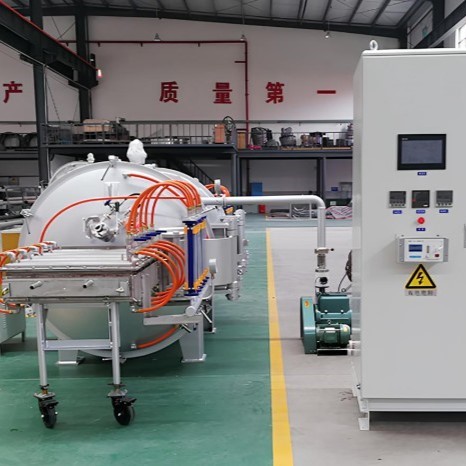
Graphitization furnace
Graphite Vacuum Continuous Graphitization Furnace
Item Number : GF-07
Price varies based on specs and customizations
- Rated temperature (C)
- 2500
- Effective heating area (mm)
- 100X200X500 / 100X400X1000 / 100X600x2000
- Power (KW)
- 80 / 150 / 300
- Frequency (HZ)
- 2500/1000
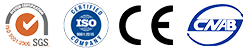
Shipping:
Contact us to get shipping details Enjoy On-time Dispatch Guarantee.
Why Choose Us
Reliable PartnerEasy ordering process, quality products, and dedicated support for your business success.
Introduction
A continuous graphitization furnace is a high-temperature furnace used to treat carbon cloth, carbon fiber, silicon carbide ceramic fiber, and other materials at temperatures ranging from 2100 to 2800°C. It employs medium frequency induction heating for rapid temperature rise and high efficiency, and its unique design ensures temperature uniformity within the furnace. The furnace features double-layer alumina brick insulation to prevent short circuits and provides excellent heat insulation and fire resistance, resulting in low heat loss and stable operation. It incorporates a constant tension control system for carbon fiber and an automatic rewinding and unwinding system for carbon felt. All operating parameters, actions, and alarms are controlled by a PLC with a human-computer interaction interface, digital flow monitoring system, and water flow monitoring and protection for each channel of the power cabinet. Multiple operating processes can be conveniently stored, recalled, and interactively operated, while real-time display and recording capabilities enhance user experience.
Applications
Continuous graphitization furnaces are widely used in the following applications:
- Continuous graphitization treatment of carbon cloth
- Continuous graphitization treatment of carbon fiber
- Continuous graphitization treatment of silicon carbide ceramic fiber
Features
Continuous graphitization furnace is a kind of high-temperature furnace used in the continuous graphitization treatment of carbon cloth, carbon fiber, silicon carbide ceramic fiber and other materials at high temperatures of 2100-2800°C. It has the following advantages:
-
High temperature uniformity: The unique furnace design greatly improves the temperature uniformity of the furnace body, ensuring consistent and uniform treatment of materials.
-
Low energy consumption: The double-layer alumina brick insulation material effectively reduces heat loss, resulting in lower energy consumption and improved efficiency.
-
Automatic control: The PLC-controlled system with human-computer interaction interface allows for precise control over operating parameters, actions, and alarms, simplifying operation and ensuring accurate treatment.
-
Real-time monitoring: The digital flow monitoring system and water flow monitoring and protection for each channel of the power cabinet provide real-time monitoring of equipment performance, ensuring safety and reliability.
-
Versatile applications: The continuous graphitization furnace is suitable for a variety of high temperature treatment and graphitization treatment applications, making it a versatile and cost-effective solution.
Principle
The continuous graphitization furnace employs medium frequency induction heating for rapid temperature elevation and efficiency. Its well-designed furnace structure optimizes temperature uniformity. The double-layer alumina brick insulation effectively prevents short circuits and ensures heat insulation and fire resistance, minimizing heat loss and enhancing equipment stability.
