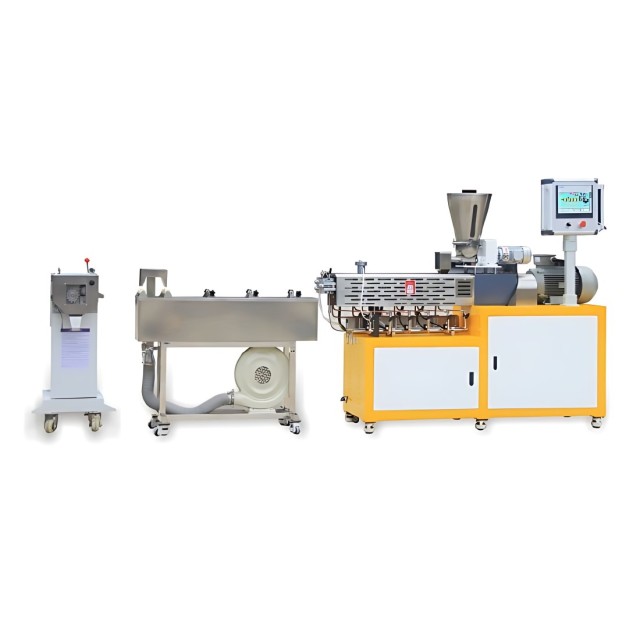
Rubber processing machine
Twin Screw Extruder Plastic Granulation Machine
Item Number : RPM-03
Price varies based on specs and customizations
- Control system
- PLC control
- Feeder
- Twin screw quantitative feeding or customized
- Cooling device
- Air/water cooling (optional)
- Cutting device
- Water strips/underwater cutting/hot cutting
- Screen changer
- Manual screen changer
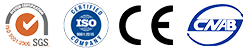
Shipping:
Contact us to get shipping details Enjoy On-time Dispatch Guarantee.
Why Choose Us
Reliable PartnerEasy ordering process, quality products, and dedicated support for your business success.
Introduction
Twin screw extruder plastic granulation machine is designed for the mixing and processing experiments of engineering plastics, modified plastics, waste plastics and masterbatches. This machine not only has the functions of homogenization, plasticizing, coloring and filling modification, but also can meet various complex processing needs, ensuring efficient material processing and the quality of the final product.
The continuous rotation of the screw repeatedly forces the material to turn, which helps to evenly mix and plasticize the material. Under the heating, mixing, shearing, plasticizing, compacting and exhausting of the twin-screw extruder, the material is plasticized into a uniform melt, and under the extrusion of the twin screw, a round strip material is extruded through the die head, cooled by water in a cooling water tank, and then diced by a pelletizer to obtain plastic pellets.
