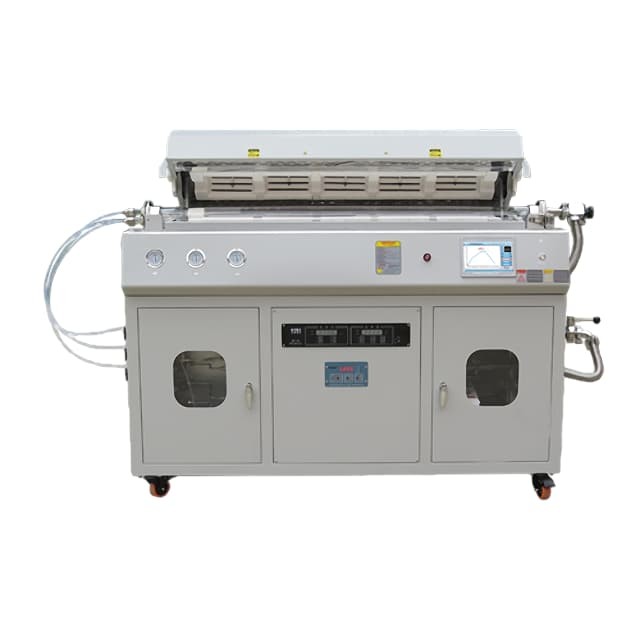
CVD & PECVD Furnace
Multi Heating Zones CVD Tube Furnace Machine Chemical Vapor Deposition Chamber System Equipment
Item Number : KT-CTF14
Price varies based on specs and customizations
- Max. temperature
- 1400 ℃
- Constant work temperature
- 1300 ℃
- Furnace tube diameter
- 60 mm
- Heating zone
- 2x450 mm
- Heating rate
- 0-10 ℃/min
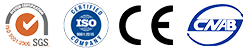
Shipping:
Contact us to get shipping details Enjoy On-time Dispatch Guarantee.
Why Choose Us
Reliable PartnerEasy ordering process, quality products, and dedicated support for your business success.
Introduction
A multi-zone CVD tube furnace is a type of laboratory equipment used for chemical vapor deposition (CVD). CVD is a process in which a thin film is deposited on a substrate by the chemical reaction of a gas or vapor. Multi-zone CVD tube furnaces have multiple heating zones, which allow for precise control of the temperature profile within the furnace. This is important for many CVD processes, as the temperature can affect the properties of the deposited film.
Multi-zone CVD tube furnaces are typically used for research and development purposes, but they can also be used in production applications. They are available in a variety of sizes and configurations, and can be customized to meet the specific requirements of a particular application.
Applications
Multi Heating Zones CVD Tube Furnace CVD Machine is widely used in various fields, including:
- Chemical vapor deposition (CVD): Growth of thin films for electronic devices, semiconductors, and solar cells
- Diffusion: Doping of semiconductors and metals
- Annealing: Heat treatment of materials to improve their properties
- Sintering: Bonding of materials through heat and pressure
- Thermo-treatments: Controlled heating and cooling of materials for various purposes
Detail & Parts
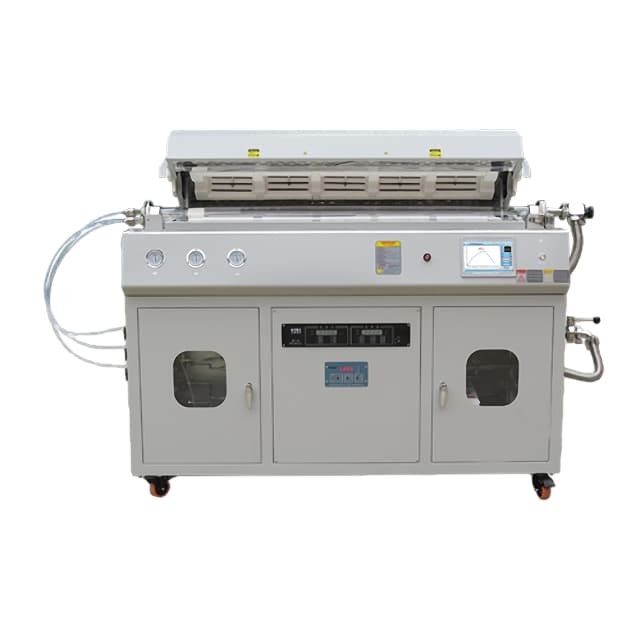
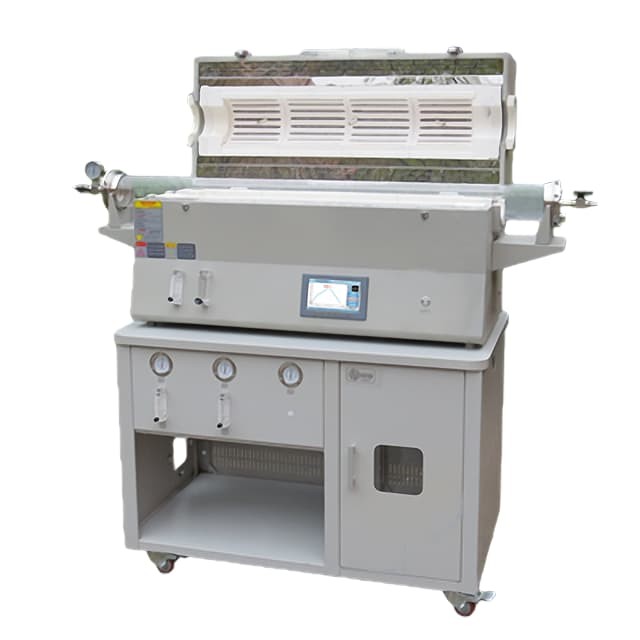
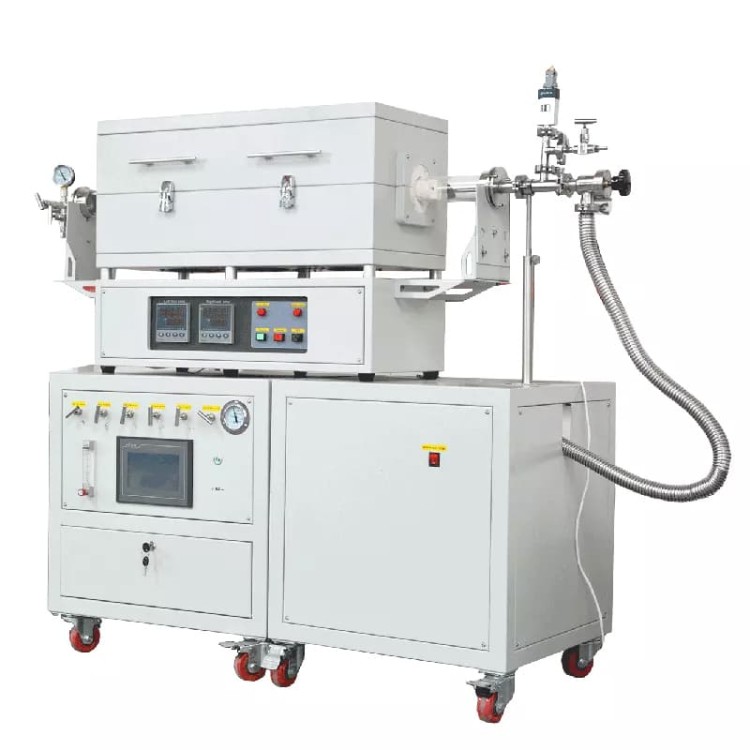
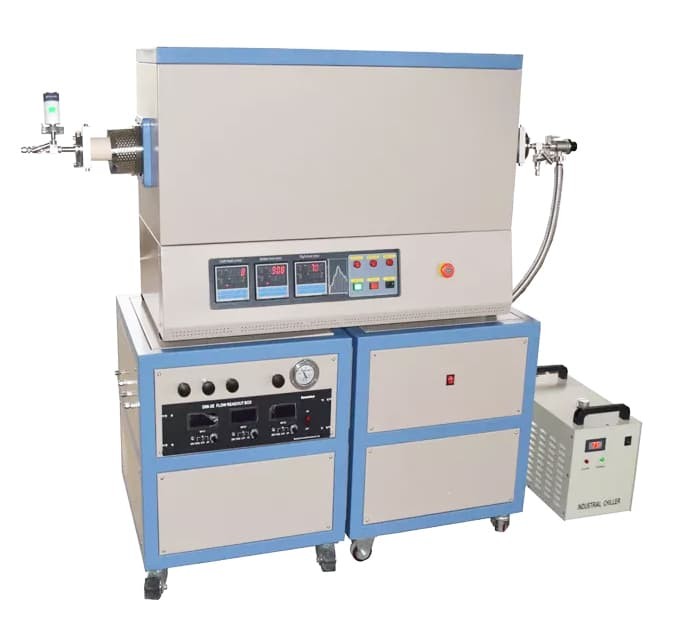
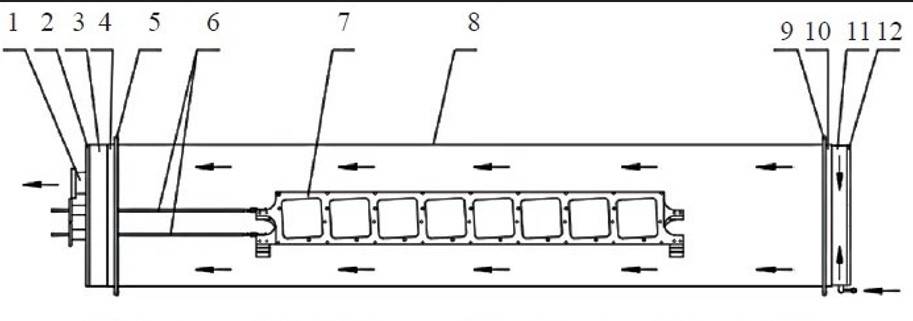
