Hot Isostatic Pressing (HIP)
Maximizing Ceramic Properties
Hot Isostatic Pressing (HIP) stands out as the premier process for manufacturing advanced ceramics, offering unparalleled advantages in terms of material properties. By subjecting the ceramic materials to high-pressure gas at elevated temperatures, HIP ensures that the final product achieves full density, a state where the material is virtually free from voids and pores. This process not only eliminates internal defects but also minimizes grain growth, a critical factor in maintaining the material's structural integrity and mechanical properties.
The benefits of HIP extend beyond mere densification. The process results in ceramics with ultimate strength, making them highly reliable and durable. This is particularly crucial in applications where failure is not an option, such as in medical implants and aerospace components. The high reliability of HIP-processed ceramics is attributed to the uniform distribution of stress and strain throughout the material, which reduces the likelihood of localized failures.
Moreover, HIP's ability to produce ceramics with exceptional hardness and transparency further broadens its applications. Transparent ceramics, for instance, find use in high-performance optics, including laser gain media and scratch-resistant windows. The combination of these properties makes HIP-processed ceramics a preferred choice in industries demanding high performance and long-term reliability.
In summary, HIP is not just a process; it is a transformative technology that elevates ceramic materials to their highest potential, ensuring they meet the stringent demands of modern industrial applications.
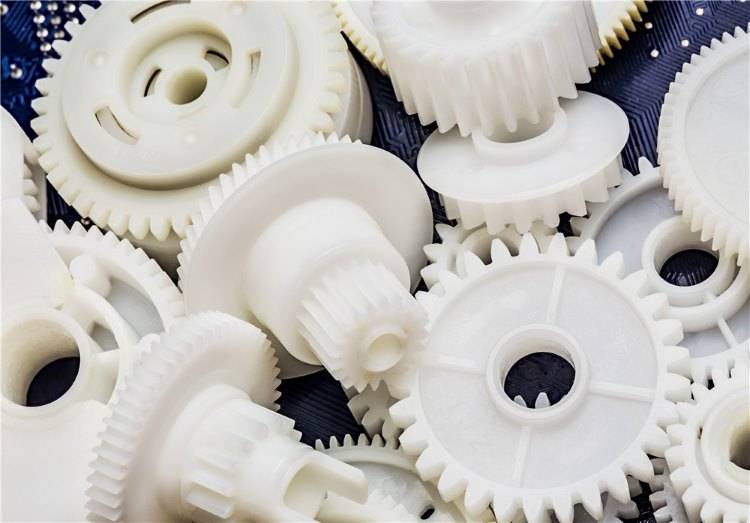
Achieving 100% Theoretical Density
Achieving 100% theoretical density in ceramic materials is a critical goal in the field of isostatic pressing technology. This milestone is not merely a number but a testament to the material's structural integrity and performance capabilities. By meticulously adjusting the sintering temperature and applying high isostatic pressure, it is possible to minimize grain growth, thereby optimizing the material's properties.
The synergy between temperature control and pressure application plays a pivotal role in this process. The sintering temperature, when precisely calibrated, facilitates the coalescence of particles, leading to a dense and uniform microstructure. Simultaneously, high isostatic pressure ensures that this densification occurs uniformly throughout the material, preventing any localized weaknesses or porosity.
This approach yields several significant benefits. Firstly, it results in maximum strength, ensuring that the ceramic can withstand high mechanical stresses without failure. Secondly, it enhances reliability, making the material more dependable in critical applications. Additionally, the reduction in grain growth contributes to increased hardness, making the ceramic more resistant to wear and abrasion. For applications requiring optical clarity, such as in laser technology or scratch-resistant windows, the material's transparency is also maximized.
In summary, the careful balance of sintering temperature and isostatic pressure not only achieves 100% theoretical density but also imparts superior mechanical and optical properties to the ceramic material.
Improving Production Efficiency
The utilization of high gas pressure in isostatic pressing technology not only facilitates the densification of ceramic materials but also introduces a buoyancy effect that significantly enhances production efficiency. This buoyancy effect allows multiple parts to be stacked within the press without the risk of sticking or sinking, a common issue in traditional pressing methods. By enabling the simultaneous processing of multiple parts, the production cycle is expedited, leading to a notable increase in output and a reduction in per-unit production costs.
Moreover, the high gas pressure ensures uniform distribution of force across all parts, eliminating the need for intricate handling and positioning. This uniformity results in consistently high-quality products, as each part experiences the same level of densification and pressure. The ability to stack parts also optimizes the use of press space, allowing for more efficient utilization of equipment and resources.
