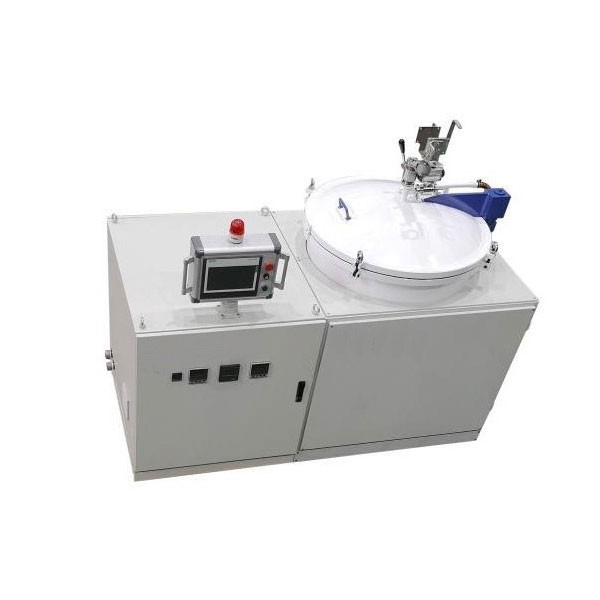
Graphitization furnace
Graphite Vacuum Furnace IGBT Experimental Graphitization Furnace
Item Number : GF-02
Price varies based on specs and customizations
- Maximum operating temperature:
- 3100℃
- High temperature zone volume:
- medium 100-300mm×100-300mm, (or customized according to users)
- Temperature uniformity:
- ≤±10℃
- Temperature measurement accuracy:
- 0.2~0.75%
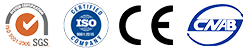
Shipping:
Contact us to get shipping details Enjoy On-time Dispatch Guarantee.
Why Choose Us
Reliable PartnerEasy ordering process, quality products, and dedicated support for your business success.
Introduction
The experimental graphitization furnace is a laboratory-specific equipment designed for universities, scientific research institutes, and other units. It serves the purpose of sintering and graphitization of carbon materials, sintering of carbon fiber ropes, and sintering and graphitization of carbon fiber filaments, among other materials that can be sintered in a carbon environment. This furnace offers high heating efficiency, ease of operation, and applicability in experiments, scientific research, teaching demonstrations, and other industries.
Applications
The IGBT experimental graphitization furnace finds applications in various industries and research fields, including:
- Ceramic firing
- Carbide growth
- Carbonization
- Graphitization
- Sintering
- Annealing
- Brazing
- Degassing
Features
The IGBT experimental graphitization furnace is a valuable tool for universities, research institutes, and other organizations. Its compact design, efficiency, and ease of use make it an ideal choice for a wide range of applications.
- Small footprint, low noise, and low energy consumption: The furnace's compact design and efficient operation make it easy to integrate into any laboratory setting.
- Ultra-high-temperature furnace body within 3000℃: The furnace can reach temperatures of up to 3000℃, making it suitable for sintering and graphitization of various materials.
- IGBT series induction heating: The furnace uses IGBT series induction heating, which reduces high-order harmonics and pollution to the power grid.
- Energy-saving: The furnace saves up to 15% more energy than traditional thyristor intermediate frequency power supplies.
- Programmable controller and human-machine interface: The furnace features a programmable controller and human-machine interface, enabling automated operation and three working modes: fully automatic, semi-automatic, and manual.
- High safety: The furnace is equipped with a comprehensive PLC water, electricity, gas automatic control and protection system, ensuring safe operation.
Principle
The IGBT experimental graphitization furnace utilizes the principle of induction heating to achieve high-temperature graphitization. IGBT (Insulated Gate Bipolar Transistor) technology provides efficient and precise power control, minimizing harmonic distortion and reducing grid pollution. The furnace is equipped with a programmable controller and human-machine interface, enabling automated operation and real-time monitoring of process parameters. The advanced safety features include PLC-based control of water, electricity, and gas, along with sound and light alarms to ensure safe and reliable operation.
Advantages
- The IGBT experimental graphitization furnace has a small footprint, is low-noise, and consumes low energy.
