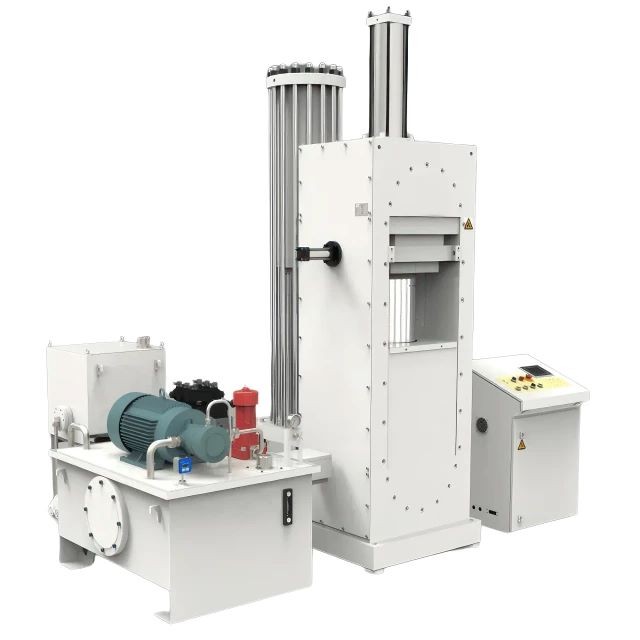
Isostatic Press
Cold Isostatic Pressing Machine CIP for Small Workpiece Production 400Mpa
Item Number : PCIS
Price varies based on specs and customizations
- Working pressure (MPa)
- 0-400
- Feeding method
- Automatic
- Effective inner diameter of high pressure chamber (mm)
- 150-300
- Effective depth of high pressure cavity (mm)
- 300-450
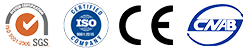
Shipping:
Contact us to get shipping details Enjoy On-time Dispatch Guarantee.
Why Choose Us
Reliable PartnerEasy ordering process, quality products, and dedicated support for your business success.
Cold Isostatic Presses employ a pressure vessel chamber to compress a powder or material enclosed in a sealed container such as tooling or bag. The resulting high pressure leads to the formation and densification of materials with a uniformly high density.
This industrial cold isostatic press features a high-pressure chamber bore of up to 300mm and an effective depth of 400mm, making it ideal for compacting small workpieces in production settings.
As the earliest isostatic pressing machine produced by our company, it has been in production for over 20 years and is highly sought-after by small and medium-sized manufacturing enterprises.
Applications
Cold isostatic pressing technology has numerous advantages over other molding processes, such as improving product performance, quality, and economic benefits.
As a result, its application field is continuously expanding, and the technology is becoming more mature. Currently, there are hundreds of product categories using this technology.
In recent decades, it has been widely utilized in industrial sectors such as powder metallurgy, graphite, ceramics, plastics, refractory materials, and hard alloys. Furthermore, it is also employed in biopharmaceutical fields for activities like high-pressure sterilization of food, drug extraction, and protein activation.