In summary, the combination of high gas pressure and buoyancy effects in isostatic pressing not only streamlines the production process but also ensures the production of high-quality ceramic parts in a cost-effective manner. This dual benefit makes isostatic pressing an indispensable tool for industries seeking to enhance their production efficiency and maintain a competitive edge.
Applications of HIP
Hot Isostatic Pressing (HIP) is indispensable in the production of high-integrity and precise components across a multitude of industries, from aerospace and medicine to automotive and beyond. This advanced technique is particularly favored for its ability to apply uniform pressure to the entire surface of a part, ensuring critical dimensions are met with unparalleled accuracy. The use of an inert gas, typically argon, within the HIP vessel further guarantees that the part surfaces remain unreactive, enhancing the overall quality and reliability of the final product.
One of the most notable applications of HIP is in the medical field, where it is extensively used in the manufacturing of implants. These implants require exceptional durability and biocompatibility, qualities that HIP can deliver through its ability to achieve 100% theoretical density and eliminate porosity. Beyond medical implants, HIP is also pivotal in the creation of SN hybrid ceramic bearings, which are essential for their high load-bearing capacity and low friction properties.
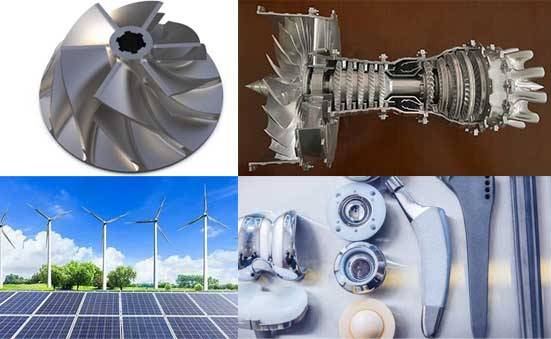
In the realm of transparent ceramics, HIP plays a crucial role in producing materials that are not only optically clear but also highly resistant to scratches and laser damage. These properties make HIP-treated transparent ceramics ideal for applications such as laser gain media and scratch-resistant windows. The versatility and precision of HIP extend to numerous other components, including gas turbine parts, pumps, valves, pistons, and cutting tools, all of which benefit from the enhanced mechanical properties and reliability that HIP imparts.
Industry | HIP Applications |
---|---|
Medical | Implants, prosthetics, surgical tools |
Aerospace | Gas turbine components, structural parts, engine components |
Automotive | Engine components, brake systems, transmission parts |
Optics | Transparent ceramics, laser gain media, scratch-resistant windows |
Industrial | Pumps, valves, pistons, cutting tools, heat treatment components |
The demand for HIP is further bolstered by its compatibility with additive manufacturing processes. Just as pores often form during casting, additive manufacturing can leave voids in parts. HIP effectively addresses these issues, making it a vital post-processing step for ensuring the integrity and performance of complex components, particularly in aerospace and medical applications where cost-effectiveness and precision are paramount.
Cold and Warm Isostatic Pressing (CIP/WIP)
Consolidation of Ceramic Powders
Cold and Warm Isostatic Pressing (CIP/WIP) stands out as the method of choice for consolidating large ceramic or refractory metal powder parts. This technique ensures not only uniform high density but also efficient production processes. The primary advantage of CIP/WIP lies in its ability to apply uniform pressure across all sides of the material, which is crucial for achieving the desired mechanical properties and dimensional accuracy.
For instance, when dealing with ceramic powders, the uniform pressure distribution helps in eliminating internal voids and porosity, which are common issues in traditional consolidation methods. This uniformity is particularly beneficial in applications where high reliability and strength are paramount, such as in the production of medical implants and advanced ceramic bearings.
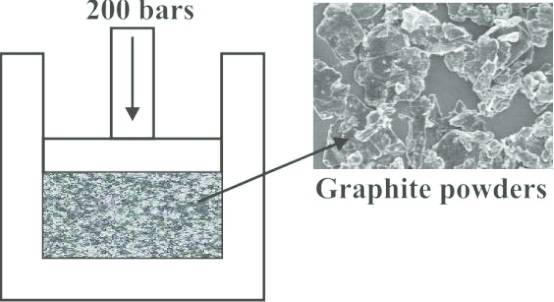
Moreover, the efficiency of CIP/WIP extends beyond just density improvement. The process allows for the consolidation of large parts without the need for complex molds or additional finishing steps, thereby reducing production time and costs. This streamlined approach makes CIP/WIP an attractive option for industries requiring large-scale, high-quality ceramic components.
In summary, CIP/WIP not only ensures the consolidation of ceramic powders to a uniform green state but also enhances production efficiency, making it a preferred method in various industrial applications.
