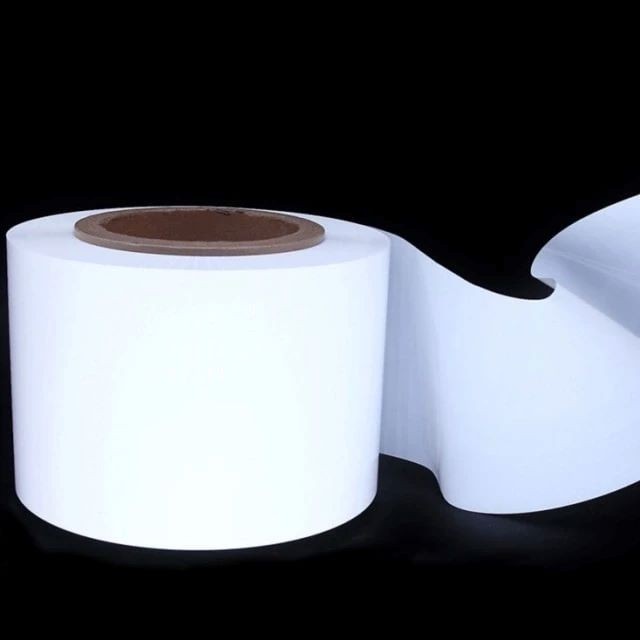
battery material
Polyethylene Separator for Lithium Battery
Item Number : BC-18
Price varies based on specs and customizations
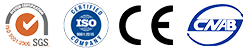
Shipping:
Contact us to get shipping details Enjoy On-time Dispatch Guarantee.
Why Choose Us
Reliable PartnerEasy ordering process, quality products, and dedicated support for your business success.
Introduce
Polyethylene separators are produced using wet and dry stretching methods, offering flexibility and diverse material options for various applications. The temperature resistance of PE and PP differs, with PE having lower resistance and PP having higher resistance. PP also has a lower density and higher melting point compared to PE. Separator strength varies with the production method, with wet biaxial stretching yielding superior longitudinal and transverse strength. PE's sensitivity to ambient pressure is a consideration in certain applications, affecting performance and suitability in different industries.
The polyethylene separator is a key component of lithium-ion batteries, located between the positive and negative electrodes. They allow the passage of lithium ions while inhibiting electron transport. The performance of the separator affects the capacity, cycle and safety of the battery, and thus is critical to the overall performance of the battery.
Detail & Parts
Technical specifications
Material: | SK single layer PE film |
thickness: | 16μm |
width: | 115mm |
Air permeability: | 200s |
Porosity: | 44% |
Heat shrinkage rate: | Vertical 3% Horizontal 1% |
tensile strength: | Vertical 1200kgf/cm2 Horizontal 1200kgf/cm2 |
Storage conditions: | The best storage environment temperature is 25±3°C, humidity is 30%-70%, moisture-proof |
The products we show are available in different sizes and custom sizes are available on request.
Advantages
- Chemical Resistance: Polyethylene separators exhibit excellent resistance to acids, alkalis and most chemicals.
- Consistent pore structure: The separator maintains a consistent pore structure with high chemical and thermal stability.
- Versatility: They are available in various battery types, making them suitable for different applications.
- Oxidation resistance: The polyethylene separator has excellent oxidation resistance, ensuring excellent cycle and trickle charge performance.
- Lateral "zero" shrinkage: The transverse "zero" shrinkage of the separator reduces internal short circuits and enhances dimensional integrity at high temperatures.
FAQ
What Considerations Should Be Made For Battery Case Gaskets?
What Is The Role Of Battery Case Gaskets?
What Are Lithium-air Battery Cases?
How Should Button Battery Cases Be Chosen For Specific Applications?
4.8
out of
5
The delivery was incredibly fast, arriving within a few days of placing the order. The quality of the separator is exceptional and has significantly improved the performance of our lithium-ion batteries.
4.7
out of
5
The polyethylene separator has proven to be an excellent investment. It has extended the lifespan and efficiency of our batteries, making them more reliable and cost-effective.
