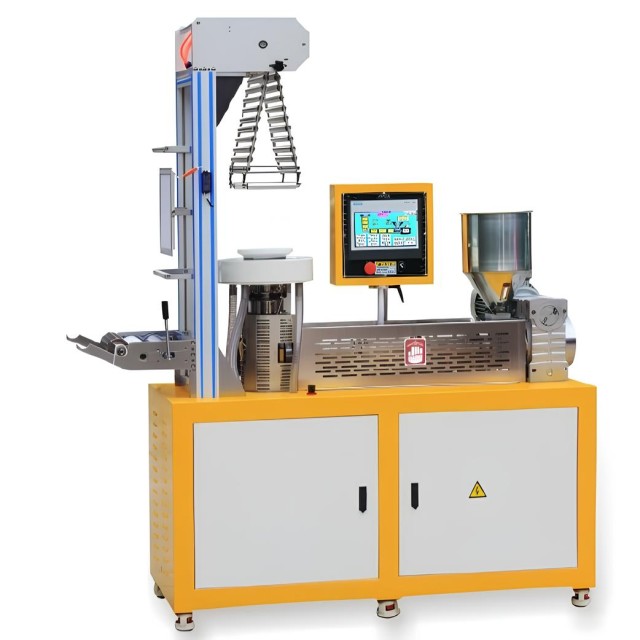
Rubber processing machine
Lab Blown Film Extrusion Three Layer Co-Extrusion Film Blowing Machine
Item Number : RPM-05
Price varies based on specs and customizations
- Screw aspect ratio (L/D)
- 33:1(or customized)
- Screw speed
- 0-95rpmFrequency conversion speed regulation
- Motor (kg)
- Variable frequency motor or servo motor
- Main motor power
- 4KW(or customized)
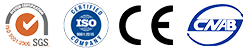
Shipping:
Contact us to get shipping details Enjoy On-time Dispatch Guarantee.
Why Choose Us
Reliable PartnerEasy ordering process, quality products, and dedicated support for your business success.
Introduction
Lab blown film extrusion is mainly used to detect the feasibility of film blowing of polymer materials and the colloid condition in the materials, as well as the dispersion of colored dispersions, controlled mixtures, and extrudates;
Detail & Parts
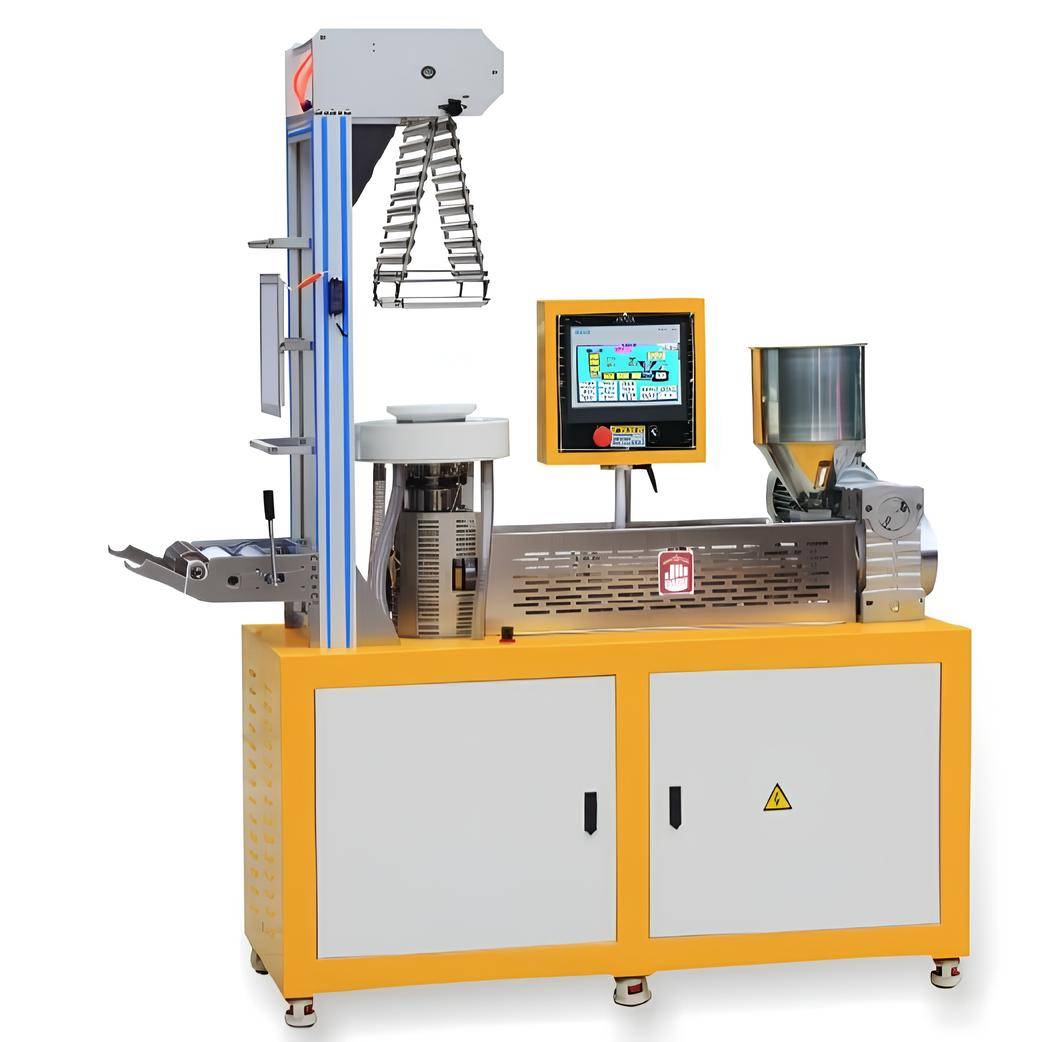
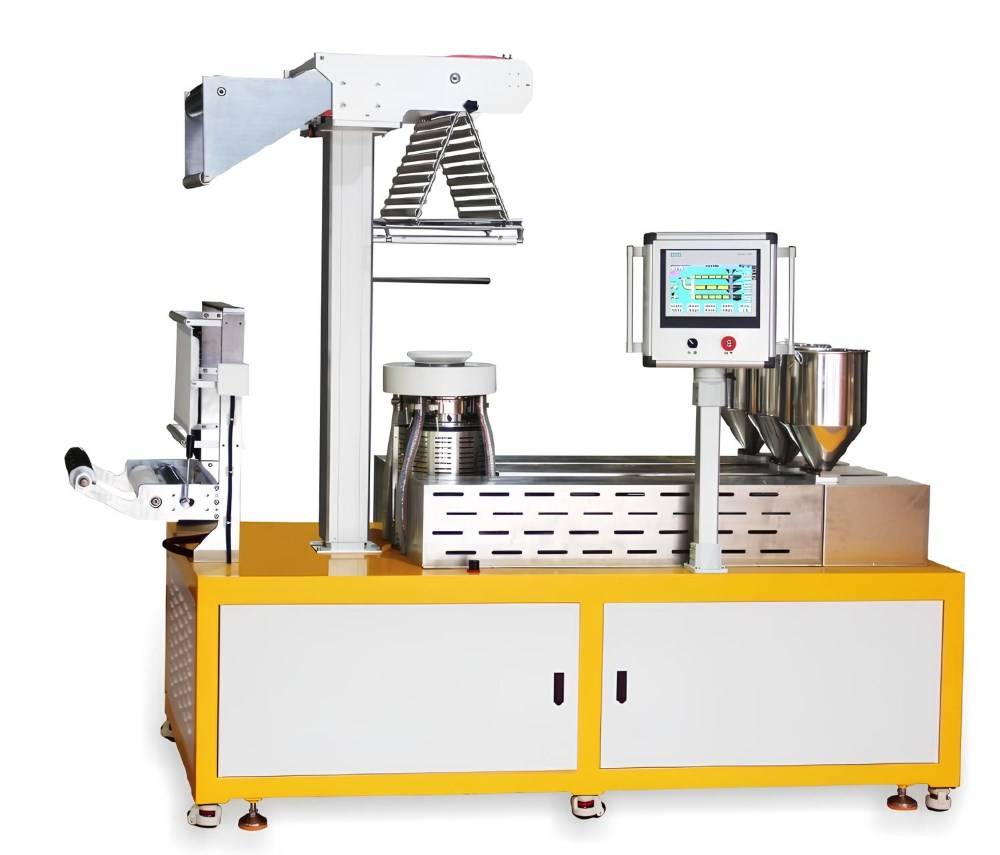
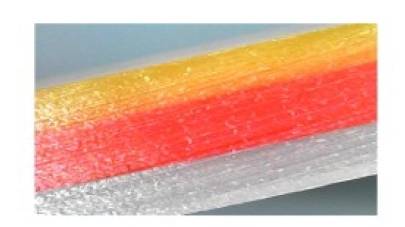
Application
The lab blown film extrusion is a small film blowing equipment specially designed for laboratory environment. It is usually used for scientific research, teaching and small batch production. Compared with large-scale industrial film blowing machines, laboratory film blowing machines have the characteristics of small size, easy operation and low cost. The application scope of laboratory film blowing machines mainly includes the following aspects:
