Introduction
Isostatic pressing is a manufacturing process that offers numerous benefits and applications in various industries. It involves subjecting a material to equal pressure from all directions to achieve uniform density and shape. This method is particularly advantageous compared to other production techniques. Isostatic pressing enables the production of parts with complex internal shapes and long thin walls, which may not be easily achievable through other methods. However, it is important to consider the limitations of isostatic pressing, such as the lesser accuracy of pressed surfaces and lower production rates compared to alternative techniques.
Table of Contents
- Introduction
- Overview of Isostatic Pressing
- Advantages of Isostatic Pressing
- Disadvantages of Isostatic Pressing
- Dry Bag Isostatic Pressing
- Wet Bag Isostatic Pressing
- Uniaxial Versus Isostatic Pressing
- Powder Preparation for Isostatic Pressing
- Applications of Wet Bag Isostatic Pressing
- Applications of Dry Bag Isostatic Pressing
- Conclusion
Overview of Isostatic Pressing
Explanation of isostatic pressing
Isostatic pressing is a powder processing technique that uses fluid pressure to compact powder mixtures and reduce porosity. The powder mixture is encapsulated using isostatic pressure, which applies pressure equally from all directions. This process involves confining the metal powder within a flexible membrane or hermetic container, creating a pressure barrier between the powder and the pressurizing medium (liquid or gas) that surrounds it.
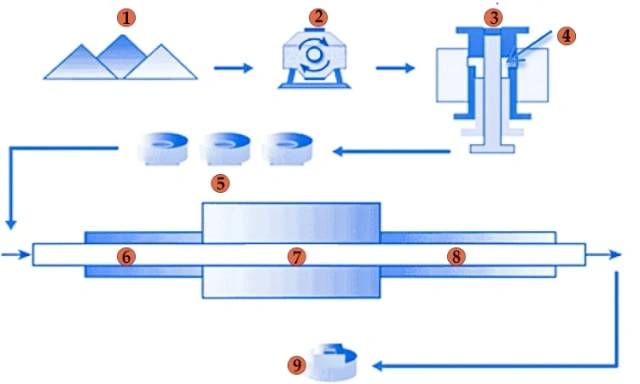
Types of isostatic pressing: wet bag and dry bag
There are two general types of isostatic pressing operations: wet bag and dry bag. The wet bag variation involves using a separate elastomeric mold that is loaded outside of the press and then submerged in the pressure vessel. After pressurization and compaction, the mold is removed from the vessel, the part is retrieved, and the process is repeated. Multiple molds can be loaded into the vessel for a single pressurization run.
On the other hand, the dry bag variation eliminates the immersion step by creating a mold that is integrated into the pressure vessel. In the dry bag process, the powder is added to the mold, the mold is sealed, pressure is applied, and then the part is ejected. The integrated mold in this process makes automation easier compared to the wet bag process.
Forming pressures for ceramics
Isostatic pressing offers unique benefits for ceramic and refractory applications. It applies a uniform and equal force over the entire product, regardless of its shape or size. This characteristic allows for the formation of product shapes with precise tolerances, reducing the need for costly machining. The isostatic pressing process has been widely used in the forming of high-temperature refractories, ceramics, cemented carbides, lanthanon permanent magnets, carbon materials, and rare metal powders.
Isostatic pressing has become a viable production tool used in various industries for consolidating powders or healing defects in castings. Its ability to achieve high compact densities and produce complex shapes has made it a preferred choice in many applications. However, it is important to note that the tooling cost and complexity of the process are higher compared to uniaxial pressing.
Advantages of Isostatic Pressing
Isostatic pressing offers several advantages over other production methods. Let's take a closer look at some of the benefits of isostatic pressing in comparison to other techniques:
Benefits of isostatic pressing in comparison to other production methods
- Low distortion on firing: Isostatic pressing results in minimal distortion during the firing process, ensuring the dimensional accuracy of the final product.
- Consistent shrinkage on firing: The shrinkage of isostatically pressed parts during the firing process is consistent, leading to predictable and uniform results.
- Parts can be fired without drying: Unlike other methods, isostatic pressing allows for firing of parts without the need for prior drying, saving time and energy.