4.9
out of
5
The separator's lateral 'zero' shrinkage feature is a game-changer. It has greatly reduced the risk of internal short circuits, enhancing the safety and stability of our batteries.
4.6
out of
5
The polyethylene separator's high chemical and thermal stability has been impressive. It has maintained its integrity even under extreme conditions, ensuring consistent performance and longevity.
4.8
out of
5
The separator's consistent pore structure has significantly improved the capacity and cycle life of our batteries. We've witnessed a noticeable increase in energy storage and reduced degradation over time.
4.9
out of
5
The versatility of the polyethylene separator is commendable. Its compatibility with various battery types has made it an indispensable component in our research and development initiatives.
4.7
out of
5
The excellent oxidation resistance of the separator has been instrumental in enhancing the cycle and trickle charge performance of our batteries. It has resulted in improved durability and reliability.
4.8
out of
5
The polyethylene separator's chemical resistance has been remarkable. It has shown exceptional resilience against acids, alkalis, and most chemicals, ensuring long-term stability and performance.
4.6
out of
5
The separator's lateral 'zero' shrinkage feature has been a lifesaver. It has eliminated internal short circuits and maintained dimensional integrity at high temperatures, significantly improving the safety and reliability of our batteries.
4.9
out of
5
The polyethylene separator's exceptional quality has exceeded our expectations. It has enhanced the cycle life and capacity of our batteries, leading to improved performance and extended lifespan.
4.7
out of
5
The separator's consistent pore structure has been a game-changer for our research. It has enabled us to achieve higher energy densities and improved rate capabilities, pushing the boundaries of battery technology.
4.8
out of
5
The versatility of the polyethylene separator has been a boon to our diverse battery applications. Its compatibility with different battery types has allowed us to streamline our manufacturing processes and improve efficiency.
4.6
out of
5
The separator's excellent oxidation resistance has been crucial in extending the lifespan of our batteries. It has minimized capacity fade and maintained high performance over extended periods.
4.9
out of
5
The polyethylene separator's chemical resistance has been a lifesaver in our harsh operating conditions. It has withstood exposure to corrosive chemicals and extreme temperatures, ensuring uninterrupted performance.
4.7
out of
5
The separator's lateral 'zero' shrinkage feature has been a major breakthrough for our battery safety. It has eliminated internal short circuits and thermal runaway risks, making our batteries safer and more reliable.
4.8
out of
5
The polyethylene separator's high-temperature resistance has been a game-changer for our high-power applications. It has enabled us to push the limits of battery performance without compromising safety and reliability.
4.6
out of
5
The separator's exceptional quality has been a major factor in our successful battery development. It has consistently delivered high performance and reliability, making it an indispensable component in our cutting-edge battery systems.
4.9
out of
5
The polyethylene separator's consistent pore structure has been a major breakthrough for our research. It has enabled us to achieve unprecedented levels of energy density and cycle life, pushing the boundaries of battery technology.
4.7
out of
5
The separator's versatility has been a major advantage for our diverse battery applications. Its compatibility with different battery chemistries and configurations has allowed us to streamline our manufacturing processes and reduce costs.
Products
Polyethylene Separator for Lithium Battery
REQUEST A QUOTE
Our professional team will reply to you within one business day. Please feel free to contact us!
Related Products
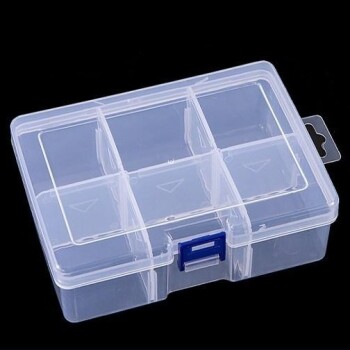
Button Battery Storage Box for Battery Lab
Button-type battery storage box, detachable, high-quality PP environmental protection material; suitable for small objects/chemicals, etc., thickened, compressive, durable, and available in a variety of styles.