Advantages
- High temperature uniformity: Medium frequency induction heating provides rapid temperature rise and high efficiency. The unique furnace design significantly improves temperature consistency within the furnace body.
- Low energy consumption and stability: Double-layer alumina brick insulation prevents short circuits, ensuring excellent heat insulation and fire resistance, minimizing heat loss, and enhancing equipment stability.
- Precise tension control: Constant tension control system for carbon fiber and automatic rewinding and unwinding system for carbon felt.
- Advanced monitoring and control: PLC controls all operating parameters, actions, and alarms. A human-computer interaction interface, digital flow monitoring system, and water flow monitoring and protection for each channel of the power cabinet provide real-time monitoring, interactive operation, and convenient storage and retrieval of operating processes.
- Suitable for various applications: The high temperature, high efficiency, and uniform heating characteristics make the furnace ideal for a wide range of high temperature treatment and graphitization applications.
Technical parameters
- Commonly used temperatures: 2000C-2800℃
- Working atmosphere in the furnace: argon, nitrogen and other inert gases
- Temperature uniformity: ≤±25℃
- Temperature measurement: far-infrared optical temperature measurement (1000-3200℃);
- Temperature measurement accuracy: 0.2~0.75%
- Temperature control: program control and manual control; temperature control accuracy: ±1℃
- Furnace structure: horizontal single-zone heating, both inlet and outlet are connected by flanges
- Heating element: graphite crucible
Product model specifications | GF-07-10×20×50 | GF-07-10×40×100 | G7-06-10×60×200 |
---|---|---|---|
Rated temperature(C) | 2500 | 2500 | 2500 |
Effective heating area (mm) | 100×200×500 | 100×400×1000 | 100×600×2000 |
Power(KW) | 80 | 150 | 300 |
Frequency(HZ) | 2500 | 2500 | 1000 |
heating method | Induction heating | ||
Import and export cooling | Cooling zones of 500-1000mm are set up at the entrance and exit respectively. | ||
Import and export gas protection | Set up 500-1000mm gas sealing areas at the inlet and outlet respectively | ||
Temperature measurement method | 1000-3200C infrared optical temperature measurement | ||
Insulation part | Hard carbon felt+soft carbon felt | ||
gas flow | 2-6m/h | ||
Oxygen content detection | Using Shaanxi Fein oxygen content analyzer, real-time detection of oxygen content and dew point real-time analyzer |
FAQ
What Is A Graphite Vacuum Furnace Used For?
What Is A Graphitization Furnace?
What Is A Vacuum Furnace Used For?
What Materials Can Be Treated In The Continuous Graphitization Furnace?
What Applications Are The Products Of The Continuous Graphitization Furnace Used In?
What Are The Main Types Of Graphite Vacuum Furnaces?
What Are The Main Applications Of Graphitization Furnaces?
What Is The Process Of A Vacuum Furnace?
How Does A Graphite Vacuum Furnace Work?
What Are The Different Types Of Graphitization Furnaces?
What Gas Is Used In A Vacuum Furnace?
What Are The Advantages Of Using A Graphite Vacuum Furnace?
How Does A Graphitization Furnace Work?
What Is The Heating Element Used In A Vacuum Furnace?
What Temperature Range Can A Graphite Vacuum Furnace Achieve?
What Are The Advantages Of Using A Graphitization Furnace?
What Industries Benefit From Graphite Vacuum Furnaces?
4.8
out of
5
The continuous graphitization furnace has been a great addition to our lab. It's easy to use and has helped us improve the quality of our products.
4.9
out of
5
We've been using the continuous graphitization furnace for over a year now and it's been a great investment. It's helped us increase our production efficiency and reduce our costs.
4.7
out of
5
The continuous graphitization furnace is a great value for money. It's well-built and has a lot of features that make it easy to use.
4.8
out of
5
The continuous graphitization furnace is a very durable product. We've been using it for several years now and it's still going strong.
