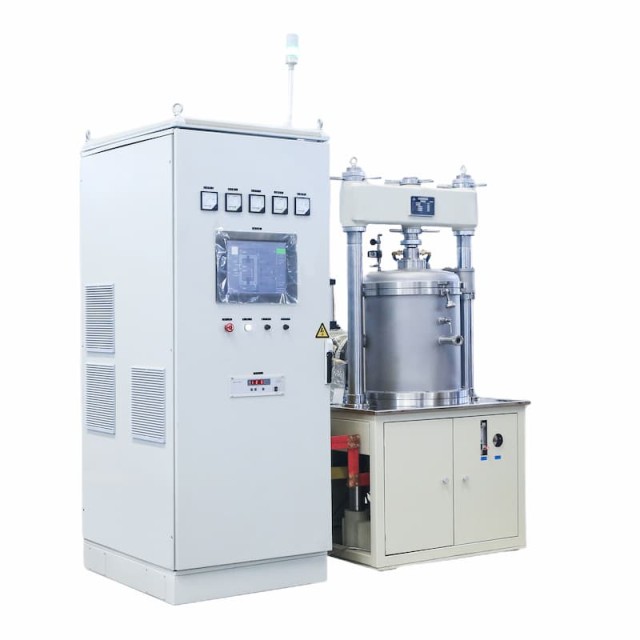
Vacuum Hot Press Furnace
Vacuum Hot Press Furnace Machine Heated Vacuum Press
Item Number : KT-VHP
Price varies based on specs and customizations
- Working temperature
- 1500℃ / 2200℃
- Working pressure
- 10-400T
- Press distance
- 100-200mm
- Vacuum pressure
- 6x10-3Pa
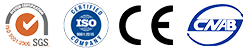
Shipping:
Contact us to get shipping details Enjoy On-time Dispatch Guarantee.
Why Choose Us
Reliable PartnerEasy ordering process, quality products, and dedicated support for your business success.
Introduction
Vacuum hot pressing furnace is a complete set of equipment that heats and pressurizes materials under vacuum or atmosphere. According to different materials and heating temperatures, heating elements can be graphite heater, molybdenum heater, and induction heating, etc; and one-way or two-way pressurization can be used for hydraulic pressurization.
Under the high temperature and high pressure and vacuum or atmosphere, the raw material solid particles are bonded with each other, the grains grow up, and the voids (pores) and grain boundaries gradually decrease;Through the transfer of materials, their total volume shrinks, and their density increases, becoming a compact polycrystalline sintered body with a specific microstructure, so that the materials can be pressed and formed.
The density, hardness and other mechanical, electronic and thermal properties of the finished materials can be significantly improved under high temperature and pressure as well as under vacuum or atmosphere
Applications
The Vacuum Tube Hot Press Furnace is a versatile and powerful tool used across various industries for high-temperature processes. This furnace, capable of operating in a vacuum or controlled atmosphere, is particularly suited for applications requiring precise temperature control and a clean environment. Key application areas include:
- Crystal Growth: Ideal for the synthesis and growth of various types of crystals, which are crucial in the electronics and semiconductor industries.
- Heat Treatment: Used for the thermal processing of metals and alloys to enhance their mechanical properties, such as hardness, ductility, and strength.
- Thin Film Deposition: Essential for the deposition of thin films in the manufacturing of electronic devices, solar cells, and optical coatings.
- Materials Science Research: Widely used in laboratories for research on new materials, including ceramics, composites, and advanced alloys.
- Metallurgy: Helps in the purification and alloying of metals, as well as in the production of refractory materials.
- Electronics Manufacturing: Critical for processes like annealing, sintering, and the production of electronic components.
- Chemical Industry: Utilized for high-temperature chemical reactions and the synthesis of chemicals under controlled atmospheres.
- Glass Manufacturing: Useful in the production of specialty glasses and the modification of glass properties through heat treatment.
- Special Materials Production: Involved in the creation of materials with unique properties, such as those used in aerospace and defense.
- Academic and Research Institutions: A staple in university laboratories and research centers for advanced materials research and development.
Detail & Parts
- Double shell structure with water-cooled jacket, the inner shell is made of stainless steel and has been finely polished. Housings are high quality carbon steel with anti-rust treatment or stainless steel with pad blasting.
- The heating element adopts graphite or molybdenum wire. Heating is divided into 1-phase or 3-phase heating. The rational design of the heating element helps to improve the uniformity of the temperature in the cavity.
- The furnace can be easily operated through the electrical control system. The temperature and pressure are controlled by PLC analog, or the sintering process is automatically completed by using a temperature and pressure programmable controller. The control system has alarm and protection functions such as water cut off, over temperature and over current.
