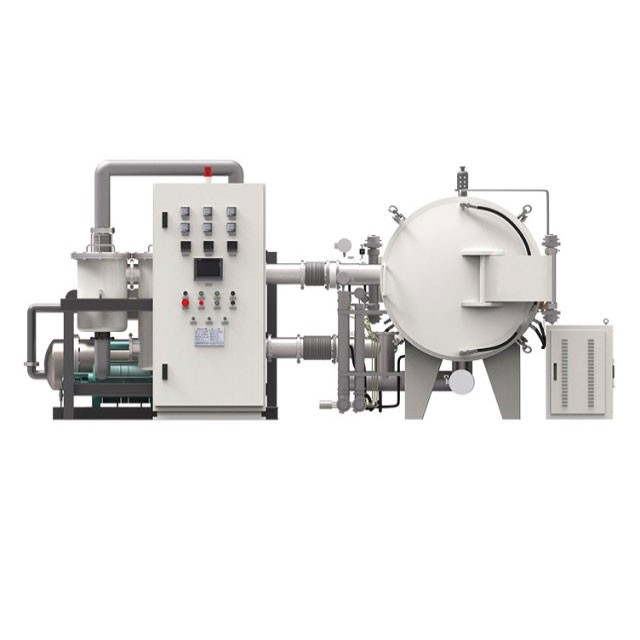
Graphitization furnace
Horizontal High Temperature Graphite Vacuum Graphitization Furnace
Item Number : GF-01
Price varies based on specs and customizations
- Volume(L)
- 192 / 350 / 484
- Rated temperature(℃)
- 2800
- Limit temperature(℃)
- 3100
- Effective heating area (mm)
- 400*400*1200 / 500*500*1400 / 550*550*1600
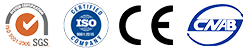
Shipping:
Contact us to get shipping details Enjoy On-time Dispatch Guarantee.
Why Choose Us
Reliable PartnerEasy ordering process, quality products, and dedicated support for your business success.
Introduction
A graphitization furnace is a key piece of equipment used in the production of carbon products and materials. It is employed for graphitization experiments and the production of various carbon materials at temperatures up to 3100°C. The furnace excels in graphitization of carbon materials and stereotyped graphitization of carbon fiber filaments. It can be configured with multiple electric furnaces to accommodate different sintering process times, allowing for continuous operation through alternating power supply and cooling.
Applications
The graphitization furnace is widely used in various industries for high-temperature treatment and graphitization processes. Here are some of its main application areas:
-
Metallurgy: In the metallurgy industry, graphitization furnaces are employed for the production of graphite electrodes, which are essential components in electric arc furnaces used for steelmaking. The high temperatures achieved in the furnace enable the conversion of carbonaceous materials into high-purity graphite, ensuring the desired electrical conductivity and thermal stability required for electrode applications.
-
Electronics: In the electronics industry, graphitization furnaces are crucial for the production of graphite crucibles, which are widely used in the manufacturing of semiconductors and other electronic components. The high-temperature environment within the furnace allows for the formation of pure and dense graphite crucibles with excellent thermal properties, chemical resistance, and high-temperature stability, making them ideal for handling molten materials and performing various high-temperature processes.
-
Aerospace: In the aerospace industry, graphitization furnaces are utilized for the production of graphite composites, which are lightweight and possess exceptional strength and thermal resistance. These composites find applications in the construction of aircraft and spacecraft components, such as rocket nozzles, heat shields, and leading edges, where they can withstand extreme temperatures and harsh environments encountered during high-speed flight.
-
Other Industries: In addition to the aforementioned industries, graphitization furnaces are also employed in a variety of other sectors, including:
- Chemical Industry: Production of carbon black, activated carbon, and other carbon-based chemicals.
- Energy Industry: Manufacturing of carbon fibers for use in batteries, fuel cells, and other energy storage devices.
- Nuclear Industry: Treatment of nuclear waste and production of nuclear-grade graphite materials.
- Research and Development: Study of high-temperature materials and processes in various fields.