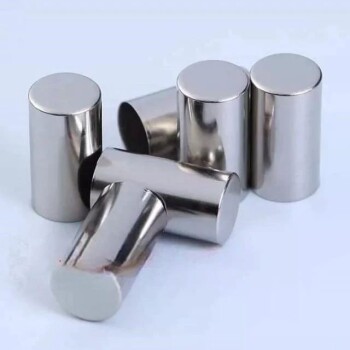
Cylindrical Battery Steel Case for Battery Lab
Lithium-ion battery casing suppresses battery polarization, reduces thermal effects, and improves rate performance.
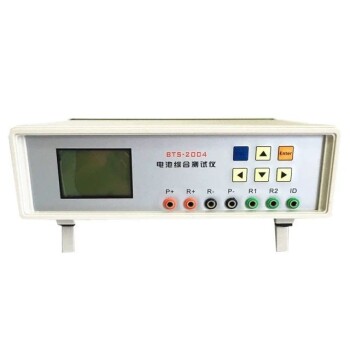
Battery Lab Equipment Battery Capacity and Comprehensive Tester
The scope of application of the battery comprehensive tester can be tested: 18650 and other cylindrical, square lithium batteries, polymer batteries, nickel-cadmium batteries, nickel-metal hydride batteries, lead-acid batteries, etc.
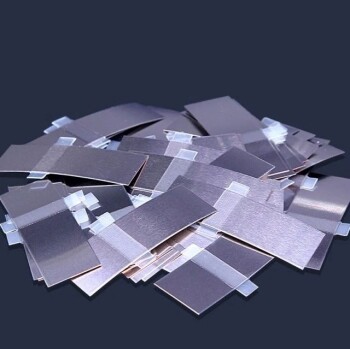
Nickel Aluminum Tabs for Soft Pack Lithium Batteries
Nickel tabs are used to manufacture cylindrical and pouch batteries, and positive aluminum and negative nickel are used to produce lithium-ion and nickel batteries.
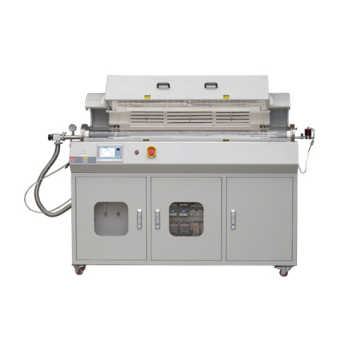
Rotary Tube Furnace Split Multi Heating Zone Rotating Tube Furnace
Multi zone rotary furnace for high-precision temperature control with 2-8 independent heating zones. Ideal for lithium ion battery electrode materials and high-temperature reactions. Can work under vacuum and controlled atmosphere.
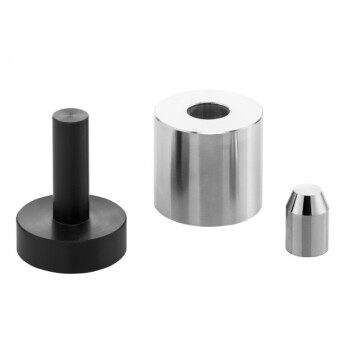
Button Battery Tablet Press Sealing Mold for Lab Use
The sealing die is essential for assembling button batteries, ensuring components like the anode, cathode, and electrolyte are securely enclosed.
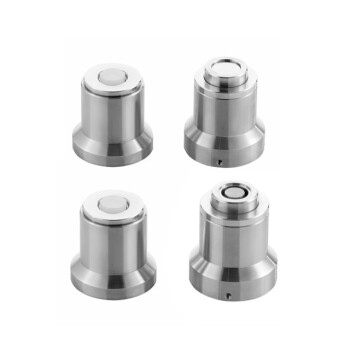
Button Battery Disassembly and Sealing Mold for Lab Use
The simple sealing and disassembly mold can be directly used on ordinary tablet presses, which can save costs, is convenient and fast, and can be used to encapsulate and disassemble button batteries. Other specifications can be customized.