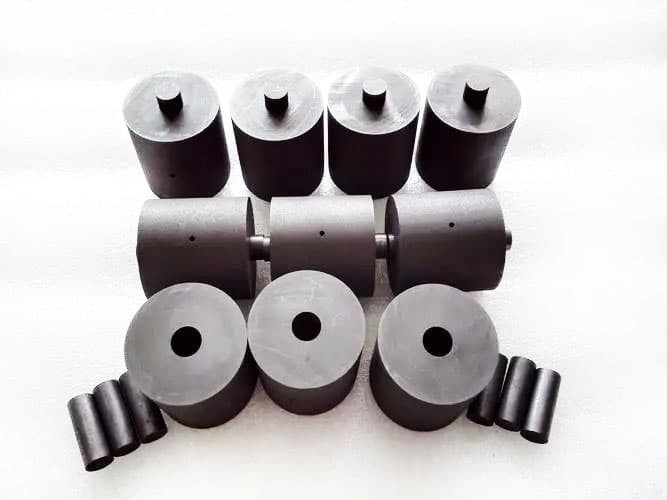
Principle
The Vacuum Tube Hot Press Furnace operates by heating and pressurizing materials under vacuum or atmosphere. It utilizes heating elements like graphite or molybdenum heaters and can apply one-way or two-way pressurization. This process bonds raw material particles, reduces voids, and increases density, forming a compact sintered body. The furnace is designed for various industries, ensuring precise heat treatment and material sintering.
Advantages
The Vacuum Tube Hot Press Furnace offers a plethora of advantages that make it a superior choice for various heat treatment processes and applications. Here are some of the key benefits:
- Versatility in Heat Treatment Processes: The furnace supports a wide range of heat treatment processes, making it suitable for various materials and industries. This versatility ensures that it can meet diverse needs in material processing.
- High-Speed Cycles with High-Pressure Gas Quench: The furnace is designed to facilitate high-speed cycles, which are essential for efficient production. The high-pressure gas quench feature enhances the cooling process, leading to faster cycle times and increased productivity.
- Energy and Resource Efficiency: With low consumption of energy and process gases, the furnace is environmentally friendly and cost-effective. This efficiency not only reduces operational costs but also minimizes the environmental footprint.
- Environmentally Friendly with Low Emissions: The design of the furnace ensures low emissions of process gases, making it an eco-conscious choice for industries looking to minimize their environmental impact.
- Simple and Modular Design: The simple design of the furnace allows for easy installation and maintenance. Its modular nature means it can be fitted and adjusted to specific tasks and plant conditions, ensuring optimal performance.
- Guaranteed Quality and Repeatable Process Resul: The furnace is engineered to deliver guaranteed quality and repeatable process results, which is crucial for industries where precision and consistency are paramount.
- Predictive Maintenance: Advanced features such as predictive maintenance help in identifying potential issues before they escalate, ensuring minimal downtime and prolonging the lifespan of the equipment.
Structure introduction
This electric furnace has two types of graphite heating and resistance wire heating, which are suitable for sintering metal powder, inorganic non-metallic materials, etc. under vacuum and hh temperature hot pressing; of course, hot pressing sintering can also be carried out under protective atmosphere. In this way, the densification of the material can be completed, deformation can be prevented, and the grain size of the nanopowder can be suppressed.
Specification |
|
---|---|
Furnace shell |
|
Stove side |
|
The heating element |
|
The insulation layer |
|
The vacuum system |
|
The main circuit of the electric control system |
|
Features
- Double layer SUS304 stainless steel vacuum chamber structure, jacket cold water circulating cooling method to keep the furnace surface temperature
- Double column supporting structure, stable hydraulic press system,pressure can be manual control or automatic control,precise pressure regulating and maintaining
- Advanced thermal insulation materials with low thermal conductivity and good thermal insulation effect, which can effectively isolate heat and reduce energy consumption
- The temperature range is wide. A variety of heating elements can be selected, such as graphite, molybdenum, tungsten, induction heating, etc. The temperature can reach 2800 ℃ in a suitable protective atmosphere, which can adapt to hot pressing sintering of different materials;
- Diversified vacuum system configuration, different vacuum degrees are selected according to the process;
- A charging and discharging system is provided, which can be used for hot pressing sintering in vacuum environment, inert atmosphere or reducing atmosphere;
- Humanized configuration, both manual operation and intelligent operation can be realized;
- One furnace for multiple purposes can be used as a simple vacuum or atmosphere sintering furnace;
- Diversified optional functional types available, vertical upper discharge, vertical side outlet discharge, one-way pressurization, two-way pressurization, etc.