- The ultra-high temperature furnace body (within 3000℃) can fully meet the sintering and graphitization requirements of various materials.
- The use of IGBT series induction heating results in fewer high-order harmonics and less pollution to the power grid, ensuring that it will not interfere with the operation of electronic equipment.
- The product saves electricity, achieving 15% more energy savings than the old thyristor intermediate frequency power supply.
- Equipped with a programmable controller and human-machine interface, the entire process can be automated and has three working modes: fully automatic, semi-automatic, and manual.
- The furnace features high safety, with a comprehensive PLC water, electricity, gas automatic control and protection system, including sound and light alarms for over-temperature, sensor failure, water pressure, water flow, furnace over-pressure, and ultra-high water temperature.
Technical parameters and model specifications
High temperature zone volume: medium 100-300mmX100-300mm, or customized according to users
Working atmosphere in the furnace: vacuum, hydrogen, nitrogen, argon
Temperature uniformity: ≤±10℃
Temperature measurement: Infrared optical temperature measurement (1000~3200℃) (low temperature infrared thermometer 300-1100℃ can be equipped on request)
Temperature measurement accuracy: 0.2~0.75%
Temperature control: program control and manual control; temperature control accuracy: ±1℃
Limit heating rate: 100℃/minute (empty furnace, depending on the volume of the high temperature zone and the furnace structure)
Comprehensive PLC water, electricity, gas automatic control and protection system. The connecting cable between the control cabinet and the furnace body can be up to 20m long, and is used for remote control of the equipment.
Configuration options:
Horizontal double door structure/vertical top opening cover
The vacuum pump adopts rotary vane pump/rotary vane pump + Roots pump + digital display vacuum gauge
Temperature measurement system: dual colorimetric infrared thermometer (1000-3200℃)/tungsten-rhenium thermocouple (0-1700℃) + dual colorimetric infrared thermometer (1000-3200℃)/single color infrared thermometer ( 300-1100℃) + dual colorimetric infrared measurement
Thermometer (1000-3200℃)
Product model specifications | GF-02-Ф10×15 | GF-02-Φ20×30 | GF-02-Ф30×40 |
---|---|---|---|
Volume(L) | 1.1 | 10 | 28 |
Limit temperature(C) | 3100 | 3100 | 3100 |
Effective heating area (mm) | Φ100×150 | Φ200×300 | Φ300×400 |
Power(KW) | 30 | 50 | 80 |
Frequency(HZ) | 4000 | 2500 | 2500 |
Temperature control method | Japan Shima Electric Thermostat | ||
Heating method | Induction heating | ||
Vacuum system | Rotary vane vacuum pump (for high vacuum requirements, Roots vacuum pump and oil diffusion pump are required) | ||
Sintering atmosphere | N2, Ar | ||
Rated power supply voltage (V) | 380 | ||
Rated heating voltage (V) | According to the design determination, configure the transformer | ||
Vacuum limit (Pa) | 100 (vacuum cold state) |
FAQ
What Is A Graphitization Furnace?
What Is A Graphite Vacuum Furnace Used For?
What Is A Vacuum Furnace Used For?
What Is The Purpose Of An IGBT Experimental Graphitization Furnace?
What Are The Key Features Of An IGBT Experimental Graphitization Furnace?
What Are The Main Applications Of Graphitization Furnaces?
What Are The Main Types Of Graphite Vacuum Furnaces?
What Is The Process Of A Vacuum Furnace?
What Are The Different Types Of Graphitization Furnaces?
How Does A Graphite Vacuum Furnace Work?
What Gas Is Used In A Vacuum Furnace?
How Does A Graphitization Furnace Work?
What Are The Advantages Of Using A Graphite Vacuum Furnace?
What Is The Heating Element Used In A Vacuum Furnace?
What Are The Advantages Of Using A Graphitization Furnace?
What Temperature Range Can A Graphite Vacuum Furnace Achieve?
What Industries Benefit From Graphite Vacuum Furnaces?
4.9
out of
5
This furnace has exceeded my expectations! It's so efficient and easy to use, making my research work a breeze.
