Activated carbon regeneration furnace is a type of equipment used to regenerate or reactivate spent or used activated carbon. Activated carbon is a type of carbon that has been processed to have a high surface area and high pore structure, making it highly effective at adsorbing impurities and contaminants from gases and liquids. It is commonly used in a variety of applications, including water purification, air purification, and the removal of contaminants from industrial process streams.
Activated carbon becomes less effective at adsorbing impurities over time as it becomes saturated with contaminants. When this happens, the activated carbon must be regenerated to restore its adsorption capacity. This is typically done by heating the used activated carbon in a regeneration furnace to a high temperature in the presence of an oxidizing agent, such as oxygen or steam. The heat and oxidizing agent work together to remove the impurities and contaminants from the activated carbon, allowing it to be reused.
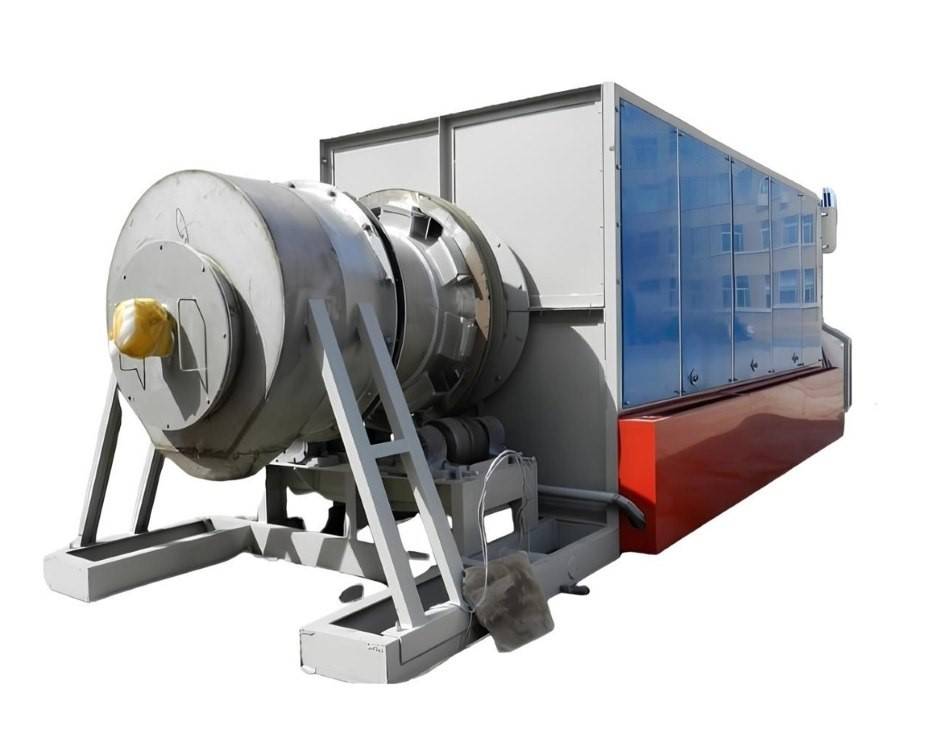
Activated carbon regeneration furnaces come in a variety of sizes and designs, and can be used in both batch and continuous processes. They are an important piece of equipment in industries that rely on activated carbon for purification and contaminant removal.
The activated carbon regeneration furnace is the key equipment in the activated carbon regeneration system. The choice of the activated carbon regeneration furnace has a great influence on the cost and performance of the activated carbon regeneration system.
There are many types of furnaces that can be used for heating and regeneration of granular carbon. The most common type of furnace is the rotary furnace, which uses a rotating chamber to evenly heat the carbon. Moving bed furnaces use a slowly moving bed of carbon to achieve evenly heating, while fluidized bed furnaces use a bed of carbon that is constantly in motion, allowing for even heating. Vertical multi-stage furnaces are less common, but they offer the advantage of being able to heat the carbon more slowly and evenly, resulting in less damage to the carbon.
Electric activated carbon regeneration furnace is one typical electric external heating rotary furnace
Here we mainly introduce the activated carbon rotary furnace
Application of rotary furnace
A rotary furnace is a type of industrial furnace that is used in many industries, such as the cement and metallurgical industries. They are generally large in scale and can be used for a variety of purposes. In recent years, rotary furnaces have often been used as activated carbon regeneration furnaces. This is because they are able to reach high temperatures quickly and evenly, which is necessary for this type of regeneration. Additionally, rotary furnaces are very durable and can withstand the high temperatures and pressures that are often required in these industries.