Schematic diagram of the typical reaction chamber structure of tubular PECVD equipment 1. Exhaust hole;2. Tail end flange;3. Tail water cooling flange;4. Tail sealing flange;5. Tail fixing flange;6. Electrode rod;7. Graphite boat;8. Quartz furnace tube;9. Front fixing flange;10. Front water cooling flange;11. Front air inlet flange;12. Furnace door
Principle
The Multi Heating Zones CVD Tube Furnace CVD Machine utilizes chemical vapor deposition (CVD) to deposit thin films onto substrates. CVD is a process that involves the reaction of gaseous precursors to form a solid film material. In the case of this furnace, the gaseous precursors are typically metal-organic compounds and/or hydrides, which are introduced into the furnace chamber and react with each other to form the desired film material. The furnace is equipped with multiple heating zones, which allow for precise control of the deposition temperature and temperature gradient. This enables the deposition of high-quality films with tailored properties, such as thickness, composition, and crystallinity. The furnace also features a vacuum system that allows for the removal of impurities and the control of the deposition pressure.
Features
Multi-Zone CVD Tube Furnaces offer a wide range of benefits for users, including:
- Independent heating zones: This allows for the creation of longer constant temperature fields, as well as controlled temperature gradients. This is ideal for applications where precise temperature control is critical.
- PID programmable temperature control: This provides excellent control accuracy and supports remote control and centralized control. This makes it easy to monitor and adjust the temperature of the furnace from anywhere.
- High accuracy MFC mass flowmeter control: This ensures a stable gas supply speed. This is important for applications where the precise control of gas flow is critical.
- Stainless steel vacuum flange with various adapting port: This provides good sealing and a high vacuum degree. This is ideal for applications where a high vacuum is required.