Scientific research experiments: In the fields of materials science, chemistry, bioengineering, etc., researchers use laboratory film blowing machines to prepare various plastic films for performance testing, structural analysis and application research.
Teaching demonstration: In the relevant professional teaching of colleges and universities and vocational and technical schools, laboratory film blowing machines are often used to demonstrate the production process of plastic films to help students understand the principles and operation methods of film blowing technology.
Small batch production: For enterprises or individuals who need to produce plastic films on a small scale, laboratory film blowing machines can meet their needs for films with specific specifications and performances, especially in the product development and trial production stages.
Customized service: Some laboratory film blowing machines can also provide customized services, producing films of specific specifications, colors, and thicknesses according to the special needs of customers to meet personalized needs.
Principle
Lab blown film extrusion is a process used to produce thin plastic films, typically from thermoplastic materials such as polyethylene (PE), polypropylene (PP), and others. This process is commonly used in research and development (R&D) laboratories to create small batches of film for testing and prototyping purposes. The lab-scale equipment allows for precise control over the process parameters, enabling the development of custom film properties.
Features
Detect the feasibility of film blowing of various polymer composite materials;
The three-layer co-extrusion structure improves the transverse and longitudinal tensile strength of the film and the puncture resistance to form a multifunctional plastic film;
The unique ABC three-layer co-extrusion flow channel design has uniform thickness and stable melt pressure, which is suitable for different composite materials;
Technical specifications
Model No. | RPM-05A | RPM-05B |
---|---|---|
Name | Single layer blown film | Three layer co-extrusion blown film |
Screw diameter | 25mm or customized | 25mm *3 or customized |
Screw aspect ratio (L/D) | 33:1(or customized) | |
Screw speed | 0-95rpmFrequency conversion speed regulation | |
Motor (kg) | Variable frequency motor or servo motor | |
Main motor power | 4KW(or customized) | |
Die diameter | 25mm( or customized) | 30mm( or customized) |
Max diameter of the film | 150-180mm( or customized) | 300mm( or customized) |
Volume(mm)(W*D*H) | 1800*800*2000mm | 2100*950*2300mm |
Weight(kg) | about 450kg | about 1100 kg |
Power supply | 3∮,AC380V | |
※Special models can be designed according to customers ' requirements. |
FAQ
What Is The Primary Purpose Of Using A Lab Blown Film Extrusion Machine?
What Types Of Materials Are Commonly Used In Lab Blown Film Extrusion?