- Lower levels of binder in the powder are possible: Isostatic pressing enables the use of lower levels of binder in the powder mixture, reducing the need for additional processing steps.
- Most green (unfired) compacts can be machined: Isostatically pressed green compacts can be easily machined, offering flexibility in the manufacturing process.
- Low internal stresses in compact as pressed: The isostatic pressing process results in low internal stresses in the compacted part, reducing the risk of cracking or deformation.
- Very large pressed part capability: Isostatic pressing can accommodate the production of very large parts using the wet bag method, expanding the range of applications.
- Low tooling cost: Isostatic pressing has lower tooling costs compared to other manufacturing methods, making it a cost-effective option for short production runs.
- Higher density for a given pressing pressure: Isostatic pressing achieves higher density for a given pressing pressure compared to mechanical pressing methods, resulting in stronger and more durable parts.
- Ability to press compacts of very high length-diameter ratio: Isostatic pressing allows for the production of compacts with high length-diameter ratios, making it suitable for a wide range of applications.
- Ability to press parts with internal shapes: Isostatic pressing can accommodate parts with internal shapes, such as threads, splines, serrations, and tapers, expanding design possibilities.
- Ability to press long thin-walled parts: Isostatic pressing is capable of producing long thin-walled parts, offering versatility in product design.
- Ability to press weak powders: Isostatic pressing can effectively press weak powders, improving the material utilization and overall quality of the final product.
- Ability to press a compact having two or more layers of powder possessing different characteristics: Isostatic pressing allows for the production of compacts with multiple layers of powder, each with different characteristics, enhancing material properties and performance.
Isostatic pressing offers a range of advantages that make it a preferred production method in various industries. Let's explore some of its capabilities in more detail.
Capabilities of isostatic pressing
- Uniform density: Isostatic pressing ensures the resulting compacted piece has uniform density, resulting in consistent shrinkage during sintering or hot isostatic pressing with minimal warpage.
- Shape flexibility: Isostatic pressing allows for the production of shapes and dimensions that are difficult or impossible to achieve using other methods, providing design flexibility.
- Component size: Isostatic pressing can accommodate a wide range of component sizes, from massive 30-ton near-net powder metallurgy shapes to small MIM parts weighing less than 100 grams.
- Larger parts: The size of the isostatic pressure chamber is the only limitation on part size, making it suitable for producing large components.
- Enhanced alloying possibilities: Isostatic pressing enables the enhancement of alloying elements without inducing segregation in the material, expanding material options.
- Reduced lead times: Isostatic pressing allows for the economical production of complex shapes from prototype to production quantities, significantly reducing lead times compared to traditional manufacturing methods.
- Material and machining cost reduction: Near-net shape parts can be fabricated using isostatic pressing, reducing material waste and machining costs.
Isostatic pressing finds applications in various industries, thanks to its unique advantages and capabilities. Let's take a look at some common applications of the isostatic press.
Application of Isostatic Press
- Pharmaceuticals
- Explosives
- Chemicals
- Food
- Nuclear fuel
- Ferrites
Other application industries of isostatic presses (pharmaceuticals, explosives, chemicals, nuclear fuel ferrite)
Isostatic pressing is a versatile production method that offers numerous advantages over other techniques. It is applicable to a wide range of materials and can produce complex shapes and dimensions with high accuracy. Whether it's achieving uniform density, pressing parts with intricate internal shapes, or reducing tooling costs, isostatic pressing proves to be a valuable manufacturing option in many industries.
Disadvantages of Isostatic Pressing
Isostatic pressing is a production method that offers various advantages over other techniques. However, it is not without its disadvantages. Let's take a closer look at some of the drawbacks of isostatic pressing:
Lesser accuracy of pressed surfaces
One disadvantage of isostatic pressing is the lower accuracy of pressed surfaces adjacent to the flexible bag. This means that subsequent machining may be necessary to achieve the desired precision. In comparison, mechanical pressing or extrusion techniques typically result in more accurate pressed surfaces.
Higher costs for fully automatic dry bag presses
Fully automatic dry bag presses, which are commonly used in isostatic pressing, require relatively expensive spray-dried powder. This can increase the overall cost of the process. The use of high-quality materials and specialized equipment contributes to the higher expenses associated with this type of press.