Detail
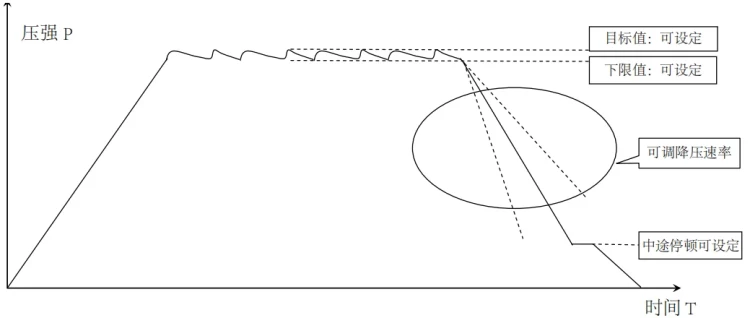
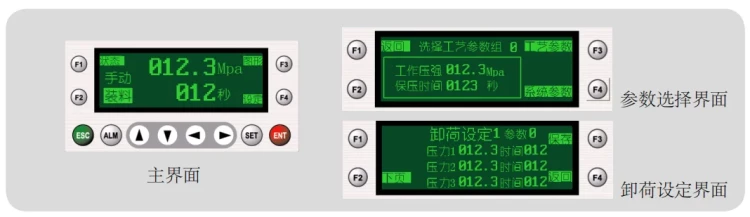
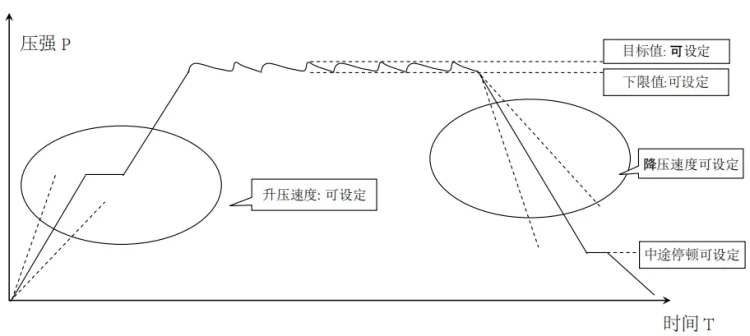
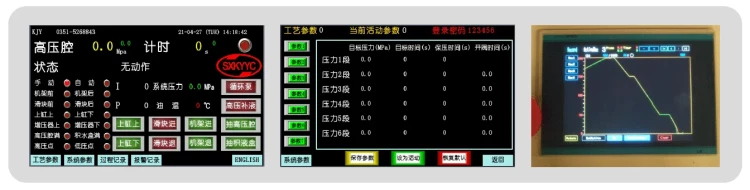
Features
- CIP produces products with high and uniformly proportional density, resulting in minimal contraction after sintering.
- It can form products with difficult-to-achieve shapes such as long rod and cylinder shapes that are not easily attainable using conventional compression molding techniques.
- Pressed products exhibit high strength, workability, and reduced internal stress.
- The molds are easy to make, with a long lifespan and low cost.
- CIP is capable of pressing big-sized products and products with different shapes simultaneously.
Advantages
- The equipment features a compact structure and a low mechanical failure rate.
- With the ability to complete a working cycle within three minutes at the fastest, it offers a remarkably high production efficiency.
- Its footprint is smaller compared to other models with the same caliber.
- The equipment lifts the material automatically, eliminating the need for auxiliary material lifting devices.
- The supercharger is a one-time pressurization type, requiring minimal technical knowledge for both equipment users and maintenance personnel.
Safety guarantee
- The manual pressure relief valve can be opened in case of emergency or failure, and the compressor's pressure relief protection can only be reactivated after the valve is closed.
- The pressure sensor and electrical control system automatically stop the booster system and activate the pressure relief system for protection when the working pressure exceeds the preset value.
- The control cabinet has a stop button that can halt the press at any point during operation.
- The electrical control programs have interlocking, so the press operates strictly according to the work procedure. If a previous procedure is incomplete or fails, the next procedure will not be carried out and an operation failure message will be issued. The next procedure can only resume after troubleshooting.
Technical specifications
Model | PCIS-150 | PCIS-200 | PCIS-250 | PCIS-300 |
Effective inner diameter of high pressure chamber (mm) | 150 | 200 | 250 | 300 |
Effective depth of high pressure cavity (mm) | 300 | 300 | 300 | 400/450 |
Maximum working pressure (MPa) | 100-400 | 100-400 | 100-400 | 100-300 |
Power | 9Kw | 9Kw | 17.5Kw | 17.5Kw |
Feeding method | Automatic | |||
Boost rate | Manually adjustable or precisely adjustable | |||
Working medium | Oil or water+rust inhibitor | |||
HMI | Text screen or touch screen | |||
Data export interface | USB | |||
Cooling method | Water cooling |
Warnings
Operator safety is the top important issue! Please operate the equipment with cautions. Working with inflammable& explosive or toxic gases is very dangerous, operators must take all necessary precautions before starting the equipment. Working with positive pressure inside the reactors or chambers is dangerous, operator must fellow the safety procedures strictly. Extra caution must also be taken when operating with air-reactive materials, especially under vacuum. A leak can draw air into the apparatus and cause a violent reaction to occur.