Features
The horizontal graphitization furnace offers numerous advantages that cater to various graphitization needs and provide exceptional performance:
-
Enhanced Temperature Uniformity: Utilizes medium-frequency induction heating for rapid temperature rise and high efficiency. The unique furnace design ensures remarkable temperature uniformity throughout the furnace chamber.
-
Innovative Induction Coil Design: The induction coil's arched structure effectively addresses insulation and load-bearing concerns commonly encountered in horizontal induction furnaces.
-
Exceptional Stability and Energy Efficiency: Double-layer alumina brick insulation material prevents short circuits between carbon felt and coils, ensuring excellent heat insulation and fire resistance. This design minimizes heat loss and contributes to the equipment's stability.
-
Continuous Operation Capability: The system allows for the configuration of multiple electric furnaces with a single power supply. This enables the sequential heating and cooling of individual furnaces, facilitating continuous operation and optimizing production efficiency.
-
Advanced Monitoring and Control System: The furnace incorporates a digital flow monitoring system with individual channel monitoring and protection in the power cabinet. It employs high-performance medium-frequency contactors and a comprehensive PLC water, electricity, gas automatic control, and protection system for enhanced safety and reliability.
Principle
The Graphitization furnace employs the principle of medium frequency induction heating to rapidly raise the temperature, ensuring high efficiency. Its unique furnace design considerably enhances the temperature uniformity within the furnace body.
Advantages
- Rapid heating and high efficiency: Utilizes medium frequency induction heating for quick temperature rise and enhanced efficiency.
- Uniform furnace temperature: Unique furnace design ensures excellent temperature uniformity throughout the furnace chamber.
- Durable and reliable: Double-layer alumina brick insulation prevents short circuits, offering good heat insulation and fire resistance, resulting in minimal heat loss and stable equipment performance.
- Flexible operation: Supports multiple electric furnaces with a single power supply, allowing continuous operation by powering on and heating or powering off and cooling individual furnaces as needed.
- Comprehensive monitoring and control: Features a digital flow monitoring system with water flow monitoring and protection, high-performance medium frequency contactor, and a PLC-based automatic control and protection system for water, electricity, and gas.
- Versatile applications: Suitable for various high-temperature treatment and graphitization processes, including graphitization experiments, production of carbon materials at temperatures up to 3100°C, and stereotyped graphitization of carbon fiber filaments.
Technical specifications
Product model specifications | GF-01-40×40×120 | GF-01-50×50×140 | GF-01-55×55×160 |
---|---|---|---|
Volume(L) | 192 | 350 | 484 |
Rated temperature(℃) | 2800 | 2800 | 2800 |
Limit temperature(℃) | 3100 | 3100 | 3100 |
Effective heating area (mm) | 400×400×1200 | 500×500×1400 | 550×550×1600 |
Power(KW) | 200 | 350 | 450 |
Frequency(HZ) | 1500 | 1000 | 1000 |
Temperature control method | Adopt Japanese Shima Electric thermostat | ||
Heating method | Induction heating | ||
Vacuum system | Rotary vane vacuum pump (for high vacuum requirements, Roots vacuum pump and oil diffusion pump are required) | ||
Sintering atmosphere | N2, Ar and other gases | ||
Rated power supply voltage (V) | 380 | ||
Rated heating voltage (V) | 750 | ||
Vacuum limit (Pa) | 100 (vacuum cold state) |
FAQ
What Is A Graphitization Furnace?
What Is A Graphite Vacuum Furnace Used For?
What Is A Vacuum Furnace Used For?
What Is A Graphitization Furnace Used For?
What Are The Main Applications Of Graphitization Furnaces?
What Are The Main Types Of Graphite Vacuum Furnaces?
What Is The Process Of A Vacuum Furnace?
What Are The Two Different Types Of Graphitization Furnaces?
What Are The Different Types Of Graphitization Furnaces?
How Does A Graphite Vacuum Furnace Work?
What Gas Is Used In A Vacuum Furnace?
How Does A Graphitization Furnace Work?
What Are The Advantages Of Using A Graphite Vacuum Furnace?
