Introduction to the Importance of Furnace Atmospheres
Furnace atmospheres play a crucial role in various heat treatment processes such as sintering and annealing. They are essential in preventing oxidation, reducing the risk of contamination, and improving the properties of the materials being treated. An inert atmosphere furnace, for example, is designed to maintain a controlled environment that is free of oxygen, moisture, and other impurities. This type of furnace is used in applications that require high-temperature processing of materials, such as ceramics, metals, and composites. The use of controlled atmosphere furnaces can result in improved material quality, increased efficiency, and reduced costs.
Table of Contents
- Introduction to the Importance of Furnace Atmospheres
- What is an Inert Atmosphere Furnace?
- Use of Inert Atmosphere Furnaces for Sintering and Annealing
- Benefits of Controlled Atmosphere Furnaces
- Improved Environmental Conditions
- Better Furnace Control and Efficient Throughput
- Two Major Categories: Batch and Continuous Furnaces
- Atmosphere Furnaces by KINTEK
- Conclusion
What is an Inert Atmosphere Furnace?
An inert atmosphere furnace is a type of laboratory equipment used for sintering and annealing processes. It provides a controlled, oxygen-free environment that is essential for certain high-temperature applications. Inert means chemically inactive, which is why inert atmospheres are necessary for chemical processes that require no reactive gas contamination.
How Does an Inert Atmosphere Furnace Work?
Inert atmosphere furnaces operate by removing oxygen and other reactive gases from the environment. This is achieved by purging the furnace with an inert gas, such as nitrogen or argon. The furnace is then heated to the desired temperature, and the material to be sintered or annealed is placed inside. The furnace is sealed to maintain the inert atmosphere, which allows the material to undergo the heating and cooling process without any oxidation or other chemical reactions.
Why Does a Process Require an Inert Atmosphere Furnace?
Many heat treatment processes require a highly controlled atmosphere to achieve the desired outcome. For example, sintering, bright annealing, and carbonitriding are processes used to manufacture parts for various industries. These processes require atmospheres that are highly controlled to ensure a successful outcome. Inert atmospheres, such as those created by an inert atmosphere furnace, are necessary to avoid chemical reactions like decarburization or oxidation that could negatively impact the quality and performance of the finished product.
The Importance of Inert Atmosphere Gases
Inert atmosphere gases are essential for creating the controlled environment required for sintering and annealing processes. Nitrogen, helium, and argon are commonly used to create inert atmospheres because they are chemically stable and have a low reactivity. By using these gases, researchers and manufacturers can create a stable, oxygen-free environment that allows for precise control over the heating and cooling of materials.
In conclusion, an inert atmosphere furnace is a critical piece of equipment for researchers and manufacturers working with high-temperature materials. By providing a stable, oxygen-free environment for sintering and annealing processes, inert atmosphere furnaces can help achieve better results and more consistent production outcomes.
Use of Inert Atmosphere Furnaces for Sintering and Annealing
Inert atmosphere furnaces are widely used in sintering and annealing processes to create an environment that is free from reactive gases. The use of inert gas, such as argon or nitrogen, creates a stable and consistent atmosphere that reduces the likelihood of unwanted reactions during the sintering or annealing process.
Benefits of using inert atmosphere furnaces
The use of inert atmosphere furnaces offers several benefits. One of the most significant benefits is improved product quality. By creating a stable and consistent atmosphere, inert atmosphere furnaces can help to produce high-quality end products with fewer defects.
Another benefit is increased production efficiency. Inert atmosphere furnaces can help to reduce processing time and improve manufacturing throughput. This is achieved by minimizing the need for rework and increasing the yield of high-quality products.
Reduction of contamination and oxidation
Inert atmosphere furnaces can also minimize contamination and oxidation, which can have a significant impact on the final properties of the product. The use of a controlled atmosphere helps to reduce the likelihood of contamination from external sources, and it also prevents oxidation of the product during the sintering or annealing process.
Versatility in materials
Inert atmosphere furnaces can be used for a wide range of materials, including metals, ceramics, and composites, making them an essential tool for many industries. The ability to use these furnaces for different materials provides manufacturers with more flexibility when it comes to product design and production.
Benefits of Controlled Atmosphere Furnaces
Controlled atmosphere furnaces offer several benefits for laboratory technicians, making them an essential tool in sintering and annealing processes.
