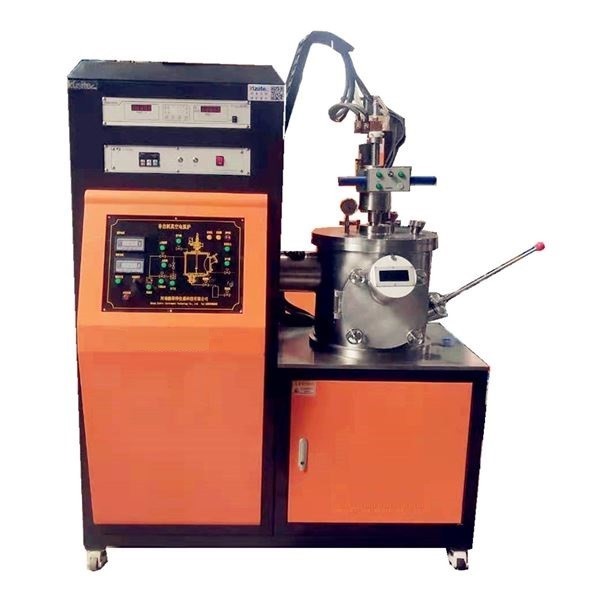
Vacuum Furnace
Non Consumable Vacuum Arc Induction Melting Furnace
Item Number : KT-VAN
Price varies based on specs and customizations
- Melting temperature
- 3500 ℃
- Vacuum pressure
- < 5 x10-3 Pa
- Melting capacity
- 20-500 g
- Rated melting current
- 200-1000 A
- Smelting station
- 5-7 standard smelting station
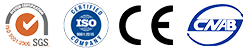
Shipping:
Contact us to get shipping details Enjoy On-time Dispatch Guarantee.
Why Choose Us
Reliable PartnerEasy ordering process, quality products, and dedicated support for your business success.
Applications
The electrode of non consumable vacuum arc furnace (also known as vacuum button furnace) is made of high melting point materials such as tungsten, which is basically not consumed in the furnace charge smelting process. At present, it is only used in the laboratory to research and manufacture refractory metals and metal carbides. It is one of the earliest vacuum arc furnaces. The furnace is small in size, small in floor space, easy to operate, and does not require professionals and professional skills. It is closed for operation, radiation free, harmless to human body, pollution-free to the environment, and fast in sample preparation. At present, it is mostly used in laboratory research to research and manufacture refractory metals and metal carbides.
Detail & Parts
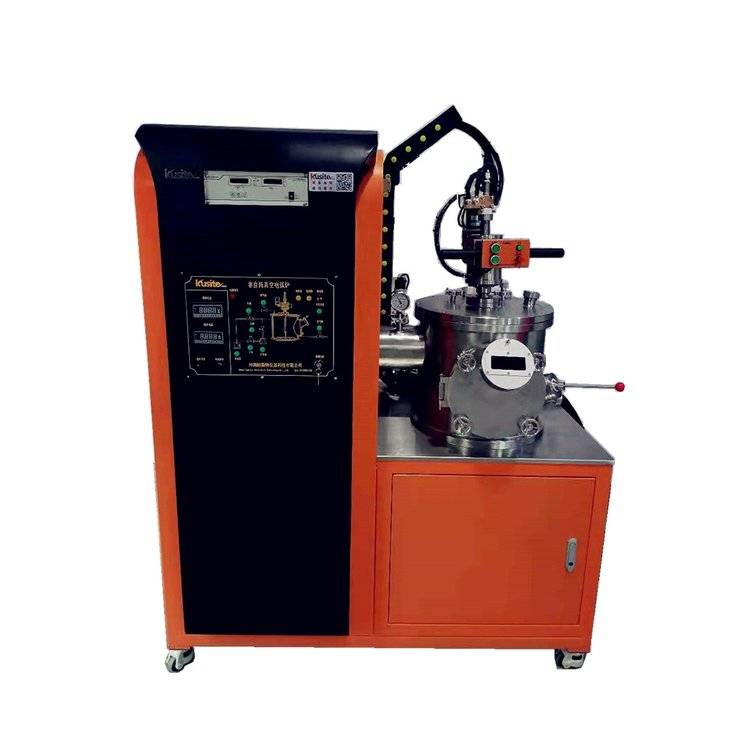
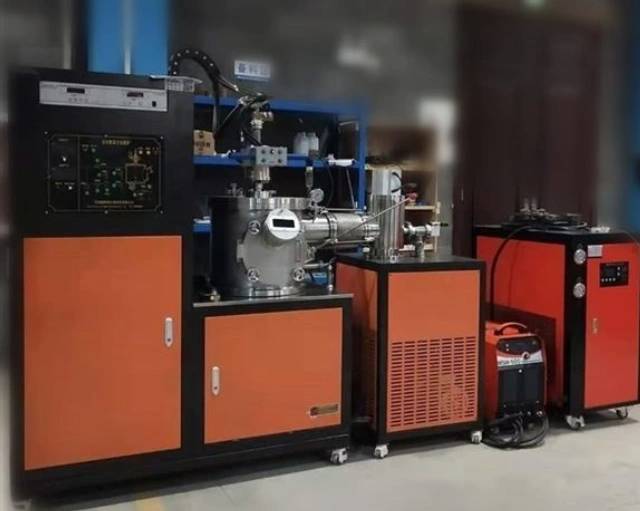
Features
- Small size, convenient operation, small floor space
- Melting temperature can reach above 3500 ℃
- The vacuum chamber is small, which can pump vacuum quickly and fill argon quickly, with fast efficiency and less argon consumption
- The water-cooled copper electrode can be moved for easy disassembly, and multiple samples can be smelted at the same time
- Sample diversity, which can be powder, filiform, chip, drilling cuttings, granular, strip, annular, sediment, etc
Component
Vacuum chamber, electric arc gun, electric arc smelting power supply, five station water-cooled copper crucible, turnover manipulator, vacuum suction casting device, working gas station, air extraction system, vacuum meter and electrical control system.
Technical specifications
Melting temperature | 3500 ℃ |
Vacuum chamber | 304 stainless steel |
Vacuum pressure | < 5 x10-3Pa |
Melting capacity | 20-500g |
Rated melting current | 200-1000A |