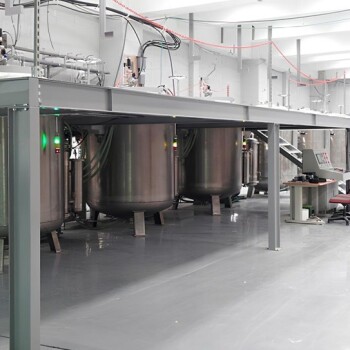
Graphite Vacuum Furnace Negative Material Graphitization Furnace
Graphitization furnace for battery production has uniform temperature and low energy consumption. Graphitization furnace for negative electrode materials: an efficient graphitization solution for battery production and advanced functions to enhance battery performance.
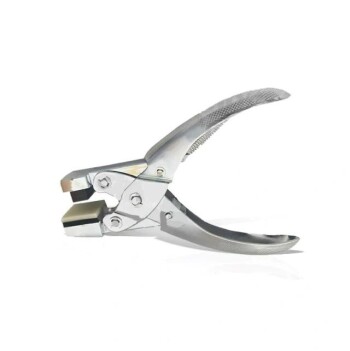
Professional Cutting Tools for Carbon Paper Cloth Diaphragm Copper Aluminum Foil and More
Professional tools for cutting lithium sheets, carbon paper, carbon cloth, separators, copper foil, aluminum foil, etc., with round and square shapes and different sizes of blades.
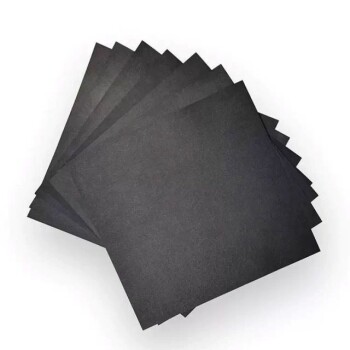
Hydrophilic Carbon Paper TGPH060 for Battery Lab Applications
Toray carbon paper is a porous C/C composite material product (composite material of carbon fiber and carbon) that has undergone high-temperature heat treatment.
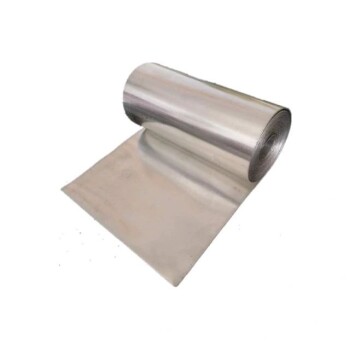
High Purity Zinc Foil for Battery Lab Applications
There are very few harmful impurities in the chemical composition of zinc foil, and the surface of the product is straight and smooth; it has good comprehensive properties, processability, electroplating colorability, oxidation resistance and corrosion resistance, etc.
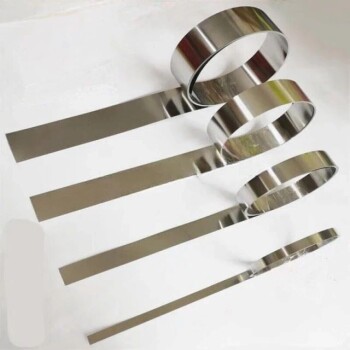
Battery Lab Equipment 304 Stainless Steel Strip Foil 20um Thick for Battery Test
304 is a versatile stainless steel, which is widely used in the production of equipment and parts that require good overall performance (corrosion resistance and formability).
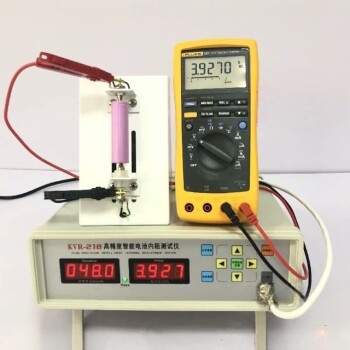
Internal Battery Resistance Tester
The main function of the battery internal resistance tester is to test the charging function, discharging function, internal resistance, voltage, protection function, capacity, overcurrent, and short circuit protection time.