4.9
out of
5
The continuous graphitization furnace is a technologically advanced product. It has a lot of features that make it easy to use and control.
4.7
out of
5
The continuous graphitization furnace is a great product for small labs. It's compact and easy to use.
4.8
out of
5
The continuous graphitization furnace is a great product for large labs. It's fast and efficient.
4.9
out of
5
The continuous graphitization furnace is a great product for research labs. It's accurate and reliable.
4.7
out of
5
The continuous graphitization furnace is a great product for industrial labs. It's durable and has a long lifespan.
4.8
out of
5
The continuous graphitization furnace is a great product for educational labs. It's safe and easy to use.
4.9
out of
5
The continuous graphitization furnace is a great product for any lab. It's versatile and can be used for a variety of applications.
Products
Graphite Vacuum Continuous Graphitization Furnace
REQUEST A QUOTE
Our professional team will reply to you within one business day. Please feel free to contact us!
Related Products
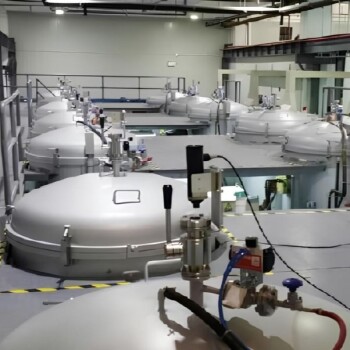
Graphite Vacuum Furnace High Thermal Conductivity Film Graphitization Furnace
The high thermal conductivity film graphitization furnace has uniform temperature, low energy consumption and can operate continuously.
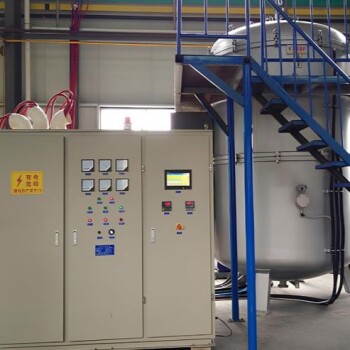
Large Vertical Graphite Vacuum Graphitization Furnace
A large vertical high-temperature graphitization furnace is a type of industrial furnace used for the graphitization of carbon materials, such as carbon fiber and carbon black. It is a high-temperature furnace that can reach temperatures of up to 3100°C.
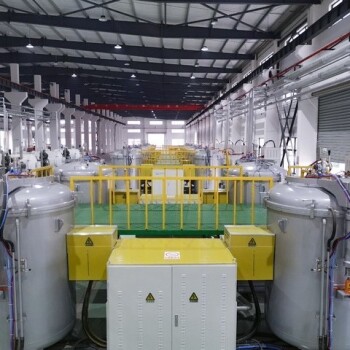
Vertical High Temperature Graphite Vacuum Graphitization Furnace
Vertical high temperature graphitization furnace for carbonization and graphitization of carbon materials up to 3100℃.Suitable for shaped graphitization of carbon fiber filaments and other materials sintered in a carbon environment.Applications in metallurgy, electronics, and aerospace for producing high-quality graphite products like electrodes and crucibles.
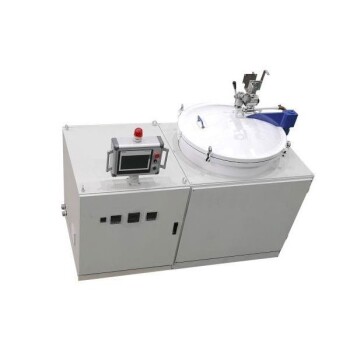
Graphite Vacuum Furnace IGBT Experimental Graphitization Furnace
IGBT experimental graphitization furnace, a tailored solution for universities and research institutions, with high heating efficiency, user-friendliness, and precise temperature control.