- KT-CTF14 Pro applies one 7 inches TFT touch screen controller: This makes it easy to set programs and analyze history data. This is ideal for applications where user-friendly operation is important.
Advantages
- Independent heating zones: Create a longer constant temperature field and a controlled temperature gradient.
- PID programmable temperature control: Excellent control accuracy, remote and centralized control support.
- High accuracy MFC mass flowmeter control:Source gases premixing and stable gas supply speed.
- Stainless steel vacuum flange: Various adapting ports for different vacuum pump station setups, good sealing, and high vacuum degree.
- KT-CTF14 Pro controller: 7-inch TFT touch screen, user-friendly program setting, and history data analysis.
- Multi-purpose: CVD, diffusion, and other thermo-treatments under vacuum status and atmosphere protection.
- Energy-saving: Ceramic fiber material and double-layer structure reduce external temperature.
- Long temperature zone: Easy to operate.
- Reliable sealing: High comprehensive performance index.
- Material options: Furnace tube available in heat-resistant steel, quartz glass, and ceramic.
- Wide applications: Element analysis and determination, small steel pieces quenching, annealing, tempering, electronic ceramics, and other new materials.
Technical specifications
Furnace model | KT-CTF14-60 |
---|---|
Max. temperature | 1400℃ |
Constant work temperature | 1300℃ |
Furnace tube material | High purity Al2O3 tube |
Furnace tube diameter | 60mm |
Heating zone | 2x450mm |
Chamber material | Alumina polycrystalline fiber |
Heating element | Silicon Carbide |
Heating rate | 0-10℃/min |
Thermal couple | S type |
Temperature controller | Digital PID controller/Touch screen PID controller |
Temperature control accuracy | ±1℃ |
Gas precise control unit | |
Flow meter | MFC mass flow meter |
Gas channels | 4 channels |
Flow rate | MFC1: 0-5SCCM O2 MFC2: 0-20SCMCH4 MFC3: 0- 100SCCM H2 MFC4: 0-500 SCCM N2 |
Linearity | ±0.5% F.S. |
Repeatability | ±0.2% F.S. |
Pipe line and valve | Stainless steel |
Maximum Operating Pressure | 0.45MPa |
Flow meter controller | Digital Knob controller/Touch screen controller |
Standard vacuum unit(Optional) | |
Vacuum pump | Rotary vane vacuum pump |
Pump flow rate | 4L/S |
Vacuum suction port | KF25 |
Vacuum gauge | Pirani/Resistance silicon vacuum gauge |
Rated vacuum pressure | 10Pa |
High vacuum unit(Optional) | |
Vacuum pump | Rotary vane pump+Molecular pump |
Pump flow rate | 4L/S+110L/S |
Vacuum suction port | KF25 |
Vacuum gauge | Compound vacuum gauge |
Rated vacuum pressure | 6x10-5Pa |
Above specifications and setups can be customized |
Standard Package
No. | Description | Quantity |
---|---|---|
1 | Furnace | 1 |
2 | Quartz tube | 1 |
3 | Vacuum flange | 2 |
4 | Tube thermal block | 2 |
5 | Tube thermal block hook | 1 |
6 | Heat resistant glove | 1 |
7 | Precise gas control | 1 |
8 | Vacuum unit | 1 |
9 | Operation manual | 1 |
Optional Setup
- In tube gases detecting and monitoring,like H2, O2 and so on
- Independent furnace temperature monitoring and recording
- RS 485 communication port for PC remote control and data exporting
- Insert gases feeding flow rate control,like mass flowmeter and float flowmeter
- Touch screen temperature controller with versatile operator friendly functions
- High vacuum pump station setups, like vane vacuum pump,molecular pump,diffusion pump
Warnings
Operator safety is the top important issue! Please operate the equipment with cautions. Working with inflammable& explosive or toxic gases is very dangerous, operators must take all necessary precautions before starting the equipment. Working with positive pressure inside the reactors or chambers is dangerous, operator must fellow the safety procedures strictly. Extra caution must also be taken when operating with air-reactive materials, especially under vacuum. A leak can draw air into the apparatus and cause a violent reaction to occur.
Designed for You
KinTek provide deep custom made service and equipment to worldwide customers, our specialized teamwork and rich experienced engineers are capable to undertake the custom tailoring hardware and software equipment requirements, and help our customer to build up the exclusive and personalized equipment and solution!
Would you please drop your ideas to us, our engineers are ready for you now!
FAQ
What Is CVD Furnace?
Chemical vapor deposition (CVD) is a technology that uses various energy sources such as heating, plasma excitation or light radiation to chemically react gaseous or vapor chemical substances on the gas phase or gas-solid interface to form solid deposits in the reactor by means of chemical reaction.To put it simply, two or more gaseous raw materials are introduced into a reaction chamber, and then they react with each other to form a new material and deposit it on the substrate surface.
CVD furnace is one combined furnace system with high temperature tube furnace unit,gases control unit, and vacuum unit, it is widely used for experiment and production of composite material preparation, microelectronics process, semiconductor optoelectronic, solar energy utilization, optical fiber communication, superconductor technology, protective coating field.
What Is A Tube Furnace?
Laboratory tube furnace is one classic external heating high temperature tube furnace, also named hot wall heating furnace.
According to the different working temperature, furnace tube material usually can be transparent quartz tubes, high purity alumina ceramic tubes and high strength metal alloy tubes.
To meet different thermal researching purposes, tube furnace can be designed with multi heating zones, so as to have a flexible control of temperature gradient in the tube working chamber; furnace tube can work with a controlled atmosphere working environment or a high vacuum working environment.
How Does CVD Furnace Work?
CVD furnace system consists of high temperature tube furnace unit, reacting gas source precise control unit, vacuum pump station and corresponding assembling parts.