What Is The Heating Element Used In A Vacuum Furnace?
What Are The Advantages Of Using A Graphitization Furnace?
What Temperature Range Can A Graphite Vacuum Furnace Achieve?
What Industries Benefit From Graphite Vacuum Furnaces?
4.9
out of
5
The delivery of the furnace was very prompt, and the customer service was excellent.
4.8
out of
5
The furnace is very well made and durable, and it has been a great investment for our laboratory.
4.7
out of
5
The furnace is very easy to use and maintain, and it has helped us to improve our research efficiency.
4.9
out of
5
The furnace is very versatile and can be used for a variety of applications, which makes it a great value for the money.
4.8
out of
5
The furnace is very technologically advanced, and it has helped us to stay at the forefront of our research.
4.7
out of
5
The furnace is very reliable, and we have never had any problems with it.
4.9
out of
5
The furnace is very efficient, and it has helped us to reduce our energy costs.
4.8
out of
5
The furnace is very safe to use, and it has a number of features that protect the user from harm.
4.7
out of
5
The furnace is very user-friendly, and it is easy to learn how to operate it.
4.9
out of
5
The furnace is very compact, and it does not take up a lot of space in the laboratory.
4.8
out of
5
The furnace is very quiet, and it does not disturb the other researchers in the laboratory.
4.7
out of
5
The furnace is very affordable, and it is a great value for the money.
Products
Horizontal High Temperature Graphite Vacuum Graphitization Furnace
REQUEST A QUOTE
Our professional team will reply to you within one business day. Please feel free to contact us!
Related Products
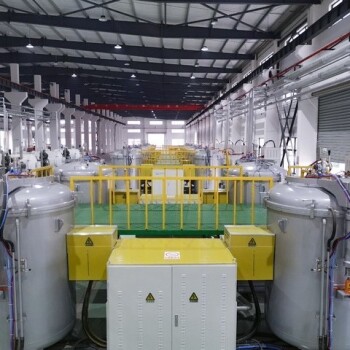
Vertical High Temperature Graphite Vacuum Graphitization Furnace
Vertical high temperature graphitization furnace for carbonization and graphitization of carbon materials up to 3100℃.Suitable for shaped graphitization of carbon fiber filaments and other materials sintered in a carbon environment.Applications in metallurgy, electronics, and aerospace for producing high-quality graphite products like electrodes and crucibles.
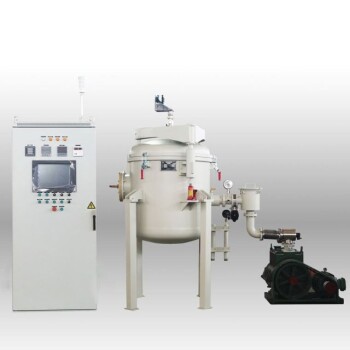
Ultra-High Temperature Graphite Vacuum Graphitization Furnace
The ultra-high temperature graphitization furnace utilizes medium frequency induction heating in a vacuum or inert gas environment. The induction coil generates an alternating magnetic field, inducing eddy currents in the graphite crucible, which heats up and radiates heat to the workpiece, bringing it to the desired temperature. This furnace is primarily used for graphitization and sintering of carbon materials, carbon fiber materials, and other composite materials.
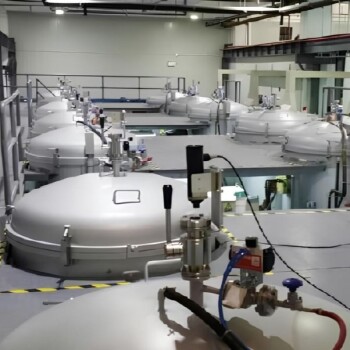
Graphite Vacuum Furnace High Thermal Conductivity Film Graphitization Furnace
The high thermal conductivity film graphitization furnace has uniform temperature, low energy consumption and can operate continuously.