Technical specifications
Working temperature | 1500℃ / 2200℃ |
---|---|
Heating element | Molybdenum/Graphite |
Working pressure | 10-400T |
Press distance | 100-200mm |
Vacuum pressure | 6x10-3Pa |
Effective working area diameter range | 90-600mm |
Effective working area diameter range | 120-600mm |
Warnings
Operator safety is the top important issue! Please operate the equipment with cautions. Working with inflammable& explosive or toxic gases is very dangerous, operators must take all necessary precautions before starting the equipment. Working with positive pressure inside the reactors or chambers is dangerous, operator must fellow the safety procedures strictly. Extra caution must also be taken when operating with air-reactive materials, especially under vacuum. A leak can draw air into the apparatus and cause a violent reaction to occur.
Designed for You
KinTek provide deep custom made service and equipment to worldwide customers, our specialized teamwork and rich experienced engineers are capable to undertake the custom tailoring hardware and software equipment requirements, and help our customer to build up the exclusive and personalized equipment and solution!
Would you please drop your ideas to us, our engineers are ready for you now!
FAQ
What Are The Advantages Of Using A Hydraulically Heated Laboratory Press?
What Is The Purpose Of A Vacuum Hot Press Furnace?
What Does A Hydraulic Lab Heat Press Do?
What Are The Advantages Of A Vacuum Hot Press Furnace?
What Types Of Samples Or Materials Can Be Processed In A Hydraulically Heated Laboratory Press?
How Does A Vacuum Hot Press Furnace Work?
How Does A Hydraulically Heated Laboratory Press Work?
What Are The Common Applications Of Vacuum Hot Press Furnaces?
How Can The Performance Of A Hydraulically Heated Laboratory Press Be Optimized?
What Factors Should Be Considered When Selecting A Vacuum Hot Press Furnace?
4.8
out of
5
KINTEK SOLUTION's Vacuum hot press furnace has been a game-changer for our laboratory. The speed of delivery was impressive, and the quality of the equipment is top-notch.
4.9
out of
5
The technological advancements in the Vacuum hot press furnace have revolutionized our research. It's user-friendly and has significantly improved our efficiency.
4.7
out of
5
The Vacuum hot press furnace is a valuable asset to our laboratory. Its durability and reliability have exceeded our expectations.
4.8
out of
5
The Vacuum hot press furnace is a testament to KINTEK SOLUTION's commitment to quality. It's a worthwhile investment that has enhanced our research capabilities.
4.9
out of
5
The Vacuum hot press furnace has transformed our laboratory. Its speed and efficiency have enabled us to complete projects in record time.
4.7
out of
5
The Vacuum hot press furnace has revolutionized our material processing techniques. Its versatility and precision have opened up new avenues of research.
4.8
out of
5
KINTEK SOLUTION's Vacuum hot press furnace has exceeded our expectations. Its user-friendly interface and exceptional performance make it an indispensable tool in our laboratory.
4.9
out of
5
The Vacuum hot press furnace is a remarkable piece of equipment. Its cutting-edge technology has enabled us to achieve groundbreaking results in our research.
4.7
out of
5
KINTEK SOLUTION's Vacuum hot press furnace is a game-changer. Its speed, accuracy, and durability make it an invaluable asset to our laboratory.
4.8
out of
5
The Vacuum hot press furnace has been a revelation. Its user-friendly design and exceptional performance have made our research more efficient and productive.
4.9
out of
5
The Vacuum hot press furnace is a remarkable piece of equipment. Its technological advancements have revolutionized our research capabilities.
4.7
out of
5
KINTEK SOLUTION's Vacuum hot press furnace is a valuable addition to our laboratory. Its reliability and durability have made it an indispensable tool for our research.
4.8
out of
5
The Vacuum hot press furnace has been a transformative addition to our laboratory. Its exceptional performance and user-friendly interface have made it a favorite among our researchers.
4.9
out of
5
KINTEK SOLUTION's Vacuum hot press furnace is a testament to their commitment to innovation. Its cutting-edge technology has enabled us to achieve groundbreaking results in our research.
4.7
out of
5
The Vacuum hot press furnace has revolutionized our laboratory. Its speed, accuracy, and durability have made it an indispensable tool for our research.
4.8
out of
5
KINTEK SOLUTION's Vacuum hot press furnace has been a game-changer. Its user-friendly design and exceptional performance have made our research more efficient and productive.
4.9
out of
5
The Vacuum hot press furnace is a remarkable piece of equipment. Its technological advancements have revolutionized our research capabilities.
Products
Vacuum Hot Press Furnace Machine Heated Vacuum Press
REQUEST A QUOTE
Our professional team will reply to you within one business day. Please feel free to contact us!