Vacuum pump is to remove the air from the reacting tube,and make sure there is no unwanted gases inside the reaction tube, after that the tube furnace will heat the reaction tube to a target temperature, then reacting gas source precise control unit can introduce different gases with a set ratio into the furnace tube for the chemical reaction, the chemical vapor deposition will be formed in the CVD furnace.
What Is The Basic Principle Of CVD?
How Does A Tube Furnace Work?
Tube furnace heating elements are placed surrounding the cylindrical cavity, furnace can only heat the samples in the cylindrical cavity through indirect thermal radiation, since furnace tube can prevent sample material from contacting with furnace heating elements and insulation materials, so tube furnace creates a clean isolated heat chamber and reduce risks of the sample material contaminating by the furnace.
Which Gas Is Used In CVD Process?
There are tremendous gas sources can be used in the CVD process, the common chemical reactions of CVD includes Pyrolysis, photolysis, reduction, oxidation, redox,so the gases involved in these chemical reactions can be used in the CVD process.
We take CVD Graphene growth for an example, the gases used in the CVD process will be CH4,H2,O2 and N2.
What Are The Different Types Of CVD Method?
What Is The Application For Tube Furnace?
Tubular furnace is mainly used in metallurgy, glass, heat treatment, lithium anode and cathode materials, new energy, abrasives and other industries, and is a professional equipment for measuring materials under certain temperature conditions.
Tube furnace features simple structure, easy operation, easy control and continuous production.
Tube furnace is also widely applied in the CVD (chemical vapor deposition) and plasma enhanced CVD systems.
What Is The Advantage Of CVD System?
- Wide range of films can be produced, metal film, nonmetal film and multi-component alloy film as required. At the same time, it can prepare high-quality crystals that are difficult to obtain by other methods, such as GaN, BP, etc.
- The film forming speed is fast, usually several microns per minute or even hundreds of microns per minute. It is possible to simultaneously deposit large quantities of coatings with uniform composition, which is incomparable to other film preparation methods, such as liquid phase epitaxy (LPE) and molecular beam epitaxy (MBE).
- The working conditions are carried out under normal pressure or low vacuum conditions, so the coating has good diffraction, and the workpieces with complex shapes can be uniformly coated, which is much superior to PVD.
- Due to the mutual diffusion of reaction gas, reaction product and substrate, a coating with good adhesion strength can be obtained, which is crucial for preparing surface strengthened films such as wear-resistant and anti-corrosion films.
- Some films grow at a temperature far lower than the melting point of the film material. Under the condition of low temperature growth, the reaction gas and reactor wall and impurities contained in them almost do not react, so a film with high purity and good crystallinity can be obtained.
- Chemical vapor deposition can obtain a smooth deposition surface. This is because compared with LPE, chemical vapor deposition (CVD) is carried out under high saturation, with high nucleation rate, high nucleation density, and uniform distribution on the whole plane, resulting in a macroscopic smooth surface. At the same time, in chemical vapor deposition, the average free path of molecules (atoms) is much larger than LPE, so the spatial distribution of molecules is more uniform, which is conducive to the formation of a smooth deposition surface.
- Low radiation damage, which is a necessary condition for manufacturing metal oxide semiconductors (MOS) and other devices
What Are The Advantages Of Using Chemical Vapor Deposition Machines?
How Many Different Types Tube Furnace?
Tube furnace can work with different mechanical functions smoothly, so there are many different types tube furnace variations for different experiment purposes, typical furnace furnaces are as below:
- Horizontal tube furnace
- Vertical tube furnace
- Split tube furnace
- Rotary tube furnace
- Tilting tube furnace
- Sliding tube furnace
- Fast heating and cooling tube furnace
- Continuous feeding and discharging tube furnace
What Does PECVD Stand For?
PECVD is a technology that uses plasma to activate reaction gas, promote chemical reaction on the surface of substrate or near surface space, and generate solid film. The basic principle of plasma chemical vapor deposition technology is that under the action of RF or DC electric field, the source gas is ionized to form a plasma, the low-temperature plasma is used as the energy source, an appropriate amount of reaction gas is introduced, and the plasma discharge is used to activate the reaction gas and realize chemical vapor deposition.
According to the method of generating plasma, it can be divided into RF plasma, DC plasma and microwave plasma CVD, etc...
What Are The Applications Of Chemical Vapor Deposition Machines?
What Are The Advantages Of Using A Tube Furnace?
What Is The Difference Between CVD And PECVD?
The difference between PECVD and traditional CVD technology is that the plasma contains a large number of high-energy electrons, which can provide the activation energy required in the chemical vapor deposition process, thus changing the energy supply mode of the reaction system. Since the electron temperature in the plasma is as high as 10000K, the collision between electrons and gas molecules can promote the chemical bond breaking and recombination of the reaction gas molecules to generate more active chemical groups, while the whole reaction system maintains a lower temperature.
So compared to the CVD process, PECVD can carry out the same chemical vapor deposition process with a lower temperature.
What Factors Should Be Considered When Selecting A Chemical Vapor Deposition Machine?
What Safety Precautions Should Be Taken When Using A Tube Furnace?
Can Chemical Vapor Deposition Machines Be Used For Multi-layered Thin Film Deposition?
4.8
out of
5
KINTEK SOLUTION's CVD tube furnace is a game-changer in our lab. The precise temperature control and uniform heating ensure consistent results every time.
4.7
out of
5
The CVD machine is a highly versatile and reliable equipment. The multi-zone heating allows us to create various temperature profiles, making it suitable for a wide range of experiments.
4.9
out of
5
The speed of delivery was impressive. We received the furnace within a week of placing the order, allowing us to start our experiments promptly.
4.8
out of
5
The value for money is exceptional. KINTEK SOLUTION provides high-quality equipment at a reasonable price, making it an excellent choice for labs with budget constraints.