Graphite Vacuum Furnace Bottom Discharge Graphitization Furnace for Carbon Materials
Bottom-out graphitization furnace for carbon materials, ultra-high temperature furnace up to 3100°C, suitable for graphitization and sintering of carbon rods and carbon blocks. Vertical design, bottom discharging, convenient feeding and discharging, high temperature uniformity, low energy consumption, good stability, hydraulic lifting system, convenient loading and unloading.
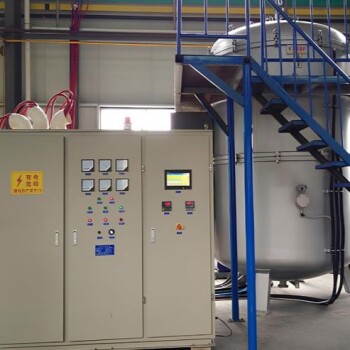
Large Vertical Graphite Vacuum Graphitization Furnace
A large vertical high-temperature graphitization furnace is a type of industrial furnace used for the graphitization of carbon materials, such as carbon fiber and carbon black. It is a high-temperature furnace that can reach temperatures of up to 3100°C.
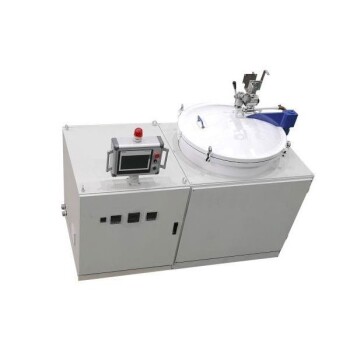
Graphite Vacuum Furnace IGBT Experimental Graphitization Furnace
IGBT experimental graphitization furnace, a tailored solution for universities and research institutions, with high heating efficiency, user-friendliness, and precise temperature control.
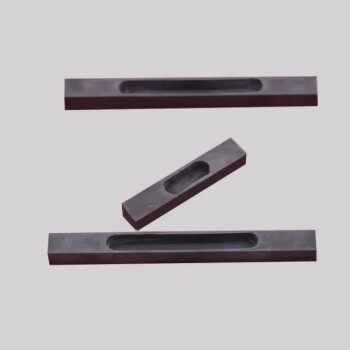
High Purity Pure Graphite Crucible for Evaporation
Vessels for high temperature applications, where materials are kept at extremely high temperatures to evaporate, allowing thin films to be deposited on substrates.
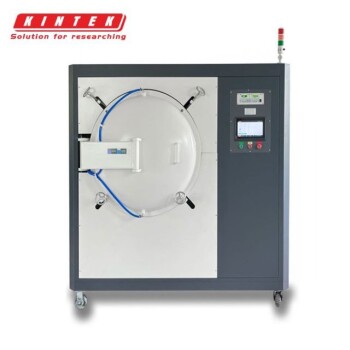
Vacuum Heat Treat Furnace with Ceramic Fiber Liner
Vacuum furnace with polycrystalline ceramic fiber insulation liner for excellent heat insulation and uniform temperature field. Choose from 1200℃ or 1700℃ max. working temperature with high vacuum performance and precise temperature control.
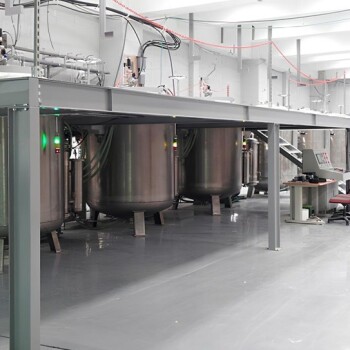
Graphite Vacuum Furnace Negative Material Graphitization Furnace
Graphitization furnace for battery production has uniform temperature and low energy consumption. Graphitization furnace for negative electrode materials: an efficient graphitization solution for battery production and advanced functions to enhance battery performance.
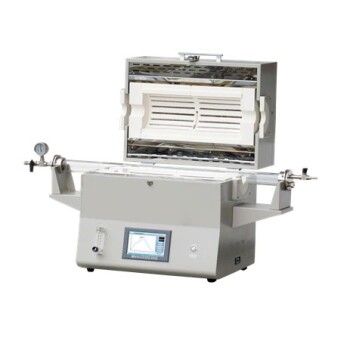
1400℃ Laboratory Quartz Tube Furnace with Alumina Tube Tubular Furnace
Looking for a tube furnace for high-temperature applications? Our 1400℃ Tube Furnace with Alumina Tube is perfect for research and industrial use.