Designed for You
KinTek provide deep custom made service and equipment to worldwide customers, our specialized teamwork and rich experienced engineers are capable to undertake the custom tailoring hardware and software equipment requirements, and help our customer to build up the exclusive and personalized equipment and solution!
Would you please drop your ideas to us, our engineers are ready for you now!
FAQ
What Is Cold Isostatic Pressing (CIP)?
Cold Isostatic Pressing (CIP) is a process used to compact and mold powders and other materials into a desired shape by applying hydrostatic pressure at room temperature. The process is performed using a flexible mold, typically made of rubber or plastic, that is filled with a liquid pressure medium such as water, oil, or a specialized fluid.
What Is Isostatic Pressing?
What Are The Benefits Of Isostatic Pressing?
What Are The Types Of Isostatic Pressing?
There are two main types of isostatic pressing:
- Hot Isostatic Pressing (HIP): This type of isostatic pressing uses high temperature and high pressure to consolidate and strengthen the material. The material is heated in a sealed container and then subjected to equal pressure from all directions.
- Cold Isostatic Pressing (CIP): In this type of isostatic pressing, the material is compacted at room temperature using hydraulic pressure. This method is commonly used to form ceramic and metal powders into complex shapes and structures.
What Are The Advantages Of Cold Isostatic Pressing?
- High green strength: Machining of the compacted material in its green state becomes more feasible.
- Materials that are hard to press: Isostatic pressing can be performed on powders without the need for water, lubricants, or binders, making it applicable to a wider range of materials.
- Predictable shrinkage during sintering is achieved due to the high compaction and uniform density.
- Time and cost savings in post-processing are possible due to the ability to create large, complex, and near-net shapes.
- Large aspect ratio parts with uniform density can be produced, resulting in improved quality.
- Green strength enables efficient in-process handling and treatment, reducing production costs.
What Is A Cold Isostatic Press?
A cold isostatic press (CIP) is a machine used to compact and mold powders and other materials into a desired shape.
The process works by filling a flexible mold, usually made of rubber or plastic, with a liquid pressure medium like water, oil, or a specialized fluid. This mold is then placed in a closed container, and equal pressure is applied to each surface to achieve a high-pressure environment.
The pressure results in an increase in the product's density and allows it to take on the desired shape.
Cold isostatic pressing is performed at room temperature, in contrast to hot isostatic pressing which is carried out at higher temperatures.
What Type Of Isostatic Pressing Equipment Do You Have?
Application Field Of Cold Isostatic Press?
Cold Isostatic Pressing is widely used for various applications, including the consolidation of ceramic powders, compression of graphite, refractory materials, and electrical insulators, as well as the production of fine ceramics for dental and medical applications.
This technology is also making inroads into new fields such as pressing sputtering targets, coating valve parts in engines to reduce wear on cylinder heads, telecommunications, electronics, aerospace, and automotive industries.
What Are The Wet Bag Process And The Dry Bag Process?
The CIP molding process is divided into two methods: the wet bag process and the dry bag process.
Wet bag process:
In this method, the powder material is placed in a flexible mold bag and placed in a pressure vessel filled with high-pressure liquid. This process is ideal for producing multi-shaped products and is suitable for small to large quantities, including large-sized parts.
Dry bag process:
In the dry bag process, a flexible membrane is integrated into the pressure vessel and is used throughout the pressing process. This membrane separates the pressure fluid from the mold, creating a "dry bag." This method is more hygienic as the flexible mold does not get contaminated with wet powder and requires less cleaning of the vessel. It also features fast cycles, making it ideal for mass producing powder products in an automated process.
What Is Isostatic Pressing Dry Bag And Wet Bag?
Cold isostatic pressing has two methods of powder loading: dry bag molding and wet bag molding. The main difference between the two is that in dry bag molding, the rubber bag used is not soaked in a liquid medium. After pressing, the briquette and the mold bag are removed, while the pressurized rubber bag stays in the container for the next filling. The mold bag used in dry bag molding has a long service life and high production efficiency, making it ideal for single-piece continuous production.