4.8
out of
5
I highly recommend this furnace for any laboratory. It's a game-changer for our graphitization experiments.
4.7
out of
5
The compact design and low energy consumption make this furnace perfect for our small lab space. Plus, the automated operation saves us so much time.
4.9
out of
5
I'm impressed with the ultra-high temperature capabilities of this furnace. It's enabled us to explore new materials and applications.
4.8
out of
5
The programmable controller and human-machine interface make this furnace incredibly user-friendly. It's a joy to operate.
4.7
out of
5
Safety is paramount in our lab, and this furnace delivers. The comprehensive protection system gives us peace of mind.
4.9
out of
5
The energy savings from this furnace are remarkable. It's not only environmentally friendly but also helps us reduce operating costs.
4.8
out of
5
The technical support from KINTEK SOLUTION is exceptional. They're always available to answer our questions and assist with any issues.
4.7
out of
5
The delivery was incredibly fast, and the packaging ensured the furnace arrived in perfect condition.
4.9
out of
5
The value for money of this furnace is unbeatable. It's a top-notch product at a reasonable price.
4.8
out of
5
The durability of this furnace is outstanding. It's built to last and withstand the demands of our research work.
4.7
out of
5
This furnace has revolutionized our research capabilities. Its technological advancements have opened up new possibilities.
4.9
out of
5
I've used other furnaces before, but this one from KINTEK SOLUTION is by far the best. It's a game-changer for our lab.
Products
Graphite Vacuum Furnace IGBT Experimental Graphitization Furnace
REQUEST A QUOTE
Our professional team will reply to you within one business day. Please feel free to contact us!
Related Products
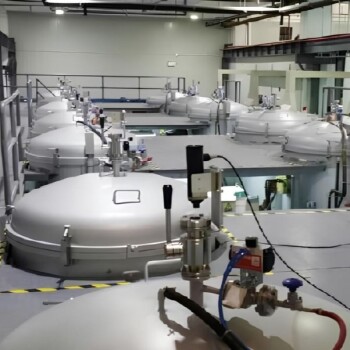
Graphite Vacuum Furnace High Thermal Conductivity Film Graphitization Furnace
The high thermal conductivity film graphitization furnace has uniform temperature, low energy consumption and can operate continuously.
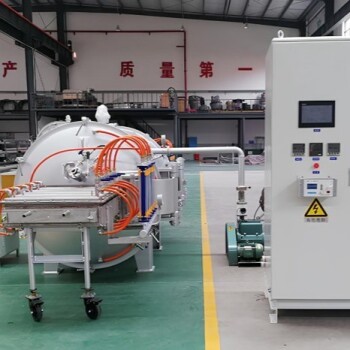
Graphite Vacuum Continuous Graphitization Furnace
High-temperature graphitization furnace is a professional equipment for graphitization treatment of carbon materials. It is a key equipment for the production of high-quality graphite products. It has high temperature, high efficiency and uniform heating. It is suitable for various high-temperature treatments and graphitization treatments. It is widely used in metallurgy, electronics, aerospace, etc. industry.
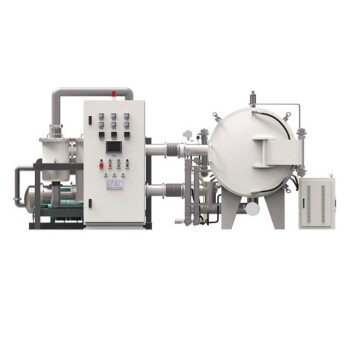
Horizontal High Temperature Graphite Vacuum Graphitization Furnace
Horizontal Graphitization Furnace: This type of furnace is designed with the heating elements placed horizontally, allowing for uniform heating of the sample. It's well-suited for graphitizing large or bulky samples that require precise temperature control and uniformity.