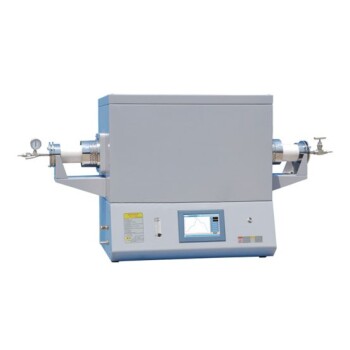
1700℃ Laboratory Quartz Tube Furnace with Alumina Tube Tubular Furnace
Looking for a high-temperature tube furnace? Check out our 1700℃ Tube Furnace with Alumina Tube. Perfect for research and industrial applications up to 1700C.
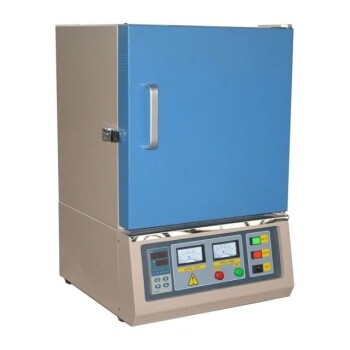
1400℃ Muffle Oven Furnace for Laboratory
Get precise high-temperature control up to 1500℃ with KT-14M Muffle furnace. Equipped with a smart touch screen controller and advanced insulation materials.
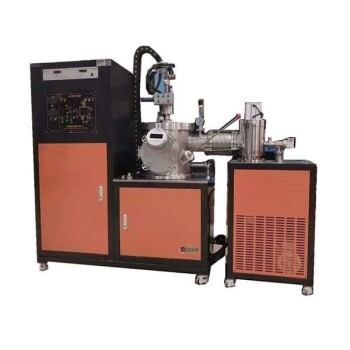
Vacuum Arc Induction Melting Furnace
Discover the power of Vacuum Arc Furnace for melting active & refractory metals. High-speed, remarkable degassing effect, and free of contamination. Learn more now!
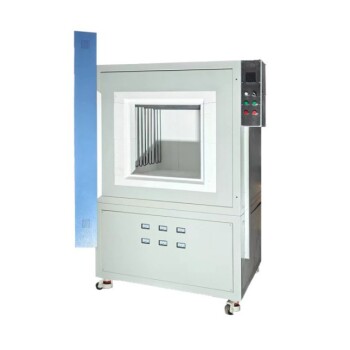
High Temperature Muffle Oven Furnace for Laboratory Debinding and Pre Sintering
KT-MD High temperature debinding and pre-sintering furnace for ceramic materials with various molding processes. Ideal for electronic components such as MLCC and NFC.
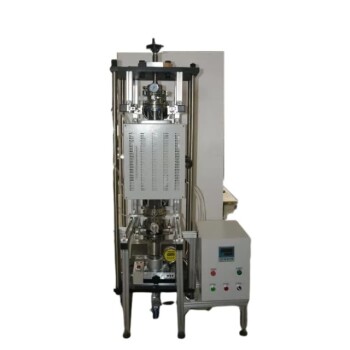
Vacuum Hot Press Furnace Heated Vacuum Press Machine Tube Furnace
Reduce forming pressure & shorten sintering time with Vacuum Tube Hot Press Furnace for high-density, fine-grain materials. Ideal for refractory metals.
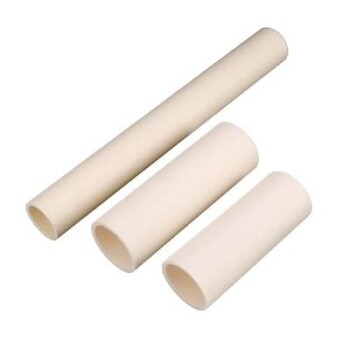
High Temperature Alumina (Al2O3) Furnace Tube for Engineering Advanced Fine Ceramics
High temperature alumina furnace tube combines the advantages of high hardness of alumina, good chemical inertness and steel, and has excellent wear resistance, thermal shock resistance and mechanical shock resistance.