Smelting station | 5-7 standard smelting station |
Insert working gas | Ar |
Optional function | Suction casting/Extra smelting station |
Warnings
Operator safety is the top important issue! Please operate the equipment with cautions. Working with inflammable& explosive or toxic gases is very dangerous, operators must take all necessary precautions before starting the equipment. Working with positive pressure inside the reactors or chambers is dangerous, operator must fellow the safety procedures strictly. Extra caution must also be taken when operating with air-reactive materials, especially under vacuum. A leak can draw air into the apparatus and cause a violent reaction to occur.
Designed for You
KinTek provide deep custom made service and equipment to worldwide customers, our specialized teamwork and rich experienced engineers are capable to undertake the custom tailoring hardware and software equipment requirements, and help our customer to build up the exclusive and personalized equipment and solution!
Would you please drop your ideas to us, our engineers are ready for you now!
4.9
out of
5
The vacuum induction melting furnace is a top-notch piece of equipment. It's incredibly efficient and produces high-quality alloys. Highly recommend!
4.8
out of
5
I'm amazed by the speed and precision of this furnace. It's a game-changer for our research lab, enabling us to conduct experiments more efficiently.
4.7
out of
5
The Non-Consumable Vacuum Arc Furnace is a valuable addition to our lab. It's user-friendly, delivers consistent results, and has significantly improved our research capabilities.
4.9
out of
5
The Induction Melting Furnace has exceeded our expectations. It's a versatile and reliable piece of equipment that has streamlined our alloy production process. Highly satisfied!
4.8
out of
5
The Vacuum Arc Furnace is a remarkable piece of technology. It allows us to create alloys with exceptional purity and precision. Truly a game-changer for our research.
4.7
out of
5
The Induction Melting Furnace has revolutionized our alloy production process. It's efficient, reliable, and produces high-quality alloys consistently. Highly recommend!
4.9
out of
5
The Non-Consumable Vacuum Arc Furnace is a must-have for any research lab working with high-temperature materials. It's a powerful and versatile tool that has enabled us to make significant breakthroughs in our research.