On the other hand, wet bag molding is a pressing process where the mold bag is soaked in a liquid medium after loading. After pressing, the mold bag and the blank are removed simultaneously. This process can simultaneously press parts of various shapes, but demolding takes longer.
What Are The Wearing Parts Of Cold Isostatic Pressing Equipment?
The wearing parts of cold isostatic equipment are mainly various seals, such as various types of seal rings, valve cores and valve seats.
How Long Is The Supply Cycle Of The Large Cold Isostatic Presses?
As the isostatic press is a customized piece of equipment, we begin production upon receiving orders. The production cycle typically ranges from 2 to 7 months, depending on the size of the equipment.
In order to quickly respond to our users' demands, our company keeps a stock of common model forgings and complete machines. This allows us to provide goods-in-stock or products with shorter delivery periods for our users.
Do You Provide Matching Cold Isostatic Press Molds?
We offer a variety of standard mold shapes for customers to experiment or validate their process. Custom mold design services are also available upon request.
Will You Install Or Debug The Large Cold Isostatic Presses For Users?
Our company offers global installation and debugging services, and we have independent export rights. We are also able to handle customs clearance procedures for exports and visas independently.
Upon receiving the equipment, users can contact our company to arrange for on-site installation and debugging.
How Long Is Your Delivery Time? If I Want To Customize The Instrument, How Long Does It Take?
4.8
out of
5
A cost-effective solution for small workpiece production, the press delivers consistent results.
4.9
out of
5
The press is easy to set up and operate, making it a great choice for small businesses.
4.7
out of
5
The press has helped us streamline our production process and improve product quality.
4.8
out of
5
The press is well-built and durable, and it has exceeded our expectations.
4.7
out of
5
The press is a valuable asset to our manufacturing line, and we highly recommend it.
4.9
out of
5
The press is a great investment for any business that needs to produce small workpieces.
4.8
out of
5
The press is easy to maintain and clean, which saves us time and money.
4.9
out of
5
The press has helped us reduce our production costs and improve our bottom line.
4.7
out of
5
The press is a great value for the price, and it has quickly become an essential part of our production process.
4.8
out of
5
The press is very efficient and has helped us increase our production output.
4.9
out of
5
The press has been a game-changer for our business, and we couldn't be happier with it.
4.7
out of
5
The press is very reliable and has never let us down.
4.8
out of
5
The press is very user-friendly and has a short learning curve.
4.9
out of
5
The press is very versatile and can be used for a wide variety of applications.
4.7
out of
5
The press is very well-made and has a long lifespan.
4.8
out of
5
The press is very energy-efficient and helps us save money on our energy bills.
4.9
out of
5
The press is very quiet and does not disrupt our other operations.
4.7
out of
5
The press is very easy to install and set up.
4.8
out of
5
The press is very compact and does not take up much space.
Products
Cold Isostatic Pressing Machine CIP for Small Workpiece Production 400Mpa
REQUEST A QUOTE
Our professional team will reply to you within one business day. Please feel free to contact us!
Related Products
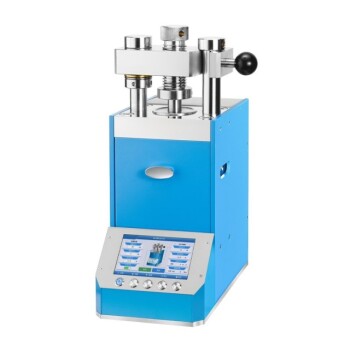
Automatic Lab Cold Isostatic Press CIP Machine Cold Isostatic Pressing
Efficiently prepare samples with our Automatic Lab Cold Isostatic Press. Widely used in material research, pharmacy, and electronic industries. Provides greater flexibility and control compared to electric CIPs.
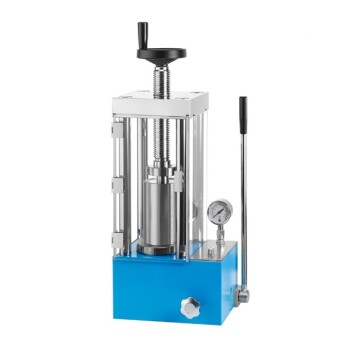
Manual Cold Isostatic Pressing Machine CIP Pellet Press
Lab Manual Isostatic Press is a high-efficient equipment for sample preparation widely used in material research, pharmacy, ceramics, and electronic industries. It allows for precision control of the pressing process and can work in a vacuum environment.