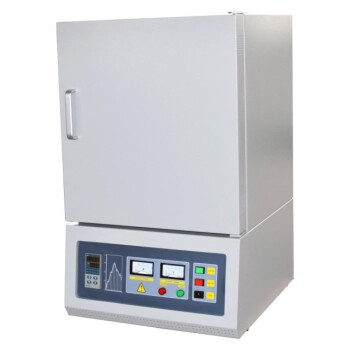
1700℃ Muffle Oven Furnace for Laboratory
Get superior heat control with our 1700℃ Muffle Furnace. Equipped with intelligent temperature microprocessor, TFT touch screen controller & advanced insulation materials for precise heating up to 1700C. Order now!
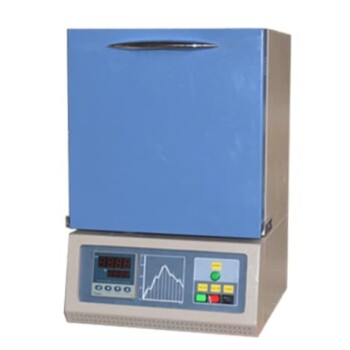
1200℃ Muffle Furnace Oven for Laboratory
Upgrade your lab with our 1200℃ Muffle Furnace. Achieve fast, precise heating with Japan alumina fibers and Molybdenum coils. Features TFT touch screen controller for easy programming and data analysis. Order now!
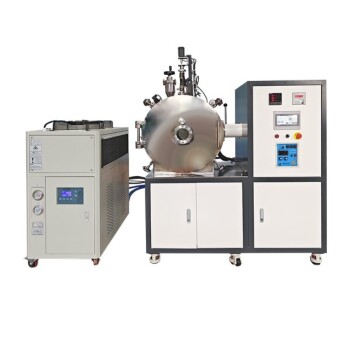
Lab-Scale Vacuum Induction Melting Furnace
Get precise alloy composition with our Vacuum Induction Melting Furnace. Ideal for aerospace, nuclear energy, and electronic industries. Order now for effective smelting and casting of metals and alloys.
Related Articles
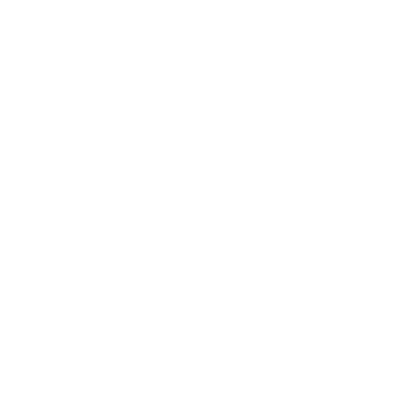
Optimizing Performance with Graphite Vacuum Furnaces: A Comprehensive Guide
Unlock the potential of graphite vacuum furnaces for high-temperature material treatment. Learn about their efficiency, customization options, automation, and key considerations for graphite rod usage.
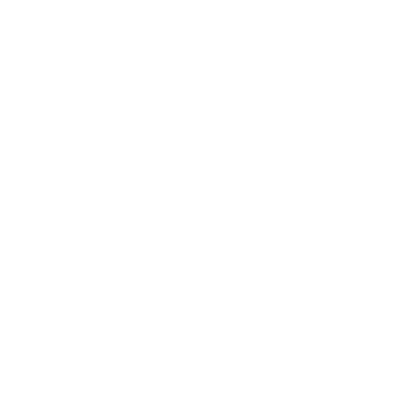
Maximizing Efficiency and Precision with Vacuum Graphite Furnaces
Discover how vacuum graphite furnaces revolutionize high-temperature material treatments with unmatched precision and efficiency. Explore customized solutions for various industries, advanced automation, and sustainable energy practices.