Tailored Environment for Specific Applications
One of the most significant benefits of controlled atmosphere furnaces is the ability to create a specific environment that can be tailored to a particular application. By controlling the gas composition, temperature, and pressure inside the furnace, laboratory technicians can manipulate the chemical reactions that occur during sintering and annealing, improving the quality and consistency of the end product.
Prevention of Oxidation
Controlled atmosphere furnaces can be used to prevent the oxidation of sensitive materials by removing oxygen from the environment. This reduces the risk of contamination and improves product purity.
High-Temperature Processing
Another benefit of controlled atmosphere furnaces is their ability to operate at high temperatures, providing greater flexibility in the materials that can be processed. These furnaces are commonly used in the production of ceramics, metals, and semiconductors, where high temperatures are required to achieve the desired properties.
Precise Control for Accurate and Reproducible Results
The precise control offered by controlled atmosphere furnaces means that laboratory technicians can achieve more accurate and reproducible results. This reduces the risk of errors and improves the overall quality of their research.
Superior to Box and Salt Bath Furnaces
Controlled atmosphere furnaces have now largely superseded box (pack carburizing) and salt bath furnaces on the basis that they exhibit better furnace control, more efficient throughput, and are less labor demanding. They also offer much-improved environmental conditions of operation without the serious problems of land contamination with toxic salts (cyanides) and the difficulties of disposing of waste salts, contaminated jigs and fixtures and pack carburizing waste.
Overall, the benefits of controlled atmosphere furnaces make them an indispensable tool for laboratories working in materials science, chemistry, and engineering.
Improved Environmental Conditions
Controlled atmosphere furnaces are designed to create an environment where materials can be heated precisely and without any unwanted contamination. One of the main benefits of using a controlled atmosphere furnace is the improved environmental conditions it provides. By controlling the atmosphere within the furnace, it's possible to reduce the amount of oxygen and moisture present, which can have a significant impact on the quality of the finished product.
Reduced Oxygen Levels
By reducing the amount of oxygen present during the sintering or annealing process, it's possible to prevent oxidation, which can lead to a weaker, less durable final product. When oxygen levels are high, it can react with many chemical elements at varying temperatures, causing oxidation. With a controlled atmosphere furnace, oxygen levels can be reduced to prevent this from happening. Nitrogen is considered a chemically inert carrier gas of air and is often used as a reducing gas to prevent material oxidation in high temp furnaces. This blanketing process is accomplished using gas inlets such as nitrogen flowmeters and an exhaust port to expel spent gas from the chamber via a fume hood or an external manifold piping.
Reduced Moisture Levels
Similarly, by controlling the amount of moisture present, it's possible to prevent the formation of unwanted chemical compounds, which can also affect the quality of the finished product. Moisture can cause unwanted chemical reactions during the annealing process, which can affect the final product's quality. By using a controlled atmosphere furnace, moisture levels can be reduced, ensuring that the final product is of high quality.
Increased Efficiency and Productivity
In addition to these environmental benefits, controlled atmosphere furnaces also offer increased efficiency and productivity, as well as greater flexibility and control over the entire sintering or annealing process. By using a controlled atmosphere furnace, it's possible to create an environment that is more conducive to the heating process, which can lead to faster and more efficient heating. This, in turn, can help to increase productivity and reduce costs.
Better Furnace Control and Efficient Throughput
Controlled Atmosphere Furnaces (CAFs) offer several benefits over traditional furnaces, including better control over the furnace environment and more efficient throughput. CAFs are designed to operate in environments with controlled levels of oxygen, nitrogen, or other gases, which can be adjusted based on the specific needs of the process.
Precise Control of Furnace Environment
One of the major advantages of CAFs is their ability to offer precise control over the furnace environment. This level of control can lead to better product quality, as it allows for more precise control of the sintering or annealing process. CAFs can operate in environments with controlled levels of oxygen, nitrogen, or other gases. This level of control can lead to better product quality, as it allows for more precise control of the sintering or annealing process.
Improved Efficiency
Another advantage of CAFs is their ability to process materials at higher temperatures than traditional furnaces, which can lead to faster processing times and increased efficiency. CAFs can often process materials at higher temperatures than traditional furnaces, which can lead to faster processing times and increased efficiency. This is particularly important for processes that require high-temperature processing, such as sintering and annealing.