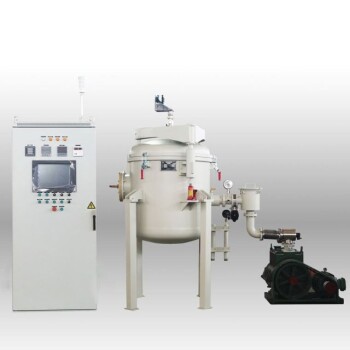
Ultra-High Temperature Graphite Vacuum Graphitization Furnace
The ultra-high temperature graphitization furnace utilizes medium frequency induction heating in a vacuum or inert gas environment. The induction coil generates an alternating magnetic field, inducing eddy currents in the graphite crucible, which heats up and radiates heat to the workpiece, bringing it to the desired temperature. This furnace is primarily used for graphitization and sintering of carbon materials, carbon fiber materials, and other composite materials.
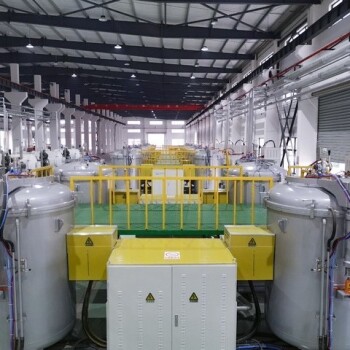
Vertical High Temperature Graphite Vacuum Graphitization Furnace
Vertical high temperature graphitization furnace for carbonization and graphitization of carbon materials up to 3100℃.Suitable for shaped graphitization of carbon fiber filaments and other materials sintered in a carbon environment.Applications in metallurgy, electronics, and aerospace for producing high-quality graphite products like electrodes and crucibles.

Graphite Vacuum Furnace Bottom Discharge Graphitization Furnace for Carbon Materials
Bottom-out graphitization furnace for carbon materials, ultra-high temperature furnace up to 3100°C, suitable for graphitization and sintering of carbon rods and carbon blocks. Vertical design, bottom discharging, convenient feeding and discharging, high temperature uniformity, low energy consumption, good stability, hydraulic lifting system, convenient loading and unloading.
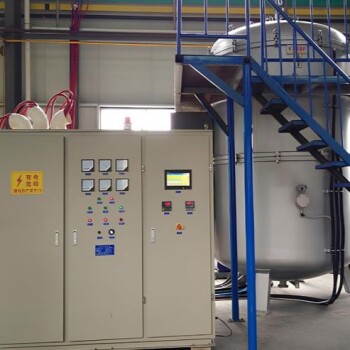
Large Vertical Graphite Vacuum Graphitization Furnace
A large vertical high-temperature graphitization furnace is a type of industrial furnace used for the graphitization of carbon materials, such as carbon fiber and carbon black. It is a high-temperature furnace that can reach temperatures of up to 3100°C.
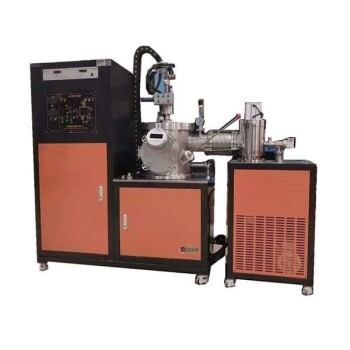
Vacuum Arc Induction Melting Furnace
Discover the power of Vacuum Arc Furnace for melting active & refractory metals. High-speed, remarkable degassing effect, and free of contamination. Learn more now!
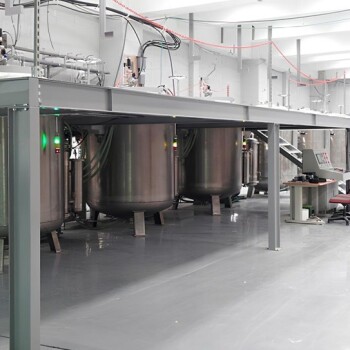
Graphite Vacuum Furnace Negative Material Graphitization Furnace
Graphitization furnace for battery production has uniform temperature and low energy consumption. Graphitization furnace for negative electrode materials: an efficient graphitization solution for battery production and advanced functions to enhance battery performance.