4.7
out of
5
The after-sales service is top-notch. The KINTEK SOLUTION team is always responsive and provides prompt support, ensuring our lab's smooth operation.
4.9
out of
5
The durability of the CVD tube furnace is remarkable. We have been using it extensively for over a year, and it continues to perform flawlessly, delivering consistent results.
4.8
out of
5
The technological advancement of this CVD machine is truly impressive. The multi-zone heating, precise temperature control, and user-friendly interface make it an invaluable asset to our lab.
4.7
out of
5
The CVD tube furnace has significantly improved the efficiency of our research. The fast heating and cooling rates allow us to conduct experiments more quickly, saving valuable time.
4.9
out of
5
The CVD machine from KINTEK SOLUTION is a reliable workhorse in our lab. It operates smoothly, providing consistent and accurate results, which are crucial for our research.
Products
Multi Heating Zones CVD Tube Furnace Machine Chemical Vapor Deposition Chamber System Equipment
REQUEST A QUOTE
Our professional team will reply to you within one business day. Please feel free to contact us!
Related Products
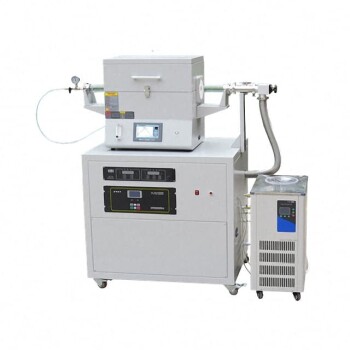
Efficient split chamber CVD furnace with vacuum station for intuitive sample checking and quick cooling. Up to 1200℃ max temperature with accurate MFC mass flowmeter control.
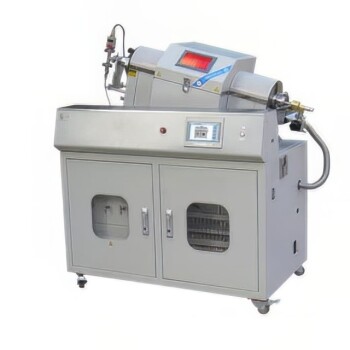
Inclined Rotary Plasma Enhanced Chemical Vapor Deposition PECVD Equipment Tube Furnace Machine
Introducing our inclined rotary PECVD furnace for precise thin film deposition. Enjoy automatic matching source, PID programmable temperature control, and high accuracy MFC mass flowmeter control. Built-in safety features for peace of mind.
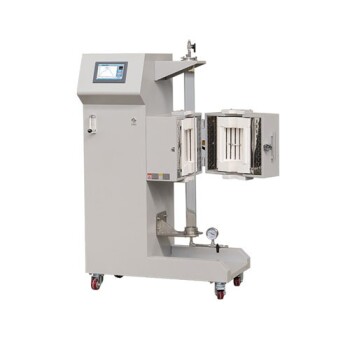
Vertical Laboratory Quartz Tube Furnace Tubular Furnace
Elevate your experiments with our Vertical Tube Furnace. Versatile design allows for operation under various environments and heat treatment applications. Order now for precise results!
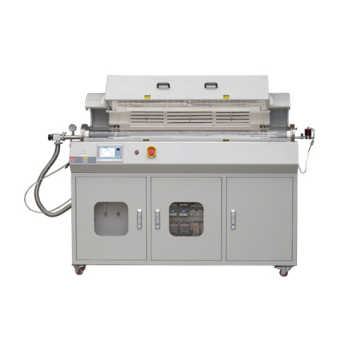
Rotary Tube Furnace Split Multi Heating Zone Rotating Tube Furnace
Multi zone rotary furnace for high-precision temperature control with 2-8 independent heating zones. Ideal for lithium ion battery electrode materials and high-temperature reactions. Can work under vacuum and controlled atmosphere.
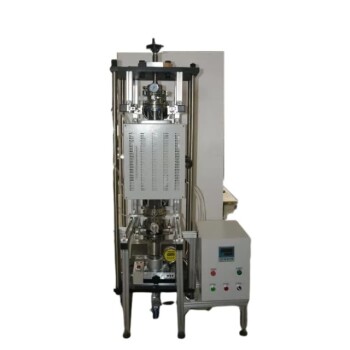
Vacuum Hot Press Furnace Heated Vacuum Press Machine Tube Furnace
Reduce forming pressure & shorten sintering time with Vacuum Tube Hot Press Furnace for high-density, fine-grain materials. Ideal for refractory metals.
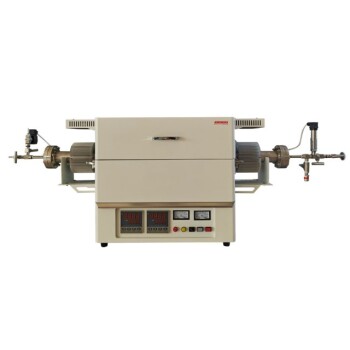
High Pressure Laboratory Vacuum Tube Furnace Quartz Tubular Furnace
KT-PTF High Pressure Tube Furnace: Compact split tube furnace with strong positive pressure resistance. Working temp up to 1100°C and pressure up to 15Mpa. Also works under controller atmosphere or high vacuum.
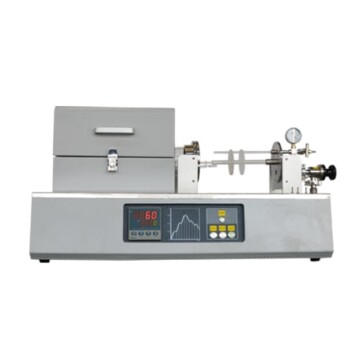
Laboratory Quartz Tube Furnace Tubular RTP Heating Furnace
Get lightning-fast heating with our RTP Rapid Heating Tube Furnace. Designed for precise, high-speed heating and cooling with convenient sliding rail and TFT touch screen controller. Order now for ideal thermal processing!