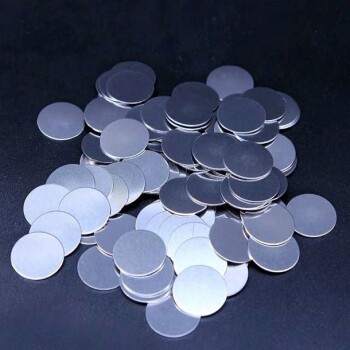
Button Battery Case Gasket for Battery Lab Applications
The gasket prevents the deformation of the internal material, and the spring sheet is conducive to the tight contact inside the battery to prevent loosening.
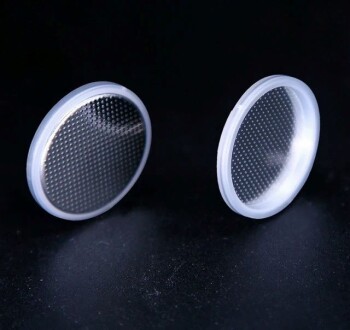
Button Battery Case for Battery Lab Applications
Button batteries are also known as micro batteries. It looks like a small button-shaped battery. Usually larger in diameter and thinner in thickness.
Electric Rotary Kiln Continuous Working Small Rotary Furnace Heating Pyrolysis Plant
Efficiently calcine and dry bulk powder and lump fluid materials with an electric heating rotary furnace. Ideal for processing lithium ion battery materials and more.
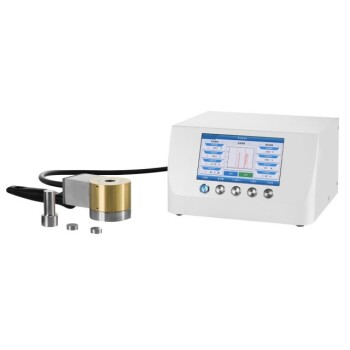
Cylindrical Lab Electric Heating Press Mold for Laboratory Applications
Efficiently prepare samples with Cylindrical Lab Electric Heating Press Mold. Fast heating, high temp & easy operation. Custom sizes available. Perfect for battery, ceramic & biochemical research.
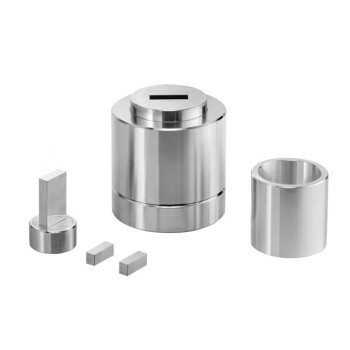
Assemble Square Lab Press Mold for Laboratory Applications
Achieve perfect sample preparation with Assemble Square Lab Press Mold. Quick disassembly eliminates sample deformation. Perfect for battery, cement, ceramics, and more. Customizable sizes available.
Related Articles
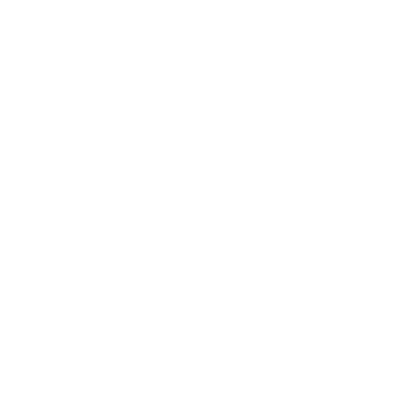
Battery sealing machine operating steps and precautions
Introduction to the operating steps and precautions of the battery sealing machine
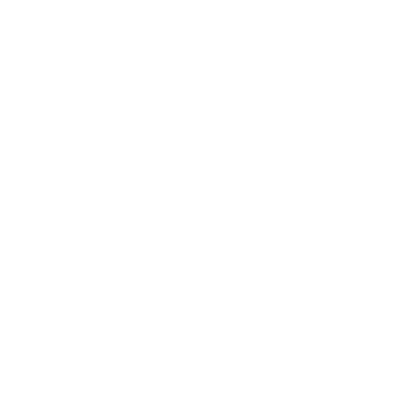
Electrolytic Batteries A Solution to the Growing Energy Demands
The design of electrolytes remains a challenge, but automated discovery and the power of AI are promising tools for advancing this field.