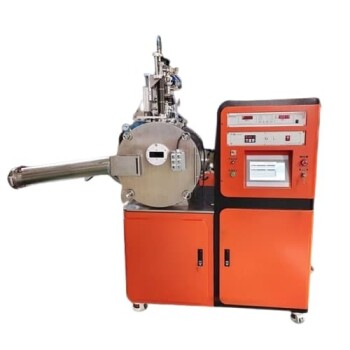
Vacuum Induction Melting Spinning System Arc Melting Furnace
Develop metastable materials with ease using our Vacuum Melt Spinning System. Ideal for research and experimental work with amorphous and microcrystalline materials. Order now for effective results.
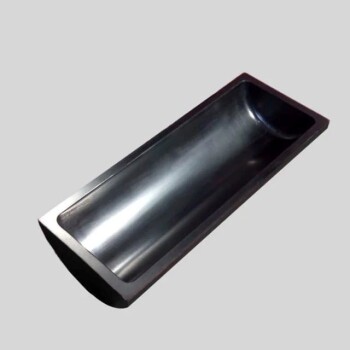
Carbon Graphite Boat -Laboratory Tube Furnace with Cover
Covered Carbon Graphite Boat Laboratory Tube Furnaces are specialized vessels or vessels made of graphite material designed to withstand extreme high temperatures and chemically aggressive environments.
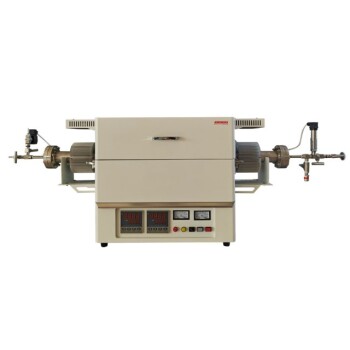
High Pressure Laboratory Vacuum Tube Furnace Quartz Tubular Furnace
KT-PTF High Pressure Tube Furnace: Compact split tube furnace with strong positive pressure resistance. Working temp up to 1100°C and pressure up to 15Mpa. Also works under controller atmosphere or high vacuum.
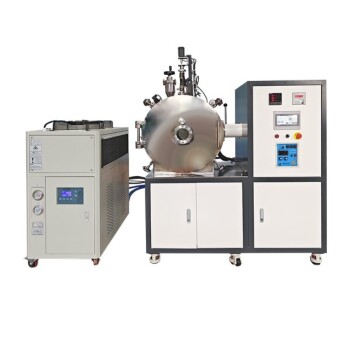
Lab-Scale Vacuum Induction Melting Furnace
Get precise alloy composition with our Vacuum Induction Melting Furnace. Ideal for aerospace, nuclear energy, and electronic industries. Order now for effective smelting and casting of metals and alloys.
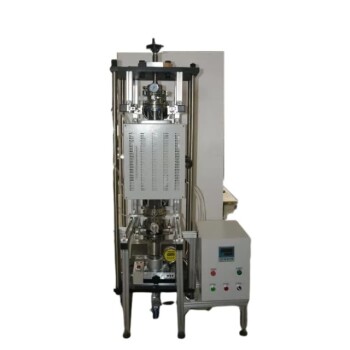
Vacuum Hot Press Furnace Heated Vacuum Press Machine Tube Furnace
Reduce forming pressure & shorten sintering time with Vacuum Tube Hot Press Furnace for high-density, fine-grain materials. Ideal for refractory metals.
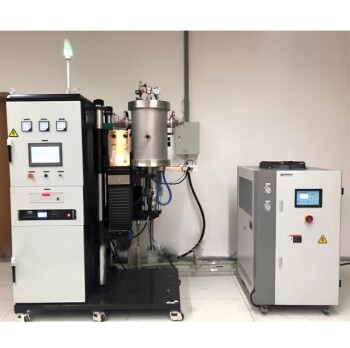
Vacuum Heat Treat and Molybdenum Wire Sintering Furnace for Vacuum Sintering
A vacuum molybdenum wire sintering furnace is a vertical or bedroom structure, which is suitable for withdrawal, brazing, sintering and degassing of metal materials under high vacuum and high temperature conditions. It is also suitable for dehydroxylation treatment of quartz materials.