Detail & Parts
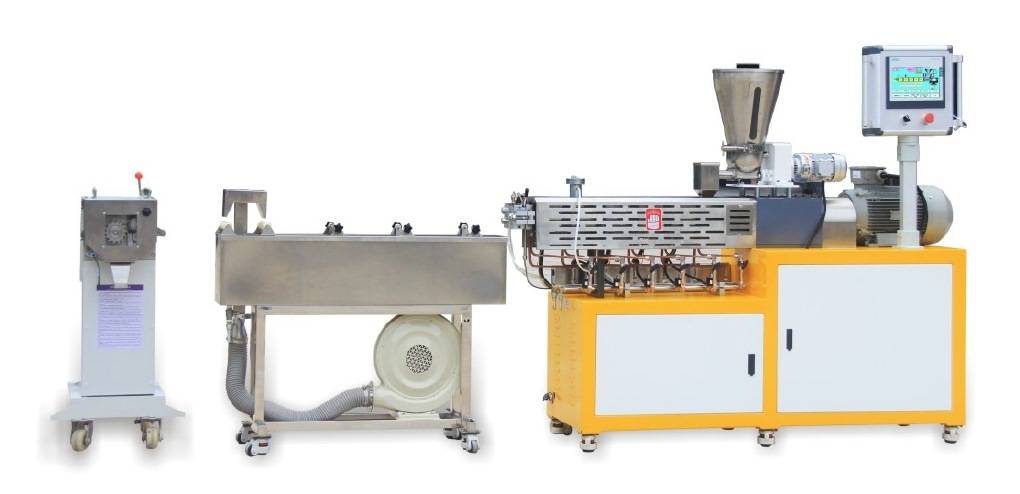
Water cooled strips series granulation machine
- PLC control system with automatic program control;
- Twin-screw quantitative feeding and side feeding are available, suitable for granular materials, powder materials and liquid materials;
- Building block screw elements have strong self-cleaning ability, and the screw combination can be adjusted according to process needs to achieve multi-purpose use of one machine;
- Quick manual screen changer to increase plasticized polymer and filter out impurities in the melt;
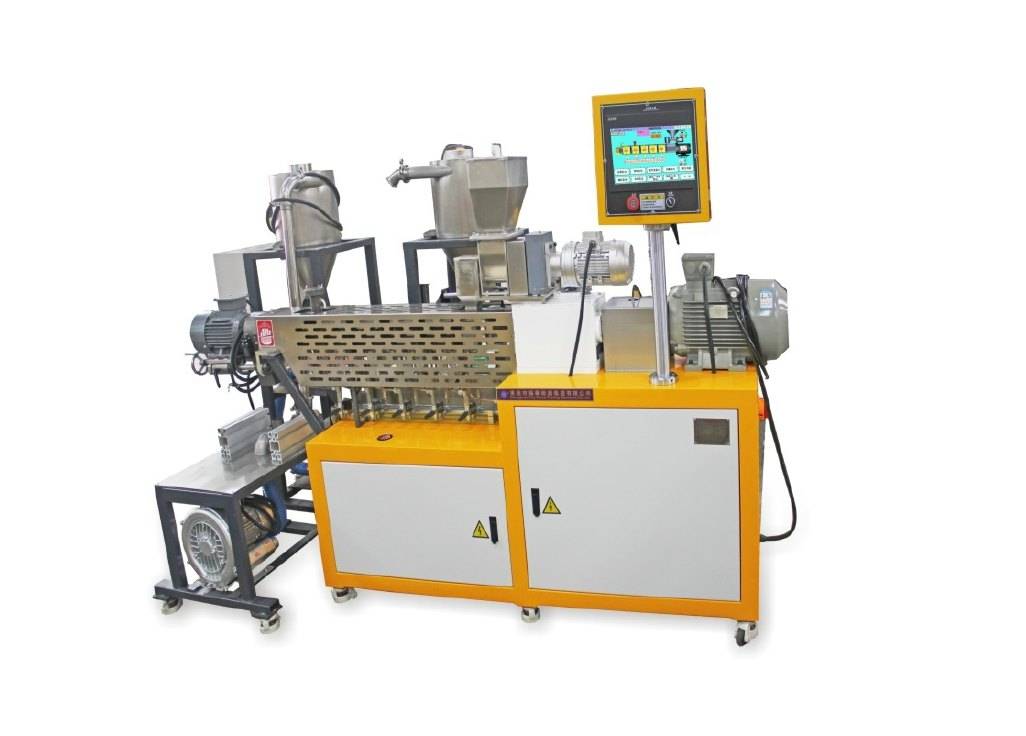
- Used for extrusion granulation of various highly filled polymers such as plastics, rubber, metal powder, etc.;
- The continuous operation is stable, requires fewer operators, is highly efficient, and saves costs;
- The screw barrel has strong self-cleaning ability, and material replacement is simple and quick;
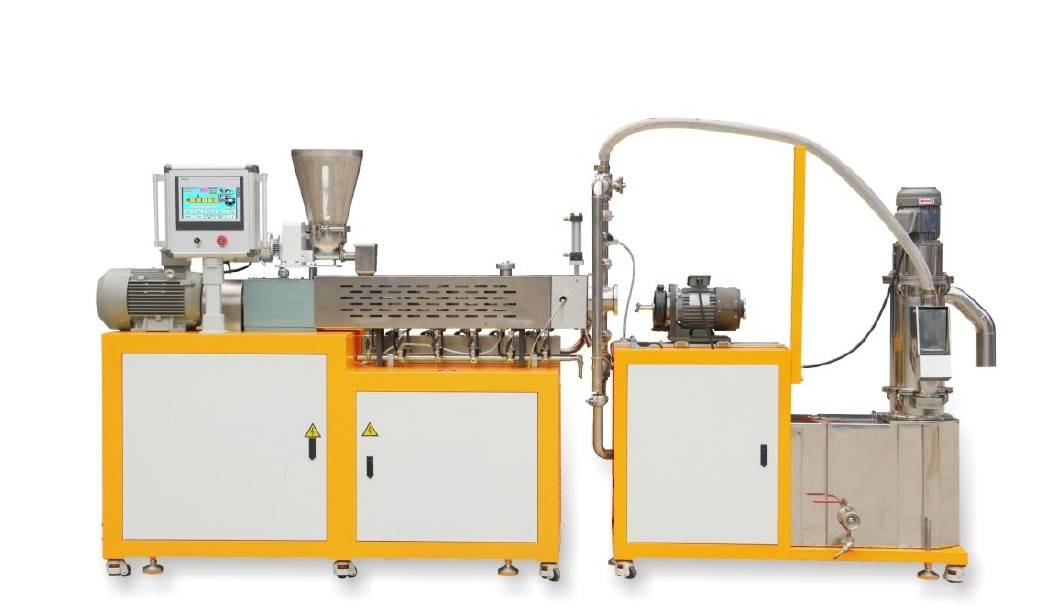
- Used for thermoplastic elastomers, hot melt adhesives, blended modified materials, etc.;
- It consists of a twin-screw extruder, die head, pelletizer head, water circulation system, dehydration, etc.;
- The particle surface is smooth and uniform, with high density, good fluidity and less adhesion;
- The closed circulation process pipeline shortens the curing time and is pollution-free, clean and environmentally friendly;
Application
- Polymer material mixing and mixing extrusion granulation: suitable for mixing and granulation of various polymer materials to ensure the uniformity and consistency of materials.