4.8
out of
5
The Vacuum Induction Melting Furnace has been a game-changer for our research. It allows us to create alloys with precise compositions and exceptional purity. Highly satisfied with its performance.
4.7
out of
5
The Induction Melting Furnace is a reliable and efficient piece of equipment. It has significantly improved our productivity and enabled us to produce high-quality alloys consistently.
4.9
out of
5
The Non-Consumable Vacuum Arc Furnace is an incredible piece of technology. It's incredibly versatile and allows us to create alloys with unique properties. Highly recommend it for advanced research.
4.8
out of
5
The Vacuum Induction Melting Furnace has enabled us to achieve exceptional results in our research. It's a powerful and reliable tool that has opened up new possibilities for our team.
4.7
out of
5
The Induction Melting Furnace has been an excellent addition to our lab. It's easy to use, produces consistent results, and has significantly improved our efficiency. Highly recommend!
4.9
out of
5
The Non-Consumable Vacuum Arc Furnace is a remarkable piece of equipment. It's incredibly precise and allows us to create alloys with exceptional purity. Highly satisfied with its performance.
4.8
out of
5
The Vacuum Induction Melting Furnace has been a game-changer for our research. It's a versatile and powerful tool that has enabled us to make significant breakthroughs in our field.
4.7
out of
5
The Induction Melting Furnace is an excellent choice for labs working with high-temperature materials. It's reliable, efficient, and produces high-quality alloys consistently. Highly recommend!
Products
Non Consumable Vacuum Arc Induction Melting Furnace
REQUEST A QUOTE
Our professional team will reply to you within one business day. Please feel free to contact us!
Related Products
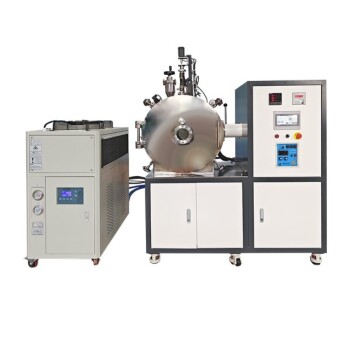
Lab-Scale Vacuum Induction Melting Furnace
Get precise alloy composition with our Vacuum Induction Melting Furnace. Ideal for aerospace, nuclear energy, and electronic industries. Order now for effective smelting and casting of metals and alloys.
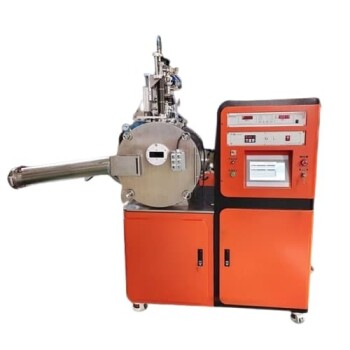
Vacuum Induction Melting Spinning System Arc Melting Furnace
Develop metastable materials with ease using our Vacuum Melt Spinning System. Ideal for research and experimental work with amorphous and microcrystalline materials. Order now for effective results.
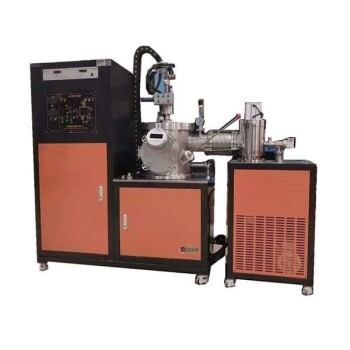
Vacuum Arc Induction Melting Furnace
Discover the power of Vacuum Arc Furnace for melting active & refractory metals. High-speed, remarkable degassing effect, and free of contamination. Learn more now!
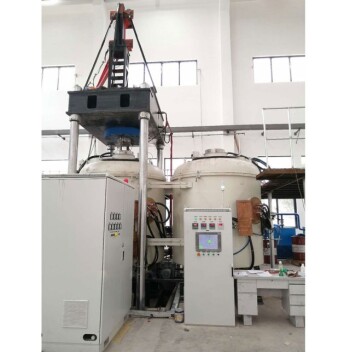
600T Vacuum Induction Hot Press Furnace for Heat Treat and Sintering
Discover the 600T Vacuum Induction Hot Press Furnace, designed for high-temperature sintering experiments in vacuum or protected atmospheres. Its precise temperature and pressure control, adjustable working pressure, and advanced safety features make it ideal for nonmetal materials, carbon composites, ceramics, and metal powders.