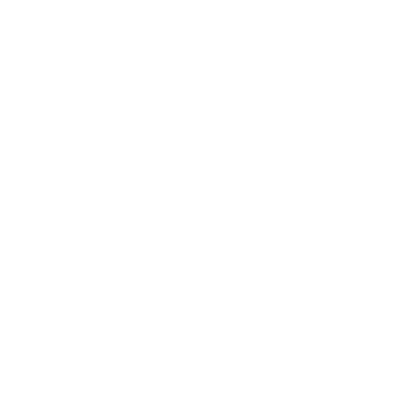
Understanding the Principles and Applications of Isostatic Pressing
In this process, the powder is filled in a mold and sealed tightly. This occurs outside the pressure vessel. After filling the mold with powder, the mold is submerged in the pressure fluid within the pressure vessel. Then isostatic pressure is applied to the external surface of the mold, compressing the powder into a solid mass.
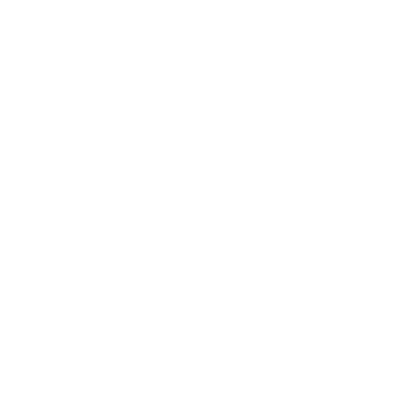
Design and Application of Reference Electrodes in Lithium Batteries
This article discusses the selection and design of reference electrodes for lithium batteries, focusing on active materials like lithium metal, lithium alloys, and lithium-embedded oxides.
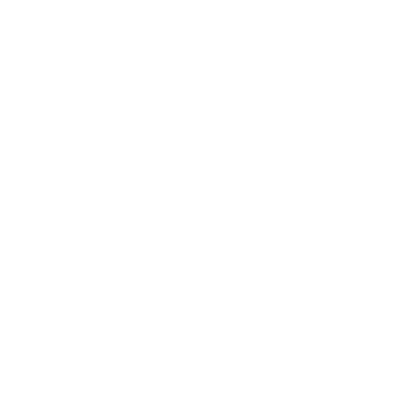
Design Principle and Application of Reference Electrodes for Lithium Batteries
Discusses the design principles, types, applications, and future directions of reference electrodes in lithium batteries.
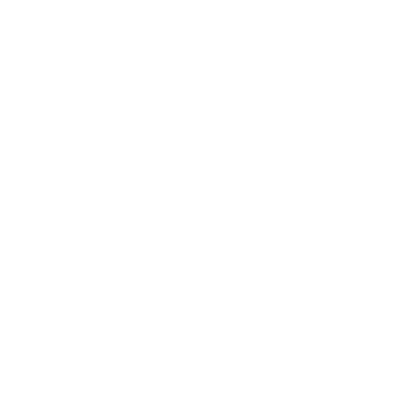
Carbon Coating for Surface Modification of Silicon-Based Materials in Lithium-Ion Batteries
This article discusses the application of carbon coatings to improve the performance of silicon-based anode materials in lithium-ion batteries.
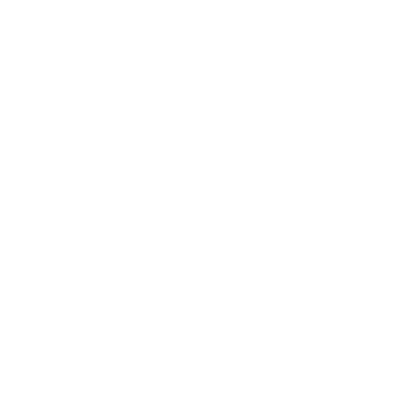
Understanding Isostatic Pressing: Process, Benefits, Limitations, and Applications
Isostatic pressing is a manufacturing process that offers numerous benefits and applications in various industries. It involves subjecting a material to equal pressure from all directions to achieve uniform density and shape. This method is particularly advantageous compared to other production techniques.