Related Products
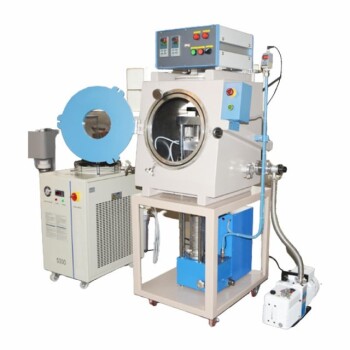
Vacuum Hot Press Furnace Machine for Lamination and Heating
Experience clean and precise lamination with Vacuum Lamination Press. Perfect for wafer bonding, thin-film transformations, and LCP lamination. Order now!
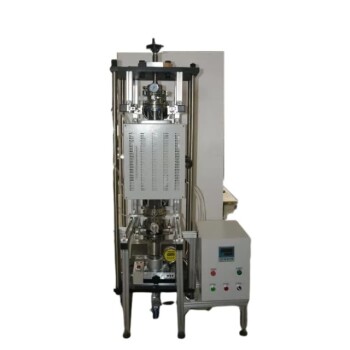
Vacuum Hot Press Furnace Heated Vacuum Press Machine Tube Furnace
Reduce forming pressure & shorten sintering time with Vacuum Tube Hot Press Furnace for high-density, fine-grain materials. Ideal for refractory metals.
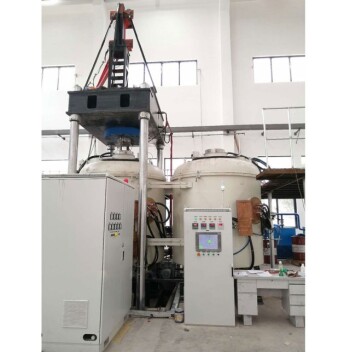
600T Vacuum Induction Hot Press Furnace for Heat Treat and Sintering
Discover the 600T Vacuum Induction Hot Press Furnace, designed for high-temperature sintering experiments in vacuum or protected atmospheres. Its precise temperature and pressure control, adjustable working pressure, and advanced safety features make it ideal for nonmetal materials, carbon composites, ceramics, and metal powders.
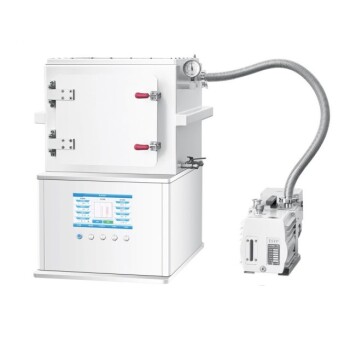
Heated Hydraulic Press Machine with Heated Plates for Vacuum Box Laboratory Hot Press
Enhance your lab's precision with our lab press for vacuum box. Press pills and powders with ease and precision in a vacuum environment, reducing oxidation and improving consistency. Compact and easy to use with a digital pressure gauge.
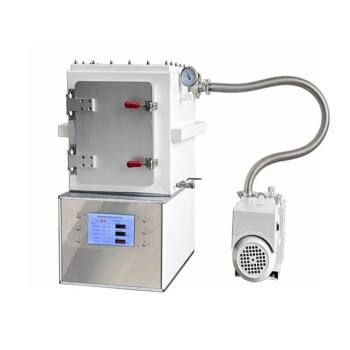
Electric Heated Hydraulic Vacuum Heat Press for Lab
The Electric Vacuum Heat Press is a specialized heat press equipment that operates in a vacuum environment, utilizing advanced infrared heating and precise temperature control for high quality, rugged and reliable performance.
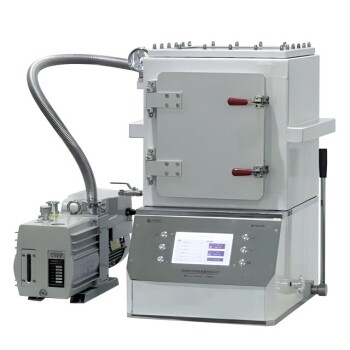
Heated Hydraulic Press Machine with Heated Plates for Vacuum Box Laboratory Hot Press
The lab press for vacuum box is a specialized piece of equipment designed for laboratory use. Its main purpose is to press pills and powders according to specific requirements.
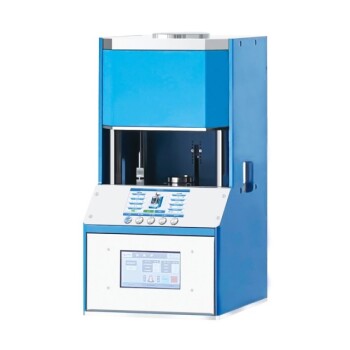
Automatic Heated Hydraulic Press Machine with Heated Plates for Laboratory Hot Press
The Automatic High Temperature Heat Press is a sophisticated hydraulic hot press designed for efficient temperature control and product quality processing.