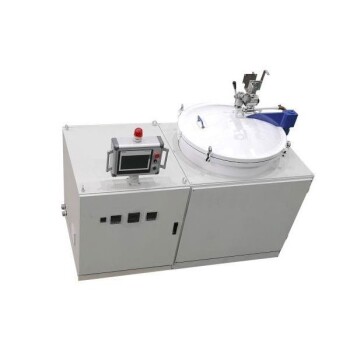
Graphite Vacuum Furnace IGBT Experimental Graphitization Furnace
IGBT experimental graphitization furnace, a tailored solution for universities and research institutions, with high heating efficiency, user-friendliness, and precise temperature control.
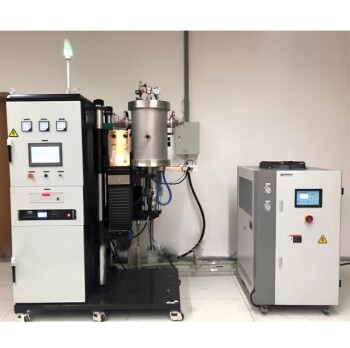
Vacuum Heat Treat and Molybdenum Wire Sintering Furnace for Vacuum Sintering
A vacuum molybdenum wire sintering furnace is a vertical or bedroom structure, which is suitable for withdrawal, brazing, sintering and degassing of metal materials under high vacuum and high temperature conditions. It is also suitable for dehydroxylation treatment of quartz materials.
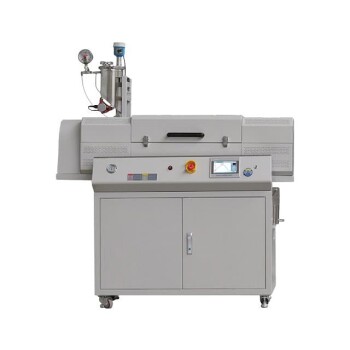
Laboratory Vacuum Tilt Rotary Tube Furnace Rotating Tube Furnace
Discover the versatility of Laboratory Rotary Furnace: Ideal for calcination, drying, sintering, and high-temperature reactions. Adjustable rotating and tilting functions for optimal heating. Suitable for vacuum and controlled atmosphere environments. Learn more now!
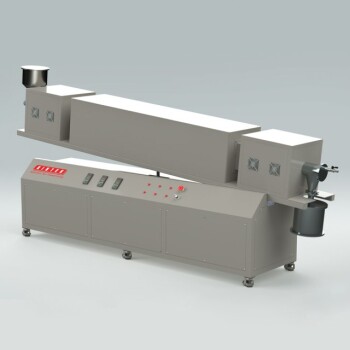
Vacuum Sealed Continuous Working Rotary Tube Furnace Rotating Tube Furnace
Experience efficient material processing with our vacuum-sealed rotary tube furnace. Perfect for experiments or industrial production, equipped with optional features for controlled feeding and optimized results. Order now.
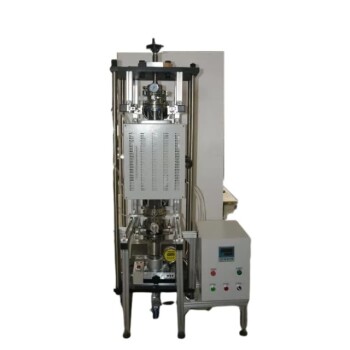
Vacuum Hot Press Furnace Heated Vacuum Press Machine Tube Furnace
Reduce forming pressure & shorten sintering time with Vacuum Tube Hot Press Furnace for high-density, fine-grain materials. Ideal for refractory metals.