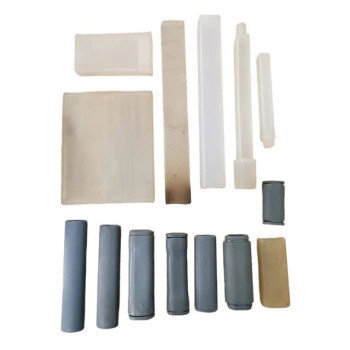
Isostatic Molding Pressing Molds for Lab
Explore high-performance isostatic pressing molds for advanced material processing. Ideal for achieving uniform density and strength in manufacturing.
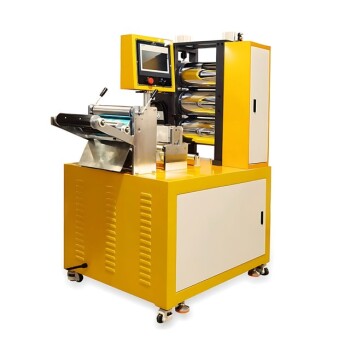
Small Lab Rubber Calendering Machine
Small lab rubber calendering machine is used for producing thin, continuous sheets of plastic or rubber materials. It is commonly employed in laboratories, small-scale production facilities, and prototyping environments to create films, coatings, and laminates with precise thickness and surface finish.
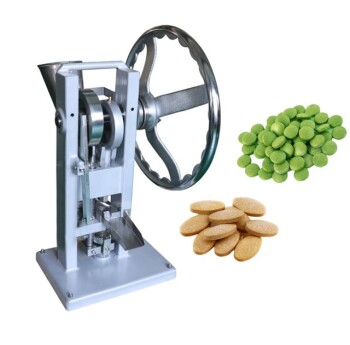
Single Punch Manual Tablet Press Machine TDP Tablet Punching Machine
Single punch manual tablet punching machine can press various granular, crystal or powdery raw materials with good fluidity into disc-shaped, cylindrical, spherical, convex, concave and other various geometric shapes (such as square, triangle, ellipse, capsule shape, etc.), and can also press products with text and patterns.
Related Articles
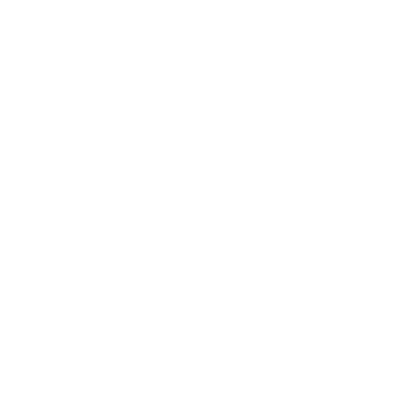
What is Isostatic Pressing Machine
Isostatic molding is a molding method that uses the incompressibility of a liquid medium and the uniform transfer of pressure. It is suitable for powder dense parts with equal pressure in all directions. The principle is to fill the mold with a liquid medium, such as water, and then subject the mold to uniform pressure. The pressure is applied by a piston or a flexible membrane.
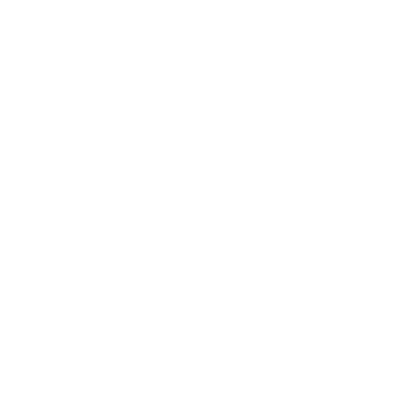
Understanding Isostatic Pressing: Process, Benefits, Limitations, and Applications
Isostatic pressing is a manufacturing process that offers numerous benefits and applications in various industries. It involves subjecting a material to equal pressure from all directions to achieve uniform density and shape. This method is particularly advantageous compared to other production techniques.