Reduced Oxidation
CAFs also have the ability to reduce the amount of oxidation that occurs during the sintering or annealing process, which can help to preserve the integrity of the material being processed. This can be particularly important for materials that are sensitive to oxidation, such as certain metals or ceramics.
Consistent Quality of Output
The precise control of the furnace environment in CAFs leads to a consistent quality of output, which is vital to applications in research and development as well as industrial manufacturing. The ability to control the levels of oxygen, nitrogen, or other gases during the sintering or annealing process ensures that the end product meets the desired quality standards.
Conclusion
In conclusion, CAFs offer a range of benefits over traditional furnaces for sintering and annealing processes. They provide better control over the furnace environment, improved efficiency, reduced oxidation, and consistent quality of output. These benefits make CAFs an ideal choice for a wide range of applications, from research and development to industrial manufacturing.
Two Major Categories: Batch and Continuous Furnaces
Controlled atmosphere furnaces are essential laboratory equipment used for sintering and annealing processes in many industries. There are two major categories of controlled atmosphere furnaces: batch and continuous furnaces.
Batch Furnaces
Batch furnaces are suitable for small quantities of products, and the material is loaded into the furnace in a batch and heated to the desired temperature for a specific period. The batch furnace is a single chamber furnace that is loaded, heated, and unloaded as a batch. The temperature, gas composition, and pressure are all set for the entire batch process. The batch furnace is ideal for small-scale production and research, and it is also suitable for materials that require a specific temperature and atmosphere for a specific period.
Continuous Furnaces
On the other hand, continuous furnaces are suitable for large quantities of products that require a continuous flow of material through the furnace. In continuous furnaces, the material is loaded at one end and transported through the furnace by a conveyor system. The conveyor system is designed to provide a continuous flow of material through the furnace. The temperature, gas composition, and pressure are controlled throughout the entire process. Continuous furnaces are ideal for high-volume production and are commonly used in the automotive, aerospace, and electronics industries.
Both batch and continuous furnaces offer several benefits. The controlled atmosphere furnaces can significantly improve the quality of the final product. The benefits of using these furnaces include reduced oxidation, improved material properties, and increased product yield. Controlled atmosphere furnaces can also enhance the uniformity of the product, reduce energy consumption, and minimize contamination and waste.
In conclusion, controlled atmosphere furnaces play a critical role in various industries, and they offer a range of benefits for sintering and annealing processes. The choice between batch and continuous furnaces depends on the specific needs of the industry or laboratory. The batch furnace is suitable for small-scale production and research, while the continuous furnace is ideal for high-volume production. Both types of furnaces are designed to provide a controlled environment that enhances material properties and minimizes oxidation.
Atmosphere Furnaces by KINTEK
Atmosphere furnaces are essential for sintering and annealing processes in a laboratory setting. KINTEK, a leading manufacturer of laboratory equipment, offers atmosphere furnaces that provide a precisely controlled environment for sintering and annealing processes to ensure the highest quality results possible.