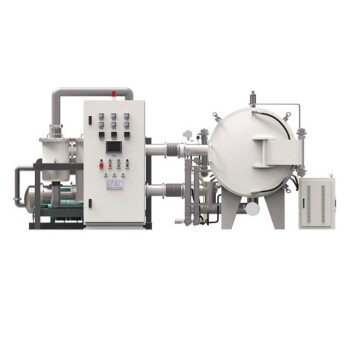
Horizontal High Temperature Graphite Vacuum Graphitization Furnace
Horizontal Graphitization Furnace: This type of furnace is designed with the heating elements placed horizontally, allowing for uniform heating of the sample. It's well-suited for graphitizing large or bulky samples that require precise temperature control and uniformity.
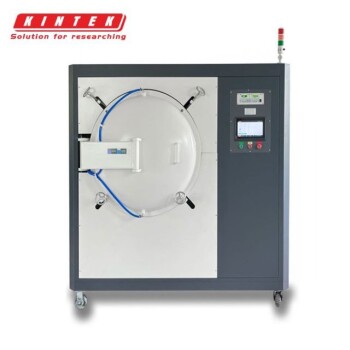
Vacuum Heat Treat Furnace with Ceramic Fiber Liner
Vacuum furnace with polycrystalline ceramic fiber insulation liner for excellent heat insulation and uniform temperature field. Choose from 1200℃ or 1700℃ max. working temperature with high vacuum performance and precise temperature control.
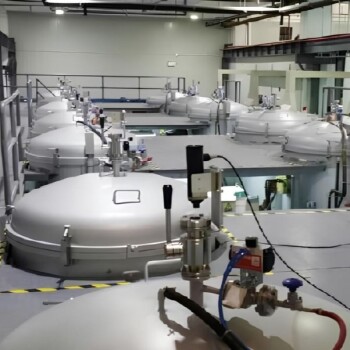
Graphite Vacuum Furnace High Thermal Conductivity Film Graphitization Furnace
The high thermal conductivity film graphitization furnace has uniform temperature, low energy consumption and can operate continuously.
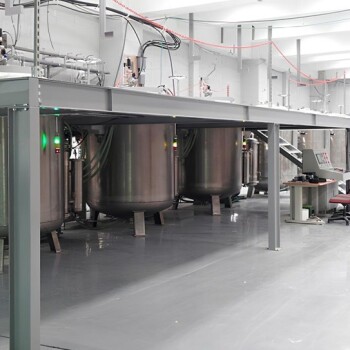
Graphite Vacuum Furnace Negative Material Graphitization Furnace
Graphitization furnace for battery production has uniform temperature and low energy consumption. Graphitization furnace for negative electrode materials: an efficient graphitization solution for battery production and advanced functions to enhance battery performance.
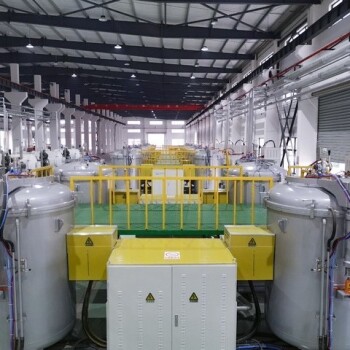
Vertical High Temperature Graphite Vacuum Graphitization Furnace
Vertical high temperature graphitization furnace for carbonization and graphitization of carbon materials up to 3100℃.Suitable for shaped graphitization of carbon fiber filaments and other materials sintered in a carbon environment.Applications in metallurgy, electronics, and aerospace for producing high-quality graphite products like electrodes and crucibles.

Graphite Vacuum Furnace Bottom Discharge Graphitization Furnace for Carbon Materials
Bottom-out graphitization furnace for carbon materials, ultra-high temperature furnace up to 3100°C, suitable for graphitization and sintering of carbon rods and carbon blocks. Vertical design, bottom discharging, convenient feeding and discharging, high temperature uniformity, low energy consumption, good stability, hydraulic lifting system, convenient loading and unloading.
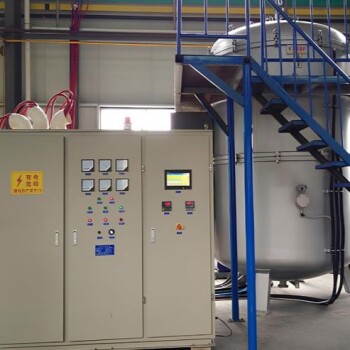
Large Vertical Graphite Vacuum Graphitization Furnace
A large vertical high-temperature graphitization furnace is a type of industrial furnace used for the graphitization of carbon materials, such as carbon fiber and carbon black. It is a high-temperature furnace that can reach temperatures of up to 3100°C.