Lower production rates when compared to extrusion or die compaction
Isostatic pressing tends to have lower production rates compared to extrusion or die compaction methods. This means that the process may not be as efficient in terms of output volume. It is important to consider the production requirements and timelines when choosing between different pressing techniques.
Despite these disadvantages, isostatic pressing still offers unique advantages that make it a valuable option for certain applications. It allows for low distortion and consistent shrinkage during firing, enables the machining of green compacts, and offers the ability to press parts with internal shapes and high length-diameter ratios. Additionally, isostatic pressing can achieve higher densities than mechanical pressing and has the capability to press compacts with multiple layers of powder.
It's important to weigh the pros and cons of isostatic pressing in relation to specific manufacturing needs to determine if it is the right choice for a particular application.
Dry Bag Isostatic Pressing
Explanation and applications of dry bag isostatic pressing
Dry bag isostatic pressing is a method of compacting powdered materials into a solid homogeneous mass before machining or sintering. It is a simple process that produces high-integrity billets or preforms with minimal distortion or cracking when fired. This process is particularly suited for producing relatively small carbide articles with axisymmetric geometry.
One of the main applications of dry bag isostatic pressing is in the production of ceramic bodies for spark plugs. The integrated rubber tooling eliminates the need for separate immersion and removal steps, making the process more automated and efficient.
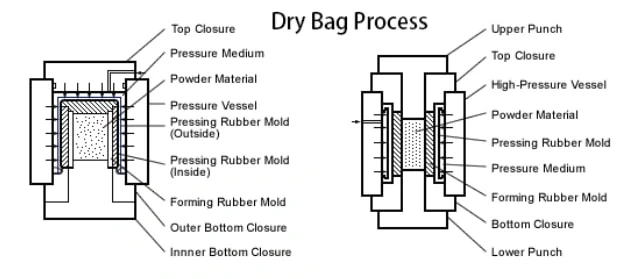
Advantages of automation in dry bag isostatic pressing
The major advantage of dry bag presses is the possibility of automation, allowing for cost-effective mass or semi-mass production of carbide articles with complex geometry. This includes rods, tubes, bushes, balls, plungers, drills, screws, nozzles, and more.
Automation in dry bag isostatic pressing also enables the production of almost net-shape hollow green compacts with precise outer and internal dimensions. This significantly reduces the amount of machining required, resulting in reduced swarf generation.
Role of WC–Co powder quality and pressing mold design
The quality of WC–Co powder and the design of the pressing mold play a crucial role in the effective fabrication of carbide green compacts. The powder quality must be carefully selected to ensure proper compaction and desired properties in the final product.
Different options for the design of pressing molds, such as integrated or exchangeable molds, offer flexibility in the pressing process. Integrated molds are preferable when the dimensions of the carbide articles remain constant for a certain period, while flexible mold systems are better suited for frequent mold changes.
Components of dry bag presses
Dry bag presses consist of a high-pressure pump, an elastic pressing mold, a pressing chamber with a membrane, and a pressure vessel. The pressure is built up by the high-pressure pump and transmitted to the pressing mold filled with WC–Co powder radially via a membrane. The pressing mold is either loaded manually or automatically.
One press run typically lasts 5-10 minutes and produces one green compact. Dry bag systems can press rods or tubes with a diameter of up to 200 mm and length of up to 600 mm. The inner and outer diameters of such tubes can be pressed with tolerances ranging from 0.1 to 1 mm, depending on their dimensions.
In conclusion, dry bag isostatic pressing is an efficient method for compacting powdered materials into solid homogeneous masses. It offers advantages such as automation for high-volume production, precise dimensions, and reduced machining requirements. The quality of WC–Co powder and the design of pressing molds are crucial factors in achieving successful fabrication.
Wet Bag Isostatic Pressing
Explanation and applications of wet bag isostatic pressing
Wet bag technology is a method of cold isostatic pressing where powder is filled in a mold and tightly sealed outside the pressure vessel. The mold is then submerged in the pressure fluid within the vessel, and isostatic pressure is applied to the external surface of the mold, compressing the powder into a solid mass.