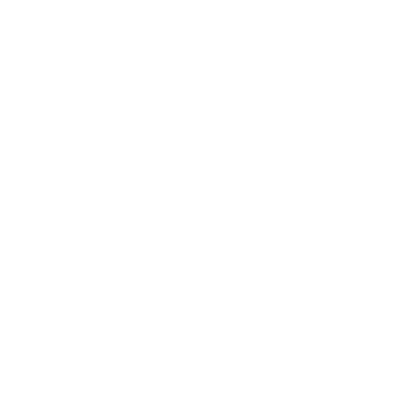
Unveiling Vacuum Graphite Furnaces: Performance, Applications, and Expert Insights
Delve into the world of vacuum graphite furnaces, exploring their exceptional performance, diverse applications, and crucial considerations. Our expert insights empower you to make informed decisions for your laboratory's high-temperature material treatment needs.
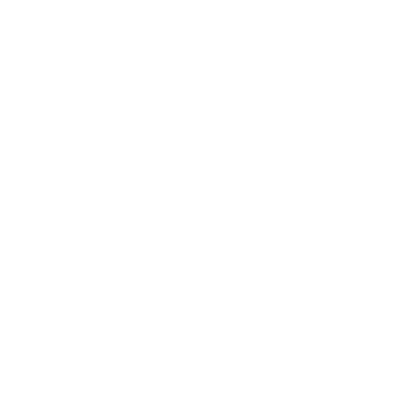
Understanding the Design and Functionality of Industrial Furnaces
Industrial furnaces are heating devices used in various industrial processes, including soldering, heat treatment of steels and alloys, and ceramics sintering.
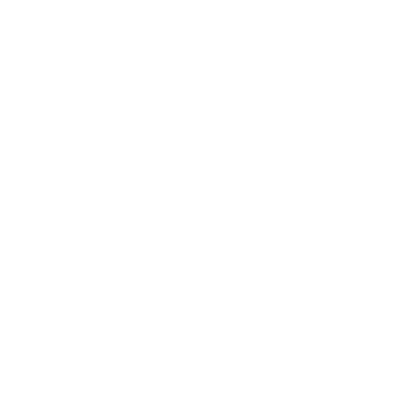
Optimizing Industrial Processes: Rotary Kiln and Laboratory Furnace Solutions
Discover how rotary kilns and laboratory furnaces revolutionize industrial processes. Learn about rotary kiln sizing and design, laboratory furnace features, and industries served. Explore the production of carbon products like biochar and activated carbon.
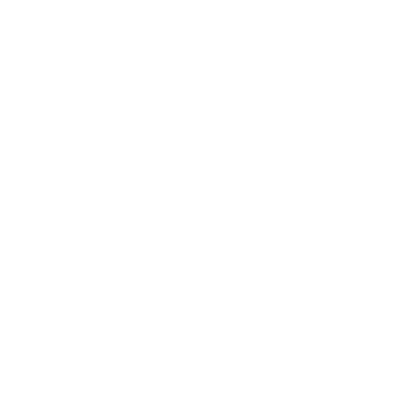
Guide to Bottom Loading Furnace
A bottom loading furnace is a type of industrial furnace that is designed for the efficient processing of materials by heating them to high temperatures.
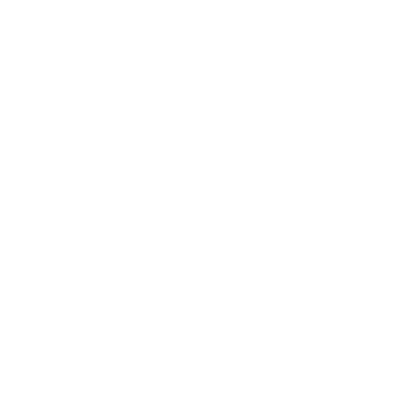
Comprehensive Guide to Atmosphere Furnaces: Types, Applications, and Benefits
Explore the world of atmosphere furnaces with our detailed guide. Learn about their types, applications in metallurgy and beyond, and the benefits they offer for precise material heat treatment.