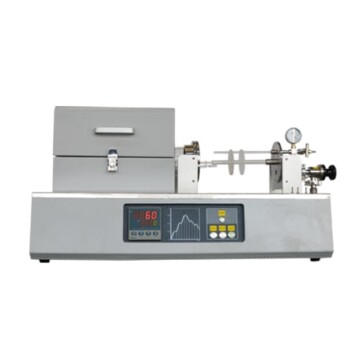
Laboratory Quartz Tube Furnace Tubular RTP Heating Furnace
Get lightning-fast heating with our RTP Rapid Heating Tube Furnace. Designed for precise, high-speed heating and cooling with convenient sliding rail and TFT touch screen controller. Order now for ideal thermal processing!
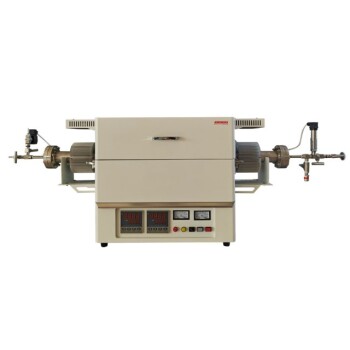
High Pressure Laboratory Vacuum Tube Furnace Quartz Tubular Furnace
KT-PTF High Pressure Tube Furnace: Compact split tube furnace with strong positive pressure resistance. Working temp up to 1100°C and pressure up to 15Mpa. Also works under controller atmosphere or high vacuum.
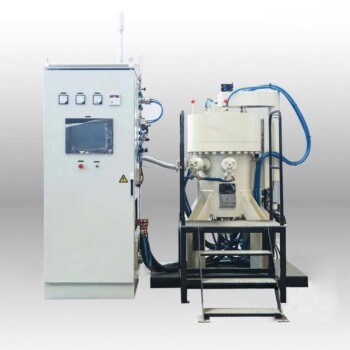
Vacuum Heat Treat and Sintering Furnace with 9MPa Air Pressure
The air pressure sintering furnace is a high-tech equipment commonly used for the sintering of advanced ceramic materials. It combines vacuum sintering and pressure sintering techniques to achieve high-density and high-strength ceramics.
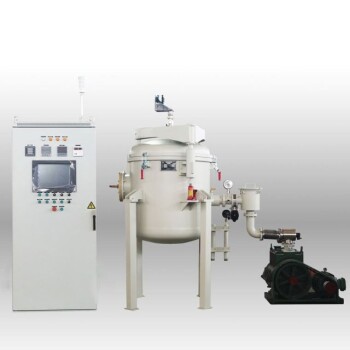
Ultra-High Temperature Graphite Vacuum Graphitization Furnace
The ultra-high temperature graphitization furnace utilizes medium frequency induction heating in a vacuum or inert gas environment. The induction coil generates an alternating magnetic field, inducing eddy currents in the graphite crucible, which heats up and radiates heat to the workpiece, bringing it to the desired temperature. This furnace is primarily used for graphitization and sintering of carbon materials, carbon fiber materials, and other composite materials.
Related Articles
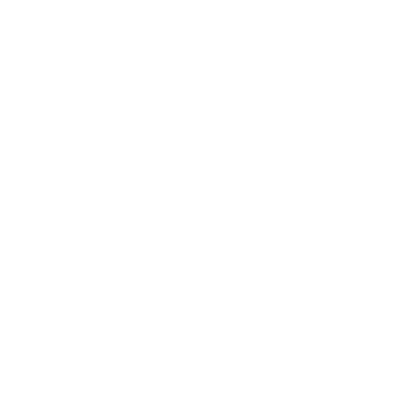
Vacuum Induction Melting Furnace: Principle, Advantages, and Applications
Discover the Vacuum Induction Melting Furnace, a specialized equipment that employs vacuum and induction heating to refine metals and alloys, ensuring high purity and precise composition control. Explore its principle, advantages, applications, and components in this comprehensive guide.