Graphite Vacuum Furnace Bottom Discharge Graphitization Furnace for Carbon Materials
Bottom-out graphitization furnace for carbon materials, ultra-high temperature furnace up to 3100°C, suitable for graphitization and sintering of carbon rods and carbon blocks. Vertical design, bottom discharging, convenient feeding and discharging, high temperature uniformity, low energy consumption, good stability, hydraulic lifting system, convenient loading and unloading.
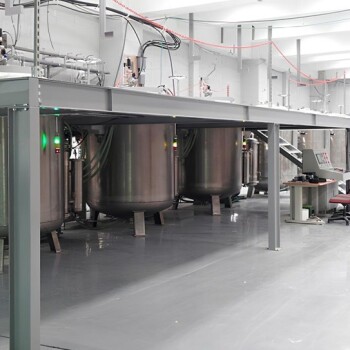
Graphite Vacuum Furnace Negative Material Graphitization Furnace
Graphitization furnace for battery production has uniform temperature and low energy consumption. Graphitization furnace for negative electrode materials: an efficient graphitization solution for battery production and advanced functions to enhance battery performance.
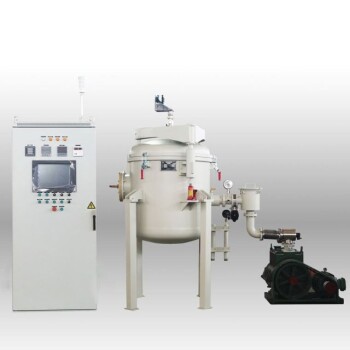
Ultra-High Temperature Graphite Vacuum Graphitization Furnace
The ultra-high temperature graphitization furnace utilizes medium frequency induction heating in a vacuum or inert gas environment. The induction coil generates an alternating magnetic field, inducing eddy currents in the graphite crucible, which heats up and radiates heat to the workpiece, bringing it to the desired temperature. This furnace is primarily used for graphitization and sintering of carbon materials, carbon fiber materials, and other composite materials.
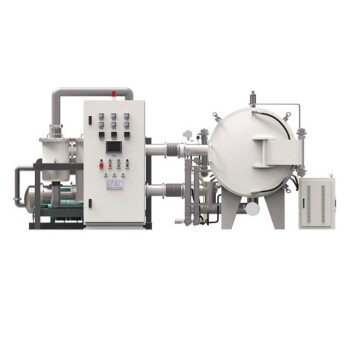
Horizontal High Temperature Graphite Vacuum Graphitization Furnace
Horizontal Graphitization Furnace: This type of furnace is designed with the heating elements placed horizontally, allowing for uniform heating of the sample. It's well-suited for graphitizing large or bulky samples that require precise temperature control and uniformity.
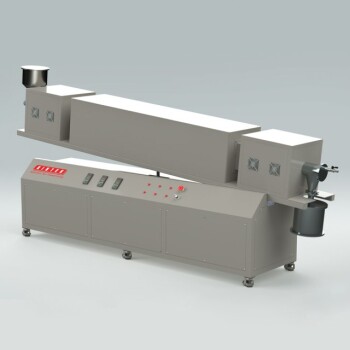
Vacuum Sealed Continuous Working Rotary Tube Furnace Rotating Tube Furnace
Experience efficient material processing with our vacuum-sealed rotary tube furnace. Perfect for experiments or industrial production, equipped with optional features for controlled feeding and optimized results. Order now.
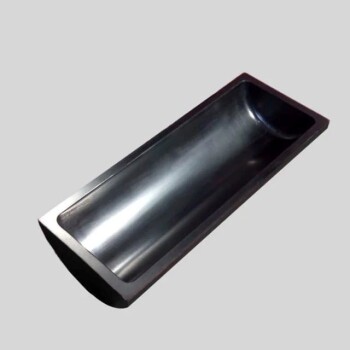
Carbon Graphite Boat -Laboratory Tube Furnace with Cover
Covered Carbon Graphite Boat Laboratory Tube Furnaces are specialized vessels or vessels made of graphite material designed to withstand extreme high temperatures and chemically aggressive environments.