This process is not as common as dry bag isostatic pressing, but there are over 3000 wet bag presses used worldwide. Wet bags can range in size from as small as 50mm to as big as 2000mm in diameter.
Wet bag technology is relatively slow, with processing times ranging from 5 to 30 minutes. However, the use of high-volume pumps and improved loading mechanisms can help speed up the process.
Wet bag isostatic pressing is often used for low-volume production of specialty parts, prototyping, and research and development.
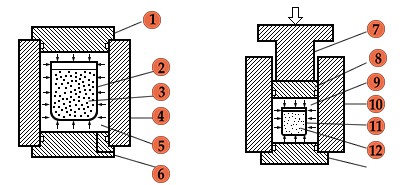
Advantages of wet-bag isopressing
Wet bag isostatic pressing offers several advantages:
-
Uniform density: Wet bag isopressing can approach the theoretical concept of isostatic pressing, resulting in a compact with a uniform density and low entrapped stress. This allows for machining in the green state without distortion.
-
Reduced distortion: When fired, parts produced through wet bag isopressing experience virtually no distortion, reducing or eliminating the need for expensive machining.
-
Automation potential: Wet bag isopressing lends itself well to automation, making it suitable for pressing relatively long runs of compacts at high production rates.
Difference between wet-bag and dry-bag isopressing
The main difference between wet bag and dry bag isostatic pressing is the method of compacting the powder:
-
Wet bag isopressing: In wet bag isostatic pressing, the powder is compacted in a sealed elastomeric mold that is completely submerged in pressurized fluid. This method is used for low-volume production of specialty parts, prototyping, and research and development.
-
Dry bag isopressing: In dry bag isostatic pressing, the elastomeric mold is an integral part of the isostatic press. The applied pressure is mostly biaxial, and the process can be automated for high-volume production.
Both wet bag and dry bag isostatic pressing offer advantages and disadvantages. Wet bag is better suited for production of large parts and allows for higher densities with minimal friction. However, loading and unloading the molds can decrease productivity and limit automation. Dry bag isopressing, on the other hand, has an edge in automation and production rate.
Overall, isostatic pressing is chosen to achieve high compact densities and access shapes that cannot be compacted in uniaxial presses. The choice between wet bag and dry bag isostatic pressing depends on the specific requirements of the production process.
Uniaxial Versus Isostatic Pressing
Limitations of uniaxial pressing that can be overcome by isostatic pressing
Some limitations of uniaxial pressing that concern regular particle packing can be overcome by isostatic pressing. Isostatic pressing applies pressure from all directions, unlike uniaxial pressing which only applies pressure from one direction. This allows for more uniform compaction and higher packing uniformity. Isostatic pressing is commonly done using two methods: wet-bag and dry-bag.
In wet-bag isostatic pressing, the powder is filled in a flexible mold, sealed, and immersed in liquid in a high-pressure vessel. The liquid is pressurized, and the pressure is transmitted through the flexible wall of the mold to the powder, resulting in compaction. Wet-bag isostatic pressing offers higher packing uniformity compared to uniaxial pressing. Pressures of up to 1000 GPa can be used, although the most common production units operate up to 200-300 MPa. Wet-bag isostatic pressing, coupled with 3D green machining, is used to fabricate complex ceramic parts at very high quality.
Dry-bag isostatic pressing is easier to automate than the wet-bag process. It involves a rubber mold tightly connected with the pressure vessel. However, the pressurized liquid does not act from all directions, so careful mold design is necessary to ensure homogeneous particle packing in the powder compact.
Comparison of green bodies produced by uniaxial and isostatic pressing
Isostatic pressing is similar to uniaxial pressing in terms of powder requirements and general process steps, but there are important differences. First, isostatic pressing takes place under hydrostatic conditions, meaning the pressure is transmitted equally in all directions, reducing die wall friction. Second, the tooling for isostatic pressing consists of elastomeric molds instead of rigid dies. The powder is loaded into the flexible mold, sealed, and pressure is applied via a liquid in a pressure vessel.