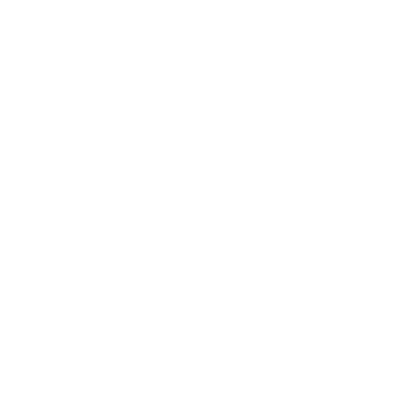
Vacuum Induction Melting Furnace vs Arc Melting Furnace: Choosing the Right Equipment for Your Process
Learn about the key differences between vacuum induction melting furnaces and arc melting furnaces, including their advantages and applications, to help you choose the best equipment for your specific needs.
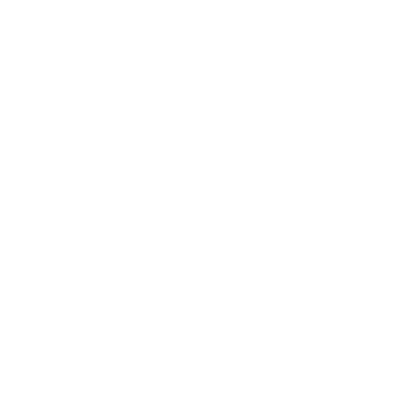
Exploring Tungsten Vacuum Furnaces: Operation, Applications, and Advantages
Discover the operation, applications, and benefits of tungsten vacuum furnaces in laboratory settings. Learn about KinTek's advanced features, control mechanisms, and the use of tungsten in high-temperature environments.
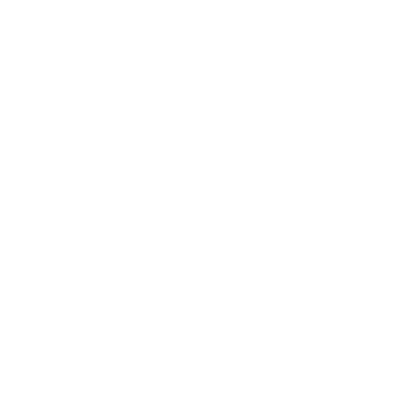
Vacuum Melting Furnace: A Comprehensive Guide to Vacuum Induction Melting
Discover the intricacies of vacuum induction melting furnaces, their components, operation, advantages, and applications. Explore how these furnaces revolutionize metal processing and achieve exceptional material properties.
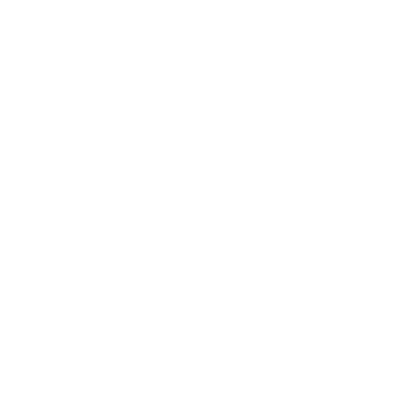
Unlocking the Potential: Vacuum Levitation Induction Melting Furnace Explained
Discover the working principles, applications, and advantages of vacuum levitation induction melting furnaces. Learn how this technology revolutionizes metal smelting, ensuring purity, efficiency, and environmental friendliness.
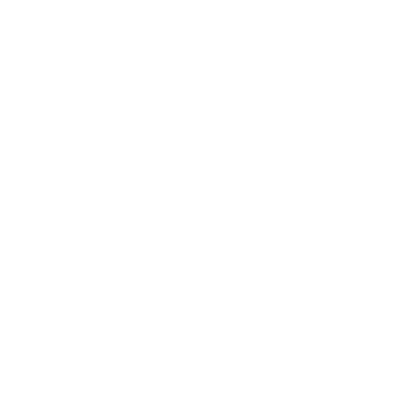
Exploring the Benefits of Using Tungsten for Furnace Heating
Tungsten has a number of properties that make it well-suited for use in high-temperature furnaces.