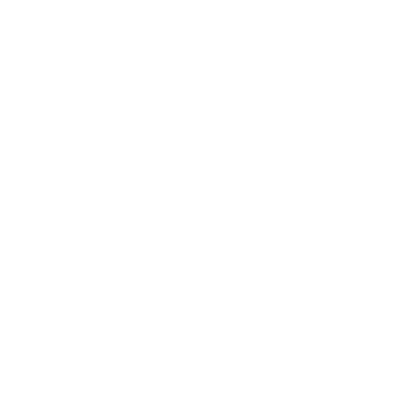
Understanding the Isostatic Pressing Process and its Types
Isostatic pressing, a technique that applies hydrostatic pressure to a material to improve its density and mechanical strength, has seen significant growth and development over the years. Isostatic pressing is commonly used for the consolidation of powders and defect healing of castings, making it a versatile process for a range of materials including ceramics, metals, composites, plastics, and carbon.
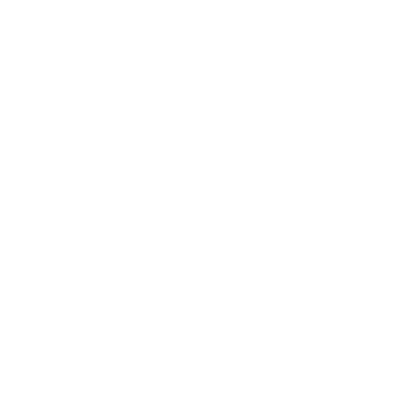
Comprehensive Guide to Isostatic Pressing:Processes, and Features
Isostatic pressing is a versatile manufacturing process that is widely used in various industries. It involves subjecting a material to equal pressure from all directions to achieve uniform density and shape. Isostatic pressing offers numerous advantages, such as the ability to produce complex shapes, uniformity in material properties, and high precision. This comprehensive guide will delve into the different types of isostatic pressing, including cold, warm, and hot pressing. We will explore the processes, features, and applications of each type, providing you with a thorough understanding of this essential manufacturing technique. So let's dive in!
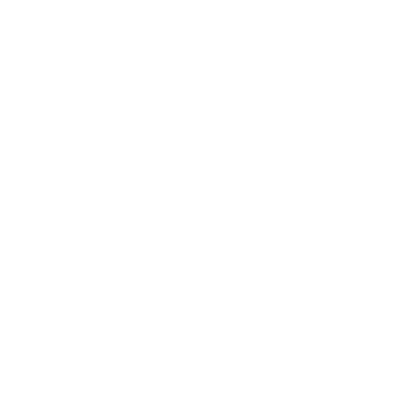
Comprehensive Guide to Isostatic Pressing: Types, Processes, and Features(3)
Isostatic pressing is a versatile manufacturing process that is widely used in various industries. It involves subjecting a material to equal pressure from all directions to achieve uniform density and shape. Isostatic pressing offers numerous advantages, such as the ability to produce complex shapes, uniformity in material properties, and high precision.
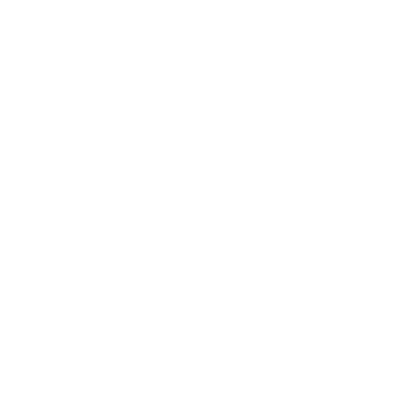
Selecting Isostatic Pressing Equipment for High-Density Molding
An in-depth look at isostatic pressing techniques and equipment selection for achieving high-density molding.