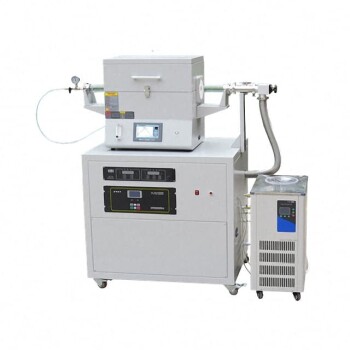
Efficient split chamber CVD furnace with vacuum station for intuitive sample checking and quick cooling. Up to 1200℃ max temperature with accurate MFC mass flowmeter control.
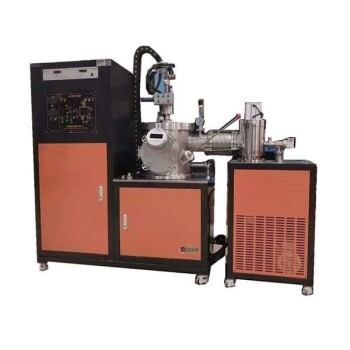
Vacuum Arc Induction Melting Furnace
Discover the power of Vacuum Arc Furnace for melting active & refractory metals. High-speed, remarkable degassing effect, and free of contamination. Learn more now!
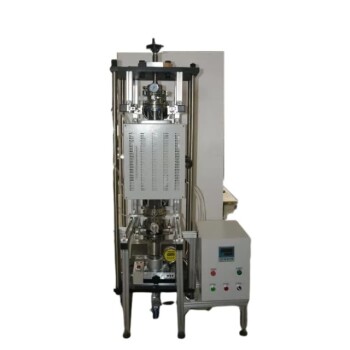
Vacuum Hot Press Furnace Heated Vacuum Press Machine Tube Furnace
Reduce forming pressure & shorten sintering time with Vacuum Tube Hot Press Furnace for high-density, fine-grain materials. Ideal for refractory metals.
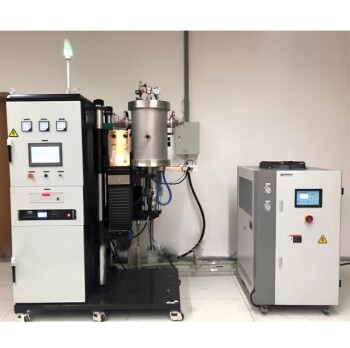
Vacuum Heat Treat and Molybdenum Wire Sintering Furnace for Vacuum Sintering
A vacuum molybdenum wire sintering furnace is a vertical or bedroom structure, which is suitable for withdrawal, brazing, sintering and degassing of metal materials under high vacuum and high temperature conditions. It is also suitable for dehydroxylation treatment of quartz materials.
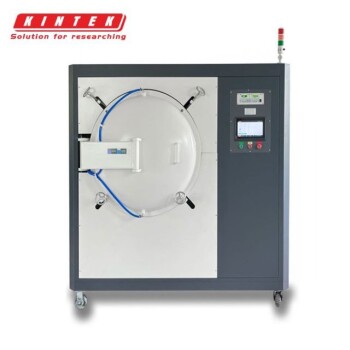
Vacuum Heat Treat Furnace with Ceramic Fiber Liner
Vacuum furnace with polycrystalline ceramic fiber insulation liner for excellent heat insulation and uniform temperature field. Choose from 1200℃ or 1700℃ max. working temperature with high vacuum performance and precise temperature control.
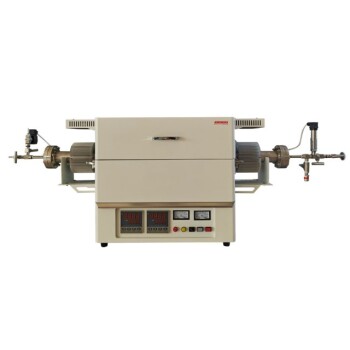
High Pressure Laboratory Vacuum Tube Furnace Quartz Tubular Furnace
KT-PTF High Pressure Tube Furnace: Compact split tube furnace with strong positive pressure resistance. Working temp up to 1100°C and pressure up to 15Mpa. Also works under controller atmosphere or high vacuum.