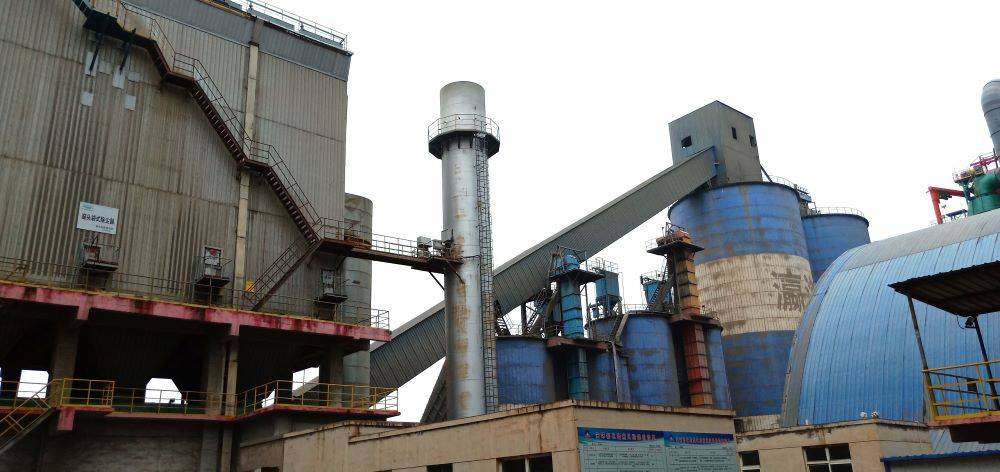
The structure of the rotary furnace
The inner wall of the drum is commonly lined with refractory bricks. The activated carbon passes through the rotary drum furnace, and the furnace body rotates intermittently or continuously to realize the constant temperature activation process of the activated carbon.A rotary furnace is a horizontal drum that is slightly inclined from the feed end to the discharge end. The residence time of the charcoal in the furnace is controlled by the inclination and the speed of the furnace body. There is a water vapor inlet in the activation area of the furnace body. There is a combustion flue gas outlet at the feed end of the furnace body. The inner wall of the drum is commonly lined with refractory bricks. The activated carbon passes through the rotary drum furnace, and the furnace body rotates intermittently or continuously to realize the constant temperature activation process of the activated carbon.
Internal heating type: In this type of rotary furnace, the heating is done by the hot gases generated inside the furnace. The advantage of this type of furnace is that the materials to be heated are directly exposed to the heated gases, resulting in a more efficient heat transfer. External heating type: In this type of rotary furnace, the heating is done by hot gases generated outside the furnace. The advantage of this type of furnace is that the materials to be heated are not directly exposed to the heated gases, resulting in a more uniform heat transfer. Combination of internal and external heating: In this type of rotary furnace, the heating is done by both the hot gases generated inside the furnace and the hot gases generated outside the furnace. The advantage of this type of furnace is that the materials to be heated are exposed to both the heated gases, resulting in a more efficient heat transfer.
The internal heating type rotary furnace has a large regeneration loss, and the furnace body is lined with refractory materials. The external heating type has a small regeneration loss, but the furnace body needs to be made of high temperature resistant materials. The internal heating type is more energy efficient, while the external heating type is better for large-scale production.
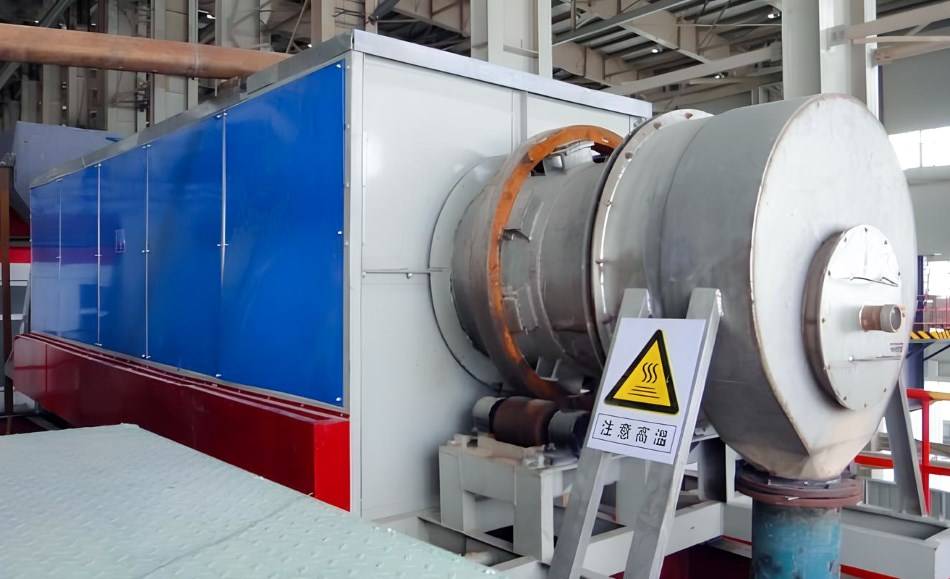
Advantage of Electric Activated Carbon Regeneration Furnace
There are several advantages to using an electric activated carbon regeneration furnace:
- Energy efficiency: Electric furnaces are generally more energy efficient than furnaces that use fossil fuels, such as natural gas or oil. This can result in lower energy costs and a smaller carbon footprint.
