Principle of Isostatic Pressing
Table of Contents
- Principle of Isostatic Pressing
- Manufacturing Process
- Overview of cold isostatic pressing (CIP) and how it achieves a uniform density in a compact
- Explanation of how no lubricant needs to be added to the powder, resulting in greater green strengths
- Details of the wet-bag technique, including the use of pressurized fluid and an intensifier/pumping system
- Details of the dry-bag technique, including its advantages in automation of bag-filling, compaction and compact removal
- Materials used in Isostatic Pressing
- Design Capabilities of Isostatic Pressing
- Discussion on how CIP can produce components and preforms of greater size and complexity
- Explanation of how components with longer length/diameter ratios can be produced with uniform density along their complete length
- Comparison of the densities and green strengths of compacts produced with CIP versus die compaction
- Details on how complex undercut and threaded shapes can be produced with CIP
Working of Isostatic Press
Isostatic pressing is enabled to produce various types of materials from powder compacts by reducing the porosity of the powder mixture. The powder mixture is compacted and encapsulated using isostatic pressure, by using pressure equally applied from all directions. Isostatic pressing confines the metal powder within a flexible membrane or hermetic container which acts as a pressure barrier between the powder and the pressurizing medium, liquid or gas that surrounds it.
Principle of isostatic pressing
- Powder is placed and sealed in a flexible mold such as polyurethane and is then subjected to a uniform hydrostatic pressure.
- Wet-bag technique. Flexible bag containing the powder is submerged in the pressure vessel containing the pressurizing fluid, such as soluble oil.
- Dry-bag technique. Flexible bag is "fixed" in the pressure vessel and powder can be loaded without bag having to leave the vessel.
Material in powder form is sealed into a flexible mold (or bag) situated inside a pressure vessel. Hydrostatic pressure is applied to the outside of the mold, until the powder molecules inside have bonded sufficiently. Subsequent finishing processes may be required.
Alternative Processes
Isostatic pressing is a powder processing technique that uses fluid pressure to compact the part. Metal powders are placed in a flexible container, which becomes the mold for the part. Fluid pressure is exerted over the entire outside surface of the container, causing the container to press and form the powder into the correct geometry. Isostatic pressing is special in its use of all-around pressure.
There are two general types of isostatic pressing operations: wet bag and dry bag. The wet bag variation involves a separate elastomeric mold that is loaded outside of the press and then submerged in the pressure vessel. The dry bag variation circumvents the immersion step by creating a mold that is integrated into the pressure vessel. In the dry bag process, the powder is added to the mold, the mold sealed, pressure applied, and then the part ejected.
Dry Bag Technology
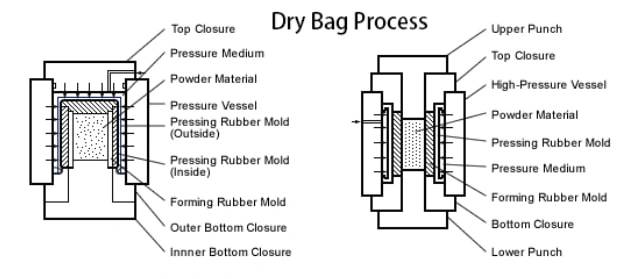
In this process, the mold is fixed in the pressure vessel. The powder is filled in the mold while it is still in the pressure vessel. After this, isostatic pressure from the pressure liquid is applied to the external surface of the mold, compressing the powder into a solid mass with a compact microstructure.
Dry bag technology is ideal for the mass production of materials. This process usually takes as little as 1 minute. It is way faster than wet bag technology.
Wet Bag Technology
In this process, the powder is filled in a mold and sealed tightly. This occurs outside the pressure vessel. After filling the mold with powder, the mold is submerged in the pressure fluid within the pressure vessel. Then isostatic pressure is applied to the external surface of the mold, compressing the powder into a solid mass.