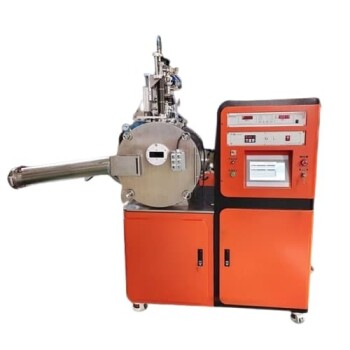
Vacuum Induction Melting Spinning System Arc Melting Furnace
Develop metastable materials with ease using our Vacuum Melt Spinning System. Ideal for research and experimental work with amorphous and microcrystalline materials. Order now for effective results.
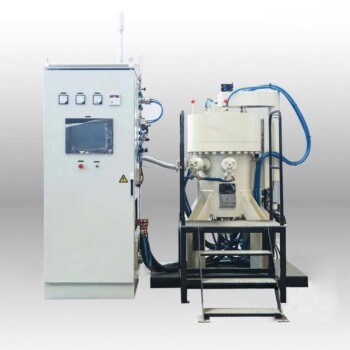
Vacuum Heat Treat and Sintering Furnace with 9MPa Air Pressure
The air pressure sintering furnace is a high-tech equipment commonly used for the sintering of advanced ceramic materials. It combines vacuum sintering and pressure sintering techniques to achieve high-density and high-strength ceramics.
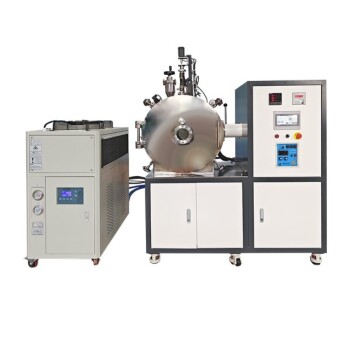
Lab-Scale Vacuum Induction Melting Furnace
Get precise alloy composition with our Vacuum Induction Melting Furnace. Ideal for aerospace, nuclear energy, and electronic industries. Order now for effective smelting and casting of metals and alloys.
Related Articles
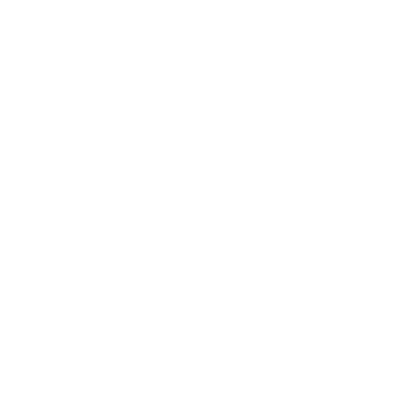
Maximizing Efficiency and Precision with Vacuum Graphite Furnaces
Discover how vacuum graphite furnaces revolutionize high-temperature material treatments with unmatched precision and efficiency. Explore customized solutions for various industries, advanced automation, and sustainable energy practices.
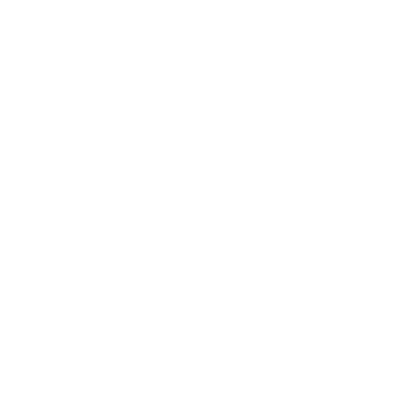
Unveiling Vacuum Graphite Furnaces: Performance, Applications, and Expert Insights
Delve into the world of vacuum graphite furnaces, exploring their exceptional performance, diverse applications, and crucial considerations. Our expert insights empower you to make informed decisions for your laboratory's high-temperature material treatment needs.