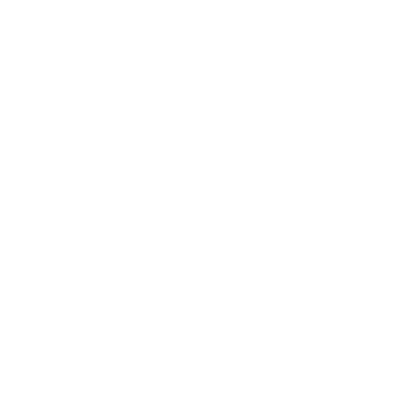
Isostatic Pressing Technology: Revolutionizing Ceramic Material Densification
Explore how isostatic pressing techniques enhance ceramic properties, achieving 100% theoretical density and eliminating porosity.
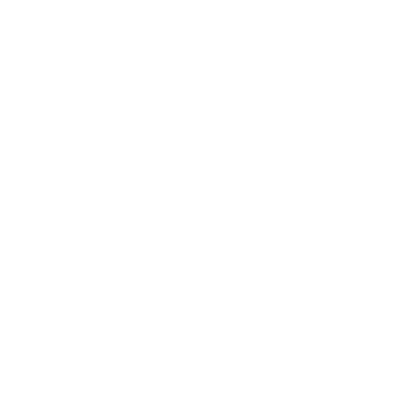
Isostatic Pressing Technology: Principles, Classification, and Applications
An in-depth look at isostatic pressing technology, its types, and diverse applications across various industries.
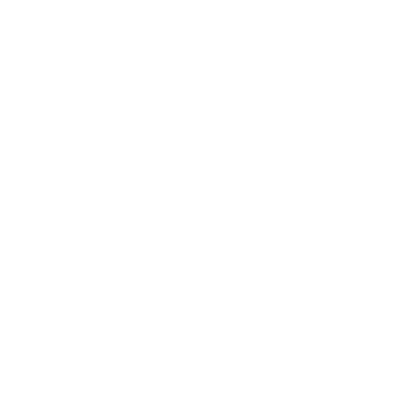
Zirconia Ceramic Rod Production Processes: Isostatic Pressing vs. Dry Pressing
A comparison of isostatic pressing and dry pressing in zirconia ceramic rod production, highlighting differences and advantages.
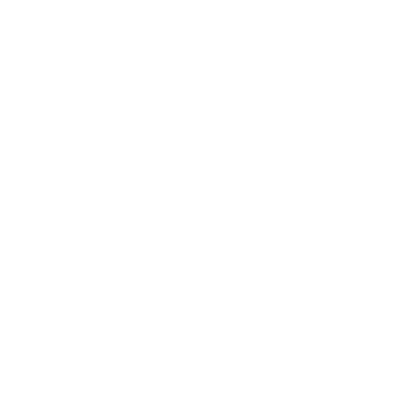
How Isostatic Presses Help Eliminate Defects in Materials
Isostatic pressing is a manufacturing process that is used to eliminate defects in materials.
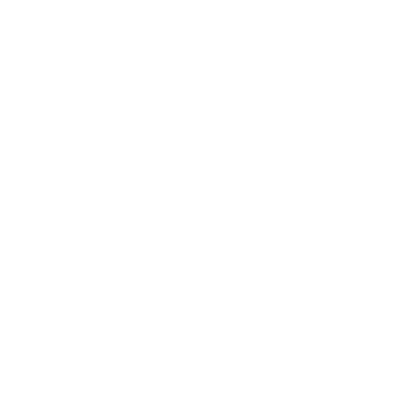
How Isostatic Presses Improve the Efficiency of Material Processing
Isostatic pressing is a manufacturing process that uses high pressure to compact and shape materials. It can be done at room temperature (cold isostatic pressing) or at high temperatures (hot isostatic pressing).
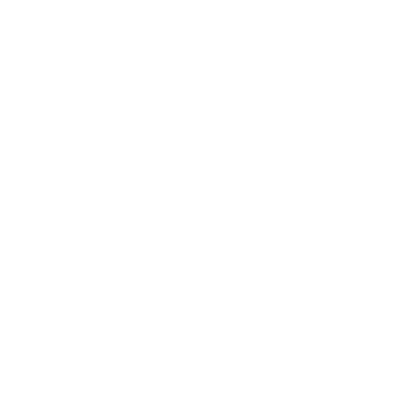
How to replace the rubber ring of isostatic press and what precautions should be taken
How to replace the rubber ring of isostatic press and matters needing attention.