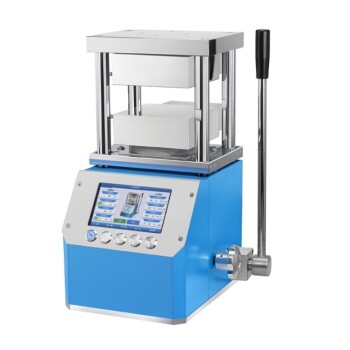
Heated Hydraulic Press Machine with Integrated Manual Heated Plates for Lab Use
Efficiently process heat-pressing samples with our Integrated Manual Heated Lab Press. With a heating range up to 500°C, it's perfect for various industries.
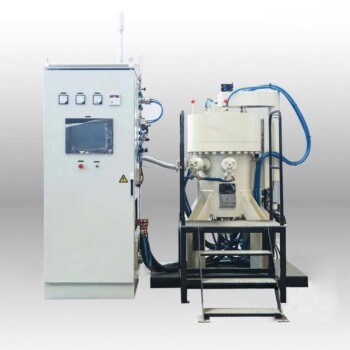
Vacuum Heat Treat and Sintering Furnace with 9MPa Air Pressure
The air pressure sintering furnace is a high-tech equipment commonly used for the sintering of advanced ceramic materials. It combines vacuum sintering and pressure sintering techniques to achieve high-density and high-strength ceramics.
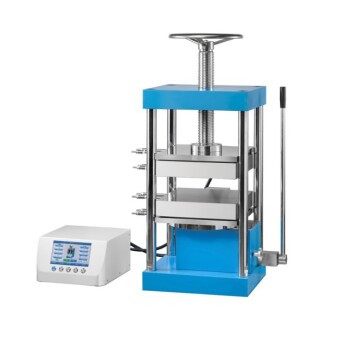
Heated Hydraulic Press Machine with Heated Plates Split Manual Laboratory Hot Press
Efficiently prepare your samples with our Split Manual Heated Lab Press. With a pressure range up to 40T and heating plates up to 300°C, it's perfect for various industries.
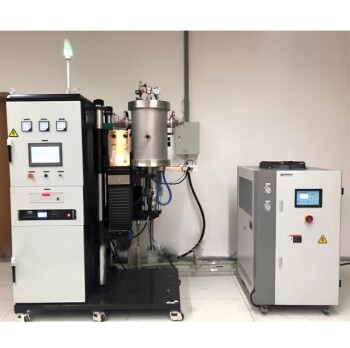
Vacuum Heat Treat and Molybdenum Wire Sintering Furnace for Vacuum Sintering
A vacuum molybdenum wire sintering furnace is a vertical or bedroom structure, which is suitable for withdrawal, brazing, sintering and degassing of metal materials under high vacuum and high temperature conditions. It is also suitable for dehydroxylation treatment of quartz materials.
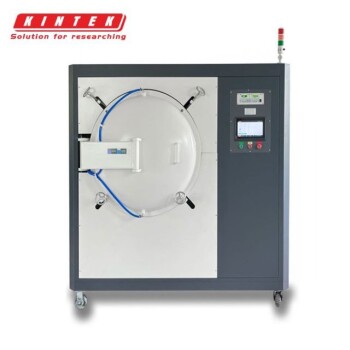
Vacuum Heat Treat Furnace with Ceramic Fiber Liner
Vacuum furnace with polycrystalline ceramic fiber insulation liner for excellent heat insulation and uniform temperature field. Choose from 1200℃ or 1700℃ max. working temperature with high vacuum performance and precise temperature control.
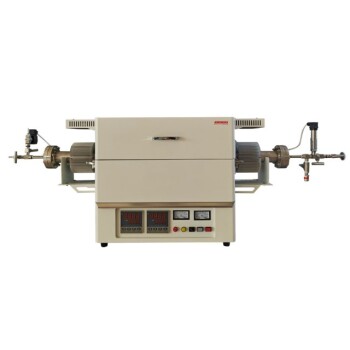
High Pressure Laboratory Vacuum Tube Furnace Quartz Tubular Furnace
KT-PTF High Pressure Tube Furnace: Compact split tube furnace with strong positive pressure resistance. Working temp up to 1100°C and pressure up to 15Mpa. Also works under controller atmosphere or high vacuum.
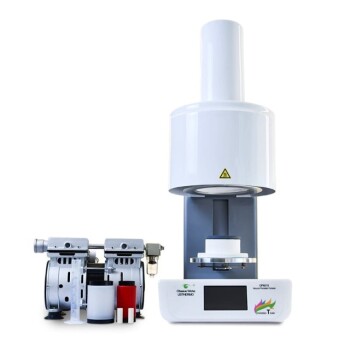
Dental Porcelain Zirconia Sintering Ceramic Vacuum Press Furnace
Get precise dental results with Dental Vacuum Press Furnace. Automatic temperature calibration, low noise tray, and touch screen operation. Order now!