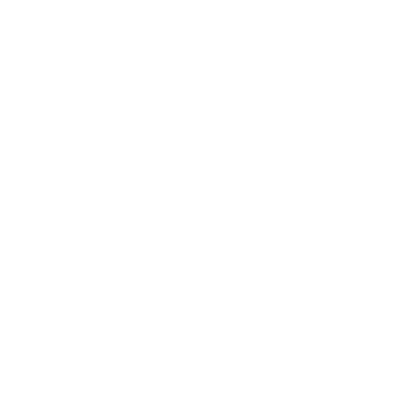
What is activated carbon regeneration Rotary Furnace
Electric activated carbon regeneration furnace is one typical electric external heating rotary furnace
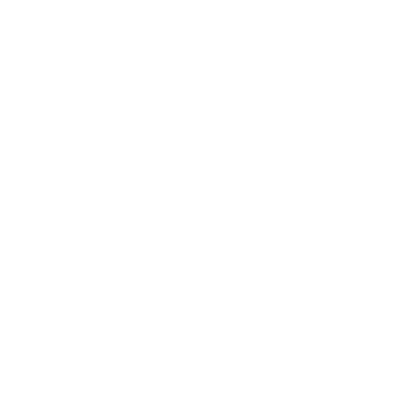
Optimizing Performance with Graphite Vacuum Furnaces: A Comprehensive Guide
Unlock the potential of graphite vacuum furnaces for high-temperature material treatment. Learn about their efficiency, customization options, automation, and key considerations for graphite rod usage.
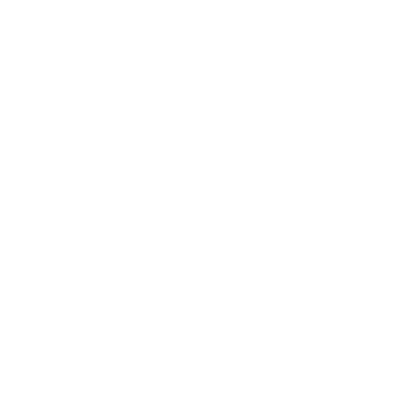
Understanding the Design and Functionality of Industrial Furnaces
Industrial furnaces are heating devices used in various industrial processes, including soldering, heat treatment of steels and alloys, and ceramics sintering.
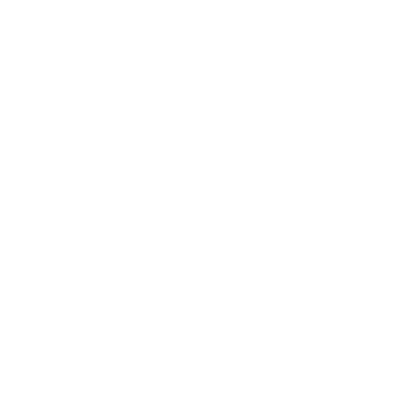
All About ACTIVATED CARBON THERMAL REGENERATION
Introduction, method and selection of activated carbon regeneration
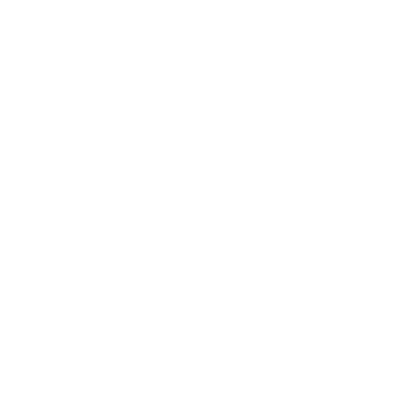
Exploring the Ashing Process and Ashing Furnace: A Comprehensive Guide
the ashing process involves heating a sample in the presence of oxygen to burn off organic compounds and leave behind the inorganic, non-combustible ash.