This process is not as common as the other type of cold isostatic pressing. There are over 3000 wet bag presses used all over the world today. These wet bags have sizes ranging from as small as 50mm to as big as 2000mm in diameter.
It takes from 5 to 30 minutes to process material using wet bag technology. Thus, it is relatively slow. However, high-volume pumps and improved loading mechanisms can go a long way in speeding up the process.
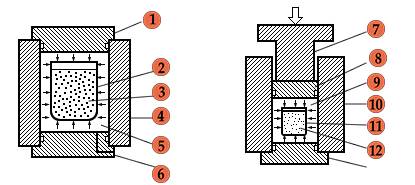
Isostatic Pressing Process
In the isostatic pressing process, products are put in a closed container full of liquid and applied equal pressure to each surface to increase their density under high pressure, thus obtaining the required shapes. Isostatic presses are widely used in the forming of high-temperature refractory, ceramics, cemented carbide, lanthanum permanent magnet, carbon material, and rare metal powder.
Manufacturing Process
Overview of cold isostatic pressing (CIP) and how it achieves a uniform density in a compact
Cold isostatic pressing (CIP) is a compaction process for powders confined in an elastomer mold. The mold is placed in a pressure chamber and subjected to high pressure from all sides. This process is commonly used with powdered metallurgy, cemented carbides, refractory materials, graphite, ceramics, plastics, and other materials. CIP helps achieve a uniform density in the compact, ensuring consistent quality and performance.
Explanation of how no lubricant needs to be added to the powder, resulting in greater green strengths
In the cold isostatic pressing process, no lubricant needs to be added to the powder. This is because the compaction is achieved through the application of pressure from all sides. The absence of lubricant results in greater green strengths, as there is no interference between the powder particles and the lubricant. This leads to a more densely packed compact with improved mechanical properties.
Details of the wet-bag technique, including the use of pressurized fluid and an intensifier/pumping system
In the wet bag technique of cold isostatic pressing, the powder material is filled in a mold or bag, which is then tightly sealed. The mold or bag is submerged in a pressure vessel filled with pressurized fluid, such as oil or water. The intensifier or pumping system applies isostatic pressure to the external surface of the mold, compressing the powder into a solid mass. This technique is suitable for multi-shape and small to large quantity production, and for the pressing of large size products.
Details of the dry-bag technique, including its advantages in automation of bag-filling, compaction and compact removal
In the dry-bag technique of cold isostatic pressing, the mold is fixed in the pressure vessel. The powder is filled in the mold while it is still in the pressure vessel. Isostatic pressure from the pressure fluid is then applied to the external surface of the mold, compressing the powder into a solid mass. The dry-bag technique offers advantages in the automation of bag-filling, compaction, and compact removal. It is ideal for mass production and can significantly reduce processing time compared to the wet-bag technique.
Materials used in Isostatic Pressing
List of various powders that can be compacted using CIP, including ceramics, tungsten powders, and high alloy ferrous billets
Isostatic pressing, also known as Cold Isostatic Pressing (CIP), is a process used to compact a variety of powders into solid shapes. This method is widely used in various industries due to its versatility and effectiveness. Some of the materials that can be compacted using CIP include:
-
Ceramics: Isostatic pressing is commonly used to compact ceramics such as alumina, silicon nitride, silicon carbide, and sialons. These ceramics are subjected to isostatic pressure, which helps reduce their porosity and increase their density.
-
Tungsten Powders: Tungsten powders are another type of material that can be compacted using CIP. This process allows for the production of various shapes and sizes of tungsten components.
-
High Alloy Ferrous Billets: High alloy ferrous billets are often compacted using CIP before undergoing hot isostatic pressing (HIP). This helps improve the overall strength and quality of the final product.
ceramics, tungsten powders, and high alloy ferrous billets
Description of how a variety of ceramics including alumina, silicon nitride, silicon carbide and sialons are subjected to CIP.