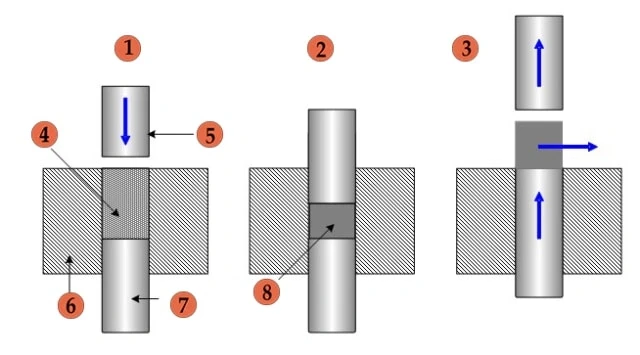
When comparing uniaxial pressing to isostatic pressing, uniaxial pressing is more suitable for small shapes at high production rates. However, die wall friction may result in non-uniform densities, especially for large aspect ratios. Isostatic pressing, on the other hand, can be used for small or large, simple or complex shapes. The uniform green density it provides offers more even shrinkage during sintering, which is important for shape control and uniform properties. Isostatic pressing also eliminates the need for a wax binder used in uniaxial pressing, eliminating the need for dewaxing operations.
Low-cost elastomer tooling is used for isostatic pressing, but close tolerances can only be obtained for surfaces pressed against a highly accurate steel mandrel. Surfaces in contact with the elastomer tooling may require post-machining to achieve tight tolerances and good surface finishes.
In summary, isostatic pressing overcomes certain limitations of uniaxial pressing by applying pressure from all directions. It offers higher packing uniformity, more even shrinkage during sintering, and eliminates the need for a wax binder. Isostatic pressing can be done through wet-bag or dry-bag methods, each with its own advantages and limitations.
Powder Preparation for Isostatic Pressing
Requirements for powder in isostatic pressing
Isostatic pressing is a powder processing technique that uses fluid pressure to compact a part. In order to achieve optimal results, certain requirements must be met when it comes to the powder used in isostatic pressing.
One important requirement is the particle size distribution of the powder. For isostatic pressing, it is recommended to use powders with grain sizes ranging from 1-5 μm. This size range allows for the formation of materials with densities higher than 98% of theoretical. The use of undoped alumina powders with an average particle size of about 0.5 μm has been found to be effective in achieving these densities.
Another requirement is the binder content in the powder mixture. The binder serves to hold the powder particles together during the pressing process. The specific binder content will depend on the type of powder being used and the desired properties of the final product. Typically, a binder content of 20%-30% is used, with a cellulose wax mixture being a common choice.
Adjustments in particle size distribution and binder content
In order to optimize the powder conditioning before isostatic pressing, adjustments can be made to the particle size distribution and binder content.
Particle size distribution can be adjusted by grinding the powder to a finer grain size. Ideally, a grain size of less than 75 μm is desired for the powder used in isostatic pressing. This finer grain size allows for better compaction and ensures a more homogeneous sample pellet.
The binder content can also be adjusted based on the specific requirements of the part being produced. Increasing the binder content can provide added strength to the pressed pellet, while decreasing it can result in a more porous structure. It is important to find the right balance between strength and porosity to achieve the desired properties in the final product.
By carefully considering the requirements for powder in isostatic pressing and making adjustments to the particle size distribution and binder content, manufacturers can produce high-quality parts with the desired properties. Isostatic pressing offers a versatile and effective method for powder compaction, allowing for the production of a wide range of materials.
Conclusion
In conclusion, isostatic pressing is a versatile manufacturing process that offers numerous benefits for various applications. It provides higher density and lower tooling costs compared to other production methods, making it an attractive option for businesses. Isostatic pressing also allows for the production of parts with internal shapes and long thin-walled parts, expanding the possibilities for design and functionality. However, it does have limitations, such as lesser accuracy of pressed surfaces and lower production rates compared to other techniques. Overall, isostatic pressing is a valuable tool in the manufacturing industry, offering unique advantages for the production of high-quality components.
CONTACT US FOR A FREE CONSULTATION
KINTEK LAB SOLUTION's products and services have been recognized by customers around the world. Our staff will be happy to assist with any inquiry you might have. Contact us for a free consultation and talk to a product specialist to find the most suitable solution for your application needs!