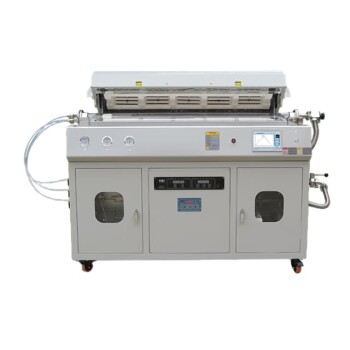
Multi Heating Zones CVD Tube Furnace Machine Chemical Vapor Deposition Chamber System Equipment
KT-CTF14 Multi Heating Zones CVD Furnace - Precise Temperature Control and Gas Flow for Advanced Applications. Max temp up to 1200℃, 4 channels MFC mass flow meter, and 7" TFT touch screen controller.
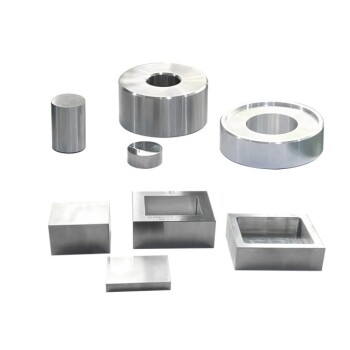
Special Heat Press Mold for Lab Use
Square, round and flat plate forming dies for hot presses.
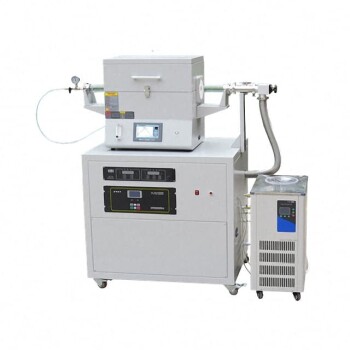
Efficient split chamber CVD furnace with vacuum station for intuitive sample checking and quick cooling. Up to 1200℃ max temperature with accurate MFC mass flowmeter control.
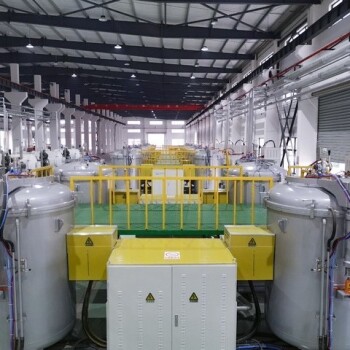
Vertical High Temperature Graphite Vacuum Graphitization Furnace
Vertical high temperature graphitization furnace for carbonization and graphitization of carbon materials up to 3100℃.Suitable for shaped graphitization of carbon fiber filaments and other materials sintered in a carbon environment.Applications in metallurgy, electronics, and aerospace for producing high-quality graphite products like electrodes and crucibles.
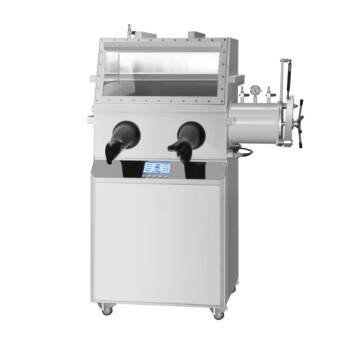
Laboratory Hydraulic Press Lab Pellet Press Machine for Glove Box
Controlled environment lab press machine for glove box. Specialized equipment for material pressing and shaping with high precision digital pressure gauge.
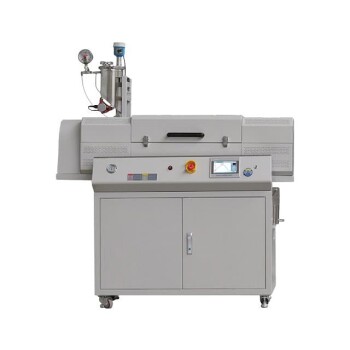
Laboratory Vacuum Tilt Rotary Tube Furnace Rotating Tube Furnace
Discover the versatility of Laboratory Rotary Furnace: Ideal for calcination, drying, sintering, and high-temperature reactions. Adjustable rotating and tilting functions for optimal heating. Suitable for vacuum and controlled atmosphere environments. Learn more now!
Related Articles
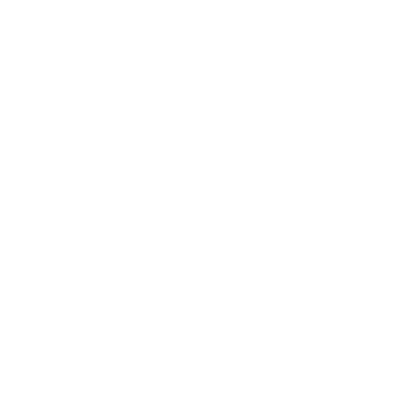
Comprehensive Guide to Vacuum Hot Press Furnace Application
The Vacuum Hot Press Furnace is a versatile tool especially suited for sintering experiments involving non-metallic materials, carbon composites, ceramic materials and metal powder materials.