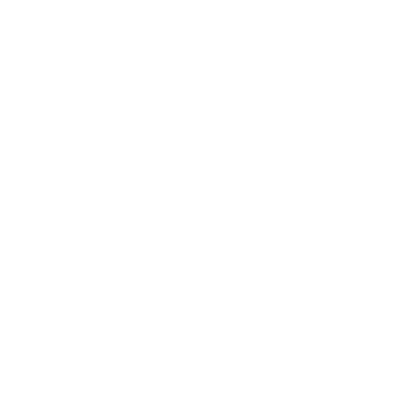
Hydrogen Atmosphere Furnaces: Applications, Safety, and Maintenance
Explore the comprehensive guide on hydrogen atmosphere furnaces, including their applications in high-end alloy sintering, safety measures, and maintenance tips. Learn about the types, components, and operational considerations for optimal performance.
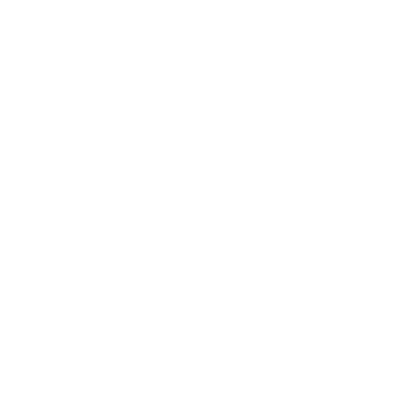
What is activated carbon regeneration Rotary Furnace
Electric activated carbon regeneration furnace is one typical electric external heating rotary furnace
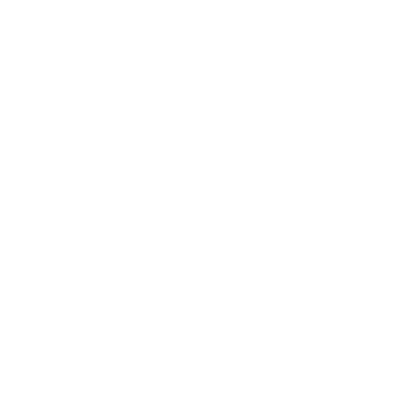
Electric Rotary Kiln Pyrolysis Furnace: A Comprehensive Guide to Pyrolysis Technology
Discover the principles, applications, and advantages of electric rotary kiln pyrolysis furnaces. Explore various heating methods, factors affecting efficiency, and the environmental benefits of this technology.
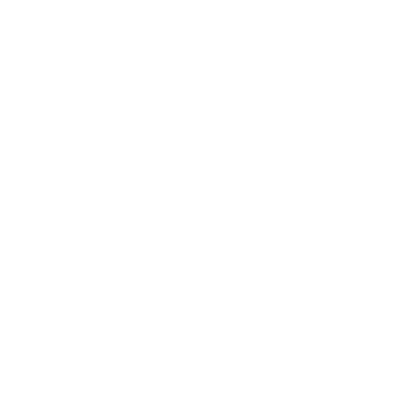
Understanding Electric Heating Systems(2): From Furnaces to Heating Elements
Discover how electric heating systems work, from electric furnaces to heating element basics. Learn about the benefits of electric heating and why it's a viable option for various applications. Find insights on heat treating furnaces and their subassemblies.
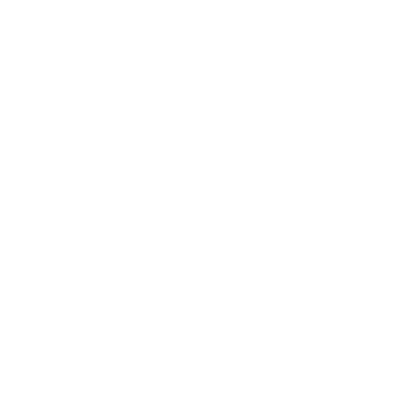
Electric Heating Systems(3): Understanding, Benefits, and Applications
Explore the world of electric heating systems, including electric furnaces, heating elements, and their benefits. Learn about the advantages, disadvantages, and applications of electric heating technology. Discover how electric heating systems work and their role in modern heating solutions.