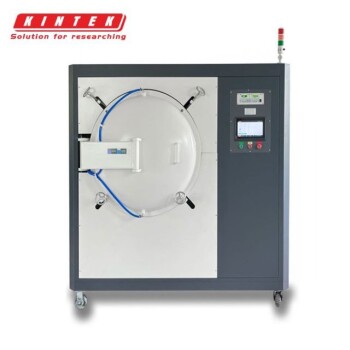
Vacuum Heat Treat Furnace with Ceramic Fiber Liner
Vacuum furnace with polycrystalline ceramic fiber insulation liner for excellent heat insulation and uniform temperature field. Choose from 1200℃ or 1700℃ max. working temperature with high vacuum performance and precise temperature control.
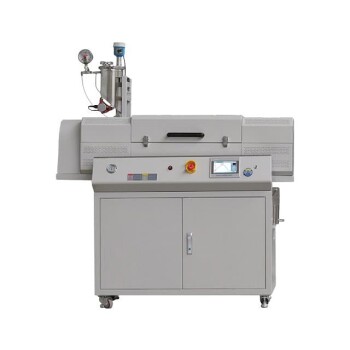
Laboratory Vacuum Tilt Rotary Tube Furnace Rotating Tube Furnace
Discover the versatility of Laboratory Rotary Furnace: Ideal for calcination, drying, sintering, and high-temperature reactions. Adjustable rotating and tilting functions for optimal heating. Suitable for vacuum and controlled atmosphere environments. Learn more now!
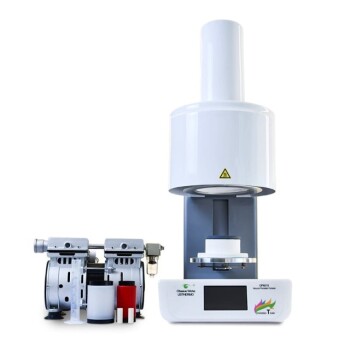
Dental Porcelain Zirconia Sintering Ceramic Vacuum Press Furnace
Get precise dental results with Dental Vacuum Press Furnace. Automatic temperature calibration, low noise tray, and touch screen operation. Order now!
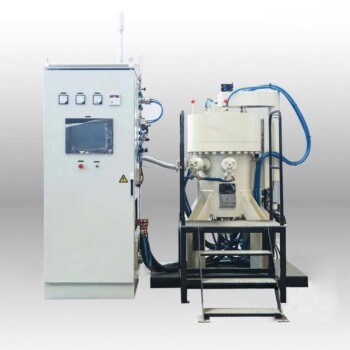
Vacuum Heat Treat and Sintering Furnace with 9MPa Air Pressure
The air pressure sintering furnace is a high-tech equipment commonly used for the sintering of advanced ceramic materials. It combines vacuum sintering and pressure sintering techniques to achieve high-density and high-strength ceramics.
Related Articles
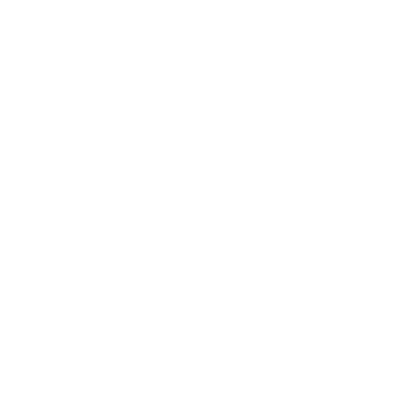
Maximizing Efficiency and Precision with Vacuum Graphite Furnaces
Discover how vacuum graphite furnaces revolutionize high-temperature material treatments with unmatched precision and efficiency. Explore customized solutions for various industries, advanced automation, and sustainable energy practices.