- Composite material blending modification and reaction extrusion: support composite material blending and reaction extrusion, improve the performance and application range of materials.
- High-efficiency mixing of polymer alloys: can efficiently process polymer alloys and achieve uniform mixing of materials.
- Polymer filling and enhancement modification: improve the mechanical properties and durability of polymers through filling and enhancement modification.
- Material dehydration, devolatilization and exhaust: effectively remove moisture and volatile substances in materials to ensure product quality.
Product features
- PLC control system: adopts automatic program control to ensure the accuracy and consistency of operation.
- Twin screw quantitative feeding: supports multiple feeding methods of granular materials, powder materials and liquid materials, and flexibly adapts to the needs of different materials.
- Building block screw element: strong self-cleaning ability, the screw combination can be adjusted according to process needs, realizing one machine for multiple uses, and improving the flexibility and versatility of the equipment.
- Fast manual screen changer: increases plasticized polymer and filters out impurities in the melt to ensure the purity and quality of the product.
Technical specifications
Model No. | RPM-03A | RPM-03B |
---|---|---|
Control system | PLC controlPLC control | |
Capacity (kg) | About 1-10kg/h(decide by formula ) | About 30kg/h(decide by formula ) |
Feeder | Twin screw quantitative feeding or customized | |
Screw diameter | 21.7mm(or customized) | 35mm(or customized) |
L:D(Length to diameter ratio) | 40 : 1 | 40:1-48:1 |
rpm Screw speed | 0-300rpm | 0-500rpm |
Motor | 4KW | 18.5KW |
Cooling device | Air/water cooling (optional) | |
Cutting device | Water strips/underwater cutting/hot cutting | |
Screen changer | Manual screen changer | |
Power | 12KW | 25KW |
Volume (mm)(W*D*H) | 4000*550*1600mm | 6800*960*1940mm |
Weight (kg) | About 580kg | About 1900kg |
Power Supply | 3∮, AC380V |
FAQ
What Is A Twin Screw Extruder Granulator, And How Does It Work?
What Are The Primary Applications Of A Twin Screw Extruder Granulator?
What Are The Advantages Of Using A Twin Screw Extruder Granulator Over A Single Screw Extruder?
What Are The Key Parameters To Consider When Operating A Twin Screw Extruder Granulator?
How Does A Twin Screw Extruder Granulator Ensure Uniform Granule Size And Quality?
4.7
out of
5
Incredible value for money, top-notch quality!
4.8
out of
5
Fast delivery, durable and technologically advanced.
4.7
out of
5
Excellent machine, highly recommend for any lab.
4.9
out of
5
Best investment for our rubber processing needs.
4.8
out of
5
Superb durability and efficiency, worth every penny.
4.7
out of
5
Technologically advanced, simplifies our workflow.
4.9
out of
5
Outstanding quality and customer service.
4.8
out of
5
Quick delivery, excellent for high-demand labs.
4.7
out of
5
Impressive technology, enhances our research.
4.9
out of
5
Reliable and robust, perfect for our needs.
4.8
out of
5
Highly durable, meets all our processing demands.
4.7
out of
5
Great value, simplifies complex processes.
4.9
out of
5
Exceptional quality, enhances lab productivity.
4.8
out of
5
Technologically superior, highly efficient.
4.7
out of
5
Durable and reliable, excellent for long-term use.
4.9
out of
5
Top-tier performance, exceeds expectations.
4.8
out of
5
Quick and efficient, perfect for our lab.
4.7
out of
5
Highly recommend for any rubber processing needs.
4.9
out of
5
Outstanding technology and durability.
Products
Twin Screw Extruder Plastic Granulation Machine
REQUEST A QUOTE
Our professional team will reply to you within one business day. Please feel free to contact us!
Related Products
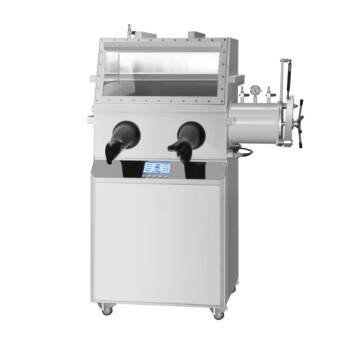
Laboratory Hydraulic Press Lab Pellet Press Machine for Glove Box
Controlled environment lab press machine for glove box. Specialized equipment for material pressing and shaping with high precision digital pressure gauge.
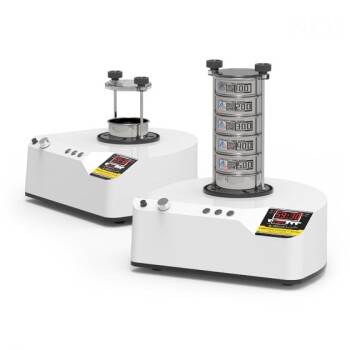
Three-dimensional electromagnetic sieving instrument
KT-VT150 is a desktop sample processing instrument for both sieving and grinding. Grinding and sieving can be used both dry and wet. The vibration amplitude is 5mm and the vibration frequency is 3000-3600 times/min.