How Does The Extruder Melt The Plastic Material?
What Is The Function Of The Screen Pack And Breaker Plate In The Extrusion Process?
How Is The Bubble Formed In The Blown Film Extrusion Process?
Why Is The Bubble Pinched At The Bottom During The Extrusion Process?
What Factors Can Be Adjusted To Control The Thickness Of The Film?
How Is The Quality Of The Film Assessed During The Extrusion Process?
Can Multi-layer Films Be Produced Using A Lab Blown Film Extrusion Machine?
What Are The Methods Used To Deposit Thin Films?
What Is Thin Film Deposition Equipment?
What Is Thin-film Deposition Technology?
What Are The Advantages Of Using Thin Film Deposition Equipment?
What Factors Should Be Considered When Selecting Thin Film Deposition Equipment?
What Safety Considerations Are Associated With Operating Thin Film Deposition Equipment?
4.7
out of
5
Exceptional quality and durability. Ideal for our lab's needs.
4.8
out of
5
Fast delivery, excellent value for money. Highly recommend!
4.9
out of
5
Technologically advanced, simplifies our research process.
4.7
out of
5
Robust design, handles complex experiments with ease.
4.8
out of
5
User-friendly interface, saves time and boosts efficiency.
4.9
out of
5
Reliable performance, crucial for our critical research.
4.7
out of
5
Compact yet powerful, perfect for small lab spaces.
4.8
out of
5
Innovative features, enhances our film blowing experiments.
Products
Lab Blown Film Extrusion Three Layer Co-Extrusion Film Blowing Machine
REQUEST A QUOTE
Our professional team will reply to you within one business day. Please feel free to contact us!
Related Products
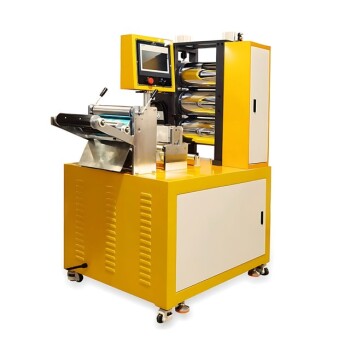
Small Lab Rubber Calendering Machine
Small lab rubber calendering machine is used for producing thin, continuous sheets of plastic or rubber materials. It is commonly employed in laboratories, small-scale production facilities, and prototyping environments to create films, coatings, and laminates with precise thickness and surface finish.
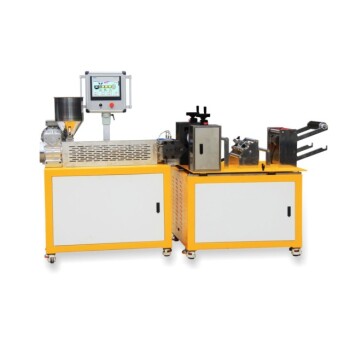
Lab Plastic PVC Calender Stretch Film Casting Machine for Film Testing
The cast film machine is designed for the molding of polymer cast film products and has multiple processing functions such as casting, extrusion, stretching, and compounding.
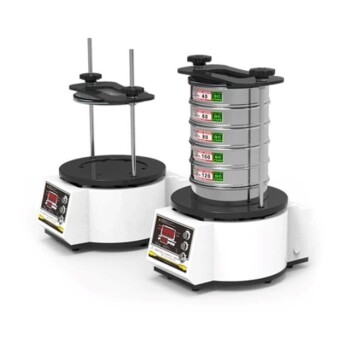
Vibratory Sieve Shaker Machine Dry Three-Dimensional Vibrating Sieve
The KT-V200 product focuses on solving common sieving tasks in the laboratory. It is suitable for sieving 20g-3kg dry samples.