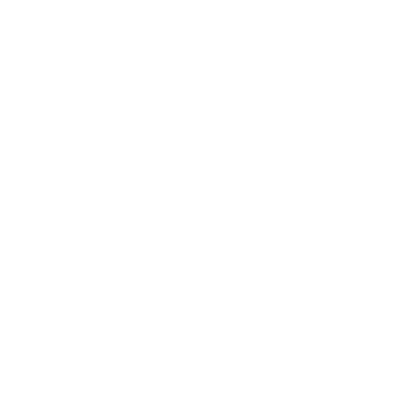
Unveiling Vacuum Graphite Furnaces: Performance, Applications, and Expert Insights
Delve into the world of vacuum graphite furnaces, exploring their exceptional performance, diverse applications, and crucial considerations. Our expert insights empower you to make informed decisions for your laboratory's high-temperature material treatment needs.
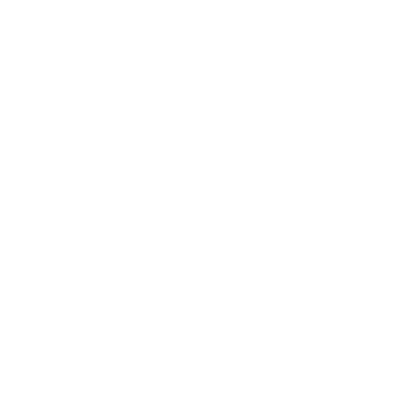
Optimizing Performance with Graphite Vacuum Furnaces: A Comprehensive Guide
Unlock the potential of graphite vacuum furnaces for high-temperature material treatment. Learn about their efficiency, customization options, automation, and key considerations for graphite rod usage.
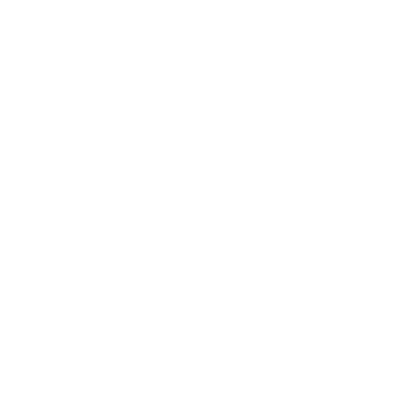
How FTIR Pellet Press Works in Sample Preparation for Spectroscopy Analysis
FTIR (Fourier Transform Infrared) spectroscopy is a powerful analytical technique for identifying and characterizing chemical compounds based on their infrared absorption spectra.
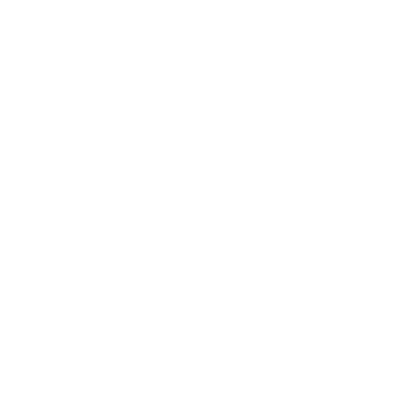
Biomass Pyrolysis An Effective Means of Producing Biofuels
Biomass pyrolysis is a process that involves heating organic matter in the absence of oxygen to break it down into smaller molecules. This technology has gained popularity due to its potential to produce biofuels.
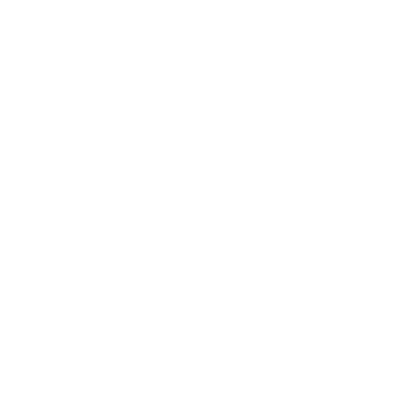
Temperature Control Requirements for Laboratory Small High-Temperature Resistance Furnaces
Exploring the precision, stability, and safety aspects of temperature control in laboratory small high-temperature resistance furnaces.
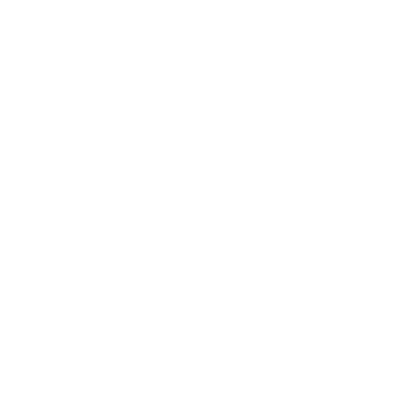
Temperature Control Accuracy of High Temperature Experimental Chamber Muffle Furnace
An in-depth analysis of factors affecting the temperature control accuracy of high temperature muffle furnaces.