Ceramics such as alumina, silicon nitride, silicon carbide, and sialons are commonly subjected to Cold Isostatic Pressing (CIP) to achieve a high level of density and strength. The CIP process involves placing the ceramic powder into flexible molds, usually made of rubber or elastomers.
There are two main techniques used in CIP: the wet-bag technique and the dry-bag technique. In the wet-bag technique, the powder-filled molds are immersed in water or other liquids, and pressure is applied isostatically. This method allows for the compaction of complex shapes and even tungsten ingots weighing up to 1 ton. On the other hand, the dry-bag technique is used for simpler shapes, where the powder-filled mold is sealed, and compression occurs between the mold and the pressure vessel.
Isostatic pressing applies pressure equally from all directions, resulting in a uniform density distribution and high billet strength. This process is particularly beneficial for ceramics with high performance and strength requirements. It allows for the production of parts with concave, hollow, and slender features, as well as other complex shapes.
In summary, Cold Isostatic Pressing is a versatile method for compacting various materials, including ceramics, tungsten powders, and high alloy ferrous billets. The process involves subjecting the powders to isostatic pressure in flexible molds, resulting in dense and strong components. Ceramics such as alumina, silicon nitride, silicon carbide, and sialons are commonly compacted using CIP, allowing for the production of complex shapes with high performance and strength requirements.
Design Capabilities of Isostatic Pressing
Discussion on how CIP can produce components and preforms of greater size and complexity
Cold Isostatic Pressing (CIP) is a powder-based, near-net-shape technology that allows for the production of metal and ceramic components of greater size and complexity. With CIP, a variety of powders, including metals, ceramics, plastics, and composites, can be pressed isostatically on a commercial scale. The process involves placing the powder in a flexible mold, which is then subjected to high pressure from all directions using a liquid medium. This allows for the production of components and preforms that are difficult or impossible to produce by other methods.
Explanation of how components with longer length/diameter ratios can be produced with uniform density along their complete length
One of the advantages of CIP is its ability to produce components with longer length/diameter ratios while maintaining uniform density along their complete length. The pressure exerted by the fluid during the isostatic pressing process provides uniform compaction of the powder, resulting in uniform density within the compacted part. This uniform density is crucial for components with longer length/diameter ratios, as it ensures consistent mechanical properties and performance throughout the entire length of the component.
Comparison of the densities and green strengths of compacts produced with CIP versus die compaction
Compared to die compaction, CIP offers the advantage of achieving more uniform densities due to minimized friction effects. Die compaction relies on rigid dies, which can result in uneven compaction and density variations within the compacted part. In contrast, CIP uses flexible molds that allow for pressure to be applied uniformly from all directions, reducing friction and ensuring more consistent density distribution. This results in compacts with higher uniform densities and improved mechanical properties.
Details on how complex undercut and threaded shapes can be produced with CIP
CIP is particularly well-suited for the production of complex undercut and threaded shapes. The flexibility of the molds used in CIP allows for the creation of intricate and intricate geometries that would be challenging or impossible to achieve with other manufacturing methods. The pressure exerted by the fluid during isostatic pressing ensures that the powder fills all the intricate features of the mold, resulting in components with complex undercut and threaded shapes. This capability makes CIP a valuable process for industries that require components with intricate designs, such as aerospace and automotive.
Isostatic pressing offers a range of design capabilities that make it a versatile manufacturing process. The ability to produce components and preforms of greater size and complexity, achieve uniform density along the complete length of components, and create complex undercut and threaded shapes makes CIP an attractive option for a variety of industries. Whether it's for applications in aerospace, automotive, or other sectors, isostatic pressing provides a cost-effective solution for producing high-quality components with intricate designs.
CONTACT US FOR A FREE CONSULTATION
KINTEK LAB SOLUTION's products and services have been recognized by customers around the world. Our staff will be happy to assist with any inquiry you might have. Contact us for a free consultation and talk to a product specialist to find the most suitable solution for your application needs!