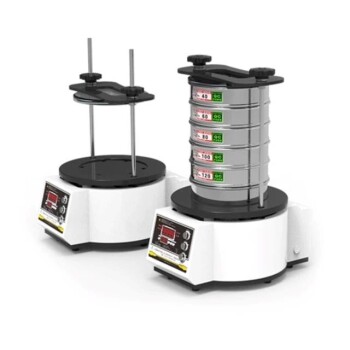
Laboratory Wet Three-Dimensional Vibratory Sieve Shaker Machine
The wet three-dimensional vibrating sieving instrument focuses on solving the sieving tasks of dry and wet samples in the laboratory. It is suitable for sieving 20g - 3kg dry, wet or liquid samples.
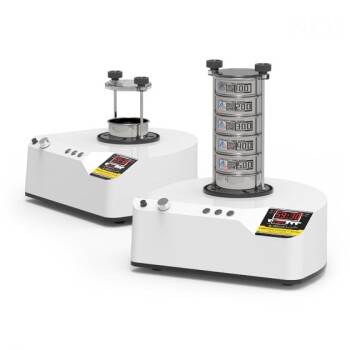
Three-dimensional electromagnetic sieving instrument
KT-VT150 is a desktop sample processing instrument for both sieving and grinding. Grinding and sieving can be used both dry and wet. The vibration amplitude is 5mm and the vibration frequency is 3000-3600 times/min.
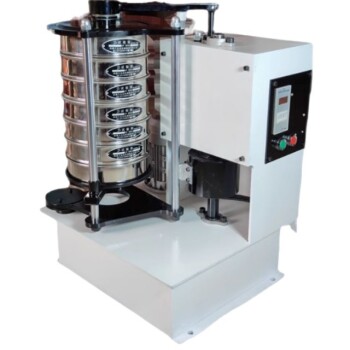
Laboratory Vibratory Sieve Shaker Machine Slap Vibrating Sieve
KT-T200TAP is a slapping and oscillating sieving instrument for laboratory desktop use, with 300 rpm horizontal circular motion and 300 vertical slapping motions to simulate manual sieving to help sample particles pass through better.
Related Articles
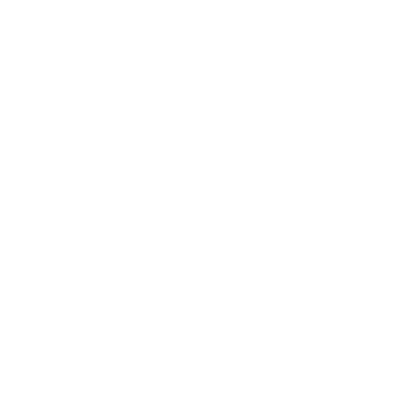
Thin Film System Design: Principles, Considerations, and Practical Applications
An in-depth exploration of thin film system design principles, technological considerations, and practical applications in various fields.
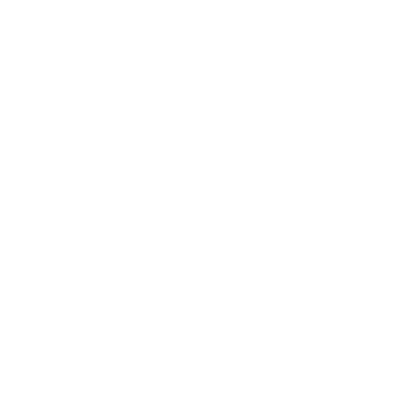
Electron Beam Evaporation Coating: Advantages, Disadvantages, and Applications
An in-depth look at the pros and cons of electron beam evaporation coating and its various applications in industries.
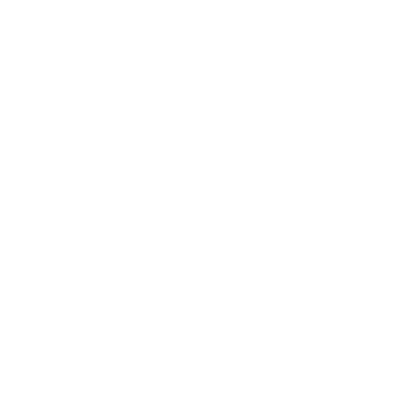
Controlling Film Thickness Tolerance in Magnetron Sputtering Coating
Discusses methods to ensure film thickness tolerance in magnetron sputtering coating for optimal material performance.