- Clean operation: Electric furnaces do not produce emissions, making them a cleaner and more environmentally friendly option.
- Safety: Electric furnaces do not produce flammable gases, which can be a safety hazard in some types of furnaces.
- Control: Electric furnaces can be more easily controlled and regulated, allowing for more precise temperature control and the ability to more accurately monitor the regeneration process.
- Maintenance: Electric furnaces typically require less maintenance and have a longer lifespan than furnaces that use fossil fuels.
- Cost: While the initial cost of an electric furnace may be higher than a fossil fuel furnace, the long-term operating costs may be lower due to the energy efficiency and lower maintenance requirements.
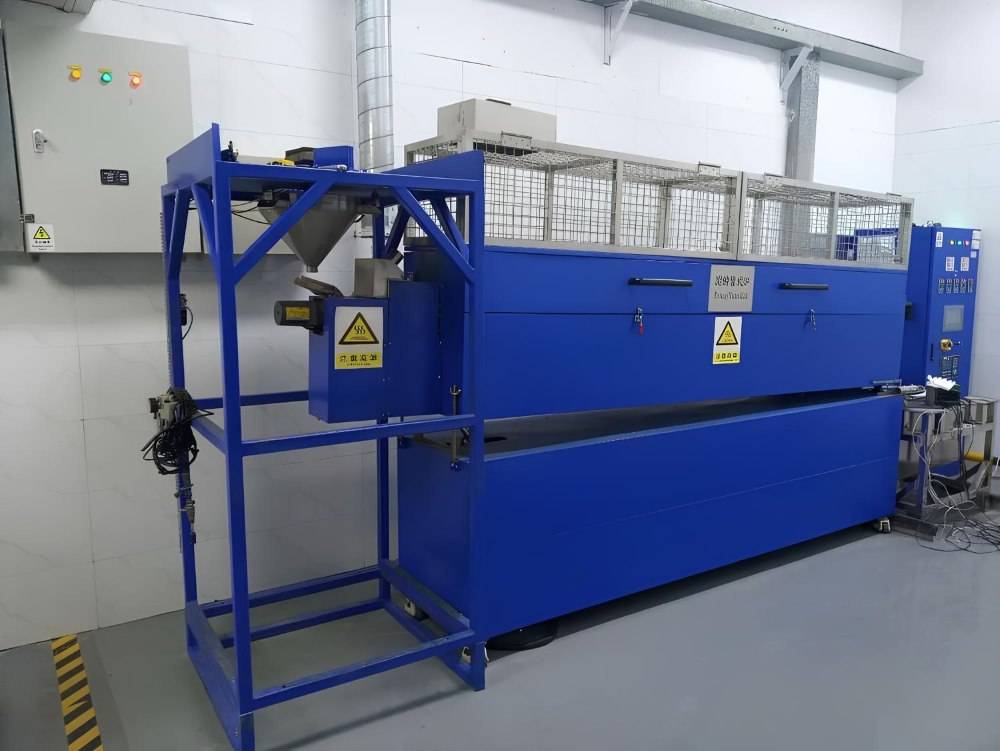
Overall, electric activated carbon regeneration furnaces offer a number of benefits, including improved energy efficiency, clean operation, safety, control, and reduced maintenance requirements.
CONTACT US FOR A FREE CONSULTATION
KINTEK LAB SOLUTION's products and services have been recognized by customers around the world. Our staff will be happy to assist with any inquiry you might have. Contact us for a free consultation and talk to a product specialist to find the most suitable solution for your application needs!