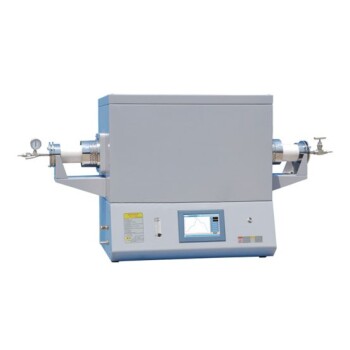
1700℃ Laboratory Quartz Tube Furnace with Alumina Tube Tubular Furnace
Looking for a high-temperature tube furnace? Check out our 1700℃ Tube Furnace with Alumina Tube. Perfect for research and industrial applications up to 1700C.
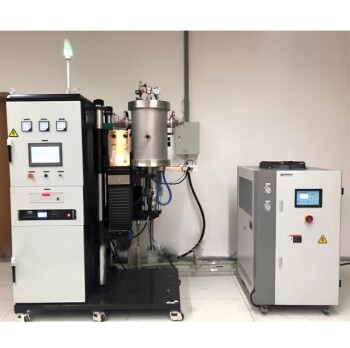
Vacuum Heat Treat and Molybdenum Wire Sintering Furnace for Vacuum Sintering
A vacuum molybdenum wire sintering furnace is a vertical or bedroom structure, which is suitable for withdrawal, brazing, sintering and degassing of metal materials under high vacuum and high temperature conditions. It is also suitable for dehydroxylation treatment of quartz materials.
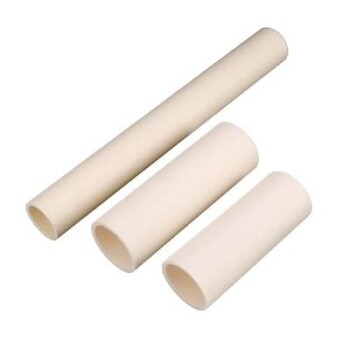
High Temperature Alumina (Al2O3) Furnace Tube for Engineering Advanced Fine Ceramics
High temperature alumina furnace tube combines the advantages of high hardness of alumina, good chemical inertness and steel, and has excellent wear resistance, thermal shock resistance and mechanical shock resistance.
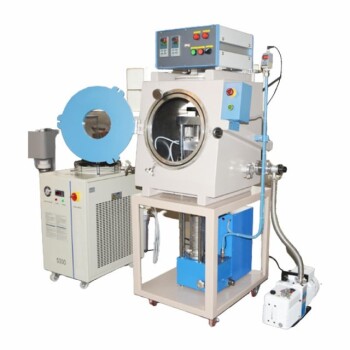
Vacuum Hot Press Furnace Machine for Lamination and Heating
Experience clean and precise lamination with Vacuum Lamination Press. Perfect for wafer bonding, thin-film transformations, and LCP lamination. Order now!
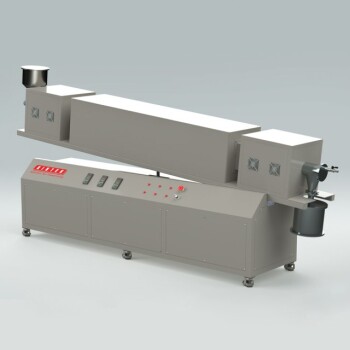
Vacuum Sealed Continuous Working Rotary Tube Furnace Rotating Tube Furnace
Experience efficient material processing with our vacuum-sealed rotary tube furnace. Perfect for experiments or industrial production, equipped with optional features for controlled feeding and optimized results. Order now.
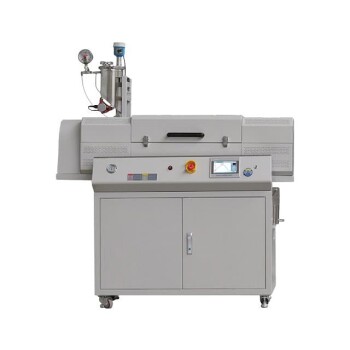
Laboratory Vacuum Tilt Rotary Tube Furnace Rotating Tube Furnace
Discover the versatility of Laboratory Rotary Furnace: Ideal for calcination, drying, sintering, and high-temperature reactions. Adjustable rotating and tilting functions for optimal heating. Suitable for vacuum and controlled atmosphere environments. Learn more now!
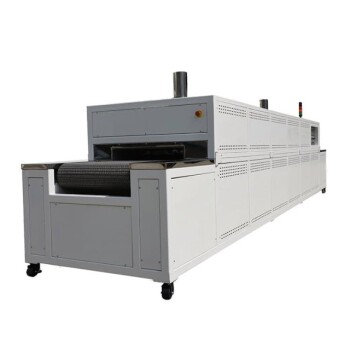
Mesh belt controlled atmosphere furnace
Discover our KT-MB mesh belt sintering furnace - perfect for high-temperature sintering of electronic components & glass insulators. Available for open air or controlled atmosphere environments.
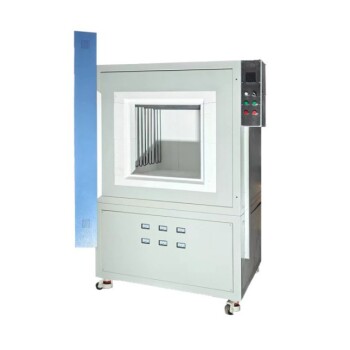
High Temperature Muffle Oven Furnace for Laboratory Debinding and Pre Sintering
KT-MD High temperature debinding and pre-sintering furnace for ceramic materials with various molding processes. Ideal for electronic components such as MLCC and NFC.