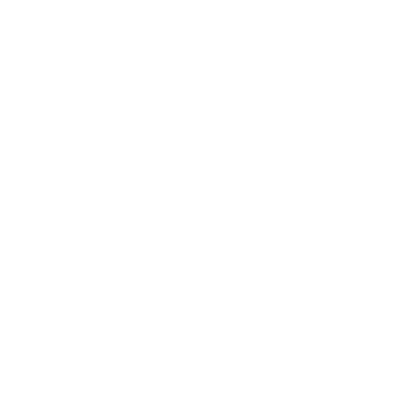
Electron Beam Evaporation: Advanced Thin Film Creation
Explores the technology and applications of electron beam evaporation in thin film production.
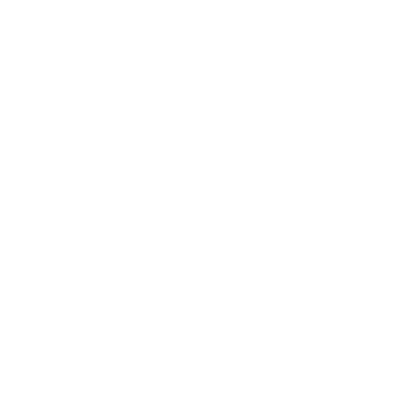
Measuring Peel Strength of Sputtered Film Layers
An in-depth guide on the definition, measurement methods, influencing factors, and equipment used for assessing peel strength of sputtered film layers.
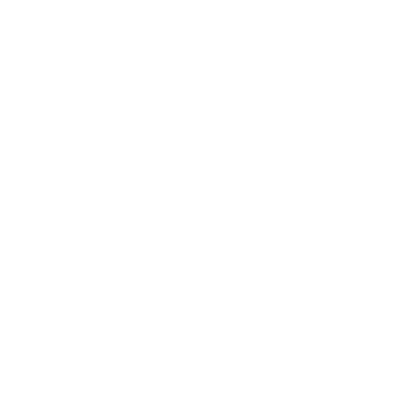
Impact of Various Power Supplies on Sputtered Film Morphology
This article discusses how different power supplies affect the morphology of sputtered film layers, focusing on DC, PDC, and RF power supplies.
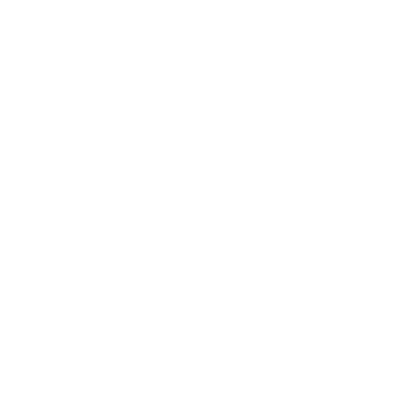
Introduction to the PECVD Deposition of Amorphous Silicon Process in Burst Film Formation
Explains the mechanism of burst film formation in PECVD deposition of amorphous silicon and solutions to prevent it.
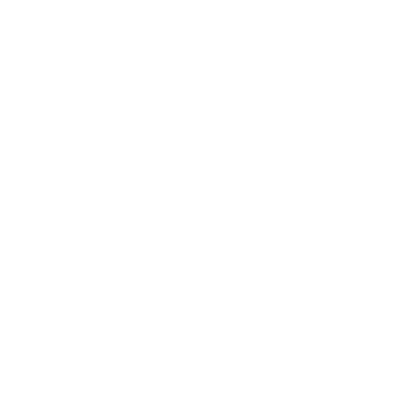
How to Choose and Optimize Water Circulating Vacuum Pumps for Your Lab
Learn how to choose and optimize water circulating vacuum pumps for lab applications, balancing efficiency and reliability.