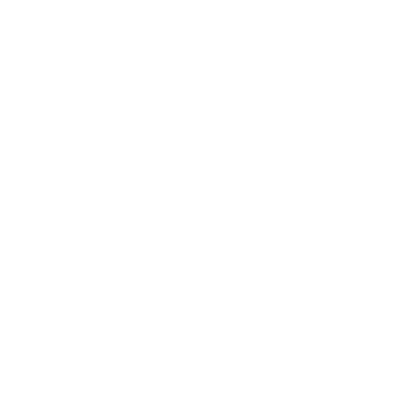
Melting process and maintenance of vacuum induction melting furnace
Melting process and maintenance of vacuum induction melting furnace
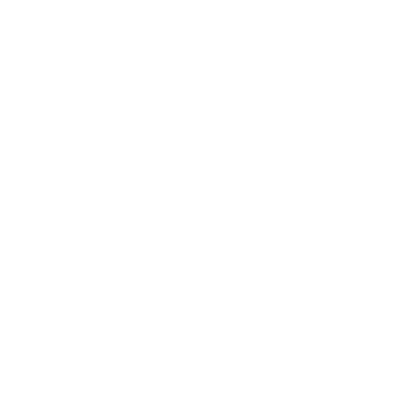
Environmental Benefits of Using an Atmosphere Furnace
Inert atmosphere furnaces are designed to provide a controlled environment for high-temperature processing of materials.
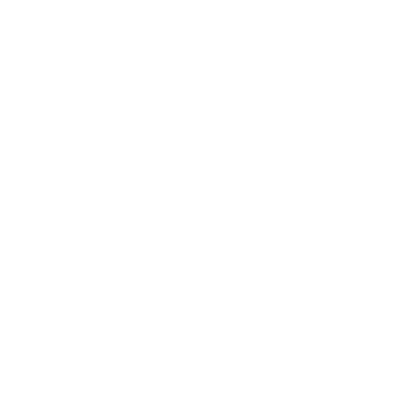
Electrode Fixture Guide: Types, Design, and Applications
Discover the comprehensive guide to electrode fixtures, covering various types, design considerations, and their indispensable role in industries like electroplating, welding, and electrochemical cells.
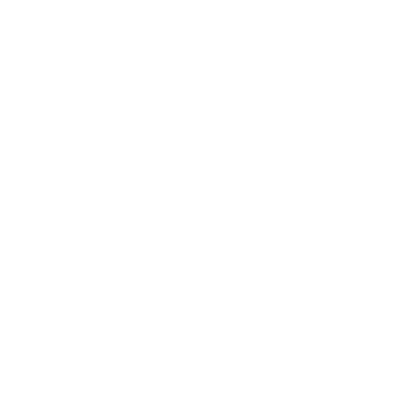
The Benefits of Controlled Atmosphere Furnaces for Sintering and Annealing Processes
They are essential in preventing oxidation, reducing the risk of contamination, and improving the properties of the materials being treated.
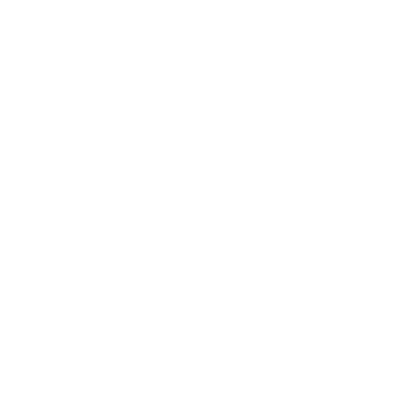
What is activated carbon regeneration Rotary Furnace
Electric activated carbon regeneration furnace is one typical electric external heating rotary furnace
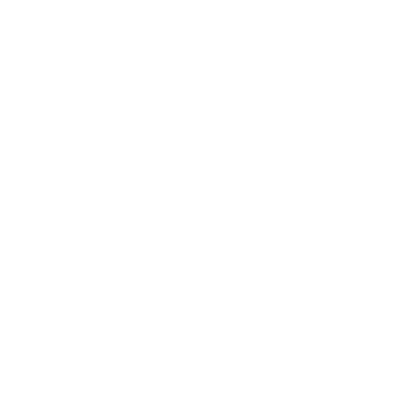
Vacuum Furnace Types and Applications
Overview of different vacuum furnace types and their uses in various heat treatment processes.