Achieving Uniform Green State
Cold and Warm Isostatic Pressing (CIP/WIP) plays a pivotal role in the consolidation of ceramic powders, transforming them into a highly uniform green state. This process is essential for ensuring that the final ceramic products possess the desired mechanical, thermal, and electrical properties. By applying controlled pressure and temperature, CIP/WIP effectively eliminates inconsistencies in the green body, which are often the root cause of performance variability in the finished ceramics.
The uniformity achieved through CIP/WIP is not just about physical consistency; it also significantly enhances the material's overall performance. For instance, a uniform green state ensures that the ceramic parts have uniform shrinkage during sintering, leading to precise dimensional control. This precision is crucial for applications where tolerance to size variation is minimal, such as in medical implants or high-performance ceramic bearings.
Moreover, the reduction in performance variability translates to higher reliability and longer operational life for the ceramic components. This is particularly important in industries where failure is not an option, such as aerospace and defense. By minimizing the variability in properties like hardness, strength, and thermal conductivity, CIP/WIP ensures that each ceramic part meets the stringent requirements of these high-stakes applications.
In summary, CIP/WIP's ability to achieve a uniform green state is a cornerstone in the production of advanced ceramics. It not only ensures the desired final properties but also significantly reduces performance variability, making it an indispensable technique in the manufacturing of high-performance ceramic materials.
Applications of CIP/WIP
Cold and Warm Isostatic Pressing (CIP/WIP) technology finds extensive applications across a diverse range of materials, each benefiting from its ability to ensure uniform high density and efficient production processes. One of the primary materials that CIP/WIP is used for is ceramic powders. These powders, when subjected to CIP/WIP, can be consolidated into large, dense parts with minimal porosity, which is crucial for achieving the desired mechanical and thermal properties in advanced ceramics.
In addition to ceramic powders, CIP/WIP is also employed in the production of isostatic graphite. This material is known for its exceptional mechanical strength and thermal conductivity, making it ideal for high-temperature applications such as furnace components and electrodes. The isostatic pressing process ensures that the graphite is uniformly dense, thereby enhancing its performance and longevity in these demanding environments.
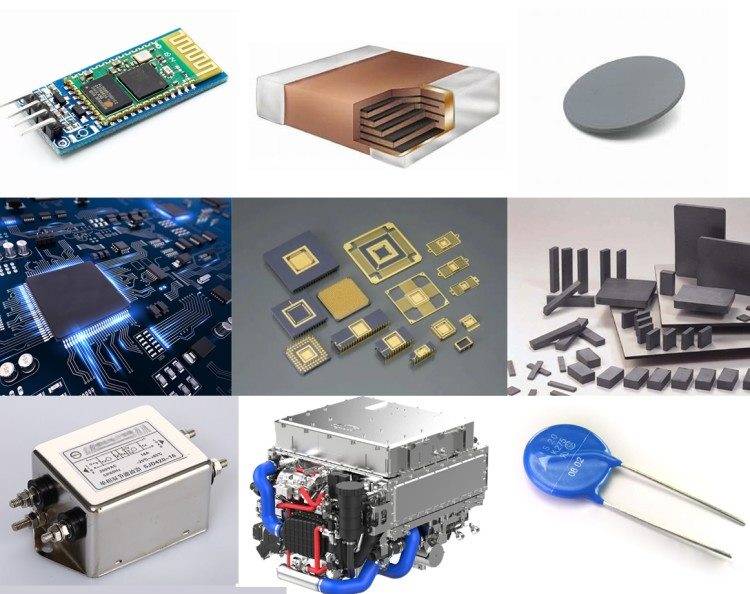
Refractory metals are another class of materials that benefit significantly from CIP/WIP. These metals, which include tungsten, molybdenum, and tantalum, are characterized by their high melting points and excellent resistance to heat and wear. The CIP/WIP process allows for the consolidation of these metals into dense, high-performance components, which are essential for applications in aerospace, nuclear, and industrial sectors.
Lastly, CIP/WIP is utilized in the production of electrical insulators. These materials must possess high dielectric strength and low electrical conductivity to function effectively in electrical systems. The uniform densification achieved through CIP/WIP ensures that these insulators meet stringent performance criteria, making them suitable for use in high-voltage applications and electronic devices.
Overall, the versatility and efficiency of CIP/WIP make it an indispensable tool in the production of a wide array of materials, each requiring precise control over density and uniformity to achieve optimal performance.
CONTACT US FOR A FREE CONSULTATION
KINTEK LAB SOLUTION's products and services have been recognized by customers around the world. Our staff will be happy to assist with any inquiry you might have. Contact us for a free consultation and talk to a product specialist to find the most suitable solution for your application needs!