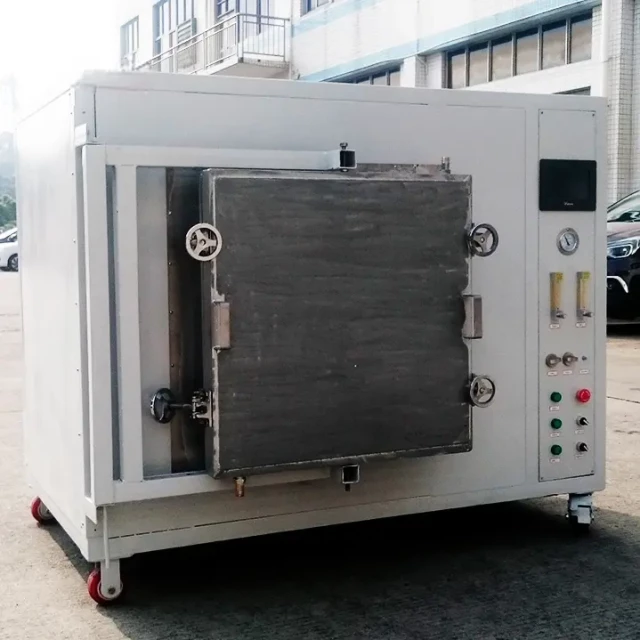
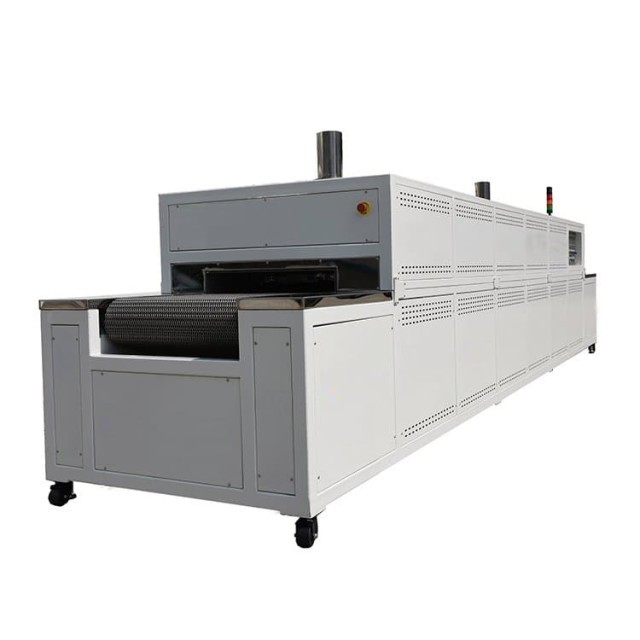
Features of KINTEK Atmosphere Furnaces
KINTEK's atmosphere furnaces are designed to meet the unique specifications of the customer. These furnaces have a range of heating zone sizes and working temperature ranges (1100°C, 1300°C, and 1600°C), making them ideal for use in a wide range of applications, from metallurgy and materials science to semiconductor processing and electronics manufacturing.
Controlled Atmosphere
Atmosphere furnaces operate by controlling the environment in which samples are heated, creating a specific atmosphere that can significantly affect the final properties of the material being processed. KINTEK's atmosphere furnaces come with several patented features that enable better mixing, resulting in improved heat transfer and mass transfer. The absence of moving parts in the tube support system provides a simple, reliable, and robust design that enhances scalability. Additionally, the tumbling action of the product within the tube results in high degrees of temperature uniformity and gas-solid contact, producing a more homogeneous product, reducing processing times, and increasing production rates.
Process Atmospheres
KINTEK's atmosphere furnaces can accommodate a variety of process atmospheres. The company's excellent seal designs and focus on atmosphere control include system integration of atmosphere recycle systems, off-gas abatement systems, and controlled atmosphere mixing for tailored process control. These atmospheres include flammables and toxic gases such as hydrogen, nitrogen, argon, air, oxygen, ethylene, methane, CO2, CO, and chlorine gas.
Customization
KINTEK approaches the design of an atmosphere furnace as a complete system, with the ability to incorporate process control systems, gas treatment and handling, turnkey installation, and complete field commissioning. The company also offers customized high-temperature laboratory furnaces that provide excellent temperature control and uniformity, as well as energy efficiency. These furnaces can be modified from a standard model or built to a customer's exact specifications.
In conclusion, KINTEK's atmosphere furnaces are an excellent choice for any laboratory looking to improve the quality and consistency of their work. These furnaces offer a precisely controlled environment for sintering and annealing processes, reducing oxidation, controlling the formation of phases, and improving the overall quality and consistency of the final product.
Conclusion
In conclusion, controlled atmosphere furnaces have become an integral part of sintering and annealing processes due to their ability to create an inert environment that prevents oxidation, reduces contamination, and improves the end product quality. They offer improved environmental conditions, better furnace control, efficient throughput, and a higher level of safety compared to traditional furnaces. KINTEK offers a wide range of atmosphere furnaces that are designed to meet the needs of various industries. Investing in a controlled atmosphere furnace can help businesses save time, reduce costs, and produce high-quality products that meet industry standards.
CONTACT US FOR A FREE CONSULTATION
KINTEK LAB SOLUTION's products and services have been recognized by customers around the world. Our staff will be happy to assist with any inquiry you might have. Contact us for a free consultation and talk to a product specialist to find the most suitable solution for your application needs!