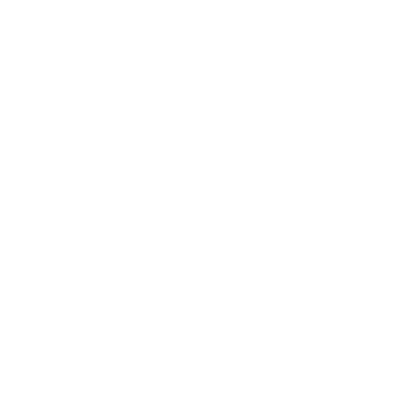
Vacuum Hot Press Furnace: A Comprehensive Guide
Gain in-depth knowledge of Vacuum Hot Press Furnaces, their components, benefits, and applications in various industries. Explore how these furnaces revolutionize material processing and achieve exceptional results.
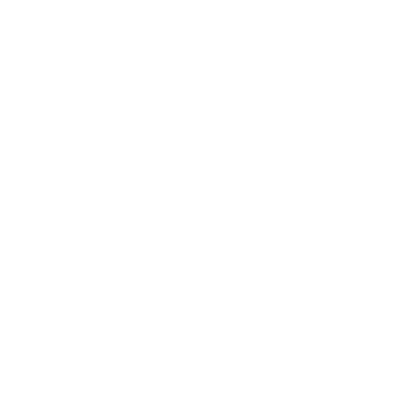
The Ultimate Guide to Vacuum Pressure Sintering Furnace: Benefits, Applications, and Working Principle
Discover the benefits, applications, and working principle of vacuum pressure sintering furnace. Learn how vacuum sintering produces clean, bright parts with incredible design flexibility and quick turnaround, and its applications in teaching, scientific research, and production. Explore the precise setting and monitoring of process parameters, and the advantages of sintering under vacuum and pressure. Find out how vacuum sintering furnace is perfect for higher temperature sintering applications and for sintering extremely reactive materials.
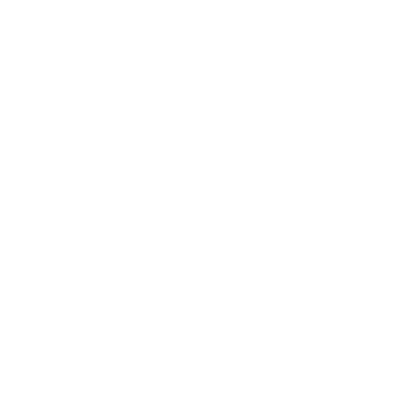
Vacuum Induction Melting Furnace: Principle, Advantages, and Applications
Discover the Vacuum Induction Melting Furnace, a specialized equipment that employs vacuum and induction heating to refine metals and alloys, ensuring high purity and precise composition control. Explore its principle, advantages, applications, and components in this comprehensive guide.
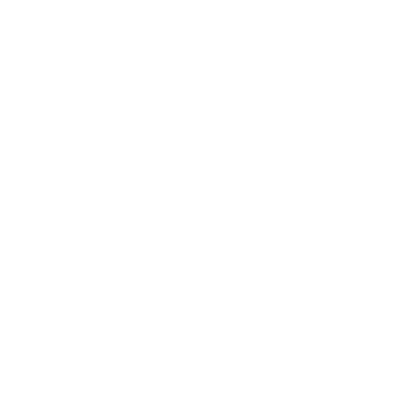
Exploring Tungsten Vacuum Furnaces: Operation, Applications, and Advantages
Discover the operation, applications, and benefits of tungsten vacuum furnaces in laboratory settings. Learn about KinTek's advanced features, control mechanisms, and the use of tungsten in high-temperature environments.
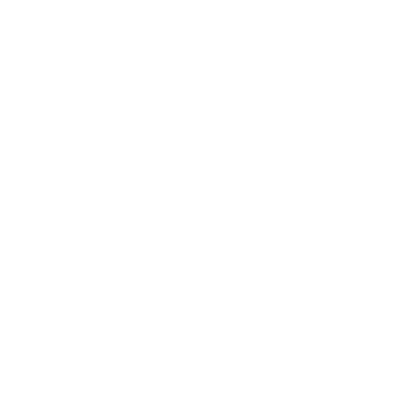
Materials Science with the Lab Vacuum Furnace
A vacuum furnace is a specialized type of furnace that is designed to operate in a vacuum environment. This means that the furnace is sealed and the air inside is pumped out, creating a low pressure or vacuum inside.