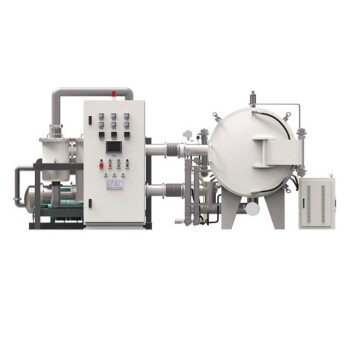
Horizontal High Temperature Graphite Vacuum Graphitization Furnace
Horizontal Graphitization Furnace: This type of furnace is designed with the heating elements placed horizontally, allowing for uniform heating of the sample. It's well-suited for graphitizing large or bulky samples that require precise temperature control and uniformity.
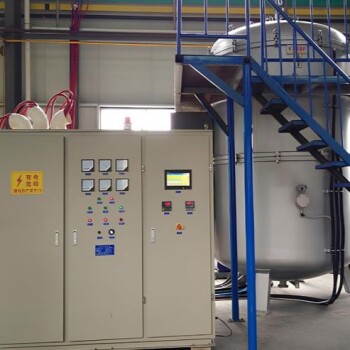
Large Vertical Graphite Vacuum Graphitization Furnace
A large vertical high-temperature graphitization furnace is a type of industrial furnace used for the graphitization of carbon materials, such as carbon fiber and carbon black. It is a high-temperature furnace that can reach temperatures of up to 3100°C.
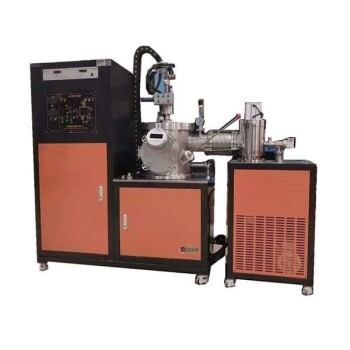
Vacuum Arc Induction Melting Furnace
Discover the power of Vacuum Arc Furnace for melting active & refractory metals. High-speed, remarkable degassing effect, and free of contamination. Learn more now!
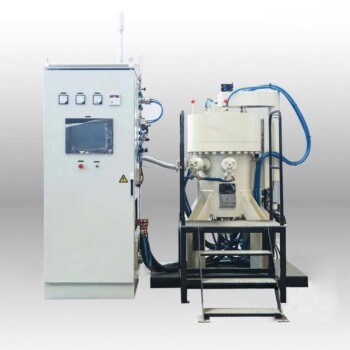
Vacuum Heat Treat and Sintering Furnace with 9MPa Air Pressure
The air pressure sintering furnace is a high-tech equipment commonly used for the sintering of advanced ceramic materials. It combines vacuum sintering and pressure sintering techniques to achieve high-density and high-strength ceramics.
Related Articles
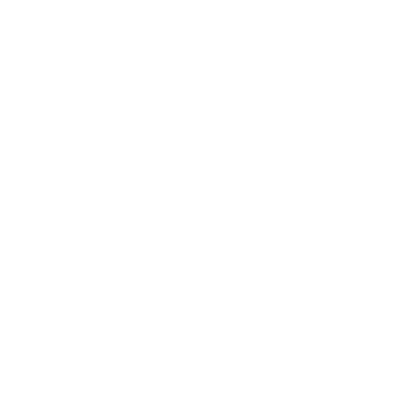
CVD furnace for the growth of carbon nanotubes
Chemical vapor deposition (CVD) furnace technology is a widely used method for growing carbon nanotubes.
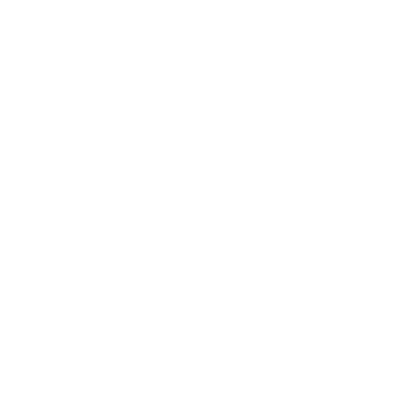
Advantages of Using CVD Tube Furnace for Coating
CVD coatings have several advantages over other coating methods, such as high purity, density, and uniformity, making them ideal for many applications in various industries.
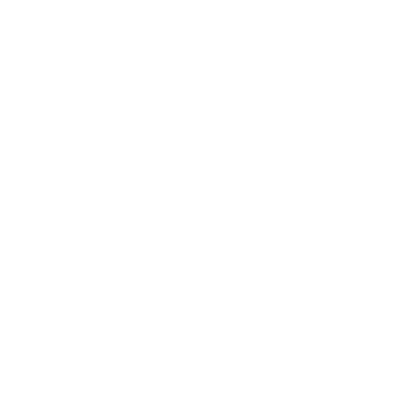
Introducing the Lab Vacuum Tube Furnaces
A vacuum tube furnace is a type of furnace that uses vacuum to isolate the process atmosphere from the external atmosphere.
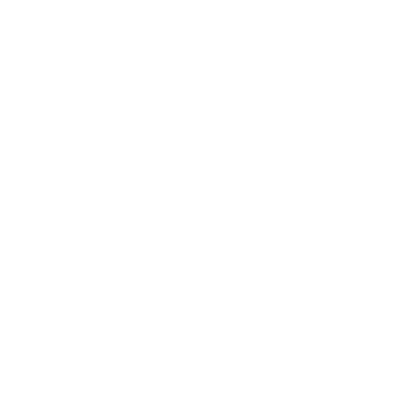
Exploring Tungsten Vacuum Furnaces: Operation, Applications, and Advantages
Discover the operation, applications, and benefits of tungsten vacuum furnaces in laboratory settings. Learn about KinTek's advanced features, control mechanisms, and the use of tungsten in high-temperature environments.