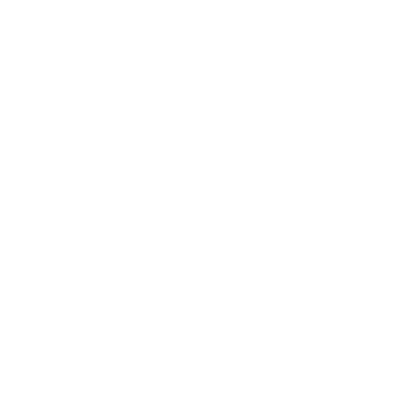
Comprehensive Guide to Isostatic Pressing: Types, Processes, and Features(3)
Isostatic pressing is a versatile manufacturing process that is widely used in various industries. It involves subjecting a material to equal pressure from all directions to achieve uniform density and shape. Isostatic pressing offers numerous advantages, such as the ability to produce complex shapes, uniformity in material properties, and high precision.
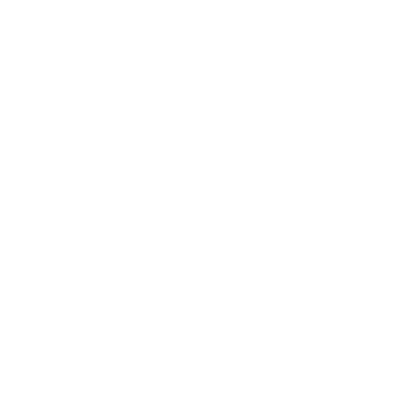
Selecting Isostatic Pressing Equipment for High-Density Molding
An in-depth look at isostatic pressing techniques and equipment selection for achieving high-density molding.
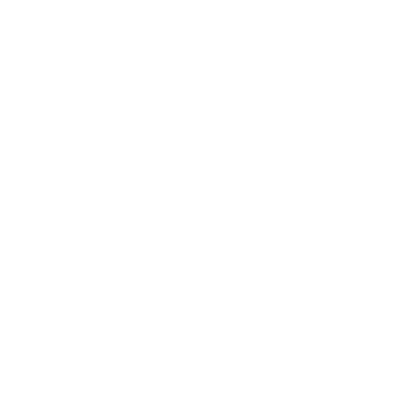
Zirconia Ceramic Rod Production Processes: Isostatic Pressing vs. Dry Pressing
A comparison of isostatic pressing and dry pressing in zirconia ceramic rod production, highlighting differences and advantages.
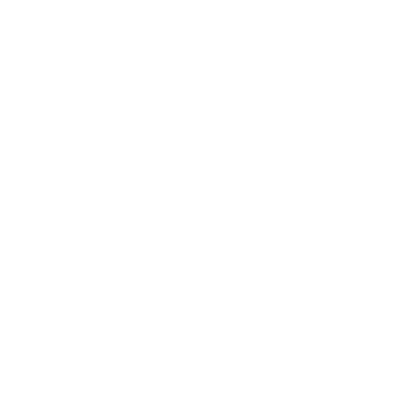
Understanding the Isostatic Pressing Process and its Types
Isostatic pressing, a technique that applies hydrostatic pressure to a material to improve its density and mechanical strength, has seen significant growth and development over the years. Isostatic pressing is commonly used for the consolidation of powders and defect healing of castings, making it a versatile process for a range of materials including ceramics, metals, composites, plastics, and carbon.
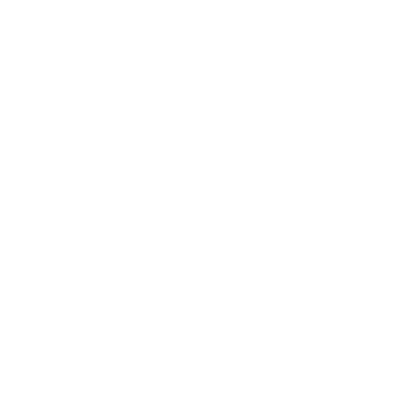
Isostatic Pressing Technology: Principles, Classification, and Applications
An in-depth look at isostatic pressing technology, its types, and diverse applications across various industries.