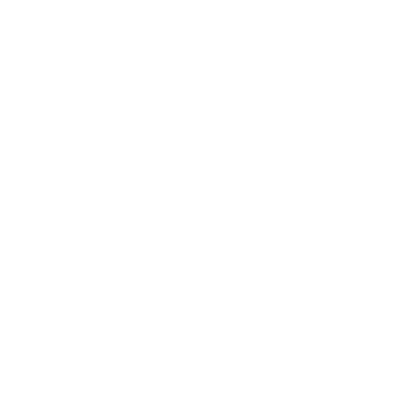
How to Maintain Your Dental Ceramic Furnace
The dental furnaces are expensive and require regular maintenance to ensure they function properly and produce accurate results.
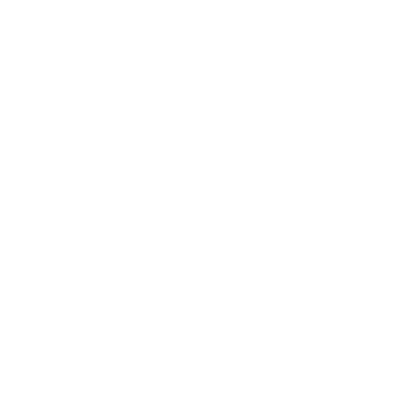
6 Ways To activated carbon regeneration
Activated Carbon Regeneration: Thermal Regeneration Method, Biological Regeneration Method, Wet Oxidation Regeneration Method, Solvent Regeneration Method, Electrochemical Regeneration Method, Catalytic Wet Oxidation Method
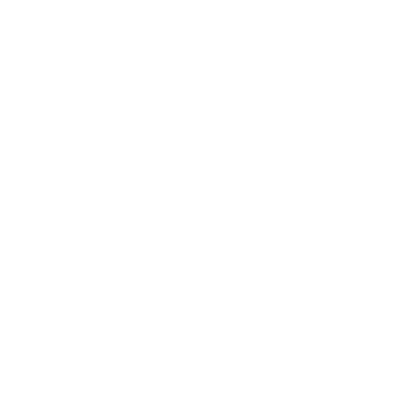
Melting process and maintenance of vacuum induction melting furnace
Melting process and maintenance of vacuum induction melting furnace
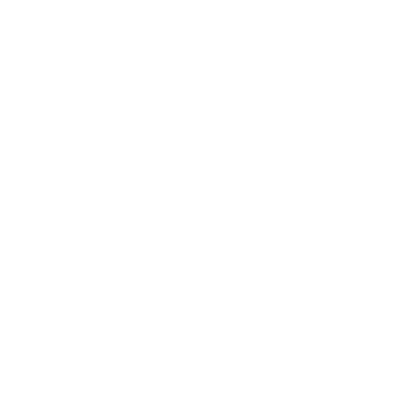
How Biomass Pyrolysis Machines Work A Comprehensive Overview
Biomass pyrolysis machines are designed to convert biomass materials into useful products such as biochar, bio-oil, and syngas.
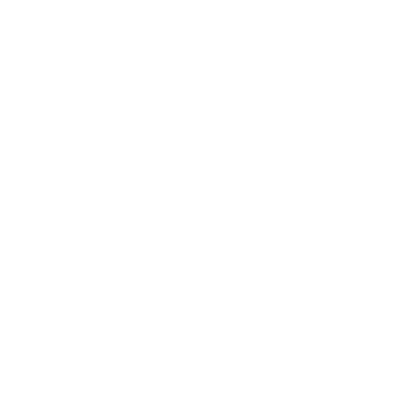
The Importance of Activated Carbon Regeneration in Water Treatment
In water treatment, activated carbon is often used as a means of removing unwanted contaminants, such as chlorine, chloramines, and organic matter, from drinking water and wastewater.