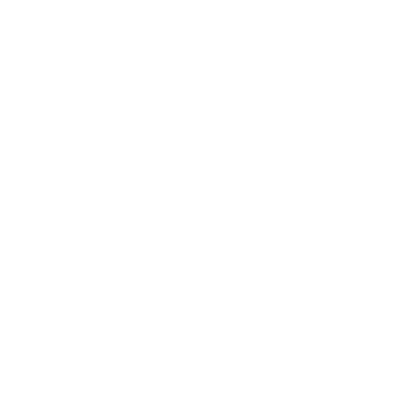
Vacuum Melting Furnace: A Comprehensive Guide to Vacuum Induction Melting
Discover the intricacies of vacuum induction melting furnaces, their components, operation, advantages, and applications. Explore how these furnaces revolutionize metal processing and achieve exceptional material properties.
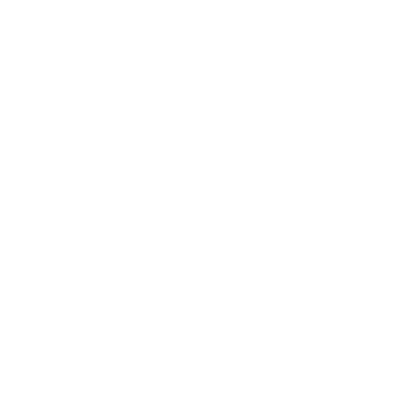
Vacuum Laboratory Furnaces in Advanced Materials Research
In addition to size, there are several other key differences between industrial-scale and laboratory vacuum furnaces
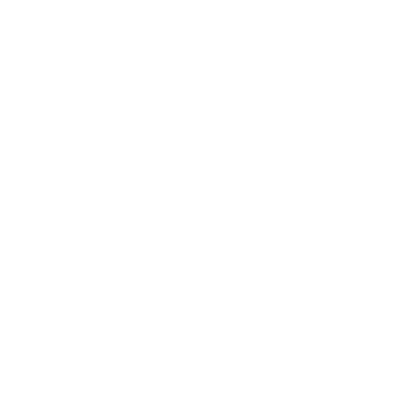
Molybdenum Vacuum Furnace: High-Temperature Sintering and Heat Treatment
Explore the advanced features and applications of molybdenum vacuum furnaces in high-temperature sintering and heat treatment. Learn about their construction, control systems, and maintenance tips.
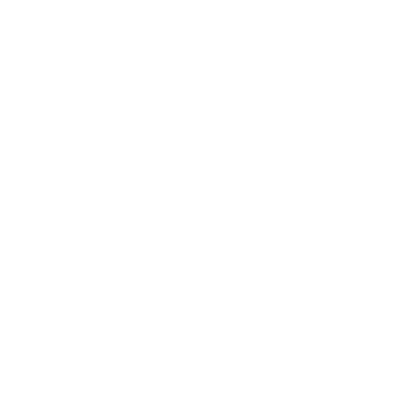
Maximizing Efficiency and Precision with Vacuum Graphite Furnaces
Discover how vacuum graphite furnaces revolutionize high-temperature material treatments with unmatched precision and efficiency. Explore customized solutions for various industries, advanced automation, and sustainable energy practices.
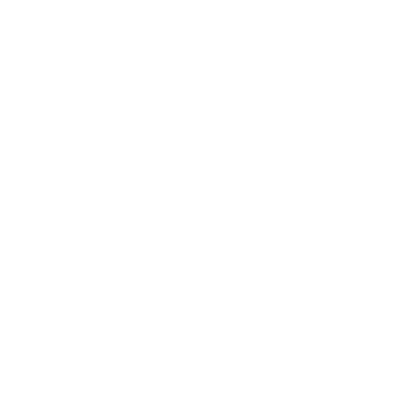
An In-depth Analysis of Hot Pressing Technology and Its Applications
Hot pressing is a high-pressure, low-strain-rate powder metallurgy process used to form powder or powder compact at high temperatures to induce sintering and creep processes. It involves the simultaneous application of heat and pressure to fabricate hard and brittle materials.
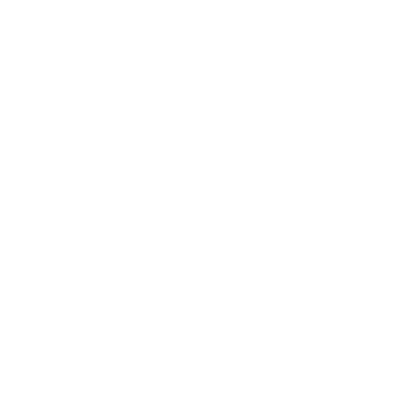
Unveiling Vacuum Graphite Furnaces: Performance, Applications, and Expert Insights
Delve into the world of vacuum graphite furnaces, exploring their exceptional performance, diverse applications, and crucial considerations. Our expert insights empower you to make informed decisions for your laboratory's high-temperature material treatment needs.