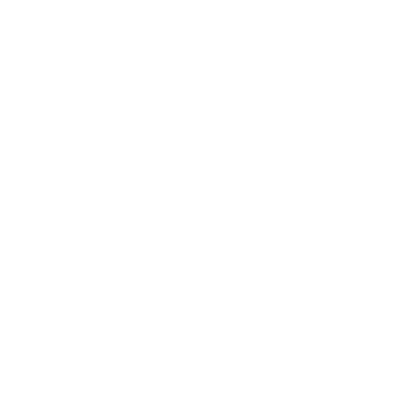
Exploring the Key Characteristics of Tube Heating Furnaces
A tube heating furnace is a specialized type of industrial furnace that is used in various industries to heat substances through the use of fuel combustion.
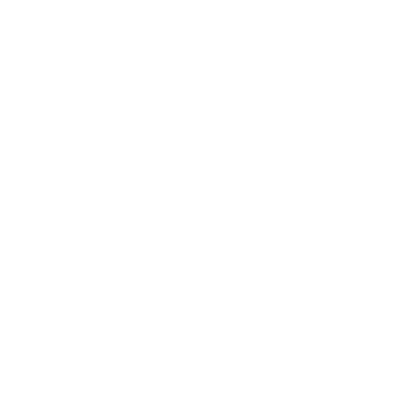
PECVD Furnace A Low-Power and Low-Temperature Solution for Soft Matter
PECVD (Plasma Enhanced Chemical Vapor Deposition) furnaces have become a popular solution for the deposition of thin films on soft matter surfaces.
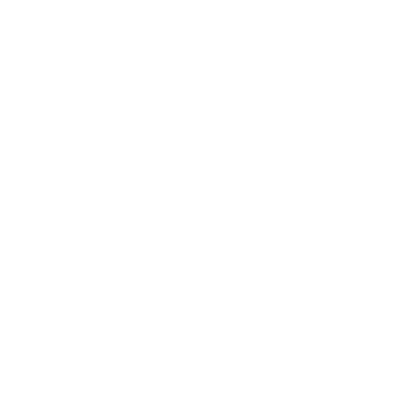
The Versatility of Tube Furnaces: A Guide to Their Applications and Benefits
A laboratory tube furnace is a specialized heating device used in scientific and industrial labs for a variety of applications.
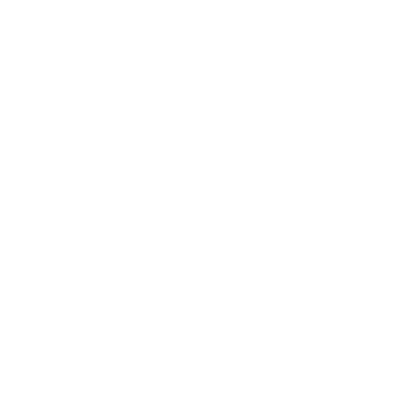
Comprehensive Guide to Tube Furnaces: Types, Applications, and Considerations
Delve into the realm of tube furnaces, exploring their types, diverse applications in industries and laboratories, and crucial factors to consider for optimal usage.
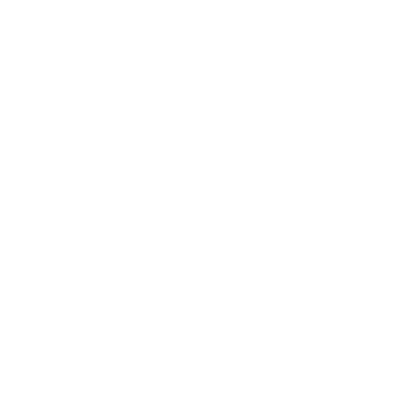
Exploring Rotary Tube Furnaces: A Comprehensive Guide
Discover the workings of rotary tube furnaces, their diverse applications, and key advantages. Explore how these furnaces operate, their suitability for different processes, and factors to consider when selecting one. Find out why rotary tube furnaces are favored in advanced materials processing.
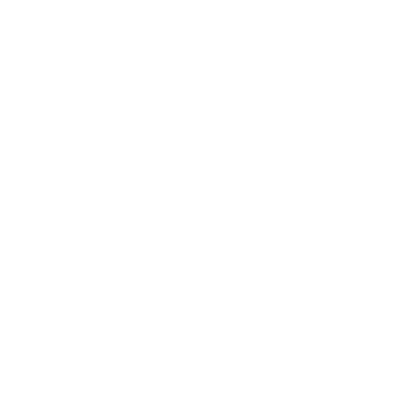
CVD Machines for Thin Film Deposition
Chemical Vapor Deposition (CVD) is a widely used technique for deposition of thin films on various substrates.
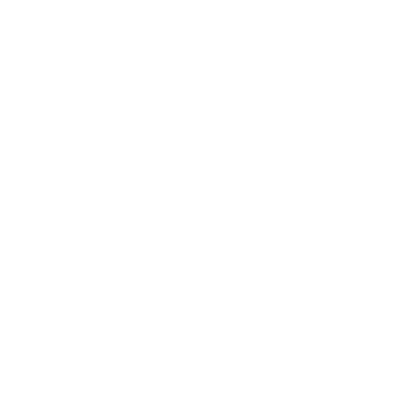
A Comprehensive Guide to Split Tube Furnaces: Applications, Features
It is accurate that a split tube furnace is a type of laboratory equipment that consists of a hollow tube or chamber that can be opened to allow for the insertion and removal of samples or materials being heated.
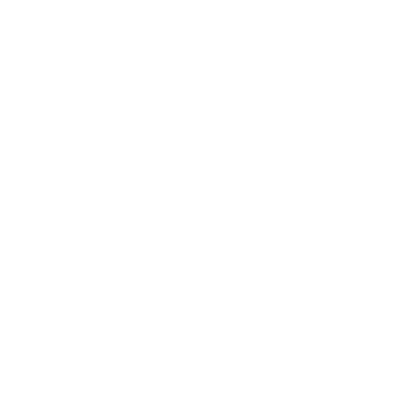
Exploring the Benefits and Applications of Rotary Furnaces: A Comprehensive Guide
Rotary tube furnaces are highly versatile tools that can be used for a wide range of physicochemical processing applications in the laboratory.