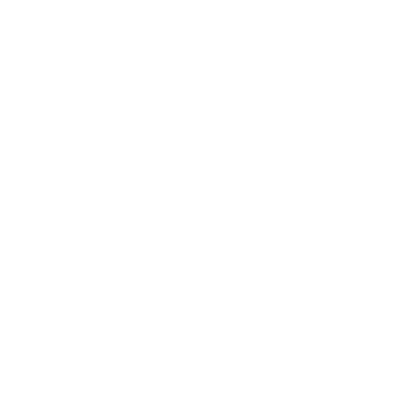
Operational Guide for Inert Atmosphere Protection Furnace in Mixed Atmosphere
Detailed guide on operating an inert atmosphere protection furnace in a mixed atmosphere, emphasizing gas control, safety measures, and process adjustments.
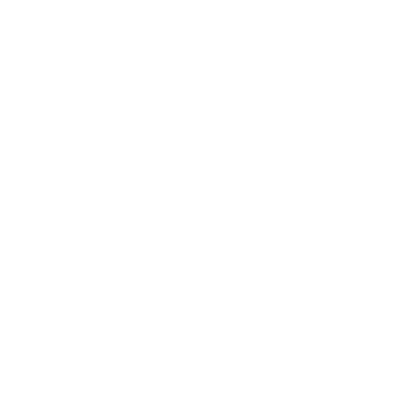
Understanding the Temperature Zones in Tube Furnaces
Explores the roles and impacts of different temperature zones in tube furnaces, focusing on constant temperature zones and their selection criteria.
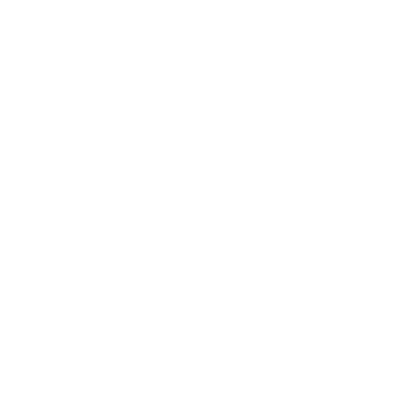
Calibration Methods for High-Temperature Muffle Furnaces
Explores traditional and system calibration methods for ensuring temperature accuracy in high-temperature muffle furnaces, focusing on temperature deviation and uniformity.
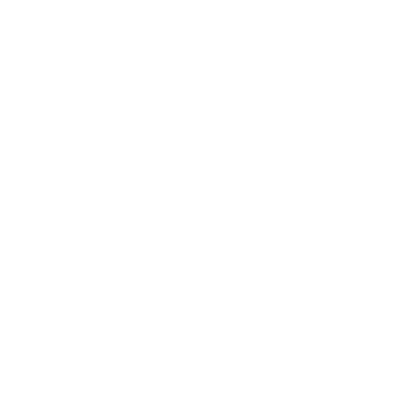
Selection of Muffle Furnace: Key Considerations
Guidelines for selecting a muffle furnace based on experimental needs, heating methods, temperature control, safety, and more.
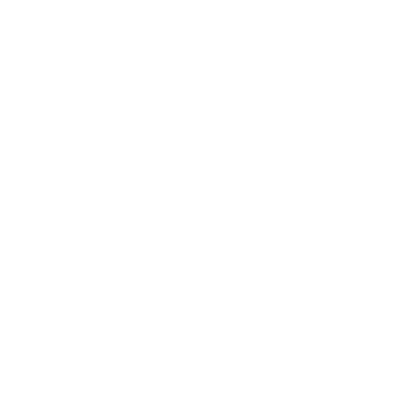
Choosing the Right Heating Method for Laboratory Experiments
Discusses different heating methods in labs and their suitability for various experiments.